Applying Joe Lstiburek’s Perfect Wall to a Barn Renovation

Good evening all.
Hope you are all well.
I have studied some of Joseph Istiburek’s perfect wall design and must say it is about time we stopped building inefficient structures.
I have a number of queries but first some information.
I am presently renovating a medium sized barn on my property.
The barn was mainly used for some hay storage, equipment storage and repair.
There is rot mostly in the lower extremeties of everything.
The barn was built on 8×8 sleepers nestled on a perimeter of stones and everything is mortised and tenoned.
I have removed boards at all vertical supports to access for jacking and have poured individual piers for each of 15 posts which are no longer supported by the 8×8 sleeper that rotted away under them.
The sleepers only rotted where the post bore onto them and caused some sagging but nothing catastrophic.
Enough of that.
My queries are as follows.
In order to follow the perfect wall method I have to cover the original and replaced barn board.
I live in Ontario Canada.
Do I first cover the exterior of the barn with 6mil poly as vapour barrier, then apply the rigid insulation, cover that with house wrap then apply my exterior sheathing which I think will be old style roofing metal to at least capture some of the rustic value outside?
Somewhere in this wall construction I need to incorporate a firestop material I have on hand.
It is 3M endothermic mat. Very expensive and designed mainly for the protection of critical wire chases such as elevator and comms.
I happened on 70 rolls of this material when a retiring commercial contractor local to me retired and wanted it gone from his expensive storage.
My question here is, can this Interam material substitute the vapour barrier if I put the aluminum side inward and tape the outer seams before applying my rigid insulation?
I am trying to use the materials I have gathered through 35 years of General construction and just being at the right place at the right time with enough cash and adequate transport.
Any help or suggestions are appreciated.
I have the following materials in enough quantities to cover the barn exterior.
House wrap (Typar)
1.5″ interlocking open cell rigid styrofoam
6mill poly
3m Interam E-5A-4 endothermic mat
Tuck tape
GBA Detail Library
A collection of one thousand construction details organized by climate and house part
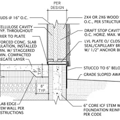
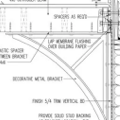
Replies
This is a fascinating project--concept wise. I'm going to give your post a bump in hopes that a seasoned builder with a solid grasp of Joe's Perfect Wall can help you out.
Thank You.
My wife has made input which changes things some.
She hopes that I could use the original weathered barn board as the finished cladding instead of metal as the barn would look like a newer pole building if I clad in steel.
I agree with her sentiment and am now looking at removal of all original board to be installed last for esthetic and historical values.
This won't change anything except what I now use as base sheathing but it does now incur some expense I was diligently trying to avoid.
The 3m stuff doesn't have any specs but it looks pretty impermeable, so it could be used for a warm side vapour barrier (your inspector might disagree though). You definitely don't want it on the outside.
If your barn structure has existing horizontal lumber between the posts, what you can do is.
install Typar on exterior face
apply foam on interior face
cover foam with 3m
paint Typar black so you don't see it through the gaps in the boards
install barn board over Typar
cover the inside with OSB
3" of foam is pretty decent insulation in your climate, if you have enough, bumping it up to 4.5" would be even better.
You can also re-shuffle this assembly as long as the layers stay in roughly the same sequence. For example barn board->typar->foam->3m->wall structure->osb.
Akos
That's good advice except painting the typar.
I think paint would seal the housewrap's one way (out) permeability.
I will clad with original barn board and strip some interior walls for batons.
Thanks much for the solid advice.
All the best.
No material is one way permeable under atmospheric conditions, all allow for moisture to move in both direction. What housewrap prevents is liquid water getting into your wall.
Most latex paints are 5 to 10 perm, while not as permeable as housewrap, is considered semi permeable. It won't trap moisture. I have done this when the budget didn't allow for one of the fancier black housewraps that are meant for open cladding and can be exposed to UV. Painting the housewrap in this case will at least offer some level of UV protection.
In your case, since you'll be adding battens, the housewrap won't be exposed to UV, so you are fine.
If you have no plan to heat and cool the barn most of what Joe is advocating is wasted on your project.
When I look at old barns most of the wall will not even keep out all the rain no less the wind. I think they survived simply because they allowed so much air movement that so what if things got wet the breeze that blows thru dried the wood before it could rot. I think the rot you did have was mostly from capillary action of water moving up thru the stone and keeping the wood wet so it could rot.
I would want to make sure you do not have wood in direct contact with the concrete and put the siding back as the way it was.
Leaky 100 year old barns are very common I am not so sure our modern walls built of “waswood” and plastic will stand the test of time so well.
Walta
Walter.
Thank you for your reply.
You are right on all counts.
I do intend to heat entire space through the winter and when I build the summer house in the top half storey I may want A/C in the summer.
The rot I have encountered IS from leaching through the tons of limestone crush a PO spread inside and out to establish a grade for perimeter and high ground inside. However with no means of drainage and the original dirt floor being crushed into a bowl by use the water just lay in the crush and the timbers wicked it up.
I was just working in a 170-year old barn today.
Barns are tough to turn into conditioned space. There's an adage, "build houses tight and barns loose." If you're not conditioning the space you want lots of air movement. When there's lots of air movement you can be less rigorous with moisture management. It's tough to take a building designed to maximize air movement into one that is essentially air-tight and moisture-tight. In a barn the exterior is a skin designed to keep out some of the wind and most of the rain. In a modern house the exterior is an assembly with a series of layers designed to control the movement of moisture and air.
So to convert an old barn into a conditioned building you're going to have to build a building within a building. First question is whether the new building goes inside or outside of the old building. Where you're going to have trouble is where the walls meet the floor and where the walls meet the roof.
I'm not saying it can't be done, it is done. But it's not simple or cheap. If you want to keep that barn feel on both the inside and the outside you're probably going to need another donor barn to provide materials. Costwise, effectively the only part of the old barn you're going to be able to keep is the framing. In a modern house the framing is a pretty small part of the cost of construction, maybe 10%. And everything is going to be more expensive than starting fresh would be.
So right.
I have decided to remove all boards.
Adding windows and doors lessens the required board footage to go back on.
I will vertically strap the entire structure on 2' centers to carry the endothermic mat serving as vapour barrier and air stop with surely something in R value.
On this I will apply my rigid insulation and then wrap entirely in typar house wrap.
Next I strap again horizontally having mitered the top edges of the strapping which will be pressure treated 5/4 x 6 deck lumber ripped in half.
Finally I apply the original boards and use extra for batons.
I have 1/3 of the barn that was a tool and work shop. I can strip the interior walls from that area to supply boards to be ripped into batons.
Thanks for your advice.
I'm glad to hear you're pressing on, the way to preserve old buildings is to keep them useful. I'd love to hear more about your project. First off, are you planning to heat or cool the building? Have you thought about how the interior is going to be finished? What about floors and ceilings?
5/4 x 6 is rather expensive here, I like the idea of treated straps but I'd go with 1x8's ripped three or four times.
Building a house you'll typically spend almost as much on windows and doors as on the framing. So think about what you're going to do for windows and doors, most old barns have lousy windows and rudimentary doors. Insulation doesn't have much point if the windows and doors are leaky.