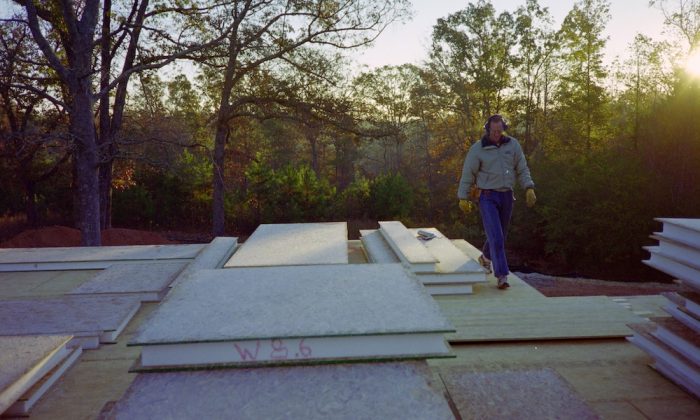
Building your first house as an owner-builder can be hectic, nerve-wracking, and wildly exhilarating. I experienced all those things and more when I built a house for myself 20 years ago. I’ve written a bit about it in the Energy Vanguard Blog, but not for a while. I’m going back to this topic now because of four things.
First, it’s the 20th anniversary. Second, I’ve had to go back and find photos to put in the building science book I’m writing. Third, I had a recent call with someone whose book helped me understand the logistics of contracting your own home. And fourth, I also spoke with the builder I hired to help me run the show during that critical period from having a foundation in the ground to being dried in.
If you’re building your forever house, as I was, let me share with you what my experience was like and give you some pointers.
Plan to spend a lot of time planning
When you embark on this project of building your first house, you need to spend more time on planning. Yes, you’ve got to have house plans. You also need a plan for getting all the materials you need. You need a plan for hiring workers and trade contractors. You need a plan for dealing with the building department and the bank. And you need a plan for the unplanned . . . as much as that’s possible.
The problem is that this is the first time you’re building a house. In my case, I’d never built anything larger than a bookcase, but I got the project to the finish line. The main thing I would change if I could go back is to spend more time planning. I thought the project was going to take two months once we started building walls. I was wrong. It took nearly two years. If I had delayed breaking ground for six months and done more planning, I could have cut the construction time and saved money, too.
From foundation to dried in
The problem was that I’m the kind of person who jumps in and then figures out how to swim. So we began shortly after getting the building permit in September 2001. (Yes, that month. It was a weird time.) We got the hole for the basement dug in late September, had our basement walls a month later, and were ready to start framing at the end of October.
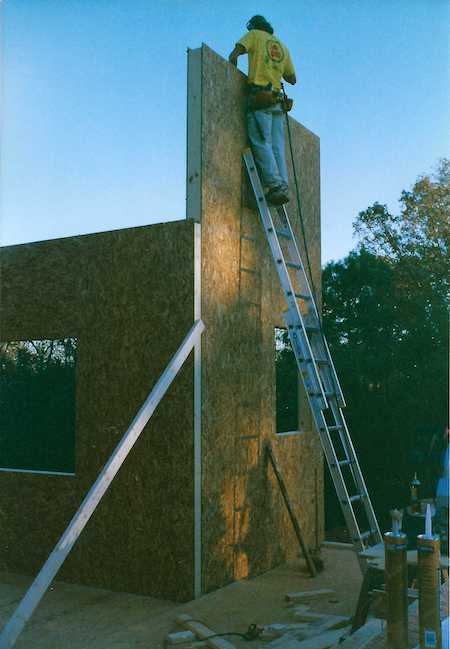
Our structural insulated panels (SIPs) arrived on October 29, and we started erecting the walls the next day. That’s Steve Tyree on the ladder in the above photo. He drew our panel plans and helped as a SIP consultant to get us started. (That’s him in the lead photo, too.) It’s hard to know which day during the whole two-year project was most exciting because there were so many (along with a few depressing days). But starting with those first floor walls would certainly be in the top three.
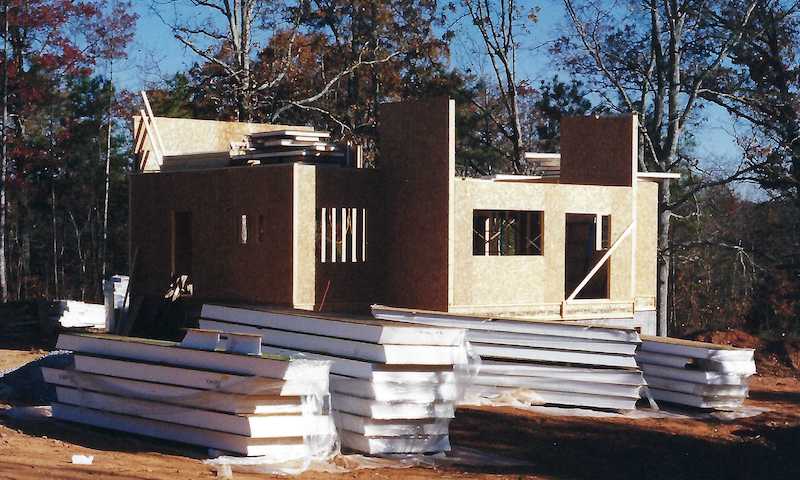
It took about a week to get the first-floor walls done and then put in the second-floor I-joists. In the photo above, we had started on the second floor walls. You can see a short section of it on the back of the house.
There’s a story with that back wall, too. We got about half of it installed and then had to tear it down. The panels came pre-fabricated so the openings for all the windows and doors would be in the right places. Of course, that depends on installing the panels facing in the right direction. As we got to the second window opening of that wall, I looked at the plans and noticed the openings weren’t in the right places.
Oops! Add a day.
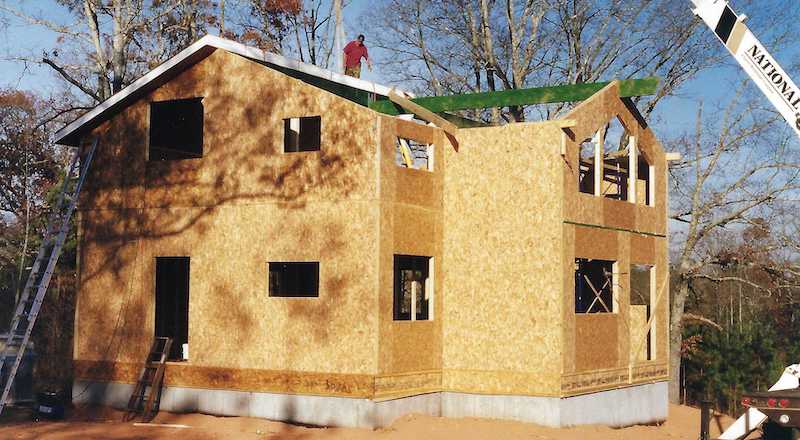
The walls went up quickly. Setting the roof panels took almost as long. The back side was relatively easy. The roof panels, being thicker than the walls, took more work getting them mated securely. The front of the roof was harder. It had two valleys, which meant cutting a lot of bevels on the splines. More than once we had to send a panel back to the ground because we cut the bevel wrong.
Oops!
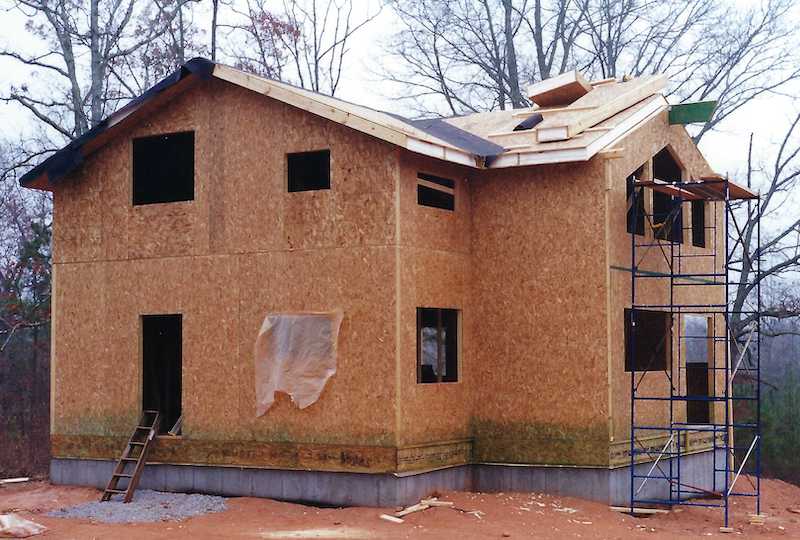
Ah, the roof is almost finished. Except there’s a story with those two panels sitting up there. Those panels weigh about 150 pounds each, and we had to place them out on the end of the prow roof. That meant the majority of each panel cantilevered over the gable end. The top and bottom of the panels attach to the ridge and eave beams.
We aborted our first attempt. None of us felt confident in the wimpy rope and ratchet strap we were using to drop the panel over the edge. So I ran to the big-box store and bought a one-ton come-along, a heavy-duty ratchet strap, and some better rope. Although it was still scary to push that first panel over the edge, we avoided catastrophe and got them set.
Whew!
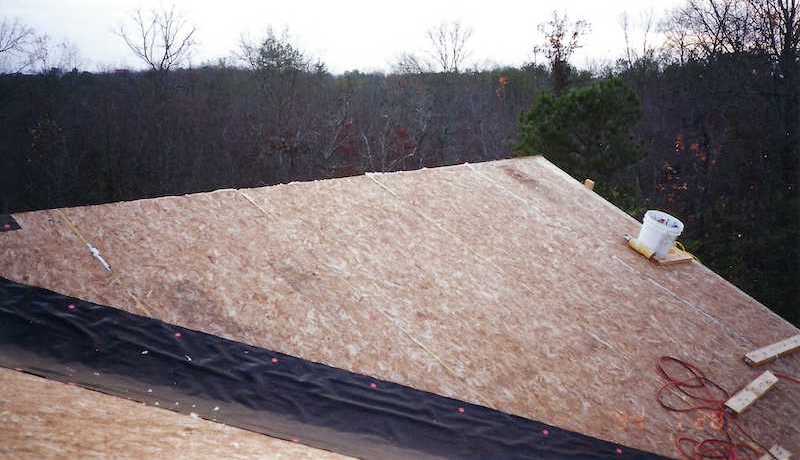
With all the roof panels in place, the last step before getting felt on the roof was putting in the rest of the long screws that secured the panels to the wall framing and ridge beams. On Thanksgiving day 2001, I spent the whole day up on the roof by myself screwing down the panels. Then we went to my friend Perry’s house and had a nice meal.
The long stretch: from dried in to living in
By mid-December 2001, we had the house dried in. I thought we were almost done. Oh, how wrong I was. (Have I mentioned it took two years?)
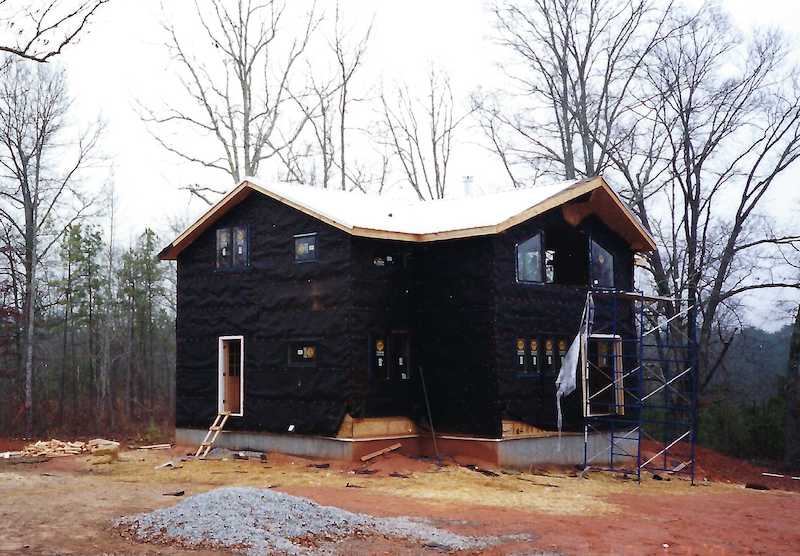
I won’t give you a blow-by-blow of everything that needed to happen, but here’s a snapshot at how things progressed:
Winter 2001-02. Did interior framing, back porch, front porch, and carport. My dad died in January, which set me back in more ways than one. We also had started the electrical work in the fall and that continued.
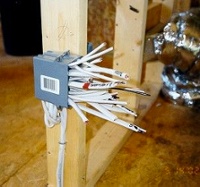
Spring 2002. Got the siding installed and did most of the exterior painting. Doing some of the painting myself in May 2002 was great therapy. Wiring continued.
Summer 2002. I framed the interior stairs (finally!) Put screen on the back porch. Started installing the tongue-and-groove ceiling on the interior. Wiring continued. Got drywall in early July. Started doing tile floors. I worked full time on the house.
Fall, winter, spring 2002-03. I was teaching physics at a local university so things slowed down. Continued with lots of details: trim carpentry, flooring, woodstove . . .
Summer 2003. Installed the greywater system and composting toilet, after an ordeal with the environmental health department. Installed cabinets, lights, plumbing fixtures, and all those other things that go into a house. Again, I worked full time on the house for the whole summer.
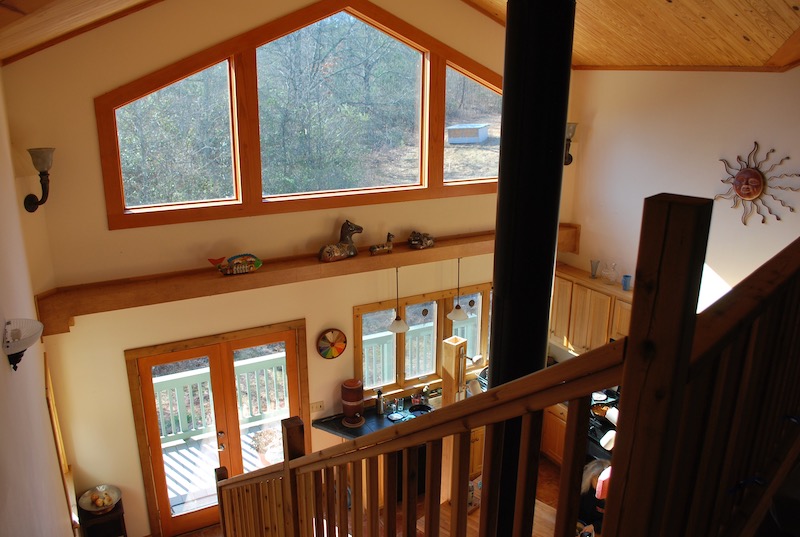
In August of 2003, we got our final inspection and moved in. Hooray! It was a cheery house with lots of light. I designed it with passive solar features that worked well. (This may be the only house in Georgia with trigonometry done on the interior wall studs.)
Advice for new owner-builders
I’ve already given you my most important advice: Do more planning. Delay the start if necessary. But I learned a lot more, too. When I first embarked on the project, I did two things. I took a weekend homebuilding class at Southface and bought a book called The Complete Guide to Contracting Your Home. Those both helped immensely. (The third motivating factor I mentioned at the top of the article was talking with the author of that book.)
Here are some other tips:
Get to know the suppliers in your area. Some are more helpful than others. Find a place (or places) that will not only sell you materials but also connect you with other people. I bought most of my materials from Home Depot, and the crew at the Carrollton pro desk were super helpful.
Buy the tools you need. I made the mistake of renting some things at first before I finally bought them. I could have saved money by buying them upfront. Of course, this doesn’t apply if you’re subcontracting everything. I did a lot of the work myself, with hired laborers sometimes.
Get help with the framing. If you’re planning to contract the house and do a lot of work yourself, get yourself an experienced framer to help if you haven’t done it before. Dan Shaw was a builder and carpenter who was essential in helping me go from foundation to dried in.
Find a good all-around contractor. For me that was Bright Construction from Franklin, Georgia. They wrapped the house with felt, installed the windows, framed the carport and back porch, and put up some of the tongue-and-groove ceiling. They were a great resource.
Plan on it taking longer than you think. I know everyone says that, but it probably will. Hofstadter’s Law says so: “It always takes longer than you expect, even when you take into account Hofstadter’s Law.” I thought it would take about two or three months. Instead it took two years.
Plan on it costing more than you think. I don’t know if there’s a financial equivalent of Hofstadter’s Law, but there should be. I made decisions all along the way that cost me more than I had planned. (The tongue-and-groove ceiling was one of them.) And one thing that makes it cost more is when it takes longer. The bank charges interest on that construction loan every month. But hey, this was going to be my forever house, so I wasn’t about to skimp.
Epilogue
I absolutely loved building my own house. The planning phase was exciting because I could imagine it all coming together. The site work and framing was my favorite part because we went from bare land covered by weeds and privet to a hole in the ground to a foundation to something that looked like a house. The last year and a half had its ups and downs, but just seeing the house develop at every stage of the way gave me great joy.
Yeah, there were low moments, but the satisfaction of seeing it all come together, the feeling of accomplishment, is something I’ll always remember—even though it didn’t turn out to be my forever house. I lived it for three years, and it was the most comfortable, energy-efficient, inspiring house I’ve ever lived in.
There was a while when I thought I’d get the chance to build another house. I wanted the chance to do it all over again without making the mistakes I made the first time around. Two years ago, however, I bought a house that I love. My wife and I have been fixing it up, and it’s going to be our forever house. (Right?)
_______________________________________________________________________
Allison Bailes of Atlanta, Georgia, is a speaker, writer, building science consultant, and the founder of Energy Vanguard. He has a PhD in physics and writes the Energy Vanguard Blog. He is also writing a book on building science. You can follow him on Twitter at @EnergyVanguard.
Weekly Newsletter
Get building science and energy efficiency advice, plus special offers, in your inbox.
17 Comments
Appreciate the article, Allison. The house looks great.
Good pep talk on the planning stage - that's where I am now, and I've just been pouring every free hour into it.
Great article. I have done many large renovation jobs but have yet to build the entire thing. You are inspiring me to do it.....maybe once I retire but before I get too old to do the work.
BTW, I once met a guy-a teacher-who built his own house during his summers. He did everything with little or no help, including put up beams..... And he only had one arm. I think of him often when I get discouraged on a project. His story reminded me of the three "P"s: perseverance, patience and playfulness (have fun doing it).
I noticed that you neglected to mention the amount of money to be saved by being an Owner/Builder - yes, I know this subject is considered by some to be socially unacceptable talk, engaged in by only crude socially suspect individuals.
So, being an old crude guy, I will bring it up for you. Did you or did you not save money with this approach? I have done similar projects multiple times over the years and have found them to be financially rewarding.
In the past, the rule of thumb was that the total construction cost of a house was about 50% materials and about 50% labor (ignoring the cost of the land) - today that ratio may no longer hold. In the years when I was involved (1971 to 2010) this seemed to be true. My general approach was to buy the property, draw the plans and get the approval and permits myself - then hire the grading and foundation (concrete work), then hire a sub to
frame up the exterior walls only and another sub to complete the roof. I then went to work and did everything else (hammered every nail, etc.). This sequence seemed to reduce the final cost by about 35 to 40 percent. By the time I got to the third one it was no longer necessary to deal with financial institutions - which makes life a lot more pleasant.
I tell this story to encourage those who are thinking about it - yes things will go wrong, mistakes will occur, sometimes you will get so tired you will think about running away to some south seas island. But, in the end it's worth it! You can do it!
I think the biggest saving is that you don't pay taxes on the work you do yourself. Otherwise, I don't think anyone with a decent salary would save a lot of money being an owner builder.
Doesn't mean it's not worth it though. A custom house is pretty much out of reach of most people unless they build it yourself.
Plus, I think we often underestimate the amount of time you have to spend supervising and planning a job even though you hire someone. It's so hard to find quality tradesperson nowadays that you really need to be there to check everything is done correctly.
"I don't think anyone with a decent salary would save a lot of money being an owner builder"
This kind of depends, and I'd say in most cases this statement is not true. Most people, including those with a decent salary, work set hours. Working on your house outside those hours doesn't take away anything from your earnings.
Trevor,
Where things get grey is when people could work those same "extra" hours at their job and pay someone else to do the construction work.
The other problem is that trades often pad their prices when a homeowner wants to be involved. They do that because it almost invariably makes the job harder due to the way it affects the schedule, and the extra work it usually involves for them.
There is a frequently told joke among builders: My rate is $50 an hour. It's $60 if you want to watch, and $70 if you want to help.
Yes or you could have two jobs instead of building your house. But building a house is probably more fun :-)
Not everyone has the will to build a house and having a job at the same time so my comment was more aimed at these people. If you are able to put the hours after your regular job, you'll save lot of money that's for sure.
Personally, I don't think I would be able to do it. I would need to quit my job or only work part time. It's just too much work.
Alex,
A lot depends on what people mean when they say they are building their own house. The range runs from just acting as project manager, to doing all of the physical work themselves.
Much of both the coordination and labour can't be done after hours. Lumber yards and concrete batch plants aren't open, your engineer isn't too happy when you call him at home after dinner, and someone needs to be on site when the sub-trades or lumber deliveries arrive. What is a fairly complicated process at the best of times becomes a lot more so when you decide you are working when everyone else isn't.
Agree with AlexPoi that you may not save money building your own home. I left a high paying (boring) engineering job, and the effective pay rate of building my house was far less. However, building was a great experience, and I'm much happier having built my own house than staying at the old job. Found other jobs afterwards. But its definitely not about the money in many cases. If you are that motivated, hard-working, and skilled, you could probably make more money working somewhere, than building your own home.
Building your own place can be an incredibly satisfying experience, but I don't know many first timers who don't also spend most of their time talking about how taxing the process was.
Part of this comes from not understanding the established process and sequence of building. Things go a lot easier if as a novice you don't try and make everyone do things the way you wish they were done, rather than the way they are. A project without a lot of exotic detailing helps.
You are likely to do a better job that pros on some tasks that require time and attention, and poorer on those that require skills and experience. Part of what distinguishes DIYers from pros is knowing where it is important to place your emphasis, and what doesn't matter. As with pretty well every skill from baking to skiing, your first house will not be as well built as any subsequent ones.
Whether you will save money depends a lot on how you value your time. If the hours you spend on it come at the expense of other paid work, then the advantage largely disappears.
All those caveats aside, there is little more satisfying that living in a space you created yourself from nothing. It's like alchemy - and if you can get through the work that leads to that result, it's magical.
Agree that if you enjoy design and construction, planned and learned how to do most everything you will do yourself, and quit your regular job (or take a year off), building your own place can be very satisfying, one of the best things you have ever done.
Helps immensely if you are a hard worker, in excellent physical condition, have someone knowledgeable you can hire to help with some of the work, avoid building during boom times (when little good help is available to hire and materials are more expensive or less available), and have the cash to fund your projects. (I didn't have the cash but managed to borrow from the subdivision developer and found a private lender if that fell through.)
KISS - Engineering principle "Keep it simple, stupid!" Easier to do, less work, less chance of errors, and less expensive. For example, build a rectangular shell (e.g., Colonial, Cape, ranch style home) without a lot of bump-outs and detailing. Build a well-insulated, very airtight shell so a mini split can handle your heating and cooling (much simpler and economical).
Plan to do things later: The object is to get a Certificate of Occupancy, move in, and get a mortgage. Defer other things when possible. I know that Malcolm reminds us of unfinished details in his own house, and its true...if you don't HAVE to do it, you might never complete those details. Can you leave some rooms unfinished for later? Plan for an addition for later? Skip the trim work for now? Do most of your own kitchen cabinets later? Get by with one bathroom and complete the others at a future date? You get the idea. I managed to get a C.O. in one year doing 80% of the labor, move in, get a full-time job, and complete the house while employed over the next two years. A lot of work but rewarding as you move from foundation, to framing, to electrical/plumbing, ... and see it all take shape. An amazing experience. Go for it!!
This is the house I built, the design, and some about the experience:
https://www.greenbuildingadvisor.com/green-homes/a-passive-solar-home-from-the-1980s
Alex:
The biggest savings come from multiple factors - first from your labor replacing that of others (this is actually a minor savings) - second from being careful in your selection of materials and finishes (also minor) - third from not having to pay interest (to a bank) on labor costs for many (20 or 30) years into the future (this is bigger) - fourth your savings from lower energy costs over many years of living in the house (this can get really big if you get the design right and live there a long time) and last, the real biggie, inflation in both house prices and interest rates. I built mine in the 70's and 80's - really high inflation years and I learned my lessons. Being a DIYer lowered the construction costs a lot but the final sales price of each house was based on a housing price appreciation rate of a full priced house from day one. The mortgage rates were based on the going rates at the beginning (around 7.3% in 1972) but they climbed to over 16% in the 80's - they are going up right now - how high will they go and for how long? Oh! one more thing my wife and I
maintained full time jobs while building those houses - if we could do it others can do it. I'm not saying they will like it but it is possible. The other real biggie is the capital gains tax rule on housing you have lived in for two years or longer, this really comes into play when the housing price appreciation rate is high (like it is right now). You could theoretically add $500,000 to your income, tax free every two years if you could build them that fast and that cheap.
Saving money building your own house will differ depending on many factors. In my case, I will coming ahead by a long shot.
Due to the high demandes in construction at the moment, contractors are drastically inflating their labour cost compared to two years ago. I have also found that they all seem tack on a minimum of 20% (more in many cases) on top of the material cost, something I had not seem before at those level.
Two companies I had received quotes for the framing were charging me about twice the cost of material (price was also to be revised two weeks prior the start of construction) compared to what I had priced out from my local Home Depot and that was before 5-10% I would likely have gotten depending on the final amount on the order.
Also in my case, I have been allowed to accumulate my vacation for the last few years so I will be still receive income during a good portion of the build while the interior work I will do on weekends or take a few weeks without pay at some point.
Arnold
Arnold, I've been in both positions as a DIY home builder and also a contractor. I can't speak directly to your price quote, but some of these general points may apply:
-Framing subs/contractors will typically buy their lumber from a yard and not Home Depot because of quality and delivery differences. This usually costs more in material but saves in labor and hassles with better, straighter lumber.
-Markups are scary for contractors right now with the constant surprise price jumps. Most yards aren't guaranteeing prices for more than a week, if that.
-Labor is tight in most places. Guys who actually know what they're doing are hard to find and even harder to convince to work for low wages. So yeah...labor is going to cost more now.
-As a homeowner you're not likely to get the lowest price compared to a GC the sub has worked with before. Chances are that you just don't know all the little details that make the job go smoothly for the framers and so they build that in to your price. If you were a repeat customer they'd have a better idea of what they're in for and could price accordingly.
Add it all up and yes...it will cost more. This is one of the reasons I built my own home too.
Wow, this brings back so many memories. I have built a number of houses for myself, but I always used subs for the majority of the work. I would go to the low cost subdivisions and visit the Roach Wagon at breakfast and lunch, and talk to the different subs. They were much less expensive than custom house subs. I previously was a project manager for a major builder so I knew all of the steps (at least generally), but when you introduce new technology, new, unexpected things can go wrong.
In the early 80's I built 50 SIPs S.F. houses in Houston, Texas. They were built as rental houses. Why SIPs? I had always tried to build energy-wise, including using wet spray cellulose--still one of the most effective energy-saving approaches. I also used polybutylene plumbing pipe--a predecessor to PEX. That pipe was later involved in a class action law suit that caused the manufacturer to go bankrupt. It is no longer an approved building product.
Why build energy efficient houses as rent houses? We had a portfolio of rental houses and we started losing tenants even though the rent was paid on time. What was going on? Turns out the utility costs were so high the tenants could not afford the utility bills to Houston Lighting and Power.
Building with SIPs in those days was different. There were no 5 axis milling machines at the time. Every cut was by hand (skill saw) by the panel manufacturer. They weren't called SIPs, they were called sandwich panels, with particle board exteriors (now oriented strand board), and expanded polystyrene foam cores. The walls were six inches and the roof was 8 inches. Any joint holidays were filled in with canned foam.
When a house was framed up with the roof on, even in Houston's 95 temp and 95 humidity outside weather, it was extremely comfortable inside. And the polybutylene piping was many times more energy efficient than copper tubing. We reduced the utility costs by 60%.
A significant benefit of SIPs: As I said, these were single family houses, and all had hip roofs, and maybe a gable on some of the fronts--to have different front elevations. We did not have access to a crane, so man-handled the roof panels into position.
Well, along came a hurricane, typical for Houston. On one project two of the roof panels slid to the ground. Took about two hours to get it repaired. Next door was a two story house that was dried-in. It fell to the ground, with lots of broken studs. Took two weeks for them to rebuild, and a much greater cost than we experienced.
In another subdivision we had a 50 foot pine tree fall across the roof of the house. It broke in half and a branch penetrated the roof panel. A couple of chain saws made quick work and got the rest of the tree away from the house. A couple pieces of square-shaped waferboard and some canned expandable foam solved the problem. Again, a couple hour task.
So, in brief they are incredibly strong, and energy efficient. Not sure they would do great in a tornado with so much uplift, but certainly better than their next door neighbor.
Congrats on building your own house. I've long encouraged all my friends to build their own house. Even my daughter, a nationally honored decorator in the Houston market, built theirs using an owner-builder company , Green Built Homes. That is a viable way to build your own house, and you can use a little or a lot of their advice and subcontractors.
BTW what's a "forever house?"
TXFrank
TXFrank,
A Forever House is one that the occupants hope to never have to move from. That's a lot better expectation to try and fulfill than when client's call a project their Dream House.
I posted this on another thread ( https://www.greenbuildingadvisor.com/question/opinions-regarding-european-hollow-insulating-clay-bricks#comment-220389?utm_medium=email&utm_source=notification&utm_campaign=comment_notification&utm_content=view ) but realize I might get better suggestions here. Hopefully it's not breaking too many forum rules. Thanks for your patience.
Hello everyone...(this is a cry for help), After years of planning and not planning during Covid delays, our Porotherm blocks will soon be sailing across the Atlantic. Never mind that shipping costs have never been higher. Unfortunately I do not have a local builder and by default am self building, a process contributors to this site suggest is possible. Until now I’ve had conversations with local masons, plumbers, roofers, etc., but not having had even vague dates, couldn’t schedule anything. We’re in a somewhat rural area that was already short of qualified tradesman. It’s proving very difficult for me to put this build together. If anyone could suggest where I might look for a construction manager, preferably, but not necessarily someone familiar with block construction, I’d be very appreciative. A fellow who has worked with Weinerberger building Porotherm houses is willing to come to the US to supervise that end of it, and I have masonry workers to assist with that part of the build. But there’s a lot more to coordinate and I’m not sure if I want to learn while doing, or if that’s even possible for me. Maybe there’s someone interested in seeing a Porotherm house get built in the US I could hire? Thanks for any suggestions.
Log in or create an account to post a comment.
Sign up Log in