Choosing a Foundation Type

I’m grappling with what to choose for the foundation / basement of our home. We’re self-building a rectangle 1.5 storey home in Climate Zone 6, and we had originally thought that we could do a simple insulated slab on grade (either a raft or monolithic FPSF) foundation, since we didn’t want/need a basement. The idea of a simple foundation with limited excavation and minimising concrete was appealing from both an environmental impact and cost point of view.
It turns out that because our site slopes down about 7% from the highest corner to the lowest corner, we’ll need to bring in engineered fill to build it up for a raft or monolithic slab. We have the additional problem of a very large tree in the middle of the house footprint, which will leave a large hole and disturbed soil once we pull the stump, and preliminary conversations with engineers have warned us against different soil substrates (since it leads to differential settling of the foundation), so it sounds like we’ll need to dig a big hole for the whole house footprint and grade it with engineered fill just to build a raft or monolithic FPSF slab, therefore making it a much more expensive option that we originally thought.
Now I’m looking at concrete frost-walls with an internal slab. Since the bedrock is between 75 – 100 cm below grade, it seems like a good option could be to pin the stem walls to the bedrock, eliminating the need for footings. Based on my research, we’d then fill inside the four concrete stem walls with engineered fill, then lay rigid foam horizontally under the interior slab and vertically on upper part of the inside stem walls (which will connect the horizontal under-slab insultaion to the vertical insulation in the stud walls), a vapour barrier and then pour the internal slab on that. This type of construction should eliminate the need to use engineered fill to grade the site, since we can just build the stem walls higher to match the grade highest point. Does this type of foundation make sense for our site, or am I making it too complicated?
I was also advised informally by an engineer to insulate the outside of the stem walls and add insulation skirting around the base of the stem wall to prevent forst heave. I thought frost heave was a problem in the soil not in the bedrock, so to me this doesn’t make sense since if the stem walls are pinned to bedrock, what are we trying to keep warm?
Finally, I was reading about something called a ‘baby basement’ (from Glatthaar Keller) where a portion of the area underneath the ground-bearing slab is a basement. I also saw an episode on the Build show network where they did something similar and called it a ‘hybrid basement’. I think this could be interesting because then we would only need to fill a portion of the foundation with the (expensive) engineered fill, and also utilises only the deepest area without needing to blast or jackhammer the shallower parts of the bedrock. I’m not sure about the detail of the basement ceiling / house floor though. I was assuming from the Glatthaar drawings that it would be concrete poured at the same time as the rest of the slab, but then how would the continuous insulation layer work, and how would the floor be supported above the basement? Has anyone done this?
…and I will be consulting an engineer – it’s required to have stamped drawings from an engineer for slab foundations in Canada – but I would love to hear experience from the GBA community to help guide my conversation with the engineer.
GBA Detail Library
A collection of one thousand construction details organized by climate and house part
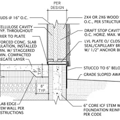
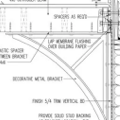
Replies
HolzHausKT,
Hopefully you will not find this TL/DR.
When building our home we faced a similar set of questions and decisions to be made. We thought the bedrock would be tilted similarly to the overlying soil. As it turned out the final elevation difference from highest to lowest point was almost 5 feet over 50 feet (approx 10% slope)and soil coverage was 4 1/2 feet to 6 ft. Due to the need for septic tank and field placements, we were thrilled to have that much soil above the rock.
If you are facing roughly 3' of soil cover as a maximum, you may be facing additional issues beyond deciding on slab details. Maybe your frost line is shallower than my 42" level and you can use the build up of exterior grade around the foundation to your advantage. Even if you have public septic and water you will need to be mindful of the freezing risks. You will also need to be aware of drainage issues around the rock/soil interface.
FWIW, when first setting out to build on our lot, we were advised to avoid getting involved with soil engineering and pray for bedrock to be within our desired depth. This was partly due to the frequent presence of expansive soil layers in our area and partly to the inherent expense of all the testing, digging, replacement materials and compaction labor costs, etc. The same issues are involved in my current build project. You have indicated soil engineers and the mitigation costs in your region are pricey. Excavating can be the more economic choice even with the taller stem walls needed. Ironically, the expansive layer both times has appeared only a foot or so above the bedrock, so any soil engineering and infill would be somewhat silly for my sites. I do face having some very tall basement walls though.
Pinning a wall profile to the stone is a choice our engineer did not make. Our engineer specified full footings despite being on "bedrock". Our sandstone is prone to fracture lines and layers, so perhaps you are "lucky" and have granite. Either way, do be aware of how water will track the rock layer and plan for above average drainage networks. Spring melts here go down into the soil and then track the rock layer, often on multiple paths due to the fractures and layers. The presence of exterior footing drains around the foundation walls only addresses part of the water issues here. I made very sure to clean the bedrock face under the footing profiles and inside the foundation perimeter. Perhaps the rough surface of the rock face was sufficient for ensuring secure footings without pinning. A heavy film of dirt might act like a bond break or crack membrane as tile people use. In any case, my concern was to not leave enough muck on the rock to choke my drainage plans.
The inside of the foundation area is connected to the lowest point on the outside footing drains and because the grade continues on down even faster, to a daylight exit. Aim your drainage to the lowest point on your lot if that doesn't endanger any neighbors. My witness pipe in that corner has confirmed my suspicions that spring melt water does indeed travel in the rock layer, which freely passes under the footings and completely bypasses the exterior footing drains. I am grateful for the continuing down hill exit line.
Due to our much higher soil depth, I have about half of the basement footprint as a full height (8') shop that is dry and reasonably cozy. To achieve good drainage and allow for pre-emptive radon piping installation, I had the contractor install only washed rock (sometimes called gravel by others on GBA?) to level the inside prior to placing sub-slab insulation. I would urge you to consider the same course of action. The cost differential between washed rock and compactable engineered fill was less than I expected and the compaction of the rock was done in larger lifts. Plus I still would have needed 6-8" for the radon pipes and provide a capillary break from the compacted fill. With your relatively shallow bedrock you may find the total thickness of layers for slab, insulation, capillary break and possible radon piping to make compacted fill a fussier choice. The pitch and depth variations across the house foot print will dictate a lot of those choices. From the information provided, I am not sure how you would get a hybrid basement to work out. Just the same any height that allows for water heaters to leak away from finished floors is a bonus.
In my opinion only, I would be very leery of using a compacted fill inside the foundation based on my experience. Had I let the original plan proceed, my lowest corner of rock would have about 2 feet of soil above the drain link to the exterior footing drain with the overall area of compacted soil being roughly 50% of the total footprint. Given the spring melt situation, all the soil would be acting as a giant sponge and resistor of water flow. It will remain unknown if the water buildup inside the foundation would have ever managed to exceed the rock bed under my slab. I at least rest easy now knowing that the spring build up stays well down in the washed rock layer and six years out, the pipe is free of mud.
As to insulation, I went with outsulation on the foundation and house. 3" reclaimed XPS all around the outside and under the slab. Frost wings were moot given our depth of soil. I have to agree, the idea of frost wings for foundations on bedrock does seem counter to common thinking, but always be prepared to learn. The downside to outsulation is application and protecting the exposed parts. More on that if you like, later.
While I have manageable temperatures in the basement, I do wish I had 4" of foam in all places. I am in CZ6B, so zero temps are common for four months or so. I do also like the fact that my entire framing assembly including the sill plates and rims are sufficiently insulated to keep them well above and moisture control issues. Insulating the interior side of a foundation up to the sill plates and then fussing with the rim pockets between joists seems like a less protective method. A poor analogy might be to imagine wearing well insulated boots with the first inch of the sole cut off the toe end. A bit chilling despite everything else being insulated.
Another detail that makes interior slabs with edge insulation somewhat annoying is dealing with the resulting gap from framed wall to slab edge. Searching GBA questions should bring up potential answers. Do plan on the slab shrinking back away from the foam and leaving a slight raised edge that will need grinding. Given that a slab will always feel cold until it is 80F plus it might be worth planning for a thin slab with crawl/partial basement. Tjoists and subflooring make a lot of sense when selecting floor finishes plus provide some access for water and electric that slabs can't. Downside is a higher belt line for door ways and siding area goes up.
Hope this helps.
Thanks for your very detailed response, I really appreciate it. I hope you don't mind, I have a few additional questions:
1) Were you able to determine the depth of the soil over bedrock before you started digging? If yes, how did you do this?
We've been hammering a long rebar stick around the site (not in the footprint yet) to get a good sample, and our septic engineer used some kind of hand auger to get a measurement - all seem to be have depth readings of around 75 cm (29.5''). I've called a few engineering companies and they all want to come to site with big machines and dig big holes (and charge us thousands) to tell us how deep the bedrock is. Almost all the nearby houses have walk-out basements so there are pretty strong indications that we're dealing with a continuous layer of sloped bedrock, but I don't want to miss a trick here.
2) Frost line - could you elaborate on your point about the additional challenges? Our frost line is at 5' (or 152 cm) so below the the depth of the bedrock (29.5'' / 75 cm) but as far as I understand the frost line and therefore the frost heave is an issue in soils, not bedrock. For the water and septic lines we've been looking at heated lines in the pipes, but there seems to be some debate if this is necessary if the pipes are sloped properly. Are there other issues here that I am missing?
I'm going to muse over some of the additional details you provided and may come back with some additional questions.
Thanks again.
HolzHausKT,
I think you have two realistic choices:
- A sloped crawlspace, which with perhaps the exception of the type of slab, gets built much like a basement.
- The hybrid, slab/crawlspace you suggest. If you go that route you will need to pour an additional stem-wall between the two and use a wood floor system over the crawlspace portion. It isn't feasible to pour a suspended structural slab. That means at the point where the two meet the floor will transition from concrete to plywood, so if you were intending to use the concrete as your finished flooring it would be pretty difficult, and that transition between materials needs some care to prevent movement. The only benefit I can see from including an area of slab is there are minimum heights for crawlspaces, so using one on the upper side of your site may necessitate either removing rock, or raising the height of the main floor.
I don't understand the necessity to insulate the stem-wall on bedrock either. It would be worth having your engineer explain why it would be useful.
Each jurisdiction has different requirements for when an engineer needs to be involved with foundations. As a general rule though Canadian building codes allow slabs with separate stem-walls under Part 9, but load-bearing slabs (monolithic ones, or with thickened edges) move the design to Part 4 which requires engineering. So depending on how you go, you may not need one.
Thanks @Malcom Taylor for the response. That's a really good tip about Part 9 of the Code, I am going to re-read it since so far 'everyone' (...or rather 3 different people) has been telling us we need an engineer.
For the wood floor system, I see a potential issue with our underfloor hydronic heating as the plan is to have a boiler stove as the main heat source (with a back-up electric boiler). Also a possible issue with the crawlspace as we are planning a barrier free entry (ageing in place...) at the upper side, so raising the slab too high to meet the minimum crawlspace requirementscould mean building a steep or very long entry ramp. I will check the measurements.
I'm curious why you didn't include packing the footprint with engineered gravel and insulation with a slab on top as one of the options. (?)
HotzhausKT,
A conventional slab with stem-walls is certainly an option. The downside on a sloped lot is that unlike a full or partial crawlspace where you can step the foundation, with a slab you will need full height stem-walls, meaning on the low side you have a lot of exposed concrete. If you go that route you need to be careful how high those walls end up as there are code limits on the height of unsupported foundation walls.
The code reference for slabs in Part 9 is 9.16.
HolzHausKT,
Finding the actual bedrock level unfortunately is pretty much only achievable with a suitable excavator. I looked into ground penetrating radar, but was told that it really doesn't function like that. It can discern disturbances in the soil profile and some kinds of soil layering but apparently not bedrock with any assurance. Not sure what to make of the archeology shows that seem to find all manner of things with it.
That aside, the size of the excavator does make a big difference. I did some test holes on my current project site with three different size machines. The smallest was about a 12,000 lb machine with an 18" bucket. It met with enough resistance to make me think I had rock at 36" on one corner of the house footprint. This surprised me as two earlier test holes with a roughly 20,000 lb machine had gotten down almost 6' only 40 feet away from the shallow hole. The final test holes we completed a few weeks ago were done with a 40,000 lb trac-hoe and (oddly) a four foot wide bucket. This machine merrily chewed down to true bedrock, which has proven to be 8-9' most everywhere. I had already paid for the trailer charge for the giant machine, so the hourly for the holes kept the cost relatively low. I can't judge what excavators can command in your area, so maybe calling more than one for "guesstimates" is the answer.
The overall pitch of the underlying bedrock is actually a bit less than the overlying soil, so you might find that the auger test holes are not truly reflective of what lies beneath. This would be especially true if you have the extremely dense packed clays we encountered at the 3-7' levels of the profile. Our geology is basically many layers of primordial beach, river deltas and landslides all jumbled up in very unpredictable ways. Some layers turned to sandstone, others crappy shale or clays that are similar to bentonite. I have at least six different profiles occurring within a 300' square. Blessedly half of that area is good for standard septic field placement.
My commenting on "other issues" was meant to be a gentle alarm bell about keeping potable waterlines unfrozen and having suitable depth and soil types for leaching fields. I have put the water line at 60" despite encountering a stretch of fractured bedrock. I could have tried laying foam board on top of the line where shallow would have been easier, but I really don't like chancing it. Heat tapes can fail when least convenient, so I would go with foam over heat tape if forced. There have been discussions on GBA about how wide the foam should be and how thick. I have seen a rule of thumb for ground temperature at 12' of depth as whatever your annual median temp is. All bets are off for the 5' and up portion. Water content of soils and vehicle traffic above a given area can radically alter what the actual temps will be. Yes the ground below is warmer, but not quite like a hot plate.
A common issue in my area is vehicle traffic across buried water and septic lines. The general idea is cars and trucks "drive down" the frost deeper than normal. I suspect that saturated soil and ice formation is the driving factor along with the loss of insulation value provided by snow cover. How it happens if less important than avoiding running water or septic lines under traffic paths if at all possible. Unplugging a frozen septic line if February is even nastier than doing one in June.
I believe code in our area demands the line from house to tank be 18" of cover, minimum 12" of cover over the tank and somewhere between the two limits for the effluent line out of the tank. Deeper is better up to a point, but that is something you must discuss with the septic engineer. If you have city sewer the more pressing issues are tree root invasion and fat-bergs. Even bath/shower water will not clear the congealed fats going down a sink, especially one with a garbage disposal. Trying to make a 30-40 foot run from the house to city line without it getting pretty chill at the pipe level is tricky. Your current perception of where the bedrock lies also means you have limited absorption capacity which may require specialized field design. It might even require establishing a completely constructed bed of sand with a pump and dump tank. Best to investigate your septic situation now before getting married to a house site.
I have some other thoughts on the foundation that might allow you to still have a near zero entry jump, but I need to tend to other things for a bit. I will get back when free.