Building a 120 sq. ft. portable office: Insulation/assembly details?

Hi, I am helping my son build a 10′ x 12′ office in Zone 4a Nashville, TN area.
What would be very economical floor, wall, roof assemblies?
Essentially I envision a storage shed, but with good envelope details.
Portability (on two 4×6 skids) so he can move it once he builds his house 1/4 mile away.
No building code for the shed/office, so I can do as I think best and economical.
Floor detail: I am at a loss since I have not seen a storage shed with insulated floor. We plan to frame it with treated 2×6 16″O.C. and cover it with 3/4″ Advantech. I though about putting 2″ foam board on top of this, but I don’t know how that would work out for finish floor? I also wondered if 2×2 16″ OC is needed on top of the advantech and fill between them with foam board and then another layer of advantech?
Wall/Roof – We have some single-wide trailer trusses that we thought to recycle. We can cover roof wall with OSB and air seal it as a whole and have no venting. Then cover the whole with 2″ foam board and then cover that with felt paper, 1×3 and lap siding on walls and tin on roof. This “perfect wall” copy will eliminate need to build soffits/facia. 2″ insulation (polyiso) and airtight wall while not much insulation, would seem pretty efficient for such a small building?
Inside he can finish out as he sees fit.
Thank you for your critique/advice.
-Mike
GBA Detail Library
A collection of one thousand construction details organized by climate and house part
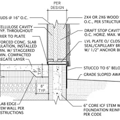
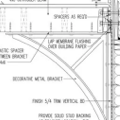
Replies
I would probably use foam board in the floor. You can put rigid foam down over the “floor”, and then put a plywood or OSB subfloor on top of the foamboard. Type II EPS would probably be a good fit for this application.
I’d use batts in the wall, and maybe some rigid rigid foam under the exterior siding, but I’d probably just leave it with batts here. I’d use batts in the roof too, and I’d strap them in. Why batts? Because they can be strapped in and won’t shift when you move the structure. I’d be worried about blown in insulation possibly shifting around too much during transport.
Basically my thinking would be to prioritize durability in transit over absolute insulating value. You’re building a special purpose structure so some of the requirements are going to be different than they would be for a “normal” stationary building.
One last thing: have you considered just buying a trailer or surplus telecom shelter and using that instead of building? Both are intended to be moved around as one unit (the telcom shelters are usually precast though so they’re very heavy), and they’re built to stay together. Construction sites use trailers as mobile offices all the time.
Bill
Thank you Bill.
If I use bats in the roof framing, does this require that I use a vented attic? I would assume yes.
When you say "foam board over the floor" do you mean:
a. floor joists, foam board, subfloor?
or
b. floor joists, advantech, foam board, plywood?
I recommended a used little camper, office trailer, but my son is very much interested in aesthetics; so, he does not want to go that route for his office.
-Mike
Yes, generally the use of batts in the roof assembly also requires that it be a vented roof. I suppose you could use spray foam ($$), or rigid foamboard on the exterior if you want to avoid the need for venting. Which way you go depends on if you want to avoid venting or not. Since this isn’t a building where code applies, you don’t have to worry about how much insulation you use as long as you use enough to avoid condensation problems.
The floor assembly, from bottom up, would be joists, OSB/plywood, rigid foam, OSB/plywood, lastly finished floor material. I wouldn’t recommend putting the rigid foam directly over the joists due to the possibility of the concentrated forces deforming the foam. A layer of OSB/plywood over the joists helps to distribute the load evenly over the rigid foam. Also, if the underside of the joists is going to remain open, I’d use plywood there. Plywood tends to hold up better than OSB in areas where it may get wet occasionally (like when transporting the building over/through puddles).
Bill
Mike,
I built something very similar to what you are describing last year. The floor was plywood over the joists, rigid foam, and a subfloor of plywood above. The walls were insulated by batts, and the shed roof was constructed much like the floor, with a layer of plywood as the finished ceiling over the rafters, foam over that, and another layer of plywood as roof sheathing. It was quite simple to build as long as you don't want the foam to be very thick.
Great. Thank you. The foam board between the two plywood floor layers - is foil polyiso ok? or?
-Mike
Mike,
You want something in the 10 psi range. Even at that you will find a bit of irregularity between the sheets of plywood subfloor when they are screwed down. I don't think the type of foam matters much beyond that. The lower layer can dry to the outside, the upper one should never get wet.
I don’t think polyiso is generally rated for compressive strength. XPS and EPS foams are. Type II EPS is probably your best bet here, but XPS may be easier to get in small quantities.
Bill
Hi Mike -
In a conditioned space that small, take care to consider air quality and how to introduce ventilation.
Peter
Do you want to build it yourself? Why? This process is far too complicated, and I wouldn't recommend you do it yourself. Today there are much better alternatives such as buying a portable desk. This will make your life much easier. I also needed one, and I found many alternatives. Later I found a guide for buying mobile office trailers and got down to business. Ultimately, I chose a very good, high-quality mobile office trailer without building it myself. This saved me a lot of personal time and money.