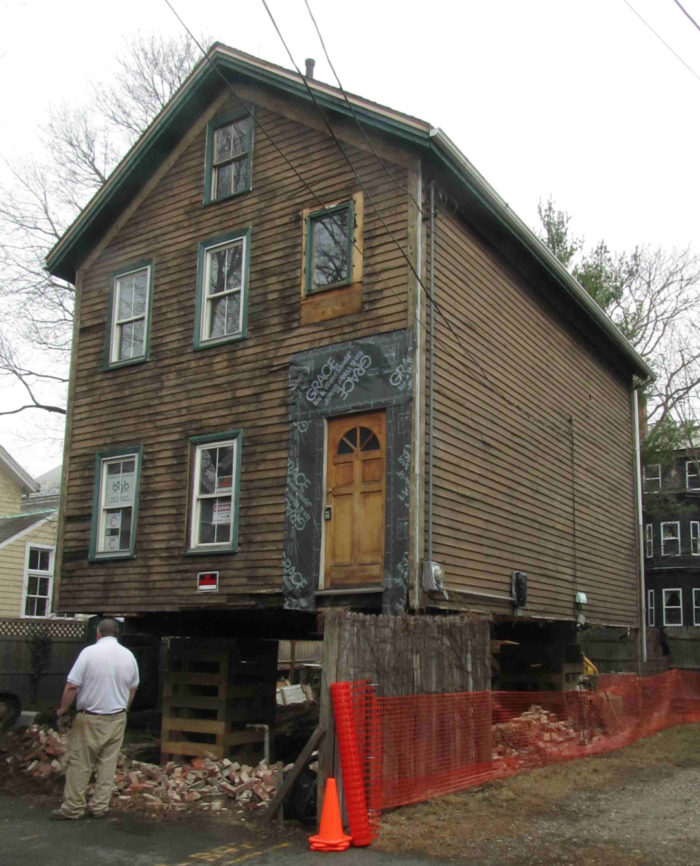
Image Credit: All photos: Brian Butler
Image Credit: All photos: Brian Butler Steel beams were slid under the floor joists to support the house while it was being jacked up. Once the jacking process was complete, the house was supported by temporary cribbing. A passerby observes the demolition of the old foundation walls. To prevent the wicking of moisture from the damp footing to the wall above, a strip of rubberized asphalt membrane was installed on top of the footing as a capillary break. The XPS insulation panels that are inserted into the Thermomass walls are equipped with fiberglass pins that keep the insulation centered in the concrete wall. Forms have been erected for the new Thermomass walls. After the foundation forms were stripped the cross-section of the completed Thermomass sandwich was apparent.
To prepare our bid for a comprehensive renovation project in Cambridge, Massachusetts, we visited the old house several times. On one of the walk-throughs, we realized that the foundation was failing in many places. We therefore proposed to raise the house and replace the entire foundation.
Raising this house was a challenging process, given the tight space and the existing condition of the house.
The house was jacked up 3 feet
We first finished all the interior demolition and removed the existing asbestos siding on the building. We then demolished the concrete slab in the basement and dug pits for the cribbing stacks to sit on. We also added new joist hangers and sistered and shored several floor joists to ensure structural stability.
Steel beams were slid under the house from front to back (see Image #2, below), and high-powered hydraulic jacks slowly raised the structure about 3 feet off its foundation, providing enough room for demolition crews and equipment to pass under the structure.
All of the existing foundation walls were then demolished (see Image #4) to make way for a new insulated poured concrete foundation and a modern drainage system.
Concrete foundation walls hide a foam filling
We used the Thermomass system for the new foundation walls. A Thermomass wall creates a sandwich with two layers of concrete enclosing a filling of rigid foam insulation. (A Thermomass wall is the inverse of an ICF wall.) The insulation in a Thermomass wall creates an excellent thermal break between the earth and the interior.
We started by installing a bituthene membrane on top of the concrete footing to create a capillary break between the footing and the wall (see Image #5).
Then the concrete contractor drilled steel dowels into the footing to anchor the wall. The next step was to set up the 4-inch-thick (R-20) extruded polystyrene (XPS) foam panels. These panels have fiberglass dowels that help keep the panel perfectly centered in the concrete form (see Image #6).
Then the concrete wall forms were erected. Finally, a concrete pump truck showed up to place the concrete. After a couple days, the forms were stripped and ready for dampproofing and backfill (see Image #8).
Better than new
Once the new foundation walls were installed, we set the house down, removed the cribbing stacks, and poured a new insulated basement slab before framing for new interior partitions.
This job was a great opportunity to save a little piece of Cambridge’s historical past. The home got a new lease on life, and will provide thermal comfort that is better than a code-built new-construction home.
Brian Butler is a production manager at Savilonis Construction Corporation in Natick, Massachusetts.
Weekly Newsletter
Get building science and energy efficiency advice, plus special offers, in your inbox.
13 Comments
cost effective?
Was this work done because the house was historically significant enough that it couldn't be torn down?
Another building site I read
Has a constant stream of questions from people asking if it is possible to do this or that to their house. Sometimes they have to be reminded that the question is not "CAN I DO THIS?" But should I do this? Given enough time, money and effort you CAN do almost anything But SHOULD you do something is an entirely different proposition. Can you put a basement where you only have a crawlspace? Sure you can. Should you spend all that time effort and money to do so instead of just buying a different home that has the features you want?
Why?
As I’m reading this article, I'm wondering, WHY? Is there a zoning reason that the building must be preserved? Was a feasibility study done? I sincerely doubt the energy savings will meet expectations. (Sometimes buying and squeezing lemons is more expensive, in money and effort, than buying a lemonade)
In most major cities in the South and SW, builders and future home owners are buying old houses in established neighborhoods, tearing them down, and building new homes as an infill project. It becomes an expensive proposition vs. moving to the suburbs, that's w/o accounting for transportation and time over a long time. It makes me wonder if this type of project in the northern climate zones make it more economically feasible.
History
Three questions in a row about the "cost effectiveness" of the project. No one raises that question when they see granite countertops, which cost far more than plastic laminate and most likely will be removed in the same timeframe, when the kitchen is deemed worn out. Perhaps this owner wanted to preserve the historic fabric of a neighborhood they love. Perhaps they wanted a basement. Yes, we can tear down everything old and replace it with fiber cement siding and vinyl windows, but that doesn't mean we should.
More on cost-effectiveness
Thanks, David.
Granite countertops. Whirlpool tubs. Three-car (or four-car) garages. Home theaters. Indoor swimming pools. A fourth bathroom. A second dishwasher. A full-scale outdoor kitchen. A man cave.
It's a long list....
We had this done.
In 2010, we
We had this done.
In 2010, we purchased a 114 year old barn that was converted to a house in 1971. It sat on a stacked stone foundation and a very shallow (0-18 inches) crawlspace. For both comfort and structural reasons, we had to do something under the house. New sill beams and frost proof walls were very expensive. A full basement was more expensive, but at the time we justified the additional cost because, if done right, we'd be gaining a lot of quality usable space.
It wasn't really an option to tear down and start new. The cost of that would be 2-3x the cost of the foundation, not including the added cost and trouble of moving out and renting for a year or so. Also, we don't mind the condition and layout of the existing living space, so the idea of an excavator piling it all into a dumpster didn't appeal to us. With the structural issues addressed, we could improve the living space as time and money allowed, and we could do it ourselves (mostly).
Unlike the house in the article, our house was not lifted. We did not have to move out of the house, or disconnect or re-route utilities. We also did not have to demo a very large masonry fireplace, which was a plus. A bobcat dug out underneath the house and as it progressed, temporary supports, cribbing and beams were installed and then the permanent footers and posts. The foundation wall was poured in four sections.
It was a huge job, and quite a feat really. There were some headaches, inconveniences and due to the way the contractor did the work, some opportunities were missed to include some details such as capillary break at footer and top of foundation. Of course, the obligatory unforeseen problems reared their head, like hitting ledge and having to split and remove it at great expense.
I specified several large egress windows, exterior waterproofing and insulation, interior and exterior drainage systems, and sub-slab insulation. Nothing to make the passivhaus people excited, but better than code, and the space is very pleasant and bright and dry.
Having lived in Cambridge for about 15 years, and eastching that real estate market, a solid house in a good location would be well worth the investment to install a full, energy efficient basement, in my opinion.
cost
It would be interesting to get the original blogger's take on the cost issue. Given that it is Cambridge, I suspect the foundation cost what one could build a whole house for in some places.
There's nothing at all wrong with renovating an old house. Most of my house was built when Washington was president. Still, it is always useful to get an idea what sort of investment is needed to do something like this. There's is also nothing wrong with tearing down a house that is past the end of its useful life, should that be the case.
What other energy efficiency improvements were done?
This post hints at other renovation done to the interior of the house. Were there any other energy retrofits that were done to the envelope? What HVAC system was installed, and was there a HERS rating done for the finished project? Or, was the only energy related work centered around the foundation?
What was the reason the client and builder chose the thermomass, and are there any articles that compare this type of thermomass wall to the alternative ICF type of wall? Was this wall type easier in a retrofit situation than the ICF?
Bringing up items such as
Bringing up items such as granites countertops and man caves misses the point entirely. Those items are expensive but not necessarily economically inefficient If others are willing to pay you for those features then they aren't a waste of resources. In fact in some homes cheap finishes are economically in efficient because buyers will penalize you more than the cost if the upgraded finishes if they aren't there already. While it is true that almost anything you do to upgrade a house can cost more than you would ever hope to recover, a change such as this invariably breaks the scale.
Prove it
What are your metrics, But Why?
Response to B.W.
B.W.,
Defending the appropriateness of installing granite countertops and building man caves, you wrote, "If others are willing to pay you for those features then they aren't a waste of resources."
Fair enough. But the same logic can be applied to a new foundation. According to your definition, the homeowners were willing to pay for it -- so it wasn't a waste of resources.
But Martin...
... methinks B.W. was referring to the effects on RESALE value of the upgrade, not the value to owner who had the granite countertops, man-cave, or CIC foundation installed.
I'm not sure there's a measurable resale value in man-caves either, but maybe. Granite countertops can enhance resale value, but it depends on local market and aesthetic impulses of the buying public, which are fickle. Granite has a decent specific heat- there's real thermal mass to be had there, along with marble staircases and floors, but it's tough to make the financial case on energy use grounds alone, eh? :-)
It's not clear to me whether a slightly higher than code-min thermal performance foundation will have the same residual value at the point of resale as granite countertops or marble showers, but the whole short-termer house flipping mindset is mentally bankrupt & stupid from the get-go from a homeowner perspective. The average US-American moves every 5-7 years, but more than half of US home OWNER have more than 10 years of tenure living in their house, and a quarter have more than 20 years. Thermal performance features often get heavily discounted at resale relative to the finish surfaces, but if you're living there for a couple of decades or more who cares? YOU get reap the benefit, and have the satisfaction of not having paid someone to build an under-performing piece of junk. Even if it just breaks even over time on energy savings, there's a built-in hedge on future energy cost inflation. If you're going to build something, it's worth building it with at least a tinge of hedge in it.
I personally like granite countertops for the long term durability, but find man-caves a silly overdone cliche'- ain't gonna build one. Again, YMMV. But how the buying public would value various aspects in a resale scenario for any of the features of my house matters not a bit. We don't plan on moving any time soon, and will continue to build it out & finish it the way WE like to live, rather than worrying about satisfying the tastes of the next owners. It's the difference between temporarily hanging out vs. actually dwelling in a house. Most homeowners end up as dwellers not short-termers- it's about living there, not flipping it when the market heats up, and living is more than a purely financial exercise.
Massachusetts has adopted IECC 2012 into the statewide buliding code, thus a minimum of R15 c.i. is required for foundation walls. The 4" XPS installed here beats current code-min by 33%- not a huge stretch. Depending on the actual upcharge (if any) of getting there using this product over other method, there is still likely to be financially rational on a longer term energy cost savings basis, especially if that basement is converted to fully conditioned living space. The footing does not appear to have been insulated, and it's not clear if the slab is either. Having the thermal bridge of the inner concrete to the footing & ~50F sub-soil undercuts the performance of that ~R20 wall somewhat, but it's not an energy disaster by any means. The above-grade portion of this type of wall probably outperforms an R21 (2.5" + 2.5" EPS) ICF, but the thermal bridge at the footing that you get here (and DON'T get with an ICF) means that it under-performs an ICF for the sub-grade portion.
I personally wouldn't build a foundation wall without better-than code R-values. YMMV. If there's an extravagance it's the "extra" R5. Taking it the extra inch to R20 isn't exactly blowing it out to PassiveHouse levels, or anything close. There may be cheaper/ easier ways to hit R20, but without a material cost & labor breakdown it's hard to make that call, but they had to hit at least R15 to even be legal.
It's not clear that it's any cheaper or better than an ICF foundation in this zone 5 climate, but would be a superior performer (if not cheaper) for above-grade walls in a cooling dominated climate.
The why and the what
Sorry for the late follow-up…
The why:
Keep in mind this is Planet Cambridge… Little colonials like this are regularly fetching over $1m, with the median square foot price of real estate currently at $558, (as of 7/24/14 on Zillow). The house sat just about on the lot line, so knocking it down and starting over was not possible with zoning, and centering a new house on the lot would have consumed the driveway on the opposite side.
Beyond the pure economics, there were dire needs to be addressed:
1. The basement was smelly. REALLY SMELLY. A constant source of musty mildew stink that permeated through the whole house.
2. The rubble foundation was unsound. The mortar joints were all but gone and some of the larger stones were coming loose, with a small cave-in that had occurred at some point of about a foot and a half in diameter.
The reasoning:
Overall, there were limited options: the architect wanted to dig down and underpin the half brick / half rubble foundation (was about 6’-2” clearance originally), to create more head clearance, but it was deemed impossible by the engineer, as the wall would have just crumbled under the digging. But the clients loved the neighborhood and were committed to a home with the highest of air quality, so we put their options on the table.
The upshots:
Electrical boxes and conduit were set in the concrete for outlets, switches and wall sconces that eliminated the need for surface raceway or any sort of furring to conceal wiring. The concrete makes a very stable substrate for plaster and paint, especially with the complete capillary break and vapor barrier. (just don’t get mad and try to punch a wall…!) No efflorescence and no condensation of any kind. In fact, when one enters the basement its easy to be completely oblivious to the fact that you are below grade at all. The new egress windows and fully glazed walk out basement door make the space bright and inviting.
Overall:
The rest of the home was completely renovated to comply with our so-called energy “Stretch Code”, which requires a HERS 65 max. We installed heat recovery ventilation and the envelope blew appx 1.0 ACH 50. Their HERS rating is still pending, but the walls were furred to accommodate 5.5” of cellulose, the roof was insulated with 9.5” of densepack cellulose and 4” of rigid exterior insulation. While appx 90% of the structure was rebuilt, we did treat the eaves like a DER, and chainsawed the eaves for a nice tight envelope, then reattached dummied overhangs and falsework to restore the original architecture. The R-value of the new basement is decent, but whats' more important is that it's continuous. Virtually zero thermal bridging. And because the insulation is sandwiched in the middle, conventional finishes can be applied to the inside and the outside. A faux brick finish outside was chosen to blend in with the neighboring homes.
Log in or create an account to post a comment.
Sign up Log in