A few questions about a new house build in KY

Hi, fairly new here, reading a lot, but trying to sign a contract in next two weeks to build ~ more or less, this house: http://houseplanit.com/plans/655653/655653-Traditional+1.5+story+home+with+4+bedrooms+and+3+bathrooms.htm
Briefly, it is a 1.5 story, about 1600 ft2 down (adding 2 ft to width for front entry garage and master closet mostly), 9 foot ceilings (not the mix shown on website) save the vault in the 15×18′ great room; 680 ft2 upstairs, 8 ft ceilings.
This will be in Lexington, KY (center of state, usda zone 6b.
The house will face nearly north (about 15 degrees towards east off of north) and have a lot of glass on the south/great room side) – But can’t afford solar right now.
Electricity … need to double check but believe it’s about $.065/kwh.
Our habits are to be, more or less, at 72F year round – sometimes I can get her to 68F on winter nights; little use of windows due to both of us having allergies. Please don’t suggest different settings, I understand those savings, it is what it is.
My wife needs everything on one level and we are empty nesters; I may have my office upstairs, but the goal is to be able to pretty much shut off the upstairs (3 bedrooms/bath; halls are open to great room below) unless we have guests.
I will install Aluminum radiant barrier in the rafters; I’d like to do the outer sheathing, but this may not work out (also I hear this kills cell phone reception, not an option as I work at home when not travelling).
EVERYTHING I see here in new builds uses Aluminum flexible ducts.
I am an engineer, have had a few houses built but it’s been over 20 years, so out of touch with current practices.
————————
Currently two different builders spec 2 separate heat pumps, 13 seer (I’ll go higher, but moderate zone probably means not much considering payback); 3 ton down, 2 ton up.
My few primary questions, since I need to spec things very soon:
First – and this is my primary question: What would be the best hvac solution here? I sense the pro community in this area adopts new things slowly, but if I get a strong consensus on a superior solution, I’ll see which of these guys I’m bidding will let me work with a contractor that will do that; seems silly to miss the chance before walls are up.
– I’m trying to get them to one unit by adding mechanical chase; last house I built – 2 story of nearly same ft2 and features this worked well, I had dampers in the separate upstairs and downstairs returns and just switched the bias on them late fall / late spring and this really seemed to keep temps even top to bottom. Yes, I know most say airflow is most efficient, just saying this worked really well comfort-wise. Again, I hope to largely shut down the 2nd floor, BUT do want a reasonable recovery if I decide I need to use it – a couple hours, not half a day… unless it’s 95F + …
– I’m reading about minisplits… just too much to figure it out in short time frame. I think about at least using them for upstairs, but wonder if the evaps can be embedded in walls so they don’t stand out so far, would like to be able to turn them on from one location vs going to each room, etc. I’m not lazy, I will read and search here for answers, but often on forums like this searches yield wide and shallow results or too many conflicting results for a non-pro to sort out. But I will be trying to do that.
2. What are the 3 things I should do to ensure the house is tight? I’ll have Anderson 200 windows or equivalent; Higher cost windows don’t appear to pay back here with moderate climate and cost of electricity. Fairly moderate here, but it has been near 0F several nights this month (not normal) and 95F is very common in August, some years may have 5-10 100F days. I’m costing XPS sheathing, but it complicates construction, not a polyiso fan. I am very hands on; will be reading more about HERS recommendations/methods, etc, will check and remediate / caulk myself after contractors are done, etc. I read something about sealing different air spaces, will try to find that again…
Any help appreciated.
ADS
GBA Detail Library
A collection of one thousand construction details organized by climate and house part
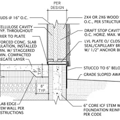
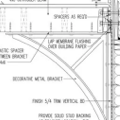
Replies
ADS,
I'm sitting here trying to figure out why no one has yet responded to your entry. I guess it's because you wrote a book--better to keep questions short and to the point.
My first thought is how could somebody come up with so much HVAC load in Kentucky with 2300 sq. ft. in a new house that you intend to make pretty air tight.. 5 tons? It's pretty easy to come up with a load much less than that. I am in zone 4 close to zone 5 (12 degree F design temperature), have a 1450 ft. sq. house on which I did a deep energy retrofit (superinsulation and air sealing). I went from a single 3 ton central heat pump to a single 1 ton ductless minisplit for heating (on the first floor, only) and then we turn on another 3/4 ton unit upstairs for hot humid summers.
I am completely sold on minisplits. They put out heat like a car heater, and I never heard anyone say they felt heat like that out of a central unit. SEER is easily 25 or more these days--I have 27 SEER.
HPSF is 12 or so, by memory (Fujitsu 12RLS2).
There's no big secrets with using minisplits, but you want an open floor plan and, I believe, a much lower HVAC load then you are talking so far. The reason for that is because point source heating (like a ductless minisplit or a woodstove) or cooling works much better if things are really tight and superinsulated. Natural, convective distribution is better with superinsulation/air tightness. The age-
old problem of an upstairs being hotter than the downstairs in winter, causing thousands of people to install separate upstairs/downstairs central heat pump units, ALSO LARGELY DISAPPEARS WITH SUPERINSULATION/AIR TIGHTENING. My upstairs/downstairs temperature differential is better now, with superinsulation and a single heating minisplit downstairs, than it was before, with a leaky, poorly insulated house and a ducted central heat pump unit.
As far as "embedding the evaps," nah, don't do that. I have no patience for anyone who can't handle the aesthetics of a wall cassette. The efficiency of the ductless minisplit, the fact that you don't have dust dragon ducting running around everywhere and floor registers getting in the way all the time, make the little bit of aesthetic sacrifice well worth it.
I'll second what Sonny said. Minisplits are truly amazing in the right house.
As far as tightening the house
1. Use EDPM construction gaskets under the sill and wall plates
2. Concentrate on air sealing every tiny hole between the living space and the roof
2a use good long lasting urethane caulk
2b buy and use a $35 foam gun (from EFI.org if your local hardware doesn't carry them yet)
3. Do a blower door test BEFORE YOU INSULATE so you can find the leaks and fix them. Doing one afterward is interesting but won't help you at all.
4. Aim for 1ACH50. It is very doable if you pay attention,
Lastly: yes, it is well worth it!
Thanks folks. sorry for long original post, trying to show all building details I thought might be pertinent. Turns out an architect (we're on trustee bd for an old bldg together) is an expert on this stuff. Builds affordable housing, taped osb "boxes" around nearly everything, 1' wide walls, etc. He was very helpful last night. Confirms what you all say: work on air leaks, best money spent.
Bob, I've heard of smoke tests, I'll find out how blower door tests are done, I like that idea a lot, thanks!
2A: urethane caulk - same or different than the PUR low expansion foam shown with the guns on EFI?
even here there are 10 choices with not a lot of differentiation! Guess everything is that way these days.
Since you are (rightly) putting any duct work inside the insulation and pressure boundary of the house a radiant barrier buys you LESS THAN ZERO in a KY climate, costing you a tiny increase in heating energy use beyond the pitifully tiny cooling saving. The only time radiant barriers have a significant effect is when the insulation levels are low (or absent), and with uninsulated cooling ducts located in the hot attic rather than inside of conditioned space.
Apply the radiant barrier money to air-sealing and deeper attic insulation. Even at R30 attic insulation, as long as the ducts are all inside, the largest cooling loads are going to be from windows. South facing window gains can be seasonally tempered with awnings or eave overhangs, but west facing window area is best minimized, since the gain of the low hanging sun occurs at the hottest part of the day, causing peak loads to soar.
But R50 cellulose is still a worthwhile level of attic insulation.
It's still possible to get significant differences in cooling loads between upper & lower floors even in super-insulated houses, since shading factors are generally higher at lower levels than higher up, and convective forces indoors isn't working in your favor during the cooling season. It's common for even super-insulated houses to have two mini-splits, one per floor.
The USDA climate zone has no relevance to your HVAC stuff- from a D.O.E. climate zone point of view you're in climate zone 4A:
https://www.greenbuildingadvisor.com/sites/default/files/images/H-T%20Zones%20with%20Cities%20ABC+.jpg
Rather than XPS, go with EPS- it's cheaper per unit-R, and unlike XPS it's R-value doesn't diminish over time. XPS is blown with an HFC soup- the bulk of which is HFC134a (automotive air conditioner refrigerant), which is an ultra-potent greenhouse gas (about 1400x C02). Most of that leaks out in the first 30 years, and as it does the R-value falls with it. By 50 years XPS and EPS of equal density have about the same R-value. But the EPS was blown with pentane (at about 7x CO2 greenhouse potential), most of which was gone before it hit the distributor's racks.
If you have a lot of air sealing to do, the 12 board foot FrothPak 2-part foam kits (about $40 from the blue or orange box-store chains) is worth a case of 1-part gun-foam cans.
If if the price of solar is daunting now, it won't be in 10 years. Give at least some consideration to your site orientation and roof pitches for future PV. In hot markets like some parts of TX they're expecting all-in turnkey costs for small scale grid tied rooftop solar to hit the $1.75/watt range (before subsidy!) in 2014, and that's likely be considered on the expensive side by 2020. The average cost last year in Germany was about $2, (and it's not because their labor rates are so cheap), where it's a mature, streamlined. and competitive market. Net metered at full retail in a place with as much sun as Lexington that would come in at roughly 5 cents/kwh on a lifecycle basis at the $2/watt price point. At a retail price from the utility of 6.5 cents you can afford to wait, but this stuff is going to be dirt-cheap by the time this place would need to be re-roofed.
Thanks Dana. The lot is very small, not much flexibility in orientation, but front orientation will be no more than 20 degrees east of true north. I won't spend money on Solar panels now, but the orientation and roof profile and pitch are near ideal for when the time comes.
I'm aware of polyiso deteriorating in r value over time, hadn't read that about xps!
Thanks for the info on the 2 part foam.
ADS