Insulating Basement Walls

Hi everyone,
I am looking to start finishing my basement. I thought I understood what I needed to do from past reading of building articles, but am now not sure
I am in downstate NY, zone 5 I believe? Basement is a walk out, with back wall and one side wall about 7 ft below grade. Other sides grade down to a walk out in the front corner
Walls are cavity block walls. Some minor flaking of old paint/white powdery stuff on walls, but no mold per se. There was a gutter issue on one side of the house and then missed for a while and I believe this has contributed to some of this white powdery mildew. But overall for the fifteen years we have lived in the house I don’t believe there’s a significant issue
From past reading on bsc, I was set to use 2 inch xps on walls . Frame in front, seal rim joist. Sheet rock and be done. Idea i thought was that the wall can slowly breathe/dry inwards if needed
Now I am seeing that this is not necessarily the correction approach. I have read posts arguing that walls do not need to be allowed to dry inward. Is this just for concrete walls or cavity block walls also? Should i be using 2 inch foil faced polyiso? Is this not similar to the old method if just putting a plastic sheet over the wall and insulating in front, or is there some breathability in foil faced polyiso?
Should I paint the interior walls with a vapor barrier paint first such as drylock and then polyiso or xps.?
Hope I explained where I am sufficiently and look forward to your input. I’ve been waiting a number of years to get to this project and now I just want to get the insulation portion done the right way
Thanks, Vincent
GBA Detail Library
A collection of one thousand construction details organized by climate and house part
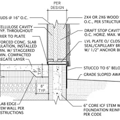
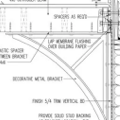
Replies
Hi Vincent.
If your basement is dry, there is no problem with your plan to insulate your walls. The masonry walls don't need to be able to dry inward and XPS will give you all the vapor control you need. You can use polyiso for this too, but that would be a choice based on R-value or environmental issues (polyiso is more eco-friendly). If your basement has any water issues at all, fix them before starting any of this work. Do a good job air sealing the rim joist before hiding it behind drywall.
Some people with basement walls that can't dry to the interior have reported mold odors (and upon inspection, found mold). Others have seen a decreased ability to handle minor external wetting. So I'd use more vapor permeable unfaced EPS. If not, a paint with mildewcide should help with the first issue.
>"Now I am seeing that this is not necessarily the correction approach. I have read posts arguing that walls do not need to be allowed to dry inward. Is this just for concrete walls or cavity block walls also? "
The block walls tolerate moisture just fine, but they also wick moisture upward. If there is a good capillary break (sheet EPDM, metal flashing, etc) between the top of the foundation and foundation sill it's fine to let the block saturate.
If there is NOT a good capillary break between the masonry & wood it's important that there is at least a foot of above grade exposure on the foundation so that the masonry (and foundation sill) can dry to the exterior, and that there is good bulk water management a the surface. Deep roof overhangs and gutters for minimum splash-back wetting of the exposed foundation can also help.
>"Should I paint the interior walls with a vapor barrier paint first such as drylock and then polyiso or xps.? "
Drylok is NOT a vapor barrier, but it does impede moisture wicking. Per the manufacturer's marketing fluff:
"Breathable film will not trap moisture in the masonry"
http://www.drylok.com/products/drylok-extreme-masonry-waterproofer.php
Since there are some signs of efflorescence it would have been a good product to use UNDER the paint, but since the wall is painted it won't change the drying characteristics of the wall by very much. If there are big sections where the paint is heavily degraded and flaking by moisture, cleaning those sections up and hitting it with Drylok wouldn't be a bad idea.
In US climate zone 5 the IRC calls out R15 continuous insulation, or the thermal equivalent thereof. In zone 5 the IRC also calls out a minimum of R5 of air-impermeable on the exterior of fiber insulation in 2x4 walls. So the best compromise here would be to install 1.5"-2" of unfaced Type VIII EPS (1.25lbs per cubic foot nominal density) trapped to the foundation with a 2x4/R11+ studwall, using unfaced or kraft faced cavity insulation. At 1.5" - 2" the vapor permeance of Type VIII EPS is about 1.5-2.5 perms (give or take), about half the vapor permeance of standard interior latex paint on wallboard, and about R6.25 (1.5") which is sufficient dew point control for R13 fiberglass, to R8.35 (2") which is sufficient dew point control for R15 fiberglass or rock wool.
It's also useful to install a strip of EPS under the bottom plate of the (non-structural) studwall as a thermal and capillary break, protecting the bottom plate from wicking moisture from a potentially damp slab, or being cool enough to accumulate excess moisture from the more humid summertime ventilation air.
There are multiple vendors of reclaimed roofing foam in NY, with several square miles of 2" -3" fiber faced polyiso in stock. (~R11-R17). Fiber faced polyiso is not a true vapor barrier, but is more vapor retardent than EPS. If the exterior side exposure on the foundation and bulk water handling details are in order it's fine to use polyiso on the walls. But don't let the cut edge of the polyiso rest on the slab, nor should it be used under the bottom plate of the studwall, since it can wick moisture. Instead, install an inch or more of EPS (any density) under both the studwall and bottom edge of the polyiso, leaving an inch or so of clearance to the wall as a drainage channel.
For sources of inexpensive reclaimed roofing EPS (almost always Type VIII) or polyiso, run these searches every so often:
https://utica.craigslist.org/search/sss?query=rigid+insulation
https://hudsonvalley.craigslist.org/search/sss?query=rigid+insulation
https://catskills.craigslist.org/search/sss?query=rigid+insulation
https://newyork.craigslist.org/search/sss?query=rigid+insulation
Search function is always helpful, you have answered some of my questions posted here - https://www.greenbuildingadvisor.com/question/wall-assembly-11?cid=206270&discussion=response#comment-206270
So I am still debating if I need internal french drain and the dimple mat, I guess I should go for it just to be save, and as I posted in the other thread, can this:
" So the best compromise here would be to install 1.5"-2" of unfaced Type VIII EPS (1.25lbs per cubic foot nominal density) trapped to the foundation with a 2x4/R11+ studwall,"
be replaced with foamular ngx (supposedly much less toxic gases and can get wet, not sure if I can believe it, but that less toxicity is driving my choice here, would prefer not to breathe it in), and can it be pair with R15 rockwool (2x4 wall) bats and not worry about condensation?
Can XPS get in touch with the slab?
The foam manufacturer claims Air Permeability at 75 Pa (L/s.m2), Negligible (0.001), but I do not fully understand this statement, I am not sure what thickness is that.
Thank you! (posted in both threads as this one is old and I was not sure if anyone would answer here)
Deleted
Deleted
How thick should the EPS under the bottom plate of the studwall be? We're doing a very similar (but it's a tear out remodel) project to our house but plan to use two 1.5in EPS sheets anchored to the block then the 2x4 walls (where we can). Should it be a 'strip' of EPS under the bottom plate or should it continue under the EPS on the wall to the block of the foundation?