Adding to existing baseboard heating system

First off, I’d like to say thanks to all the people out there who have contributed to this forum. I’ve learned a lot.
I’m currently working on finishing my basement and I want to add some heat down there. I have leftover Fintube from a recent renovation that I’d like to use, and I think I know what my load is (how much Fintube I’ll need to install), but my concern is with short-cycling my boiler just to raise the temperature about 10 degrees down there.
-Location: Southern Maine along the coast
-Poured concrete walls
-Newly insulated w/ 2″ of XPS, locked in with metal Z-channel 2′ O.C. (drywall will hang on the Z-channel)
-First floor above is 2×10 joist construction–thinking about insulating to cut down on noise
-Buderus G115 (95k btu) oil fired (Riello burner) w/ indirect domestic hot water
-Currently 2 heating zones + the indirect hot water
Last winter, which was relatively mild, my basement temp held at around 60 degrees F without any insulation. The heating pipes are a mix of 3/4″ copper and 5/8″ pex. The pipes aren’t insulated but I’m planning on changing that.
I did a calculation of my heating load based on last winter’s data, as Dana had described in his blog https://www.greenbuildingadvisor.com/article/out-with-the-old-in-with-the-new. I realized that In Jan-Mar I only used about 35K btu of heat from the boiler (the recent installation of a propane fireplace probably offsets about 20-30k BTU of load). Interestingly enough my calcs from Mar-Jun show a use of 45-55k BTU from the boiler. I suspect that the fireplace was used less in those months but I have nothing to back that up. It was a cold rainy spring.
So right off the bat, I know that my boiler is oversized for my current house application. However, I’m planning on finishing a space over the garage (about 700 sq ft) and adding a heating zone there. I also would like supplemental heat in the garage. The space above the garage will likely be insulated with spray foam. So, it seems that I’ll still have more than enough heating capacity for that space.
Back to the basement: Based on a quick calculation at https://loadcalc.net/ I found that my basement will require about 6500 BTU of heat. At 580 BTU/foot, I should only need about 11 feet of Fintube. And that’s for the entirety of the basement…we’re not finishing all corners of it. I’m figuring on putting 3 feet of Fintube under each of the three 31″x12″ windows.
So maybe now you can see where my question is going. With only 9 feet of heat + probably around 90 feet of tubing, I’m feeling like there’s going to be some sort of short cycling involved.
Should I put this on its own circulator pump (currently each zone uses its own 007). Or should I somehow add the basement to the end of an existing loop (like the 1st floor) with a zone valve to allow it on/off whenever it needs heat and the 1st floor is running.
Additionally, about 1/3 of my first floor square footage (15’x25′, 3 exterior walls and one bedroom) is original R11 fiberglass insulation. The rest of the 1st floor got 3″ closed cell when we renovated. This lesser insulated portion is not where the gas fireplace is, and as a result was noticeably colder. So I was considering adding this portion to the end of my basement loop with a 3-way zone valve to add to the run length and provide a bit of “boost.”
Despite all my reading/thinking/etc., I’m unsure what the right/best way to accomplish this is, while using existing parts/systems appropriately/smartly.
Thanks!
GBA Detail Library
A collection of one thousand construction details organized by climate and house part
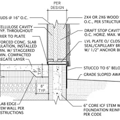
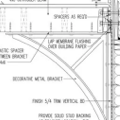
Replies
>"-Newly insulated w/ 2″ of XPS, locked in with metal Z-channel 2′ O.C. (drywall will hang on the Z-channel)"
That doesn't even meet IRC code minimum for US climate zone 6. The warranteed R-value of 2" XPS is only R9. Code minimum is R15- continuous insulation. If the Z-channel is attached to the foundation, and thermally bridging the 2" insulation it's even worse, due to the very high thermal conductivity of the steel, and the amount of steel surface area in contact with the foundation.
Perhaps you can describe the assembly a bit better, or make a sketch (or take a picture)?
XPS is also arguably the LEAST green insulation material in common use today. It is blown with an HFC soup, the major fraction of which is HFC134a (an extremely powerful greenhouse gas, ~ 1400x CO2 @ 100 years) which would be contraband as of 1 January 2019 had the US signed the Kigali Amendment to the Montreal Protocol.
https://materialspalette.org/wp-content/uploads/2018/08/CSMP-Insulation_090919-01.png
>"I realized that In Jan-Mar I only used about 35K btu of heat from the boiler (the recent installation of a propane fireplace probably offsets about 20-30k BTU of load). Interestingly enough my calcs from Mar-Jun show a use of 45-55k BTU from the boiler."
The error from both domestic hot water use and solar gains make March-June calculations much less accurate & reliable than winter data. I'm assuming by "...about 35K btu of heat from the boiler..." you actually mean a design heat load of about 35,000 BTU/hr @ your 99% outside design temperature (?), which would be about right for a tight 2500' house with double-panes and an insulated basement.
The average winter load would likely be under 20,000 BTU/hr if the design load is 35K, and the shoulder season average load would be under 15K, maybe even under 10K. Idling losses and abandoned heat on a 95KBTU/hr Buderus when the average heat load was <15K could exaggerate the numbers by that much.
>"Back to the basement: Based on a quick calculation at https://loadcalc.net/ I found that my basement will require about 6500 BTU of heat. At 580 BTU/foot, I should only need about 11 feet of Fintube. And that’s for the entirety of the basement…we’re not finishing all corners of it. I’m figuring on putting 3 feet of Fintube under each of the three 31″x12″ windows".
A heat emittance of 580 BTU/hr per foot would be at an average water temp (AWT) of about 170F (180F out of the boiler, 160F back.) Is that where you're actually running it?
I believe Buderus makes a retrofittable "smart" control for that boiler which would likely improve the overall efficiency, and make the shoulder season numbers more similar to the dead-0f-winter numbers.
I suspect your boiler is the G115/4 WS, which has a DOE output of 109K, and a net IBR rating of 95K (which is not the appropriate number to use if the boiler is inside of conditioned space, such as in your basement.) The water volume of the G115/4 WS is 10.8 gallons, or 90lbs, at it weighs 403lbs perhaps 300lbs of which is the cast iron, which has a water-weight thermal mass equivalent of another 33lbs, call it 125lbs total water-equivalent after adding in the water in the fin-tube & distribution plumbing.
With 125lbs of thermal mass and a heat emittance of 6500 BTU/hr, or (/60=) 108 BTU minute, with the burner off the temperature is only slewing 108/125= 1.16 F per minute. So even if the boiler's differential is only 10F, the time between burns would be at least 10F/1.16 F per minute= 8.62 minutes. No matter how short the burns there would still be fewer than 60/8.62= ~7 burns per hour, if serving ONLY that zone. While that's not great, it's also not a short-cycling disaster, since most of the time the thermostat would be satisfied in just ONE burn cycle, or even ZERO cycles with some heat purging boiler controls.
The BTU/hr of the burner is about 17x the BTU/hr of the design condition loadof the basement, and there's enough thermal mass in the system that the basement zone is probably the LEAST worrisome zone from a short cycling perspective. The main problem is burner oversizing relative to your whole-house load.
To emit the whole 109K at an AWT of 170F would take 175-200' of baseboard. Do you even have that much baseboard in your house? (A total of 175- 200' of baseboard could emit 35-40,000 BTU/hr at an AWT of 120F, which is domestic hot water temperatures.)
Designing the zone to deliver the heat at an AWT of 120F would only bump the total linear feet to about 30-35', which is pretty cheap in the grand scheme of things, and would put in range of using a water heater rather than a boiler, or even a reversible air source chiller type heat pump at some future date.
>"So right off the bat, I know that my boiler is oversized for my current house application. However, I’m planning on finishing a space over the garage (about 700 sq ft) and adding a heating zone there. I also would like supplemental heat in the garage. The space above the garage will likely be insulated with spray foam."
That boiler has enough burner output to heat my antique 2400' house + 1500' of basement down to temps well below -100F. Expecting another ice age, are we?
The additional 8000-10,000 BTU/hr design load of 700' of insulated bonus room barely moves the needle on the oversizing factor. You could heat two or even three of your houses at the same time in it's current state with that boiler.
But can I convince you to insulate it with something greener than spray foam?
There is nothing particularly green about spray foam (even worse if it's closed cell) and there are cheaper/greener ways to air seal the bonus room than insulating it with foam insulation. Cellulose has about the same R/inch as open cell foam and several times the thermal mass of spray foam (any density) , giving it a favorably lower thermal diffusivity at any given R-value or thickness, making it outperform spray foam measurably during the shoulder seasons. And unlike spray foam, cellulose has a NEGATIVE carbon footprint- it's sequestered carbon, after all.
One way I've gotten around low load zones is by putting it in series with the indirect, just after it. You would need a differential bypass valve around the zone (to allow flow through the indirect when the zone is off).
something like this
-boiler->pump->indirect->MiniZone with diff bypass->return
The zone thermostat ties into parallel with the indirect Tstat, either one can turn the indirect pump on.
If you are adventurous and some height you can also do a poor man's heat purge with the indirect by raising it up above the boiler. With some careful plumbing, you can get the heat from the boiler to thermosyphon into the indirect after the boiler is done firing. Not as fast as heat purge controls, but pretty good for free. This works well for me as the indirect is a couple of floors up.
>XPS
Didn't realize how awful the stuff was for the environment. I selfishly wanted something non-organic next to the concrete and in the basement because eventually something will leak down there and it will get wet. And I didn't want to lose any space in the room because of extra walls. I'm using metal studs where I can as well.
This is the Z: https://www.clarkdietrich.com/products/drywall-framing/z-furring-channel
In retrospect (and after dealing with the PITA installation of the Z-channel), I would have been better w/ 1" continuous foam and a 2.5" metal stud wall in front of that with an R-8 batt. That would have at least gotten me a bit closer to R-15. And would have only kicked out the exterior wall 1.5".
Images attached.
>Heat loss measurement numbers
I meant to say heat load/hour in BTU. So my heat load math came out around 35,000 BTU/hour (when I look at both a 60 deg and 65 deg balance point). Half my 1800 sq ft cape (built in early 90s) has brand new Marvin Integrity double hungs. The older ones are Andersen (and some have condensation circles in the middle). A little more than half the first floor has spray foam to achieve R-21. The rest has R-15 fiberglass (2x6). The attic was air sealed and filled with blown-in cellulose to achieve R49. There's a 16 foot dormer upstairs that also got sprayed to achieve R-21.
>Outdoor Reset
I've been contemplating putting in the outdoor reset kit for the Honeywell Aquastat that's already installed on it (model L7224A). It seems to make more sense now. One concern was that the indirect hot water tank wouldn't perform up to standards during the shoulder seasons, but I see that there's an override when that is calling for heat.
>Basement Heating
Yes, the boiler runs at 180 deg right now. Sounds like if I leave it at that, my basement isn't going to be doing any "damage" with short cycling because it may not ever need to burn, or get it over with in one burn.
@Akos - I like your idea also of sharing the indirect water heater zone. But might not be necessary based on Dana's calcs.
My entire house (without the basement) is just shy of 100ft of fintube total, across 2 zones. Downstairs has 41ft of normal output + 8ft of high output. Upstairs has about 47ft of normal output.
Are you maybe suggesting that I lower the boiler temp all the time? Down to 120deg?
>Bonus Room
Great to hear that I've got the heating capacity...I think I'll heat my garage off this boiler as well! (maybe via a hydro air element?)
>Greener Insulation
I'm all ears for alternate solutions (that may also be cheaper than foam). I like spray foam because I know I can insulate to my roof deck and not worry about venting. I like it because I don't have to worry about critters eating through it and squatting at my place. I like it because it adds rigidity to the building. I like it because it includes a vapor barrier by default. But I don't like its cost or the way it smells or the suit you need to wear when applying it.
Tried to post this a few days ago, and although it said it was posted, I don't see it. So here it is again (maybe it didn't like the attachments?) :
>XPS Didn't realize how awful the stuff was for the environment. I selfishly wanted something non-organic next to the concrete and in the basement because eventually something will leak down there and it will get wet. And I didn't want to lose any space in the room because of extra walls. I'm using metal studs where I can as well. This is the Z: https://www.clarkdietrich.com/products/drywall-framing/z-furring-channel In retrospect (and after dealing with the PITA installation of the Z-channel), I would have been better w/ 1" continuous foam and a 2.5" metal stud wall in front of that with an R-8 batt. That would have at least gotten me a bit closer to R-15. And would have only kicked out the exterior wall 1.5". Images attached. >Heat loss measurement numbers I meant to say heat load/hour in BTU. So my heat load math came out around 35,000 BTU/hour (when I look at both a 60 deg and 65 deg balance point). Half my 1800 sq ft cape (built in early 90s) has brand new Marvin Integrity double hungs. The older ones are Andersen (and some have condensation circles in the middle). A little more than half the first floor has spray foam to achieve R-21. The rest has R-15 fiberglass (2x6). The attic was air sealed and filled with blown-in cellulose to achieve R49. There's a 16 foot dormer upstairs that also got sprayed to achieve R-21. >Outdoor Reset I've been contemplating putting in the outdoor reset kit for the Honeywell Aquastat that's already installed on it (model L7224A). It seems to make more sense now. One concern was that the indirect hot water tank wouldn't perform up to standards during the shoulder seasons, but I see that there's an override when that is calling for heat. >Basement Heating Yes, the boiler runs at 180 deg right now. Sounds like if I leave it at that, my basement isn't going to be doing any "damage" with short cycling because it may not ever need to burn, or get it over with in one burn. @Akos - I like your idea also of sharing the indirect water heater zone. But might not be necessary based on Dana's calcs. My entire house (without the basement) is just shy of 100ft of fintube total, across 2 zones. Downstairs has 41ft of normal output + 8ft of high output. Upstairs has about 47ft of normal output. Are you maybe suggesting that I lower the boiler temp all the time? Down to 120deg? >Bonus Room Great to hear that I've got the heating capacity...I think I'll heat my garage off this boiler as well! (maybe via a hydro air element?) >Greener Insulation I'm all ears for alternate solutions (that may also be cheaper than foam). I like spray foam because I know I can insulate to my roof deck and not worry about venting. I like it because I don't have to worry about critters eating through it and squatting at my place. I like it because it adds rigidity to the building. I like it because it includes a vapor barrier by default. But I don't like its cost or the way it smells or the suit you need to wear when applying it.
This image is a thermal-bridge train-wreck disaster:
https://www.clarkdietrich.com/sites/default/files/imce/images/products/Framing-Interior/Z-Furring/Z-FurringWall.jpg
With R9-R10 foam the net performance after thermal bridging will be about R5-R6, maybe less depending on the furring thickness (don't even bother trying to calculate it.) When using steel studs or steel furring in a basement, always put them on the interior side of the assembly using bottom & top U-channel tracks, and keep the insulation layer continuous. It goes up quicker, and performs better. If reworking the materials already invested, with 2" of continuous foam and a furring-studded wall with unfaced R8 batts between the furring it'll come close to code-min performance. If it floods the most that would need to be replaced is the R8 batts, and then only the part from the high-tide mark downward.
>"My entire house (without the basement) is just shy of 100ft of fintube total, across 2 zones."
--------
>"I've been contemplating putting in the outdoor reset kit..."
The ratio of the 35K heat load and 100' of fin tube is 350 BTU/hr per foot, which can be met with ~140F-145F average water temp. Odds are it never needs more than 150F water even during cold snaps below the 99% outside design temp.
The ratio of the 109K boiler output and 100' of fin tube is 1090 BTU/hr per foot, which can't be met even with 215F steam. The boiler is simply oversized.
Outdoor reset on the BOILER is going to buy you next-to-nothing. Simply turning the boiler down to it's entering water temperature limits (which could be 140F? I'd have to look it up for that boiler) would probably still cover your cold snaps. I'm guessing dropping the boiler to 155F or so may be the lower limit before the return water would be chronically too cool, but try it out, take some measurements. The lower the boiler temp, the lower the standby & distribution losses, and higher the average comfort level. Almost NO system needs 180F water, even during Polar Vortex disturbance cold snaps.
An insulated buffer tank and an outdoor reset controlled mixer to allow the radiation to run at much cooler temps without compromising the boiler or flue with excessive condensation would offer a bit more comfort, but probably isn't worth the investment. For the kind of money it would take, spending it on a single modulating ductless heat pump (or two) might be the better bet. A single 3/4 ton or 1 ton Fujitsu has enough capacity to cover about half your design heating load, offsetting quite a bit of oil use, since most of the time it's well above 0F on the southern Maine coast. (Portland is +2F or warmer for 99% of the hours in a year.)
https://ashp.neep.org/#!/product/25333
https://ashp.neep.org/#!/product/25335
Paragaphs are your friend. Learn to love them.
Don't know how far down the road you are with the Z channels. With the high thermal conductivity of the metal Z, you loose about 1/2 the effective R value of the insulation (I think might even be more with rigid).
Much better to strap install a continuous layer of insulation then strap it out for drywall (1/2 plywood strips are enough). Even if you have to go with thinner insulation, the effective R value of the wall is much higher.
Sorry about the paragraph thing...I wrote it w/ paragraphs but it didn't post that way!
I'm basically done w/ the Z. No turning back at this point. You live and you learn. It's still better than the way I found the 20 year old home, without any insulation down there. I've got baby #4 coming in December and need to be drywalling ASAP! Maybe that's the wrong attitude long term, but I know there are much leakier, less-green houses than mine (as I look across at a building from the 1890s).
>>Heating Water Temp
@Dana, after I read your first reply, I set that Aquastat as low as it could go which is 140. My quick math also found that 150 degree water should get me through the cold snaps just fine, but we'll leave it at 140 until we have an issue! My biggest concern was the indirect recovery rate, but that seems to be just fine so far. I need to install a new tridicator to know what my return temp water is, but the Aquastat is calling for burner when it hits 120.
Obviously during this time of year, it is suffering from short cycles..I'm talking 2-3 minute burn times. I'm hoping this changes as it gets colder, but I'm not so sure it will change all that much. More load is what I need to throw at it....bonus space plus garage heat.
I thought about a buffer tank, but it looked like I'd be spending at least $1K on the tank, plus the hook-up. And a new modern boiler sized appropriately would cost me like 2 or 3K. So that math didn't make sense. Since this system only has a few years on it so far, I'll keep it maintained the best I can and hope I don't have to replace it before the 4th one is through college.
Just curious though, what WILL BREAK from short cycling? How much cost are we talking in parts/labor over a 20 year period? When does it start to make sense to scrap the thing (or sell it used) and get a modern mod-con propane boiler?
Thanks!
>"Obviously during this time of year, it is suffering from short cycles..I'm talking 2-3 minute burn times. I'm hoping this changes as it gets colder, but I'm not so sure it will change all that much. More load is what I need to throw at it....bonus space plus garage heat.
How many burns per hour?
Opening up the high to low differential temperature will improve the burn times. If you're only letting it swing from 140F to 150F (a 10F swing), increasing the high-limit to 160F with a low-limit of 140F will more than double it, since the thermal mass is still about the same, yet the heat emittance goes up with higher temp, so there is less "extra" heat to raise the temp of the thermal mass. A ten minute minimum burn time would be awesome, but a five minute burn time would be fine. Sub-3 minutes, and more than 5 burns per hour is a bit hard on the equipment, and takes a toll on efficiency.
>"Just curious though, what WILL BREAK from short cycling?"
The ignition components are the first and most obvious things that wear out- twice the number of cycles per year = half the lifespan, 4x the number of burn cycles = 1/4 the lifespan. Automatic dampers have similar issues.
The average raw combustion efficiency takes a hit too. With an oil burner it takes about 15 seconds after ignition for the combustion efficiency to stabilize, with a fixed amount of additional fuel use/waste per ignition cycle. When the average burn time is only 150 seconds (2.5 minutes), 10% of that burn time is at a dramatically lower combustion efficiency, whereas 15 seconds out of a 600 second (10 minute) burn is only 2.5% of the total burn time, so the consequences of that inefficient burn interval is diluted. A (not very good or accurate ) industry rule of thumb is that a short-cycling boiler takes about a 10% hit an as-used AFUE compared to the same boiler running reasonably long but much fewer burn cycles of similar total net burn time serving the same loads.
The lowest high limit on this Aquastat is 140. There's a built-in differential of 20 degrees, so it will go down to 120 before it turns back on.
I'm going to rig up an old Crestron system I have to track the cycles. I'll hook up the high-voltage output of the Aquastat to a relay to trigger a low-voltage input on the Crestron box. I'll write some code to monitor that closure and log what time it happened, and how long it lasted. Hopefully I can push that data to somewhere on the web so its easily viewable. It would be interesting to have that data as the winter goes on.
Thanks again.
120F-140F without proper boiler inlet temperature protection is problematic with a mid efficiency boiler. I would stay above 140F return, (150 to 160 on the outlet). You can add in a mixing valve to limit it then you can get closer to the condensing zone.
-Is my Buderus G115 at 86% rated efficiency considered mid-efficiency?
-What do you mean by adding in a mixing valve? Would this be to lower the baseboard temp but keep the boiler temp hotter? How would that plumbing look?
Since it is a non condensing unit, you have to be careful with return water temperature. Too cold and you start condensing and demaging the boiler or the exhaust pipes.
Take a read through this series (there are 4 parts), there should be a setup there discussed that matches yours.
https://www.pmmag.com/articles/102245-modern-hydronics-done-right