Building envelope and insulation for new build holiday home

I am sorry this is so long, but your expert thoughts are greatly appreciated!
Background:
– In the planning stages of a two storey holiday home with an unheated garage below and 2 bedroom with living area and small bathroom on the second floor.
– 40 x 30’ foot print, about 800sq ft for the living area. 1:12 “Flat” roof
– Climate zone 4 marine (north of Vancouver, Canada). Temperature rarely drops below about 28F and the building will be unheated and unoccupied for long periods in winter. Summers are warm but typically not humid.
– Fairly remote area so we intend on using a prefab company to build the wall, floor and roof structures but we hope to complete the building envelope and insulation ourselves.
Having read many articles and Q&A posts, I’ve come up with the below roof plan I’d appreciate input on, but more importantly input on the walls as there seems to be many more options to go with.
Roof from inside to outside: R40 is our ceiling requirement, but this drops to R26 for cathedral and flat roofs and we are proposing a 1:12.
1) Ideally exposed timber rafters/beams. Option 2 engineered rafters which we paint to save money. Depth TBC, but the span is about 15’ so perhaps 16”.
2) On top of the rafters ideally T&G pine that could be left exposed/unpainted. Option 2, high grade ply that could be painted on the underside. The idea is to avoid the need to drywall the ceiling, which would save a fair amount of time and cost. Also, getting drywallers at this location would be difficult.
3) A self- adhesive vapour barrier applied to top of the roof deck. Such as:
https://www.iko.com/comm/product/iko-mvp-modified-vapour-protector/
4) 2 layers of 3 to 4″ poly iso insulation, staggered seams. Possibly thicker if costs allow. 5) 1/2″ ply (metal roofing at this low pitch seems to require solid surface otherwise would be nice to avoid this and use purlins instead). Detail to be decided once metal roof specs confirmed. The ply/purlins would need to be fixed down through to the rafters, preferably with thermally broken fasteners
6) Self-adhesive vapour permeable roofing underlayment. Preferably with built in air gap (for drainage and air circulation). A high spec underlayment seems to be necessary for low pitch such as ours.
http://www.westmansteel.ca/public/File/webfiles/WestmanSteel_UnderlaymentPLATINUM.pdf
http://www.core-construction-products.com/products-leed-energy-star-net-zero-energy-efficient-insulation-concrete-building-materials-homes-east-usa/colbond-drainage-roofing/metal-roof-underlay-enkamat.html
7) Metal standing seam roof, might be with hidden clips or exposed self-tapping screw type.
Question: Given the plan to leave the rafters exposed and the fact that the rafters will likely continue to the outside of the building to form the overhang, what is the best way to insulate at the soffit area (above the wall top plates) if the roof insulation is all above the rafters? We could cut solid foam to fit between rafters and fit to the outside? The overhang/soffit area will be clad with cedar so this approach would hide the foam.
These rafter penetrations the ‘building envelope’ seem to pose numerous challenges with regards to insulation and air sealing, but I am not sure of a way around it as we are designing at 4-6’ overhang . Very open to thoughts I couldn’t find any details/drawings within GBA but probably missed it!
Walls from inside to outside: R20 needed
1) Similar to the above, we’d like to avoid drywall. So finishing will likely be wood cladding or reclaimed materials on the inside.
2) Vapour Barrier. Simple poly or go for a ‘smart’ barrier like Membrain if the building will be unheated for large periods in winter?
3) “Fluffy” insulation between 2×6 studs
4) Sheathing. We are considering Zip system either insulated or uninsulated. But cost may be prohibitive.
5) If not insulated Zip, should we consider foam outside the sheathing given the property is not fully occupied in winter? I am probably more concerned about achieving an air tight envelope than a highly insulated one to save money.
6) Weather Barrier. If not ZIP, should we just stick with a standard housewrap and be very thorough with taping and sealing all penetrations etc. Or spend the extra on a drainable wrap like the below that would allow us to avoid the need to fur out for the cladding. Our code calls for a 10mm rainscreen. http://www.benjaminobdyke.com/products/slicker-hp-rainscreen-10-mm
7) Furring strips if we don’t use a WRB with a rainscreen
8) Exterior cladding is cedar T&G and fastened standing seam metal cladding
Floor of the 2nd level from inside to out: R28 needed by code
1) 3/4″ OSB, board seams glued and boards glued down to joists (would act as a vapor barrier?). The OSB could be varnished and left as finished floor until budget allows for something else.
2) “Fluffy” insulation between floor joists above the unheated garage area.
Ventilation
– Assuming we can achieve a fairly airtight building, and an ERV is too costly for a holiday home. Should I assume that a bathroom fan and kitchen extractor fan will provide enough air movement? Should I allow for a passive source air vent or two and if so where should they be placed?
– Heat will largely be via a wood stove. I am considering a high efficiency European model, any thoughts on if I should try to source a direct supply air vent for it I understand can be available.
GBA Detail Library
A collection of one thousand construction details organized by climate and house part
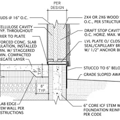
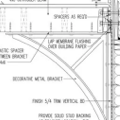
Replies
Quinn,
i'll leave other posters to comment on your plans from a building science standpoint. From a code perspective I think there are couple of things you might have to address.
-If "north of Vancouver" is close enough to to be included in the high seismic provisions of the code, the roof needs to be sheathed in "panel-type roof sheathing" (9.23.16.1). Whether it would be acceptable that this sheathing is separated from the roof structure by that much foam is something you should probably run by your inspector. Similarly, insulated Zip-R might not meet the seismic requirements for your wall sheathing.
- Houses built over garages typically run up against the braced wall panel ratio requirements on the wall where the door is situated. You may need engineered shear-walls on both sides.
- Your plans for ventilation and exhaust fans will be governed by 9.32.3.4. which requires full-time mechanical ventilation at rates set by the code.
From a design perspective I would urge you to increase the pitch of your roof. I've installed a lot of Westman steel roofing. Like many other products it performs well when kept within the limits of its specifications. Going to the edges of its capabilities, by using the extreme end of the slope requirements, makes the whole assembly a lot less resilient than it would be if it were,say, a 2:12 roof.
Good luck with your project!
"thermally broken fasteners" from #4 on the roof section - I don't think these exist for the proposed application.
Malcolm
Thanks very much for your answers. The project is on the Sunshine Coast specifically. Noted regarding the seismic issues, I am hoping the prefab company will be familiar with these issues and can advise accordingly. I suspect we will end of with ply immediately above the rafters to act as the sheathing. Sounds like ventilation is going to be tricky to meet code as there will not be a forced air system, perhaps it will need to be passive source vents in the rooms and common area, and a dedicated exhaust air, clearly it would be better to go HRV but for a cabin largely heated from a wood stove it is difficult to justify that cost.
Interesting regarding the pitch despite what Westman says is okay down to 3/4:12. This is an important design consideration off the start as the pitch drastically impacts the look of the building.
Tim - I see your point, the thermally broken fasteners seem to be made to fix foam down, not overlying ply or purlins. Perhaps no avoiding long screws down into rafters here.
Thanks again!
Quinn,
You have lots of questions -- so many questions that you might want to consult with an architect or an experienced builder. Sometimes homeowners find that learning everything about construction can be challenging -- and that's an argument in favor of hiring experts to help you.
Some comments:
1. If you decide to create overhangs by allowing your rafters to penetrate your air barrier at the ceiling/wall intersection, you are going to have a lot of air leaks. The best way to handle this problem is to install an air barrier (for example, taped drywall) on the underside of your rafters. If you insist on leaving your rafters exposed on the interior, these rafters should stop at the plane of the exterior walls.
2. The use of "wood cladding" as an interior finish material on your walls is risky (depending on your insulation details). Most walls need an interior air barrier. MemBrain can sometimes be detailed as an air barrier, but it's fragile. I don't recommend the use of polyethylene as an air barrier. In general, taped drywall works best at this location. If you want to install boards on the interior side of the drywall, you can.
3. Using a wood stove in a tight house can be tricky. You may need a ducted source of combustion air, or you may need to get used to opening a window when you light a fire.
-- Martin Holladay
Hi Martin
Yes many questions, apologies! The building is being designed by an experience prefab manufacturer but I am trying to inform myself as much as possible. I've taken a PassivHus building envelope course and undertaken a couple major refurbishment projects in the UK, however always trying to learn more!
Noted re your comments. I'll take that into account, drying walling without the need to have a nice finish is something we may need to consider, then covering the drywall with our chosen material.
Thank you