Temporary Insulation Panels for Cold Storage

I have a tree farm in Central Alberta, near Edmonton. We have about 10,000 F heating degree days. Cold winters, warm to cool summers. Temperatures over 30 C (88 F) are uncommon, but spring temps in the 70’s are common.
I have a cold room that I use or storing tree seedlings for about 6 weeks in spring.
The building is 12×12 feet 2×4 construction, fiberglass insulation, exterior face plywood, internal face OSB, wrapped with flax straw bales on edge. 18″ of blown celluose in the ceiling. A 3 foot path all the way around is insulated with 3 layers of insulated tarps, probably total insulaiton value varying from R2 to R6.
There are eight 55 gal drums in the shed on pallets filled about 3/4 full with water. Several inches of scrap styrofoam float on top. This keeps the barrels from freezing down from the top and splitting.
During the winter, the door is left open, allowing frost to chill the slab and area under the slab. Typically there is a 5-10 degree C lag between temperatures inside the shed and outside. E.g. right now it’s -17 outside and -10 inside the shed. This lag is a combination of the water mass in the barrels, and the heat in the ground.
Come early spring I put about 3 feet of snow in the shed, then spread and pack it, giving about 2 feet of thickness. I’m guestimating a density of about 0.5. I cache snow under insulated construction tarps to top this up.
Once seedlings arrive I have a box fan in there blowing against snow. The goal is to maintain a temperature of just above freezing at close to 100% humidity as I can. I’m happy if it’s between 1 and 2 C and RH of 95%.
Using just the ice in the barrels, I can maintain about a 20-25 C temperature differential between inside and outside. Barrel walls are 1/8″ polyethylene. If we get 30 C temps (has happened once) my room temperature rises to about 5-7 C. 1 day at 5 C is about as harmfull as a week at 1 C in terms of seedling viability. The snow floor kept this rise to about 3 C on exceptionally hot days.
I’m considering removing the barrels
My snow/ice keeps very well for about 6 weeks. (3 weeks of spring, then trees arrive, and 3 weeks of storage. Then the loss rate climbs sharply. I suspect that I’m getting heat flow from the surrounding ground that finally warms up the deep frost under the slab, and starts to melt the snow from the bottom.
However, my efforts to find out what slab heat losses are resulting in vague generalizations aimed at heating situations, or math that is way above the pay grade of a simple farmer.
Is this a reasonable scenario?
Would it be worth making movable panels of 2″ styrofoam, backed with thin plywood, letting the room cool, then putting the panels down just before filling with snow?
I would like to get two more weeks storage time.
I’m looking for a short term solution — one that will last 1-3 years.
***
The present shed is too small.
I’m looking at replacing it with longer term solution using 3x4x8′ straw bales enclosing a 24×24 foot space, with a 40×40 foot roof to provide enough overhang (4 feet) to keep the bales exterior dry.
Before you start: No I cannot afford a proper walk in cooler. Numbers I’ve seen for conventional buildings with adequate cooling not only are horrendously expensive, but they exceed my farm electrical service (7 kVA)
GBA Detail Library
A collection of one thousand construction details organized by climate and house part
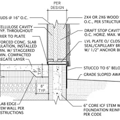
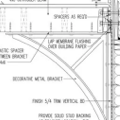
Replies
Yes, it'll be worth the insulation on the slab.
As a side note, heating is just cooling in reverse: imagine you're trying to keep heat OUT instead of IN. The insulation stuff is all the same, aside from which side you'd put a vapor barrier/retarder. All the R value stuff works pretty much the same in either direction.
I would find some reclaimed XPS to put over your slab. XPS is physically more durable than most EPS ("regular" styrofoam), so it will hold up better for you over time. Places like discountinsulation.net are one potential source, but also check Craig's List in your area since many reclaimers advertise there. Try for at least R10 (2") worth of XPS on that slab, and run a little bit up the sides too so that the snow is entirely against XPS on the bottom and on all four sides. Make a sort of bathtub for the snow :-D
The insulation will insulate the snow from the ground, which will slow heat GAIN in your case, which is what is what is melting the snow. You may want to consider getting additional foam board for your shed too. You don't really need any plywood backer if you're going to put all that snow on top -- you can walk on XPS as long as you're careful. You might want to try to find the higher density grade (like the 250 series of Foamular, for example), which has a higher PSI rating and will be a little more durable compared to the lighter density 150 variant.
As long as you can get the reclaimed material cheaply, I think this is worth doing and will buy you some more cooling time. Painting the exterior of your shed, including the roof, white will also help a little.
Bill
What you have sounds a lot like what used to be called an icehouse.
Basically the more insulation you have the less ice you need.
The basic equation for heat movement is heat flow= temperature difference * area/insulation level.
In traditional units, BTU/square foot/hour= (temperature difference (degrees F))(area (square feet))/R-value
A pound of ice absorbs 144 BTU when it melts.
So basically you figure out how many square feet of surface area -- walls, floors and ceilings -- your building has. Then you calculate the target temperature for the interior and average exterior temperature and you get the temperature difference. Then estimate your insulation level. With those values you can estimate the BTU/hr; multiply by number of hours of cooling you want and you get total BTU's. Divide that by 144 to get pounds of ice.
Then you can either adjust the insulation level or the amount of ice until you get values that work for you.
OK, so how do you estimate the exterior temperatures? For the walls and ceiling it's simple. You look at weather statistics and find the average high and low monthly temperature for your area for the months you care about, and just average them.
The floor is trickier. The surface of the earth is at air temperature, but as you go down the temperature increases. This is because the core of the earth is at around 9000F and soil has insulating value so there is a temperature gradient. Typically at around ten feet depth the soil stays at the year-round average temperature. If you insulate above the ground the ground temperature increases -- the outside of the insulation is at air temperature and the bottom of the insulation is closer to the center of the earth and warmer.
So, for a back of the envelope calculation, here's what I would do: Assume that your soil is at year-round average temperature ten feet down. Get your average local temperature from weather statistics, both annual and for the month in question. Assume that your soil has an insulation value of R4 per foot, or R40. Calculate how much above-ground insulation you have. The floor temperature is going to be given by the ration of insulation above the floor to below the floor, multiplied by the temperature difference.
For example, let's say your average annual temperature is 50F, and the average temperature for the time you care about is 40F. Assume you have R20 insulation in your icehouse. So you have R40 below, R20 above, so 2/3 of the insulation is below ground and 1/3 above ground. Ground level is going to be 1/3 of the way between air temperature and ground temperature, or 43.3F.
In this example the floor will be slightly warmer than the air so you want slightly more insulation in the floor than in the walls and ceiling.
If you post your actual numbers we can help you work through the numbers. Once you get some design goals then we can work on what is a practical design. Sounds like an interesting project!