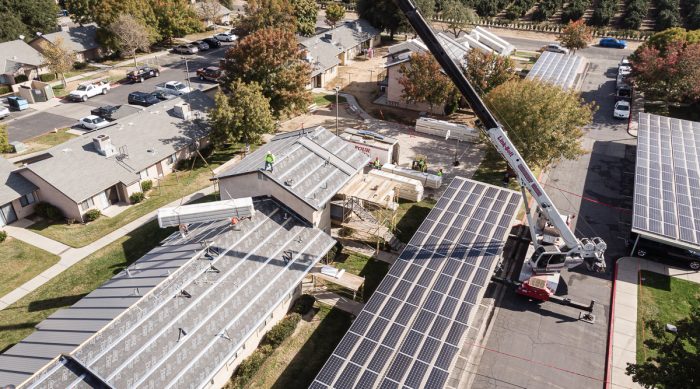
It’s been more than a decade since the Dutch government invested $40 million of seed money in “Energiesprong,” or Energy Leap, a campaign to upgrade the energy performance of existing row houses at no net cost and minimal hassle to their occupants.
The novel approach involved fitting older homes with prefabricated panels containing insulation, windows and doors, and upgraded mechanical systems. Panels could be set with a crane and a relatively small crew to transform an existing house within a week or two while residents mostly stayed put. Thousands of homes have been upgraded since the start of the program in 2010, and the effort subsequently spilled over into other parts of Europe as well as the U.S.
For a variety of reasons, progress here has been halting. But a new round of grants from the U.S. Department of Energy (DOE) totaling $32 million could help seven separate teams advance new techniques for upgrading existing housing. The grants are part of a campaign to reduce energy use in buildings, which currently consume 40% of all U.S. energy, and knock the dust off the country’s hidebound building industry by introducing new technologies and techniques for upgrading housing.
A deep-energy retrofit including major changes to the building envelope along with HVAC upgrades is very effective at reducing energy use and making houses more comfortable, but these one-off projects are expensive, time-consuming, and applicable to only a single project. The new grants will pay for developing techniques that use prefabricated wall components and “drop-in replacements” for mechanical systems to substantially reduce energy consumption.
The grants come through the department’s Building Technologies Office, which also fostered the Advanced Building Construction Collaborative to develop new ways of updating existing buildings and reducing heating and cooling loads by between 50% and 75%. The ultimate goal is building decarbonization. The demonstration projects are aimed at public housing, manufactured housing, privately owned affordable housing and student housing, the department said, but the techniques should be useful to existing commercial buildings as well. Demonstration projects are planned in more than a dozen states around the country.
Here’s a summary of who gets the money and what projects the grants will help, as provided by DOE:
The University of Central Florida leads this effort to retrofit eight manufactured housing units and four single-family homes. Each will get a “technology pod” consisting of a minisplit heat pump and a heat-pump water heater powered in part by photovoltaic panels. The university hopes to commercialize the manufacture of the pods and make them applicable to different climate zones. Low-cost improvements to ductwork, air-sealing, and insulation also are included.
Fraunhofer USA Center for Manufacturing Innovation in Brookline, MA, leads a group developing a super-insulated, prefabricated wall panel for single-family homes. Building locations are in Massachusetts, Pennsylvania, and Vermont. Developers say they will use digital tools such as computer-aided design and virtual reality training for installers to make exterior upgrades achievable in two weeks’ time.
Oak Ridge National Laboratory collaborates with others to produce a modular, exterior panel retrofit on a dozen single-family attached duplexes and one small commercial building in Knoxville, TN.
At the Syracuse University campus in New York, entire student dormitories are the target of a retrofitting technique that could be applied to multifamily housing in general. The approach includes R-30, airtight panels as well as monitoring equipment to keep tabs on existing HVAC systems.
The Home Innovation Research Labs in Upper Marlboro, MD, leads a project to upgrade three low-rise multifamily buildings in Albany, NY, with insulated panels that improve existing R-values by a factor of four. Developers said the technology could be applied to nearly 2 million multifamily buildings across the U.S. that date from the 1970s and ‘80s.
The National Renewable Energy Laboratory heads an effort to prefabricate insulation panels for two 13-unit low-rise buildings located in Arvada, CO. The DOE said the approach uses 3D virtual reality technologies to build the panels offsite with a 50% savings in construction time and construction costs. According to the department, 90% of the people living in the facilities where upgrades are to take place qualify for a state-housing voucher program.
Rocky Mountain Institute leads another effort to benefit low-income housing, this one a nine-story mid-rise in Cambridge, MA, with 120 units. This project, too, includes insulated panels, mechanical system pods, and prefabricated ductwork.
Applying the Dutch model not so easy
A variety of organizations and developers have looked at ways of upgrading existing buildings with prefabricated parts, although nothing has emerged in the U.S. to date that’s as streamlined as the Dutch program. REALIZE, an RMI initiative, that includes Passive House Institute U.S. (PHIUS) as a partner, has been working on ways to develop prefabricated packages for upgrading existing buildings. A separate program in New York called RetrofitNY also is at work. The agency just announced $5 million in funding for deep-energy retrofit pilots for affordable housing.
Work continues on many fronts. Last year, the owner of nine buildings housing a total of 146 apartments in New York City announced plans for a $20 million upgrade that would include the installation of 8-in.-thick walls containing insulation and heating and cooling lines on existing masonry walls. Developers hoped the upgrades, which would cost about $137,000 per apartment, would reduce energy costs for the owner, RiseBoro Community Partnership, by 80%, or $180,000 per year. Improvements also included new flooring and renovated bathrooms and kitchens. The project was certified by PHIUS.
But unlike the Dutch model, the New York project did not include prefabricated panels. Instead, the buildings are getting new facades that use an External Insulation Finishing System, or EIFS. At the time, Ryan Cassidy, RiseBoro’s director of sustainability, told GBA that using prefabricated panels would be challenging in New York City’s narrow streets and that he didn’t think the technology had matured enough to be successful here.
“I love the Dutch model, and I think it’s probably the long-term solution but we’re not doing it here,” Cassidy said. “Hopefully this is a good example of how to bridge until we get to that scalable Dutch model.”
In California, REALIZE looked at ways to retrofit stick-framed buildings but learned quickly that wall panels complete with doors, windows, and HVAC pods just didn’t exist in the U.S. Instead, the group was working with Dryvit on a panelized EIFS product insulated to R-16 and with building airtightness of between 1 and 2 ACH50.
In Boston, WinnDevelopment and the Castle Square Tenants Organization are working on a REALIZE project to upgrade Eva White Apartments, which consist of two seven-story buildings and a total of 102 low-income units. Developers and architect Reisen Design Associates considered several possible technologies for the all-electric deep energy retrofit—including traditional EIFS, curtainwall assemblies, and panels similar to the Dutch model—before settling on a Tremco panel system called Revitalite. The panels will come with integrated windows and should deliver R-30 walls and air leakage of only 0.2 ach50, according to RMI Manager Brett Webster. With roof R-values upgraded to R-40, energy consumption should decline by 60%. According to REALIZE, the project is moving ahead with full financial support, including a $1.6 million grant from Eversource, a New England energy delivery company.
Fixes for a stodgy industry
The new round of DOE funding is part of a broad effort to make the U.S. construction industry more productive, less bound to convention, and better able to take advantage of developing technologies.
“The United States building sector is at a crossroads,” says a report from the Advanced Building Construction Collaborative published last July. “A range of institutional barriers and market failures have impeded national efforts to boost construction productivity, energy efficiency, decarbonization, and affordability.” At the same time, the report adds, new technologies and approaches are emerging that have the potential to change the marketplace.
According to the report, issues facing the construction industry include the threat of catastrophic climate change, a housing shortage that is driving up prices, labor shortages, and supply chain disruptions. There’s also been in increase in imports of prefabricated building products from suppliers abroad. “Taken together,” the authors said, “all of these factors put enormous pressure on the sector to adapt. If the U.S. buildings sector—including the construction and real estate industries—does not transform to respond promptly to these challenges and trends, it risks increasingly severe—and already evident—economic and societal consequences.”
The collaborative, formed by RMI and a number of public and private partners under the auspices of the DOE, is trying to push the construction industry to modernize and adapt.
Many technologies that can move the industry ahead already exist, the report says, and there is plenty of interest in putting them to use. But widespread adoption will require cost competitiveness, low risk, and ease of use, among other things.
A number of other countries, including China, Canada, and Sweden, have made significant investments to modernize construction while the U.S. seems stymied by localized building practices, a short-sighted focus on profits, and a resistance to new ideas. To date, the report says, there has been no coordinated, national effort to push the construction industry forward. “Without coordinated efforts,” it adds, “the United States is likely to lag behind nations that are making strides to modernize their construction sectors.”
Retrofitting existing buildings is an especially attractive target. Roughly 4 billion square feet of new buildings go up every year, the report says, but there are some 160 billion square feet of buildings constructed prior to 1980 that could be brought up to modern performance standards. The report cites Energiesprong as an example of how existing housing can be improved with a minimum of disruption, but the report adds:
“The overall scope and pace of retrofit activities in the United States, however, must well exceed those undertaken in Europe due to the size of the U.S. building stock. The challenge may also be greater in the United States, as less of the domestic multifamily housing stock is publicly controlled, and neither the climate zones nor the building typologies are as uniform as in some European countries.”
Reasons for optimism ahead
Lucas Toffoli, a manager in RMI’s Carbon-Free Buildings program as well as the Advanced Building Construction Collaborative, says the construction industry faces the same challenges today as it did when the report was issued. But the tone of the conversation is changing. Climate change, ongoing workforce issues, and an affordable housing crisis all are coming to a head at the same time. In response, the industry is sitting up and taking notice.
For example, embodied carbon in buildings and building materials was not a topic that even high-performance builders were talking about several years ago, he said in a video call. Now there’s a lot of interest in carbon counting from bread-and-butter companies, investors, and company boards. Further, the industry once believed, mistakenly, that domestic construction was not something that could be outsourced to overseas firms—until that started to happen. Now, there are operational buildings in the U.S. that were primarily fabricated in such places as China and Poland, shipped here and assembled. That’s helping to push the conversation along.
“It’s never as fast as we’d like it to be but we’re seeing that play out with a lot of innovation and emergent actors trying to put together technical as well as business solutions,” he said. “Also, there are impacted parties who for a long time thought they had other priorities but are now starting to see climate change and industrialized construction and modernization of construction as areas that are central to their business strategy.
“We all need to recognize that building decarbonization is part of the solution to an existential crisis that is only getting worse, and what better to invest in than that.”
New and retrofit markets face different problems. In new construction, there are a lot of examples of Passive House–level construction that are cost-competitive with a “business as usual” building approach.
Finding ways to retrofit existing housing affordably on a national scale, particularly multifamily projects, is tougher. In Europe, the original Energiesprong program had certain inherent advantages, Toffoli said, including a more homogenous target housing stock and a generous initial subsidy to get things rolling. The picture is different in the U.S., with 100 million housing units spread across a very big area, a high degree of localization in the industry, and many different building types.
“On the retrofit side, the reality is that deep-energy retrofits are still fairly costly,” Toffoli said. “That is made more so by the fact that it’s not always possible to underwrite all of the potential energy benefits not to mention all of the non-energy benefits that in some cases might even be more valuable than the energy savings. We just don’t have a great way of capturing those right now.”
He continued, “I’m talking about things like health and comfort and in commercial buildings you might have improved productivity and in residential buildings you might have lower incidence of asthma and things like that. There are grid benefits. The retrofit side is thornier, a little more complicated.”
One challenge here is to set up the means to make energy retrofits palatable even when the upfront costs are higher. The financial tools are available, he said, it’s just a question of bringing them together so that providers can offer a package that includes performance and equipment warranties.
Toffoli sees the Advanced Building Construction Collaborative as a “market facilitation hub” with room for anyone who’s interested in how to modernize the industry while working toward building decarbonization.
“And,”‘ he said, “we can also ensure that as the construction industry modernizes, with all of the benefits that has for the economy and for the workforce, we don’t just turn it into an engine to basically get faster at building inefficient buildings.”
Scott Gibson is a contributing writer at Green Building Advisor and Fine Homebuilding magazine. This post was updated on May 11 to include new information about the REALIZE project in Boston.
Weekly Newsletter
Get building science and energy efficiency advice, plus special offers, in your inbox.
One Comment
Thanks for this Scott. This is really the elephant in the room at the moment. Large scale changes in our industry’s approach to, well, everything honestly is needed. Looks like there’s more happening than I was aware of and that’s great to see.
Log in or create an account to post a comment.
Sign up Log in