Critiques or Suggestions for this Wall / Roof Assembly

Hello,
I’m working on a home design and wanted to ask for any constructive comments the community might have. We are looking to build a very well-insulated envelope with a straightforward process that most building crews could implement. Cost is not the primary factor, insulation-value and durability is. This is in climate zone 5.
I’ve attached my first pass at a shingle roof (RF-1) and stucco wall (PL-1). The basic concept I am working with is that the exterior Zip sheathing on walls/roof is our water/air barrier that will dry to the exterior. The interior side of sheathing and framing would be coated in a generous pass of closed-cell spray foam, creating an impermeable air layer. This prevents the condensation issue of interior vapor reaching the exterior sheathing. Extra space in the cavity would be filled with readily available batt insulation.
Walls get Zip R12-Sheathing for the thermal break. The roof gets a layer of rigid foam on the interior side for a thermal break. I looked at options for applying foam to the roof exterior (nailbase, for ex.) but I thought it would be simple and hard to mess up the continuous seal between the Zip R wall sheathing and Zip roof sheathing if I kept it exposed. Would it be problematic to layer additional rigid insulation on the exterior roof sheathing as it would inhibit drying?
I’ve attached some detail drawings showing what I currently have.
Thank you!!!
GBA Detail Library
A collection of one thousand construction details organized by climate and house part
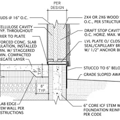
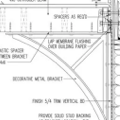
Replies
You generally design SPF out of a new build. SPF is expensive, not the most environmentally friendly insulation and there are simpler ways to air seal.
For example, in your walls, if you go with 2x8 HD batts and skip the SPF, it would get you pretty close to the same R value (~R38) but cost much less to build. Very easy to air seal the sheathing with tape or mastic which you are already doing for the continuity of the WRB on the ZIP. In zone 5, this assembly would need some vapor management, something like one of the smart vapor barrier on the interior would work.
The thicker zip needs a special framing nailer, make sure your builder knows. It might be simpler to go down to Zip R9.
For the unvented roof, you do need the SPF, there I would skip the interior foam and change the rafters to I-joists. The thinner web on these has much lower thermal bridging negating the need for the rigid plus you get more effective assembly R value out of your SPF. You can bump up your fluffy to make up for the extra R value as long as you maintain the ratio of 40% overall R value for the SPF.
Thank you Akos, your suggestions seem very appropriate. Just so I fully understand, can you elaborate a bit on the '40% overall R value for the SPF' rule you alluded to? I'm not familiar with it, but it seems like you're suggesting that the insulation in the cavity should be 40% SPF and 60% batt or eq. (all in terms of R-value?)
That is correct for roofs. You can read about the ratios needed for walls and roofs here:
https://www.buildingscience.com/documents/building-science-insights/bsi-100-hybrid-assemblies
Walls are more forgiving. There with the proper ratio of rigid/spf and fluffy painted drywall is sufficient for vapor control and you can skip the warm side vapor barrier. If you have less than the ratio in the table, you need a class I warm side vapor barrier.
Stucco is not a forgiving cladding, you are on the right track by including drainage in your assembly. Also make sure the flashing details around openings are handled properly, these are easy to get wrong requiring very expensive repairs down the road.
Thank you Akos, I appreciate the article. Would you agree that the intent of the code is to establish -minimum- % for the spray foam so that it functions sufficiently as a class II vapor retarder? So, for example, if my ratio of cc spf exceeded the 40% req'd in the table it would be just as well? I am contemplating 4" of cc spf which has a permeance of .11 at that thickness. I've attached a snapshot of the wall and roof details I'm working on.
cc SPF above 2" is a class I vapor retarder, very little moisture moves through it.
The SPF serves two purposes in most assemblies. It brings the temperature of the first condensing surface (ie the SPF towards the interior) above the expected winter time average dewpoint (thus more SPF in colder climates). It also prevents interior moisture from getting to the exterior sheathing and condensing.
Since most compact roofs have shingles or a membrane which are not vapor open, you really need both functions.
The one issue with your stackup is that with interior rigid your roof has no way to dry. It would probably work, but one skipping the interior rigid is more robust.
Walls usually dry to the outside through the siding so there are more ways of dealing with condensation and vapor control. This is why you can get away with walls with all fluffy insulation or walls that don't have enough rigid/SPF for condensation control.
Thank you Akos, I really, really appreciate the input. I'm definitely going to switch out the XPS layer for EPS or Polyiso as I understand these are much more permeable as well as environ. friendly. I thought to add that layer for a little bit of thermal bridge mitigation but it is obviously creating a double layer of vapor impermeable surfaces which is a no-no.
As I suggested earlier, I would go for I-joists and skip any interior rigid. Around me for long spans, I-joists are cheaper than larger dimensional lumber, plus most cases you can go for 24OC.
If you want to keep the assembly as is, unfaced EPS is probably your best bet.