Net-Zero-Ready Wall Assembly

In general terms which do you think would be the better R-40-ish wall assembly in Zone 5 for a builder new to net zero ready construction, a standard 2×6 wall with 3-4″ of exterior foam/rainscreen (“outie” windows on 2×4 bucks) or a double 2×4 stud wall (“outie” windows on exterior sheathing)? I’d use dense-packed cellulose in each assembly, with the double stud wall running about 11″ thick. Vinyl siding is likely to be the exterior wall surface.
I’ll work with an experienced designer to get the all of the air & water control details incorporated into the plans, but am curious if one of those two approaches will be more likely to be less easy to screw up / more likely to be done correctly. I’ll of course be watching over all the details like a hawk 😉
GBA Detail Library
A collection of one thousand construction details organized by climate and house part
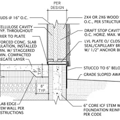
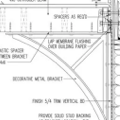
Replies
For our pretty good house, we used a double stud wall. Our builder had never done one, but found it simple to build. I think the key is a good set of drawings, which carefully detail the placement and installation of the air barrier. And of course, the builder needs to be attentive to detail. Our builder, Tom Greenleaf, was great. .59ach50.
I prefer an approach with a fair amount of continuous exterior insulation. 2-4” if you can. Even IECC 2021 will require R5 CI in your 2x6 wall if you went prescriptive.
If you are really turned off by the idea, you could look at the TStud product, which significantly reduces thermal bridging in your stud cavity approach. You can get up to R40 with their 2x8 application.
Joseph,
As a relatively new self-builder and to NZR/Passive, I too set out to find a near R40-effective wall for zone 5. It was an existing home, with 2x4 walls, so I was stuck with that, and decided to add as much foam as I could to the exterior. I settled with reclaimed polyiso with a total thickness of 5".
There were many challenges building this way, and frankly, I wouldn't recommend it. It complicates the entire job to a degree that just becomes frustrating. I was thankful enough to get some Alpen windows with very deep exterior trims, but every other detail is difficult. It's doable, but there are tons of issues that stack up.
While you could certainly build that assembly, the biggest issue I see with your plan is to use vinyl siding. I'd assume that you'd want to put a rainscreen on the exterior foam, and would likely need to use 1x4 wood furring strips attached to the structure. If you did that, you would also need some type of continuous flat surface to nail the siding to.
I would absolutely go for the double-stud method if I was in your position. It's very "normal" construction, just more of it. I've recently worked on a double-stud project, and it's just much, much easier. It gives you all of the energy benefits, and has exterior sheathing to nail your vinyl siding to.
In terms of window placement, you'll find that mid-mounted windows, or windows that align with the insulation planes, are the most efficient. They also protect the windows from exposure, and you can also insulate the exterior of the window frame, if the frame allows. Many passive-style windows have large frames specifically for this reason.
Again, these are just my opinions, but I really would pursue the double-stud solution. Exterior foam that thick is just a pain.
Thanks,
Aaron
There are downsides to both proposed wall assemblies - a 2x6 wall with 3 to 4 inches of foam requires lots of long/strong fasteners to support the siding, (these are expensive and act as heat radiators), a lot of labor- intensive fiddley work on the exterior, are something of a fire hazard, and the final (actual or real) R rating will be no more than about 35 with 4" of Styrofoam or about 36 with 3" of polyisocyanurate (4" w0uld bring it up around 42). These numbers do not take into account the heat loss caused by the multitude of fasteners required by the foam.
A double stud 2x4 wall filled with cellulose has a different set of problems. First the R value (real or actual) for an 11" thickness will be about 34. Unfortunately, there has never been a real scientific study done on settling in cellulose filled walls but there is more than enough anecdotal evidence make one suspicious. Take a look at this video about a house built in Fairbanks where the builder went to an unbelievable amount of trouble trying construct a house with cellulose filled walls only to find settling anyway about a year later - https://www.youtube.com/watch?v=Xen_VWyDezY.
My recommendation: A 2x4 double stud wall with 3 inches of foil faced polyiso sandwiched in the middle - and mineral wool between the studs. The total R rating will come out about 40 and the thickness (stud face to stud face) will end up 10 inches. You will never have a condensation problem inside this wall in any weather, the polyiso is easy to fasten ( think! short fasteners and not too many of them) to the inside face of the exterior 2x4 studs and protected from physical damage by the two stud walls (also from fire and insects). The only downside - the materials are a bit more expensive than a cellulose filled wall. GOOD LUCK!
Isn’t it more common to attach vertical wood furring/strapping through the rigid insulation back to the structure as a means to provide a convenient cladding attachment? This is what Building Science Corporation suggests and has determined it to be both cost and thermal effective.
Do you have a WUFI hygrothermal analysis for your proposed assembly? Is it common to put a class 1 vapor retarded in the middle of the double stud wall? That would prevent drying in both directions. Truly curious, as I haven’t designed one before.
Fasteners through exterior rigid foam do not significantly affect thermal transfer trough the insulation. This means the fasteners don’t appreciably reduce the effective R value of the wall assembly. There is a thread in the GBA Q and A forums where I actually calculated the total BTU loss for fasteners in a common grid spacing and it wasn’t much. You’ll loose more heat through air leaks in keyholes and other small things than you will through the fasteners in continuous insulation.
“Thick” exterior rigid foam usually means more than 2”, and more than 2” is where exterior trim details get more complex.
I don’t really see a problem with the “foam in the middle” wall assembly aside from a more complex construction process to build it.
BTW, if you’re worried about cellulose in walls settling over time, put in some baffles at the halfway point or maybe in thirds. Use thin material like. 1/8” hardboard or 1/2” polyiso. You don’t need much support here, just enough to limit compaction of the cellulose over time.
Bill
assuming 16" OC for the outer load carrying wall and foil faced PU, I get R 43 and a bit.
Thats without all the fasteners and top/bottom plates.
A double stud wall is far easier to do, especially for a conventional builder unfamiliar with using exterior foam/poliso. Conventionally installed cellulose could settle some, but should not be a problem with dense-packed cellulose. There would be minimal if any settling with dense-packed cellulose. Dense packed cellulose may require having an experienced contractor available in your area. Cellulose is relatively easy to install, cost-effective, and sustainable (I guess until we stop producing newsprint!). Those who have used dense-packed cellulose may wish to chime in here. (I've used exterior polyiso and self-installed cellulose.) Netting is required to break the interior spaces into smaller spaces to accomplish sufficient density.
To meet fire code, you need to have firestop span between the two walls every 10' on the interior of the double-stud wall (3/4 ply might be easiest). Window bucks can be part of this firestop, just have to add ply or Type X drywall spanning between the two walls above and below the window bucks. Easy enough to add and can help with the dense pack process to divide up the spaces being filled.
You can adjust that space between walls to obtain R-40 total wall R-value, or whatever R-value is desired. Your walls might end up almost a foot thick. But same for 2x6 plus all that exterior insulation. Exterior insulation would give you a little more interior space, as well as exterior overhang space for any exterior slab/basement wall insulation below the protruding wall.
Polyiso between the walls would work too, but can create a vapor barrier. Vinyl siding technically might limit water vapor transmission through the wall, as would polyiso. There's enough open air spaces in vinyl siding applications that would allow drying to the exterior. Probably for non-foil faced polyiso too. Assure that you can dry to the inside and outside, and avoid foil-faced polyiso (a vapor barrier) between double walls. For the same reason, using a poly air barrier anywhere inside the wall might trap moisture.
A smart vapor retarder would help reduce moisture migration to the sheathing in winter, where you could have condensation and wetting of the sheathing (which typically dries out in the summer). Investigations show that this theoretical problem has turned out to not be a problem in double walls with cellulose especially, as it can absorb and release some of that vapor moisture migrating through the wall. But I'd use it just to be safe, but others would likely say its unnecessary. Others have recommended a vapor retarding interior paint to reduce wintertime water vapor migration through the wall to the sheathing.
To easily adjust whatever space you wish between the two walls, I am assuming you could use a single top plate for each of the two walls, with double 3/4" ply as the second top plate spanning the tops of both walls and providing firestop at the top of the wall (and below floor joists or attic).
Minor detail: I might suggest putting polyiso glued to a double wall top plate that bridges the two walls of the double stud walls. That way, if there is some settling, a polyiso foil facing could reflect heat back away from the wide top plate thermal bridge. And the polyiso itself would provide a little extra R-value to reduce heat loss from the wall cavity out that top plate. Same idea could be used for the bottom of window bucks in a double-stud wall.
Lots of great info in here. One super minor point:
> Window bucks can be part of this firestop, just have to add ply or Type X drywall spanning between the two walls above and below the window bucks.
YMMV, check with with your local code official, offer not valid in all jurisdictions, etc., but the IRC does not require Type X for fireblocking. 1/2" drywall is sufficient. From R302.11.1: "One-half-inch (12.7 mm) gypsum board."
No expert here, but I'm struggling to see why Forrest Stanley's design wouldn't work. Passive House designer Natalie Leonard, Passive Design Solutions, uses this assembly in her Stock Plans, in Nova Scotia no less (see Passive House Accelerator / Bringing Passive House to the Mainstream). She uses 2x6 framing for the outer wall, but everything else is the same.
Why is the vapor barrier in the center a problem, as long as the interior face stays warm enough to prevent condensation from inside? It's not just a sheet of poly; it's insulation. As long as you allow the inner wall to dry to the interior (no inside poly or vinyl wallpaper), it doesn't seem much different than a single wall with exterior CI. If the outer wall is reasonably vapor-open to the exterior and has a rainscreen, it seems pretty safe too. Why does it matter whether the wall can dry "all the way through", as long as all the vulnerable components have a drying path in at least one direction? Only downside I can see is possibly higher material cost over other options.
One question - what about insulating the inner wall with dense pack cellulose? Outer wall may be tricky to do with cellulose unless you have a plan to keep it dry during construction. Mineral wool would be easier to install from outside, although you'd still need to let it dry out if it got wet before the sheathing was on. Or else maybe you sheathe and insulate the outer wall before you put up the rigid foam?
Typically the walls and exterior sheathing go on together or in close sequence. Partly for bracing against racking, partly to close in the building from the weather. Often for convenience if you build the walls on the floor, then raise the wall into place.
IF you have building inspections to pass during construction, you have to pass the framing inspection before you add insulation, so they can inspect all the framing. So the framing and sheathing are done, and the insulation is installed afterwards. The plumbing and electrical have to be installed and pass inspection before insulation as well. Otherwise too much is buried in insulation, hidden from the inspector. Then they will inspect the insulation if there's an inspection for that. (I had to do all of these...and many more). Some places you have few or no inspections.
I suppose you might be able to convince the inspector to allow you to make some adjustments to this schedule...maybe...like if they trust you and you have photos, videos or ?
You could get rigid polyiso in between the double walls by cutting to fit past the inner wall, but sure would be easier to install before the inner wall. Since the inner wall is not structural (typically), maybe the inspector would be fine with leaving it for later...assuming they can see all the electrical and plumbing work if there's an inspection to be done after polyiso is installed between the double walls.
Remember that over time, people change the interior finish and the exterior cladding. Who knows they may do in the future. So a vapor barrier mid-wall might be a future problem...but maybe not your problem.
The foil is what makes foil-faced polyiso a vapor barrier. Why not use polyiso that is NOT foil faced? Foil needs an airspace to reflect heat back and add some R-value to the assembly (reflect heat in that airspace next to the foil). So doesn't do much good with adjacent insulation.
Instead of speculating, why not just run the WUFI hygrothermal analysis to be sure?
I just quickly skimmed the PH Accelerator presentation and looked at Natalie’s detail. She even says in her presentation that it was important to run the WUFI analysis because a wall in x location worked, but the same wall in y location didn’t.
Also she calls out rigid insulation in the middle of her wall. Not foil faced polyiso. Can you point me to where she puts a class I vapor retarded in the middle of her assembly?
You can also look at a 2x8 24" OC wall with 1.5" of exterior polyiso.
This is not quite an R40, but pretty close enough that it won't matter for energy use and you can simply nail the vinyl up straight through the foam.
Chicagofarbs,
You're right - Natalie Leonard doesn't exactly specify the type, thickness, or perm rating for the rigid foam layer in the video I cited (I wondered about that too when I first viewed it). The graphic does show that she's using it for the air/vapor control layer, with joints taped on the inside. Some kind of facer would seem to make it easier to tape, but I guess it's not absolutely required. The bullet points mention "air sealing from the inside" and "varying insulation levels" for different climates, which I believe refers to the foam layer.
All that said, she also posted a later video on the same site about the Sunflower Social Housing Project in Halifax. This uses the same basic assembly, although here she calls out 1 1/2 inch foil-faced polyiso, again as the air/vapor control layer.
What she doesn't say much about in either video is how the windows are installed - water management details, how the air barrier is connected. I think you'd want to have all that figured out beforehand; I don't know those answers.
Robert makes some good points in post above about how future residents may unknowingly change the vapor profile and about inspections. Akos' assembly (post #12) looks pretty good to me, a lot harder to screw up and good performance in all but the coldest climates.
Be careful with vapor retarders/barriers in the middle of a wall. From the 2021 IRC:
A vapor retarder shall be provided on the interior side of frame walls of the class indicated in Table R702.7(2), including compliance with Table R702.7(3) or Table R702.7(4) where applicable. An approved design using accepted engineering practice for hygrothermal analysis shall be an alternative.
> 2x8 24" OC wall with 1.5" of exterior polyiso.
2x8 walls aren't listed by the 2021 IRC, but for Z4-Z6 extrapolation leads to "use this wall only with a Class II smart-retarder". Higher perm GPS or mineral wool would be better.
Code does not require continuous exterior insulation.