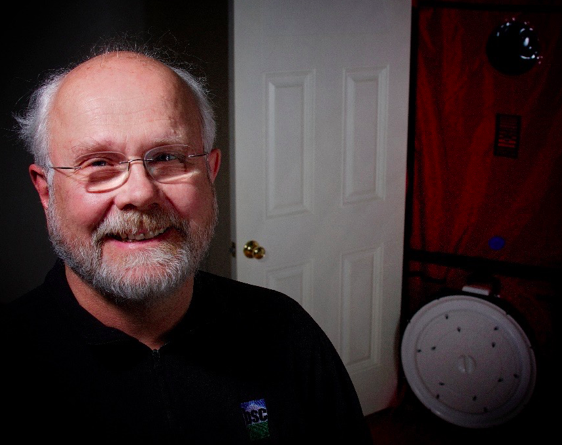
Many in the green building industry are familiar with Gary Nelson’s work. He is one of the founders of The Energy Conservatory (TEC), and he helped design the Minneapolis Blower Door. Recently, I had the opportunity to chat with Gary. My intent was to ask questions from the perspective of a practitioner working in the field. I was also curious about his experiences using the equipment he helped develop. We chatted for over an hour and a half, and his responses provided a wealth of information that I believe GBA readers will value.
Randy Williams: I live in Northern Minnesota, climate zone 7, and often have to run blower-door tests in very cold temperatures. I conducted a test when the outdoor temp was -20°F; the interior space was heated to 68°F. I use a laptop and software to control the blower door, which asks for both the interior and exterior temperatures. What effect does temperature, either very cold or very hot, have on test results?
Gary Nelson: The inside and outside temperatures that are entered into the software—as long as the leaks don’t change size—should result in accurate corrections for temperatures, at least in theory. It turns out the actual flow or cubic feet per minute (CFM) of air does change a little bit; it might be 10% or so, if you go from 70°F to 0°F. The correction means you should get the same result, no matter the inside and outside temperatures.
But leaks do change size, especially with humidity. Because wood swells in the summer, joints like those between a bottom plate and subfloor can get smaller. At TEC, our calibration chamber is made out of 3/4-in. OSB and is 8ft. by 8ft. by 16ft. In winter, it has a little less than 1CFM@50 Pascals (Pa) of leakage; it’s about half that in summer. We measure the leakage rate every few months, and it goes up and down every year. That tells me leaks change. In the case of our calibration chamber, we think the changes are related to humidity because the temperature is about the same year-round, but the humidity is much higher in summer.
RW: I’ve been testing some exceptionally tight houses recently—several are below 1 air exchange per hour at 50 Pa (1ACH50). I worry about these houses experiencing extreme negative pressures when exhausting equipment is operating. One house measured −15Pa when the dryer was running. How should we be addressing make-up air in such houses? I’m not talking about combustion air but rather make-up air for dryers, average-size range exhaust hoods, bath exhaust fans, etc. Should we be installing an open or controlled vent to the exterior to address any negative pressure these exhausting devices create? Is there a better way to address this issue?
GN: This is a big question that I keep hearing and asking. I was out with the Minnesota Center for Energy and the Environment (MNCEE) two winters ago, when they were using the Aerobarrier system in a new apartment building. When they were done with one of the apartments, it was less than 100CFM50 of total leakage. Dave Bohac, MNCEE’s director of research, and I had a discussion about how the kitchen fan was going to work. What about the dryer? What will happen when they are both on at the same time? We didn’t have answers.
In houses that don’t combustion appliances, there’s no problem. When the dryer is on, the house goes negative 25Pa or even 50Pa. It’s an intermittent thing. When it’s below zero outside and it’s a three-story house, the pressure at the bottom of the house could be −15Pa for weeks at a time because of the stack effect. At the top, it could be +15Pa. Windows at the top of a house during cold weather sometimes freeze shut.
If there is big negative pressure for a long period of time, and there are fairly large leaks through a wall causing air to hit the backside of sheetrock and make it cold, there could be frost. But if the building is tight—which it probably is given the big pressures—and there aren’t any large leaks, I’m not too concerned about intermittent pressures up to 50Pa. The reason for a 50Pa limit is that at 50Pa, it’s going to take about 10lb. of force to open an exterior door, and there are safety standards that limit the force to open a door to 10lb.
However, once a house is down under 100CFM50, and the exhaust appliances are outputting more than 100CFM, make-up air is needed. There are make-up air units designed to be interlocked with exhaust appliances, and they have heaters to warm the incoming air. Electro Industries in Minnesota makes one. I’ve heard good things about their product because the dampers, heater controls, and interlocks are included in a fully designed system.
I think there are possible solutions using an ERV or HRV but I am unaware of anything on the market yet. A solution for dryers is to use a heat-pump dryer that doesn’t exhaust air from the house. I almost put one in my house during a recent remodel but decided against it when I heard they were noisy. I have recently heard that noise isn’t a big problem.
RW: I see various issues with attached garages, many of which are conditioned. The current ANSI/RESNET/ICC 380 standard prohibits attached garages—whether conditioned or not—from being included in either the volume calculation or the blower-door test of a home. In your opinion, is this exclusion a mistake? If so, why?
GN: I am a member of the 380 Committee and was partly responsible for the standard. The ICC and IRC codes require that there be an air barrier between a house and a garage. They does not require an air barrier between the garage and the outside. I did some research on this about six months ago, and couldn’t find much information on energy efficiency requirements for garages. With a fully conditioned garage, I don’t believe there are any requirements for a vapor retarder or an air barrier in the exterior walls. But the thermal envelope of the house must contain a continuous air barrier according to codes. It has to be part of the thermal envelope, but they don’t really define “air barrier” very well. The RESNET 380 standard for doing a blower-door test does not make clear the intent of the test in terms of what is being measured. I’m lobbying for making it clearer. I think it should say: “The purpose of the test is to test the integrity of the designed continuous primary air barrier.” It’s important that it be primary because the garage may have an air barrier to the exterior.
The same is true of a three-season porch. I have a sunporch with R-40 walls and triple-glazed windows, and it and is very airtight. It’s also insulated and air-sealed on the interior. Because of the way RESNET works and the way the international codes work, that’s not considered a conditioned space because it doesn’t have a heating system. I think it should be made clear that when performing a blower-door test, the door from the porch to the outside should be open, and the door between the house and the porch should be closed. The reason being that the primary air barrier is the air barrier in the thermal envelope separating warm from cold. With the attached garage situation, it’s the wall between the house and garage that needs to have the air barrier.
The 380 standard was recently amended to require an open door or window between the garage and the outdoors during a blower-door test. This way, the air barrier between the house and garage is tested. (Update: Gary lost this fight and the standard was reverted back to requiring the garage doors and windows be closed during blower-door testing. This may have to go out for public review, which means this might not be the final word on the subject.)
RW: I recently had a home test at .33ACH50. The home is code-built and nothing special in the way of air-sealing or insulation. It’s a complete surprise that it tested so tight. I re-measured twice and conducted three more tests because I didn’t trust the data. All had the same results. Have you had any blower-door tests or testing experiences that caught you by surprise?
GN: Back in the early 1980s, one of my mentors was Dave Robinson—a physicist who designed the first super-insulated house in Minnesota. His brother built the house using two large pieces of poly for the air and vapor barriers. He owned a rubber and plastics company, and could get 8 mil. sheets of poly that were 30-ft. wide by 100-ft. long. He figured out how to cut and fold them so there was one joint between the wall and the ceiling and another joint between the wall and the floor. The house measured .2ACH50. I had never seen anything like it.
There was an early blower door I made that used flow-measuring nozzles designed by Harold Orr from Saskatoon. I had to use the smallest nozzle possible—it was about 1-1/2 in. in diameter—and I was puzzled by how long it took to get the house up to pressure. When I turned the blower door off, I could hear the air whistle for a long time as it went back through the blower-door fan. This was because the air in the house was compressed and had nowhere to get out except back through the small nozzle of the blower door. It was at least 20 years before I heard of a similar scenario. Recently, especially with ZIP sheathing catching on, it has gotten easier to make tight houses. I’m sure there are a lot of them getting down to 1ACH50 or less without the builder realizing it.
RW: How have your own homes—current or past—performed during blower-door tests? Did you design any unique or outside-the-norm details to improve performance? Did you set an airtightness goal?
GN: My house was built in 1907. We moved in in 1978, and in 1980 I started working for the state energy office as an engineer designing an energy audit. That’s when I became interested in making houses more efficient. We had terrible ice dams. It’s a 1-1/2-story house, with a roof that was half rotten because of the ice dams and the condensation in the attic. So, we took off the roof and made it a full two-story house. We added 3in. to 4 in. of foam board on top of the original wood sheathing. We used nail-based sheathing that was made from chip board laminated to 3 in. of high-density polyurethane foam on about half of the house; on the other half we used cheap 4-in.-thick high-density EPS foam designed for use under roadbeds.
The plan was to make the foam airtight. We held 4-ft. by 8-ft. sheets of board foam about 1/4 in. apart and squirted one part polyurethane foam between the sheets. The foam then expanded and completely filled the joints. We also put in new triple-pane windows. Unfortunately, this was before low-e or argon or good edge spacers, so they all failed.
I knew about air-sealing attics, so we did a good job with that. We got the house, which was about 2400 sq. ft., including the basement, down to around 1000CFM50 or 3ACH50. I don’t know what it was to begin with because I didn’t have a blower door then, but by the time I finished, I had one to use. There were some areas that were difficult to access, so they were not air-sealed, including the front porch, two bay windows, a sunporch, and the garage. It was also difficult to do a good air-sealing job at the foundation well and rim joist.
In 2017, all of those problem areas were fixed as part of a new renovation that added about 900 sq. ft. of floor area. We took off all of the siding because the joints between the sheets of foam had cracked. There were a few places where cedar shingles had turned black or were cupping, and when we took the cedar shingles off, we found the sheathing underneath was black. The places that were black were located where the house was leaking air through the failed joints in the foam. These failures didn’t cause the measured airtightness to change much; it was still about 1000CFM50 when we started the renovation. But they did allow for enough air to exfiltrate and condense on the cold surface of the chip board, causing deterioration.
Now that we are done with the second renovation, the house airtightness measures about 500CFM50 or about 1ACH50. If I were going to build a new house, I would plan for it to be less than .5ACH50. It’s really not hard to do.
Notably, there was a radon-related issue during the renovation. I imagine all of the houses you build have at least some protection for radon. Because you air-seal, you likely try to make the slab as tight as possible. Before the renovation, our house had a few long-term radon tests that measured about 4 pCi/L, so I wanted to ensure a sub-slab depressurization system that included a fan. The architect, general contractor, and subs were all experienced with radon protection, and I was traveling a lot so I left them to it. I did suggest the smallest RadonAway fan be used since the slab addition was only about 450 sq. ft.
The day before the slab was going to be poured, I took a quick look. Everything appeared right with the exception of the poly under the 4 in. of XPS. I knew it should go on top of the XPS. However, I didn’t think about how the slab or poly was going to be sealed to the EPS concrete forms, or how the plumbing penetrations for the new full bath would be sealed. By the time I had a chance to think it through and do some testing, the basement was largely finished, including drywall and finished trim.
When the house was completed, I determined that when the radon fan was turned on, it depressurized the house by about 3Pa and was sucking about 70CFM of air out of the house. This meant that I didn’t need the top-of-the-line ERV that was installed for ventilation. I also measured the pressure in the sump that is located far from where the radon fan is drawing, and found it to be −11 Pa, as opposed to the desired −1 or −2. So, I sealed the sump cover and all the joints in the new slab that I could access, and then restricted the outlet of the radon fan to get the pressure in the sump to be about −2Pa. I have since estimated that it’s still drawing about 25CFM of air from the house. The fan seems to have gotten noisier since I restricted it, so I’m planning to replace it with a variable-speed fan that won’t need to be restricted and will be both quieter and more efficient.
I gave a talk about this experience at a radon training symposium and learned from several of the instructors and attendees that my experience was typical, at least for Minnesota, in terms of how slabs are sealed during new construction. Now, I recommend that house depressurization due to radon fans should always be measured, and that the amount of air drawn from the house by the radon system should count as a whole-house exhaust ventilation system. I’m guessing this is a much bigger problem than people are aware of.
RW: In your opinion, are the current codes of 3ACH50 or 5ACH50 sufficient or should they be changed? If so, at what point is a house tight enough?
GN: I think code should probably be 1ACH50 or 1.5ACH50, not 3ACH50. Three was a good place to get things started. People were worried that if the code requirements were too tight, there would be problems with indoor air quality. I think it’s more likely to have issues at 3ACH50 because a ventilation system that’s not working correctly can lead to problems that can go undetected. When our house was at 3ACH50, we could get by with running the exhaust-only ventilation system just some of the time. Now, although the house is much tighter, if the ventilation system stops working, the air gets stale, there is condensation on the windows, and there are noticeable odors. This doesn’t happen in leakier houses. However, I think it’s safer to have a really tight house because when something isn’t right, you know it.
RW: Should there be any changes made in the way we test? Do the current testing standards using RESNET/ICC380, ASTM E779 or ASTM E1827 provide us with the best blower-door test results?
GN: I think the current test standards are okay. None have a really good definition of what the air barrier is or the intent of the test and how to prepare the building. For single-family homes, I think the RESNET 380 standard is probably the best, and I think it’s going to get better.
RW: There has been a lot of discussion about moving away from the ACH50 number to CFM per sq. ft. of surface area. Should the industry make the change?
GN: I think the codes should get away from ACH50 and move to CFM50/sq. ft. If that happens, the number should be about .065. There is no exact equivalent between ACH50 and CFM50 per sq. ft.; it depends on the house’s surface-to-volume ratio. The surface area should be the whole envelope surface, including below ground—all six sides of the box. The RESNET standard says to use the exterior dimensions of the walls. I have always used the inside dimensions—it’s the usable floor space that matters. It is crazy to me that adding 6 in. of insulation to the outside of walls is seen as increasing the floor area. The reason that’s in the standard is because of an ANSI standard developed by real estate agents. Real estate agents don’t want to go inside the building to measure the floor area, and they want it to be as big as possible so they measure on the outside. For some reason, we adopted that standard for measuring floor area.
RW: Is there a new technology or a change to the way we currently test that you find exciting?
GN: There is a pulse technique from the U.K., where a tank of compressed air is used to make a quick-pressure pulse that is analyzed to calculate the airtightness. I think it’s probably okay, and may have some special applications but it doesn’t help find leaks. To me, the main reason to use the blower door is not just to get a number, it’s to help figure out where the leaks are.
RW: What lessons did you learn in your career that changed the way you design or manufacture your equipment and/or software? Did you have a moment of discovery that influenced TEC?
GN: Yes, I was driving from my hometown of Two Harbors to Minneapolis, thinking about how we were going to seal our blower door into a doorway, and I came up with the idea of four L-shaped pieces of plywood that were slotted—like the current frame—but I used plywood instead of aluminum. It was simple, light, and cheap, and it worked really well. Then we came up with the idea of the cam levers.
The data logging program TECLOG was designed to study back drafting, and the Duct Blaster came from collaborating with several researchers on studies around residential duct leakage and distribution system efficiency. We developed techniques for both measuring and locating duct leaks that were used in the first studies of energy savings. We worked on a project with researchers from Ecotope, a consulting firm in Seattle, as well as with Washington State University on a grant from DOE to design a device to measure flows though air handlers. This resulted in the TrueFlow, which is currently being improved to be available as a wireless digital device.
RW: When I purchased my first blower door, it was a tool that energy auditors/raters needed to properly do their jobs. Today, educated building contractors are purchasing blower doors to build the best houses they can. Did you foresee this shift in who would be purchasing your equipment? Many of these builders learn to use the equipment by watching online videos rather than in a classroom setting. Is there a piece of advice you could give to a builder just learning how to use this equipment?
GN: Around 1980, when I first saw a blower door, I thought within five years every builder would have one. Airtightness was starting to be emphasized because the Swedish building codes required 3ACH50 for single-family houses and 1ACH50 for multi-family buildings above three stories. I thought the market would be builders but they have never been a big market for us. I still think builders are the ones who need it.
RW: Is there a piece of advice I could give a builder ready to use a blower door?
GN: Yes, read the manual, watch the video. This isn’t hard. We are measuring the air going out of the fan, which is the same as the airflow coming in through the leaks. We are measuring how much pressure that creates in a building. It’s a simple concept, and it’s an easy piece of equipment to use. I always teach people how to do a simple single-point test using the DG-1000 pressure and flow gauge.
RW: Would it be better to run a single-point or a multi-point test when it’s really windy?
GN: Either one works but take multiple readings. If what you care about is CFM50 or ACH50, taking more measurements of the flow at 50Pa will be more accurate than taking the same amount of time measuring at different pressures. I like to take a 30-second baseline reading, and then a 30-second reading at about 50Pa using the CFM@50 mode on the gauge. I repeat this five times. The range of resulting values is a good estimate of the range of values that the true value falls between, and the average of the five values is the best estimate. If all five values are less than what is required to pass the test, you can be pretty confident the house passes. Unfortunately, we don’t have software that supports this procedure, but I hope we will add this or something similar in the near future as we work on improving accuracy in windy weather.
If you are doing a multi-point test with TEC Auto Test, turn Wind Assistant on; it will set the time averaging to 30 seconds—the default for Wind Assistant. After the test, look at the results to see if the resulting confidence interval (the +/- %) is good enough. To get it to be smaller, repeat the test but change the time averaging period in Wind Assistant to 60. Keep in mind that this is still a work in progress, so give us a call if you need help.
RW: Are you currently working on any projects?
GN: There are several interesting things I’m working on. One is a fog puffer made from an e-cigarette and a turkey baster that we just introduced as a kit. I’m happy with the quality of the fog it makes but am anxious for feedback from people that will be using it in the field before making some possible improvements. There is also a commercially available fog generator that I’m modifying for field use, when more fog is helpful.
Additionally, I’m helping to improve the accuracy of the blower door during windy weather. I designed a simple T fitting for the end of the outside tubing that both reduces wind noise and protects the end of the tube from admitting rainwater. It will soon be a standard part of every blower door we make.
And we are working on our TEC Auto Test software to make it detect wind and come to better conclusions about when to make longer data-point time averages. I continue to participate in several committee meetings to improve ventilation standards and building test procedures, and I’m looking forward to getting back to attending conferences in person again.
_________________________________________________________________________
Randy Williams is a builder and energy rater based in Grand Rapids, Minnesota. Photo courtesy of Gary Nelson.
Weekly Newsletter
Get building science and energy efficiency advice, plus special offers, in your inbox.
2 Comments
Nice Q&A.
> air drawn from the house by the radon system should count as a whole-house exhaust ventilation system
But where it is drawn from is unknown. Meaning that practically (eg, keeping a bedroom or office healthy), it should often be ignored.
There is also "ASHRAE Standard 62.2 assumes that a home will receive outside air from infiltration at a rate of 2 cfm/100 sq ft." This needs to be revisited for tight houses.
Tight houses make "negative interior pressure in Winter, positive in Summer" much more feasible. Since this has a large beneficial effect on wall/ceiling moisture, it might allow some lower cost designs (eg, less exterior foam or no need for an interior side air barrier).
Good interview, Randy
The seasonal ACH50 of the TEC test chamber was interesting. Tighter in summer with higher humidity, more flow in winter as the wood dries out. Would not have thought much about a radon reduction system drawing air out of the building envelope, makes a difference in a tight house.
Log in or create an account to post a comment.
Sign up Log in