1950s brick home: Crawl space wall insulation questions

Hi, I am working on insulating and sealing the crawl space of my 1950s brick home in Zone 4 in central VA. I have pulled out the fiberglass insulation on the floor joists and am getting ready to start work on replacing the vapor barrier and insulating the walls with foam board.
The walls of the crawl are block and brick with uneven areas where extra mortar dried. I was planning on using borafoam http://www.nisuscorp.com/pest-management-professionals/products/bora-foam to insulate the walls and the areas of the crawl space walls between the joists because it insulates and functions as a vapor barrier. The house doesn’t really have rim joists, the joists just sit in the brick and there are 2 x 4’s nailed in at the top. The questions I have are:
1. Is it ok to cut and cobble the foam board into the areas of the crawl space walls between the joists where the rim joists would be in a newer home or will this trap moisture near the ends of those joists and cause they to decay/fail? I have attached pictures showing these areas.
2. Does the crawl space wall need to be nice and flat or is chiseling away extra mortar and obstructions to get it mostly flat provide a good enough surface to attach the foam board insulation to?
3. Should I consider other foam board insulation like formular XPS instead of the borafoam EPS (with 3 mil poly on each side of the board)? I like the borafoam because it includes the poly on the board so I figured I wouldn’t need to run poly up the wall as far if I used it and because it is termite resistant.
Thank you.
GBA Detail Library
A collection of one thousand construction details organized by climate and house part
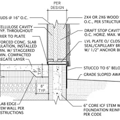
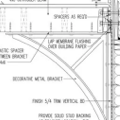
Replies
Matt,
Here is a link to an article that discusses the risks associated with insulating walls with embedded joists: "Insulating Basement Walls With Embedded Joists."
Concerning your question about chunks of mortar on your uneven walls, this is a judgment call. If the wall is extremely uneven -- as typically occurs with a stone-and-mortar wall -- the best solution is to insulate with closed-cell spray foam. If it's only somewhat uneven, you may be able to knock off the protruding globs of mortar with a mason's hammer, and end up with a wall that is flat enough to insulate with rigid foam.
If you do end up using the rigid foam, you need to pay very careful attention to air sealing at the perimeter of the wall -- probably with canned spray foam -- to avoid hidden air pathways that allow convective looping that might undermine the insulation's effectiveness.
Thanks Martin. Given what I have read I need to seal all the joints between the brick and the wood of the joists with caulk (silicone, acrylic, or what?) and air seal the remaining area with foam board and/or spray foam, is that correct? This would reduce the chances of moisture damage to the ends of the joists after the walls have been completely insulated?
Matt,
Like most foam insulation, Bora-foam is considered combustible. Their tech sheet says that is "must not be exposed to sources of ignition." In code speak, this means that if the crawl space is accessible only for servicing equipment, an ignition barrier is required over the foam. If there can be any storage in the crawl space, a thermal barrier is required.
Thanks Peter, I'm having a hard time finding a supplier where I can get the faced foam like thermax locally. The box stores like Lowes and HomeDepot don't seem to carry or ship it near me in Richmond, VA. Do you know of a good supplier for one of the faced foams that ships it or is near me?
You should read below, particularly the section containing "The best insulations to use are foam based and should allow the foundation wall assembly to dry inwards." Ie, no poly on the walls.
https://www.buildingscience.com/documents/information-sheets/crawlspace-insulation
Jon, I read through the article but am a little confused by the mix of information online. Assuming I ignore the requirement for ignition barrier and use a more vapor permeable foam on the walls like formular (semi permeable), is the thought process that it would allow any moisture in the joist ends to dry inwards?
Yes - brick, mortar, wood - they are all drier with some ability to dry inward.
For maximum drying capacity use unfaced EPS (white, macroscopic beads, like a beer cooler), not XPS like Foamular which as lower vapor permeance, and is blown with climate damaging HFCs, and ends up at the same thermal performance as EPS of similar density & thickness after several decades.
Type VIII roofing insulation is often available on the reclaimed goods market for a fraction of the cost of virgin-stock, and 3" would get you to current IRC code minimums or slightly better. Use foam is perfect for cut'n' cobbles, where a few corner dings on the full sheet doesn't present a problem.
Fiber face polyiso works too, but it's about as tight as 2" XPS due to the facers. That's not terrible, but you may want to leave 2" clearance around the embedded joists for drying. It's more readily available on the reclaimed goods market than EPS in my area, and maybe yours too:
https://richmond.craigslist.org/search/sss?query=rigid+insulation
https://lynchburg.craigslist.org/search/sss?query=rigid+insulation
If the foam is the only insulation it doesn't take huge expense or a lot of additional work to glue half-inch wallboard onto it using foam board construction adhesive. Then you'd have the thermal barrier against ignition.
Don't worry too much about the brick Not drying out around the joists. I work on homes over 100 years old and any with this style stay dry. Brick really doesn't wick water like cement. I think because brick is so porous. I would leave a little space to ensure this in all directions.
I had not read Martin's article--it's a really good one for this topic.
In my own home, (see this GBA Green Home case study: https://www.greenbuildingadvisor.com/green-homes/deep-energy-makeover-one-step-at-a-time), I had to deal with very similar issue: first floor joists let-in to concrete masonry block. No capillary break between the wood framing and the concrete block.
While it is possible to get wicking from ground water all the way up through a concrete foundation to the first floor framing, this is just rare. What is NOT rare is to have splashback at or near grade wetting the top course or two of block, which then wicks water to the floor framing. So, surface water management at grade is really important. This was certainly the case for my home. I managed splashback on the block and now 19 years later, when I test the floor joists they are the same moisture content as floor framing not connected to the block: dry.
Peter