3-D Networks, Premature Shingle Failure and Ant Farms

homedesign
| Posted in Energy Efficiency and Durability on
(In no particular order)
http://www.buildingscience.com/documents/insights/bsi-056-leiningen-versus-the-ants-redux
GBA Detail Library
A collection of one thousand construction details organized by climate and house part
Search and download construction details
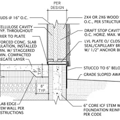
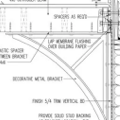
Replies
See caption to Photo 6 of the Insight Article(reverse flashing)
"the sheet metal should have been tucked under the furring strips..."
I see this same problem with many of the BSC and GBA window details
I have pointed this out to GBA and BSC in the past
https://www.greenbuildingadvisor.com/community/forum/energy-efficiency-and-durability/12411/flashing-details
https://www.greenbuildingadvisor.com/community/forum/gba-pro-help/12435/problem-not-scale-details
All this plastic is nauseating. Dr. Joe's jokey bedside manner does not inspire confidence that he's really got this figured out. I'd like to know how widespread it is for ants to invade foam.
All that bituthene seems way over-the-top.
No wonder Herr Chlupp has been moving towards less-foamy approaches to building.
I like Joe's humor and I applaud Joe for experimenting and reporting his failures.
I don't think the "perfect wall" and the "perfect roof " are elegant solutions
I was once attracted to the "perfect concept".....
The Force is Strong
I think the Euros, Chlupp,Hulstrunk and Riversong are on a better track.
Riversong used to quip that the Perfect Wall earns its name by requiring perfection in the installation and detailing, or else it will fail. There may be some truth to that. I agree that it's helpful when people document failures--that's why this website is so much more interesting than say Dwell magazine, which tries to present every project as an unequivocal success. My concern here is that the new Perfect Wall reduces risk through brute force, adding ever more sticky membranes and now PVC trim. Maybe if Dr. Joe were a structural engineer his walls would be 2" thick steel plate. It might work but isn't a good example to follow.
I found this article very helpful. I have been looking at the PERSIST and REMOTE building methods for creating and insulating a workshop, and better understanding how walls and roofs with exterior rigid foam insulation perform in practice is very enlightening.
See https://www.greenbuildingadvisor.com/blogs/dept/musings/getting-insulation-out-your-walls-and-ceilings for more details on PERSIST.
Luke...
Moisture and water vapor is of your FATHER. Welcome it. Make your designs work with it. Your structures can not resist the FORCE of vapor drive.
H2o permeates everything any everywhere. It seems un-natural to me to make more and more elaborate shields to keep it out. New water and vapor impearmeable peel and stick or foam solutions are clashing with wood. Sure- you can try and keep all forms of H2o out... But by the same methodology, once it gets in... You've trapped it.
The unseen and awsome power of "THE FORCE" will triumph. Accept it. Allow water into your being.
Ok... Goofy enough language. I blame it on JB.
These Vapor tight membranes are not the layers you're looking for
move along...move along
Nerds ;-)
I like to call this kind of assembly a "lobster trap."
Working with water.... a grand idea.
I am concerned about some of the details in the new membranes. He has peel and stick both above and below the roof insulation, and then he puts more on the upper roof sheathing.
Won't there be trapped moisture in the roof insulation? Once the water gets in, I don't see how it can get out? I suppose that is what you mean by "lobster trap".
Any way to contact Joe to find out why he built a lobster trap?
Clement... I think the point of this thread and of Joe's assembly is to go full force against "lobster trapping" the moisture. Like we did in Afganistan... w/ MRAPs... and if yaa watch the news... the MRAPs are still able to be blown sky high..... just takes more brute force and determination.
The same with the pesky ants and water at Joe's... it's a battle style... that if you have enough money you may win more often but when you lose... oh will you lose big time.
So... yes Clement... yes you are right... but for now... Joe... is not going crazy wondering about where is occasional ant is coming from!
Anyone care to guess the cost of the barn renovation? $100,000?
Payback?
CO2 analysis?
A new FHB article about the same project
Free at BSC
http://www.buildingscience.com/documents/published-articles/pa-foam-shrinks/view
from the FHB article:
"Clearly, there were more issues with this
building than just the shingles and the foam"
The foam issue and other issues are discussed in the Article
The Shingle "Issue" is never addressed.
Was it really just a Vanity/Fashion Issue?
Choosing the wrong product..... Dark Green Shingles for a "look"
Were the shingles merely poor quality?
Did all the shingles "fail"...or was the failure concentrated in a certain area?
Was the Shingle Issue related to the Assembly Design?
Was there a "perfect storm" of conditions that caused the shingle failure?
My observation (Summer Camp 2010)... the "toasted shingles" were confined to one area.
It was a South-West facing Roof Slope.
However, not all South-West facing shingles were "toasted".
The concentration was a part of the roof that was shaded by the Main House in the morning.
Could it be that once the sun came around ... the top side of the DARK shingles was rapidly heated while the bottom side of the shingles was relatively cool (thanks to the superinsulated compact assembly)?
While the other (unshaded) Southwest shingles were slowly preheated ...and did not experience the same rapid stress?
As Mr. Brooks has mentioned the force is strong; for me open service bays, simple framing methods, minimal thermal bridging, simpler air sealing details and a"rain" screen for walls and roof are a big draw. Foam and impermeable layers are just the opposite.
So, what about using this basic idea with more permeable materials for a wall/roof like this, inside to outside: drywall (not ADA), PERSIST style framing cavity with utilities, OSB/Plywood sheathing sealed as air barrier, housewrap installed as water resistive barrier (WRB, not sealed as an air barrier), rock wool (i.e.: Roxul Comfort Board), furring/strapping (3/4" minimum air gap, suitable for cladding), cladding.
This appears to have an air barrier safe from home owners, the potential to dry both directions from the OSB out and in. Structural framing within the conditioned space and for our mixed humid climate, where we build in the Texas hill country, a reduction of direct solar radiant gain from our walls and roof.
Bruce,
Substituting Rockwool for foam and ditching the vapor barrier
Is being considered by BSC... here is one example
http://www.buildingscience.com/documents/reports/rr-1104-hygrothermal-analysis-exterior-rockwool-insulation
Your stratagem sounds like an improvement
not-so-foamy...good
The Claddings have a drainage/pressure moderation gap/chamber...good
The whole thing can "Breathe" ....good
There is a thermal "break/gap" between Cladding and the thermal layer...good
Reduction of thermal bridging to the structure...good
Is it Buildable?...maybe... for very simple shapes
Is it Affordable?...maybe
Is it High Performance?....that depends...
How thick of Rockwool are you talking about?
I think as the "Outsulation" gets thicker ....
and the Architecture becomes more complex (fashionable)....
It becomes less and less Buildable...
especially around windows and doors
John...
Thanks for the link, I hadn't seen that.
John & Bruce,
Here is your Roxul wall. We just made this prototype in the shop to check a few details and see how our new Heco Topix Therm worked. We still have some details to work out but the method is sound.
As far as how much Roxul to use... Try 10.5"...
Go big or go home.
AJ Builder,
You have to admit. Behind 10'5" of 6.2lb density mineral wool, the OSB air/vapor barrier is well out of harms way. Even here in the damp Pacific Northwest.
Well... I guess you don't HAVE TO agree...
Albert,
Thanks for posting the images. So why such a thick block of insulation? After all, Joe L's troubles traced back to one solid layer rather than several layers with staggered joints. I would think it's best to have at least two layers, so a single gap won't go all the way through.
I'm a big fan of the concept of using mineral wool panels on the outside of wall sheathing.
Damn Albert,
Just think what you could do if you were passionate about what you were doing!
Very nice.
Nice Mock-ups
Nice High res photos (I rotated one for you)
Next challenge "The Betsy Pettit Dormer"
and "The Gambrel Roof with a dormer"
TJ, I'm not so sure that non-staggered thermal panels was "the problem"
the problem was lack of an air barrier
non-staggered joints was the original excuse..but there's more to it
In the new FHB article.. Joe admits that he had a dumb primary air barrier
http://www.buildingscience.com/documents/published-articles/pa-foam-shrinks/view
nevermind ... I am rethinking my comment
Albert,
Looks really good for a "batt" assembly ;-)
TJ,
This is still in development. The idea with the big blocks is that it's a faster build because you handle less pieces. It's easier for us than you'd think because this version is built flat in out prefab shop.
Your "gap" issue is well put. That's part of the next step in design. I first wanted to see how the screws work in this thickness. They work great. That's a story for another day.
Your gap issue is the next step I'm dealing with. Our vendor here in the Pacific Northwest has some new CNC cutting equipment and tell me that they can cut some joints pretty efficiently. Imagine those big blocks with an alternating rabbit joint like old time shiplap. Or a tongue and groove joint like wooden flooring (I just have to make it complicated.).
I should be done sometime this spring and our shop will publisher a white paper and detail sheet. I'll send a copy to Martin and perhaps GBA will find room for a guest blog on it.
JB,
Where do I start?
The only thing "batty" about this is me. :)
Shapes... It's just thick. As long as your dormer doesn't need to be more that 8" wide at drywall... We're good! Gambrel? What's a Gambrel?? OK... I see you are holding my support (from last year's Q&A) of Besty's good sense to employ "joy" in design. So... It's just a shape. I guess it would be easier if it was thinner and maybe foam. -Only because we are more familiar with that. However, when the Gambrel comes, we'll hire you for the envelope detailing. That way you can answer your question (also because I have no friggin idea.)
Let me know when you make up your mind on the edited (again...) comment.
Passion? I really do need to "get a life" I keep slamming my head against the same damn rock wall. Problem is that at 6.2 lbs density it doesn't hurt so I keep doing it. Perhaps this is what prozac is for?
Albert, this reminds me of joking with people on a job site about bales of cellulose--that would make a nice wall, why not just stack them up? With your megablocks of rockwool that would almost work.
TJ,
It's pretty fun to reach this far out. Obviously it doesn't take much to make me laugh about this one also. It is like playing with big blocks.
I can't really take too much creative credit. This is actually a common European build. It's what is typically applied to a Cross Laminated Timber building. All I'm trying to do is make a system to apply it to our stud walls. The issue I face is with a CLT you can run a big long screw anywhere. It's like one big 3 1/2" piece of plywood. On my prototype the screws go into the flat 2x4 that acts as a ledger along with a broad face to receive the screw. We used a 300mm long Heco Therm Screw on it through the 1x4 + MW and into the ledger. It worked well and didn't puncture the OSB air-barrier.
In the below pictures is CLT building. You can see that the face of it is taped and has some blocking for structural attachment of accessories. The Wood gets insulated and the concrete garage and brick stairwell is thermally broken. Most of the garage is full of Mineral wool and a few pallets of pink EPS.
it's fun to think of these things in a new way.
WOW! John was really making me think about modified larsen trusses filled with cellulose again, but this is beautiful. Fire resistance, thermal mass and an R45 wall until you punch holes in it with windows and doors.
Since my supplier hasn't even figured out how to get 3" Comfort Board panels bigger than 2x4, I can't imagine having cut blocks show up on our jobs. Thanks for posting Albert. I'll follow your progress with interest.
Go Big- I was thinking here in the Texas hill country of using 6" on the walls and 9" on the roof. Though for super insulation you'd really need more like 15" on the roof.
My thought was that if you constructed a metal roof atop a radiant barrier, vented 1-1/2" air gap and then your 9" of mineral wool the radiant break would reduce the amount of insulation needed. Frankly, with our solar gain here I have been wondering if adding the radiant barrier to the east and west walls would be a good idea, too.
Those screws are awesome, (I obviously haven't priced them yet), too. Albert thank you for helping me answer so many questions.
Albert,
I am guessing that you are counting on doing a lot of off-site prefabrication with your system.
It looks like a system that will require a lot of precision and preplanning.....CNC etc
Sort of like a much Impoved SIP
It is probably not meant for the "stick builders"...because we can't go to the lumber yard and buy "AutoCad 2x4's", we don't build perfect foundations and most of us are not as precise as you are.
I am not a fan of the Innie windows.... because you will have to fabricate a piece of furniture to encase every window and door....with multiple nodes of failure possible.
but again ... if you are prefabricating off-site and you have CNC .. then it could work for you.
Also...it looks like you could easily do outie windows with your system.
I am curious what you have in mind for the roof assembly.
Is it basicaly the same system tilted?
John and Albert...
I've seen videos from Germany with folks using these blocks field cut with a serrated knife rather than the CNC approach.
I can appreciate the desire to handle less pieces, but I think layering 3" panels would provide a better thermal blanket and help still air movement within the blanket.
Bruce, I have seen those videos too.
I noticed on one video that they hand cut the blocks and used only one layer.
They did have good airtightness at the sheathing and then they wrapped the Rockwool with "Wind-tight" Tyvek.
I think with one very good air barrier and a good wind barrier that perhaps the gaps between rockwool are not such a problem.
https://www.youtube.com/watch?v=wBQHBr7zn0M&feature=related
I think in this particular video that they may have a primary wall with cellulose and then the rockwool layer is in addition.
John, the wall in the video uses a low density mineral wool, probably ~2 PCF. That's why they needed to fit it between framing, and to add the wind-block layer. It takes a higher density panel (6-8 PCF) to allow a continuous wrap with strapping on the outside. I'm not sure how significant wind losses could be for high density wool without a wind block. You can certainly blow air through 8 PCF material. For a windy site it might make sense to put housewrap on top.
Thanks TJ
Have you had a chance to build with outside-rockwool yet?
Or build a mock-up?
John, I have something in the works that will use 4" high density (8 PCF) Roxul, with 1x strapping on top. I made some mockups with squash block strategies (aiming to use lower density rockwool) and have one that's pretty cool, but it wouldn't be easy to build. Continuous insulation just makes more sense, and the word is getting out that you can use dense wool as an alternative to rigid foam.
Albert's mockup is provocative--it helps to give a sense of possibility about high R-value assemblies. Lumber yards are selling foam sheathing at 1/2" and 1" thick, and I imagine people saying, gee do I need a whole inch? Folks should spend a minute looking at Albert's 10" blocks. Then it gets easier to say, let's do four inches. My project starts with a 2x6 wall and only 4,500 HDD, so it wouldn't really make sense to go any thicker (12" assembly and R-36).