Best rigid insulation to add to exterior of existing 2×6 wall with poly vapor barrier?

As part of replacement of T1-11 siding with fiber cement on a building in Zone 6A, I plan to add 2 inches of exterior rigid insulation outboard of existing 5/8 inch plywood sheathing and additional sheathing on the exterior of the rigid insulation as a nail base for the fiber cement. I expect to use some type of rain screen between the new sheathing and the fiber cement.
The existing wall is 2×6 framing @ 24 inches o.c. with R19 fiberglass insulation and an interior polyethylene vapor barrier that must remain in place under the interior gypsum board.
XPS appears to be a better choice than EPS for R value, and 2 inches (R10) appears to be better than 1 inch to raise the temperature of the existing sheathing to limit the chance of condensation. Drying to the exterior may be slowed by the added rigid insulation and new sheathing.
Given the need to maintain the existing interior poly vapor barrier, what is the best approach to adding insulation on the exterior, minimizing moisture related issues, and supporting the relatively heavy fiber cement?
Thanks for considering this question.
GBA Detail Library
A collection of one thousand construction details organized by climate and house part
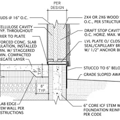
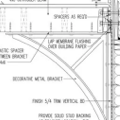
Replies
Al,
No matter what type of foam you install, don't expect that your wall assembly will dry to the exterior. Here is my standard answer to questions like yours:
Many energy experts have worried whether it's a good idea to install exterior foam on a house with interior polyethylene. Although it would be better if the poly wasn't there, the fact is that tens of thousands of Canadian homes with interior poly have been retrofitted with exterior rigid foam, and there haven't been any reports of widespread problems. According to building scientist John Straube, all indications show that these retrofits are "not so risky as most people think. These homes will probably be fine."
That said, the installation of exterior foam is not advised on any home that has suffered wet-wall problems like leaking windows, condensation in stud cavities, or mold. If you plan to install exterior foam during a siding replacement job, keep an eye out for any signs of moisture problems when stripping the old siding from the walls. Investigate any water stains on housewrap or sheathing to determine whether the existing flashing was adequate.
If there is any sheathing rot, determine the cause -- the most common cause is a flashing problem, but condensation of interior moisture is not impossible -- and correct the problem if possible. If you are unsure of the source of the moisture, hire a home performance contractor to help you solve the mystery.
If your sheathing is dry and sound, I don't think you need to worry about adding exterior foam. Adding a rainscreen gap will certainly go a long way toward avoiding future moisture problems. Of course, it's important to be meticulous with your details when you are installing your new WRB and window flashing. It's also important to keep your interior relative humidity within reasonable levels during the winter. Never use a humidifier.
To summarize, here are four caveats:
1. Be sure that your foam is thick enough to keep the wall sheathing above the dew point in winter. Read more on this topic here: Calculating the Minimum Thickness of Rigid Foam Sheathing .
2. When the siding is being removed, inspect the existing sheathing carefully for any signs of water intrusion, and correct any flashing or housewrap problems.
3. Install rainscreen strapping so that there is a ventilated gap between the new exterior foam and the siding.
4. Keep your interior humidity under control during the winter; if the interior humidity gets too high, operate your ventilation fan more frequently.
Al: I was wondering why a full layer of additional sheathing is felt to be necessary, considering the expense. Couldn't you do wood strips, -they could be 2 bys or even 1 bys, run vertically over existing studs and fastened well. This would be a big part of the fastening of the rigid foam, and also provide an air space behind the new siding for ventilation. The only reason I can think of not doing this is if the fastening of the cement board every 24 inches is not enough. But even with new sheathing you would still want to hit the studs I would think. Fastening thru the sheathing gives little thickness for holding and puts extra holes in your rigid foam below it.
In response to Howard Gentler's comment, I thought there might be added value in more continuous backing behind the fiber cement where the studs are spaced 24" o.c. I had thought the venting might be accomplished with a layer of rainscreen material between the fiber cement and the sheathing. I have seen 1x3 vertical strapping used where the framing is 16" o.c. but need to get more information on the application and performance where studs are 24" o.c.
Al, your thinking may be prudent and worth the expense. I was probably thinking more about wood clapboard. I don't know much about cement board, -I know it is heavy and strong, but may be brittle as well, such that if something hit hard between the nailing strips there might be cracking. I guess you can find that out, but wouldn't hurt to have a solid surface behind it certainly. You might check on whether the rigid foam itselt would be adequate backing.
Al, if you want continuous backing for the siding then you could install furring strips between the rigid insulation and the outer sheathing. Then install asphalt paper and siding just as without a rainscreen. Fiber cement lap siding is thin (5/16") and can look wavy on 24" spans. Or, install furring over the studs plus at the midpoints (so 12" on center), and no extra sheathing. Half the furring will have limited strength but you only need functional support for lap siding every 24" anyway, and the "in between" furring should avoid waves or gaps between the planks.
Definitely skip the additional sheathing. You have just protected your existing plywood by insulating it sufficiently to keep it warm and dry. The second layer would be entirely outside the insulation making it vulnerable to rot. Putting the new sheathing on top of your rain screen strapping will make things even worse.
The best rigid insulation on an interior poly clad home in a cold climate is rigid rock wool, not foam. A distant second is Type-I (1lbs density) or Type-II (1.5lbs density EPS.)
XPS is far to vapor tight, even at 2/R10, where it's running ~0.6 perms. And R10 wouldn't be enough to keep the sheathing warm enough to have much winter-time drying in that stackup anyway, even intot a vented rainscreen. Go for R12 minimum, but keep it more vapor-open. Type-I EPS would be over 1.5 perms at R12 (3") , and Type-II EPS would still be above 1 perm even at R12.5( also 3".)
R12 in rock wool is also 3", but is over 50 perms, making for a MUCH faster drying rate, and keeping the sheathing warm enough to have at least some mid-winter drying hours.