Energy Upgrades for a Historic House

We’re looking at buying a 4000+ square foot federalist style building from the early 1800s in Zone 5 (Massachusetts). It’s constructed like three standard gable houses of decreasing width in a line, with an attached garage on the back. The front section is brick with a slightly protruding (cantilevered) clapboard gable, and the rest is clapboard. I’ll be finding a lot more about the construction in the next week, hopefully.
I’ve found that the current owners go through about 2000 gallons of heating oil per year.
So, for now suppose the brick is structural and the house is post framed. Where is the most bang for the buck going to be reducing energy costs? How even do you air seal a building like this, especially if you want to avoid interior renovations (except maybe sealing and insulating a walk up attic.)
GBA Detail Library
A collection of one thousand construction details organized by climate and house part
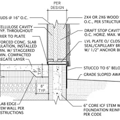
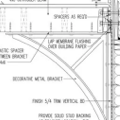
Replies
John,
How is the basement constructed? What is on the roof (condition?)?
Just as an immediate return on top of air sealing, I would first just find an alternative energy source. Oil has recently been cheaper but it is going back up I believe. Just switching to gas a few years back saved me a lot of cost, I burned 800 gallons a year at almost $4 per gallon with a house much smaller. The furnace was ancient though. There are better sources than natural gas readily available but changing over and then finding ways to insulate will help keep costs down. You have to be careful insulating an old home for many reasons, you will find more information on this site. Also in a old home be prepared for hidden problems, confusion, and the need for smart or at least highly trained contractors that work with older homes.
Most bang/buck is clearly air sealing, but the construction details matter. Can't really advise there without more detail.
Is it the original antique windows? Are there storm windows? Are new windows or storm windows even an option? (Any historical district limitations or personal aesthetics limiting that?)
How much of the interior side of the exterior walls are you willing/able to gut & do over? Is exterior insulation an option?
What sort of heating system is the 2000 gallons of oil being burned in?
The heating system is a boiler for forced hot water.
I should have answers to a lot of the construction questions on Friday, so I'll post an update then.
Regarding the title of your post, I like to tell my customers that "we can fix anything, if you are willing to write a big enough check". We could build an entirely new building, for example, although that's a pretty drastic way to "fix" anything :-)
Old double hung windows are notorious for air leaks. You probably won't have much in the way of insulation in a home that old either, unless it's undergone some level of energy upgrades. I completely agree agree with Dana regarding air sealing, and note that brick can make that tricky since you don't want to get into a situation with trapped moisture freezing in the brick. The more detail you can provide about the structure, the better the advice you'll get as to what to do to make things better.
The short answer is you can absolutely improve on the old home's energy performance, but it might be pretty expensive to do.
Bill
Regarding the idea of changing your energy source, this might be of interest: Heating Historic Houses With Heat Pumps.
I'm very curious to hear more about this thread and look forward to future replies. I have a 175 year old house in central MA (Zone 5) built into a hill with a walkout basement. The basement above grade brick (front) wall where you walk out faces south and gets LOTS of direct sunlight. The west wall is also brick and mostly above grade. The other 2 below grade walls of the basement are stone/rubble? I need to do a water and air control layer very very badly all over the house. I want to at least pop out all the (not original-vinyl 20 yearold) windows and properly flash and air seal the window openings and then figure out the best method for thermal control layer all around the house. Seems doing it from the outside to address thermal bridges would be best but am ok with gutting the house and probably will anyway. Then I want to do cold weather heat pumps and put solar panels on the south facing roof which gets hammered with sunlight all day.
haha, I'll make my own thread about this but I eagerly await comments about this thread!
Before you do anything consider this old house survived because whatever water gets into the walls is able to evaporate and get out before anything starts molding and or rotting. The old window flashing was generally very poor by today’s standards but it was good enough because the walls were uninsulated and leaked air like a sieve and things dried quickly, in short lots of heat energy in the walls to evaporate the water and lots of air movement to carry the moisture away.
If you really want modern insulation and air tightness you must almost start over with modern flashing details and air gaps between the missionary and the carpentry this is no small feat and impossible without disturbing the old work.
Walta
Thanks for your reply Walta. Yes, it seems like a lot to do, I essentially need to create a building envelope because there is essentially NO water or air control now. And while that allowed things to dry things have indeed rotted and molded. At least 2 structural beams in basement have rot and WDI damage and I think the whole back/north side sill needs to be replaced. These were put in 175 years ago and are basically the thousand year old wood (and rocks) that Joe Lstiburek talks about. Otherwise they'd be long gone I think.
It seems to me that putting an air and water control layer over the whole house from the outside would be the most straight forward since the siding on the top 2 floors above the basement needs to be replaced anyway (walk out basement in front is exposed brick with nothing on the interior side either - you can see outside through the brick in spots) and roof is over 30 years old and needs to be replaced too.
I'm assuming the "sheathing" under the siding on the middle and top floor is not even contiguous and is boards with gaps so I'm thinking maybe a whole house application of something like Proseco/fluid applied WRB for the air and water control. I don't think I need new sheathing for structural reasons so it seems instead of Zip or some other OSB w/integrated WRB that a fluid applied or stick on WRB would make sense. This would set me up to then safely put a thermal control layer on this very old house to finally keep some heat inside I think. Would you say so? The basement which is a brick wall above grade on the south and west sides facing the direct sun, and then stone below grade on the north and east sides, I'm not sure about for the WRB, which I know has to be continuous around the whole house.
Okay, so I got in the place with an inspector, and I was pleasantly surprised. It's in, as it goes, pretty good condition. The original structure is essentially a post and beam framed wooden box with a brick exterior. The brick, above basement level, does not appear to be structural, but that's an educated guess by the inspector. The barn/garage is also post and beam. The garage and original house have been joined together with modern additions that are stud framed.
It is not a historic building. Literally the next lot over is the start of the historic district. It has recent additions, some vinyl siding, and "modern" windows. By which I mean 20-70 year old replacement windows, some with storms, some cracked, with lots of loose glazing and flaking exterior paint.
There's some clear low hanging fruit. The attic has a whole house fan that I think isn't doing the house any favors. There's also a single glazed window in the finished original-house attic that opens onto the unfinished vented attic of the addition. I could feel the heat coming through. I think we'll need to get MassSave to do a thermal camera audit in the winter to see where the major problems are.
The foundation is fieldstone and brick, so I don't think I can do much there. The gutters and downspouts need work. There's some bare dirt in the basement that I'll cover up with plastic and a slab.
The heating system is also a challenge. It's a ~15 year old Weil McLain boiler with 5-zone hydronic + indirect hot water with cast iron baseboards and some radiators. Word is that the gas pipe is down the block and would be expensive to run over. There are also a pair of 20ish year old mini splits that provide cooling to portions of the house. The house does have 200 amp service.
That's the state of things. So, clearly improving the windows and fixing the attic will help. I'm not clear on how to improve the brick areas. Even if the brick isn't structural, it's 200 year old brick in decent shape that I don't want to wreck with freeze-thaw. I would like to improve air sealing, but I'm not sure how to do this with brick. The modern additions should be straight forward to handle though.
>"The original structure is essentially a post and beam framed wooden box with a brick exterior. The brick, above basement level, does not appear to be structural, but that's an educated guess by the inspector."
That should really be verified before making any big changes on the exterior walls.
>"It has recent additions, some vinyl siding, and "modern" windows. By which I mean 20-70 year old replacement windows, some with storms, some cracked, with lots of loose glazing and flaking exterior paint."
What is under the vinyl siding? (Painted brick?)
It sounds like window replacement with something higher performance and more consistent than the current random collection might be in order, but when, what & how kind of depends on what you decide to do with the walls.
>"The foundation is fieldstone and brick, so I don't think I can do much there."
Au contraire!
Brick & fieldstone foundations usually leak copious air, and can be brought up to current insulation standards with 2" of HFO-blown closed cell spray polyurethane foam. Air sealing the BOTTOM of the house is as important as air sealing the attic, since the distance between the big leaks a the bottom to the big leaks at the top determine how much 24/365 "stack effect" infiltration is happening.
>" I think we'll need to get MassSave to do a thermal camera audit in the winter to see where the major problems are."
A $200 FLIR One IR camera attachment for a tablet computer or cell phone can do quite a lot. Taking it a room at a time, a cheap FLIR and a $100 big-ish window fan (eg: Lasko W16900 ) for pressurizing/depressurizing the house a room, wing (or sometimes a whole floor) at a time can be help nail down the location of the worst offending leaks with a bit of diligence. MassSave won't usually do blower door tests or IR imaging on the first pass, but you can, and it'll save time (=money).
>"Even if the brick isn't structural, it's 200 year old brick in decent shape that I don't want to wreck with freeze-thaw. I would like to improve air sealing, but I'm not sure how to do this with brick."
With decent roof overhangs the brick won't be chronically wet enough to cause problems after insulating it with a flash-inch of closed cell foam on the interior. In some cases it'll be possible to insulate with cellulose, which will share the moisture burden with the brick, but that has to be analyzed by a true expert. If doing a full-gut on the interior, giving it a half-inch air gap between the brick and the next layer, adding vents & weeps for the gap to convect to the exterior will help keep the brick dry, behaving like more recent modern brick veneer walls do. If they can use these solutions successfully on double-wythe structural brick in Ontario & Quebec (which they do) the more temperate climate of Boston makes it comparatively easier & more forgiving.
Use the whole house fan for your own blower door testing.
Whole house fans can be really nice to cool things off if you have the right climate for them. You may want to upgrade to one of the modern ones that actually does a good job of self-air sealing when not in use. The older ones just had some spring operated louvers that are typically VERY leaky.
BTW, I second Dana's suggesstion of trying a DIY blower door setup, but I would use some smoke sticks and not just a cheapie IR camera. I have found the cheap IR cameras for phones and tablets can be really hard to get useful info from (and I do have one myself), due in part to the low resolution, but also due to the lens. It can be difficult to figure out what you're looking at sometimes. Smoke sticks are easy to use, and it's east to interpret the results they provide too.
Bill
The vinyl is in the more modern additions that do not have brick.
I have concerns about insulating fieldstone with. I had a 1870s fieldstone basement, and the mortar softened over time and needed significant repointing.
If I put 2" of spray foam on this fieldstone, would it not stay more wet, get cold faster, and be more vulnerable to frost heave? As I recall, you're supposed to use lime mortar when repointing old walls specifically because modern mortars are less water permeable and will speed wall damage. CCSF would seem to hold back the water and also make the wall almost impossible to repoint.
I guess here's my concern: CCSF would certainly make the basement itself warmer and less moist. But 20 years down the road am I going to seriously regret it?
>"I had a 1870s fieldstone basement, and the mortar softened over time and needed significant repointing."
The mortar gets soft from moisture MOVING through it, taking away minerals with it. If you repair any mortar issues and install ~0.5 perm foam insulation on the interior side the moisture stays put and hits saturation of whatever is being leached, rather than moving it out and replacing it with new, unsaturated ground water.
>"If I put 2" of spray foam on this fieldstone, would it not stay more wet, get cold faster, and be more vulnerable to frost heave? "
The stone & mortar stay a bit wetter, but frost heave is from what happens to the soil, which will be pretty much the same as it was before.
Frost heave requires wet SOIL that dwells below freezing for several weeks. If it never gets cold enough or wet enough the risk isn't there. If the If the footings under foundation walls are above frost line there is some risk of frost heave, but that's a matter of how well drained it is. A perimeter drain to keep the soil near the bottom of the foundation interior or exterior will fix that too.
What happens when the fieldstone and mortar gets cool enough for the water to freeze during the winter? I mean, I guess it was already moist previously, so this was already happening on some scale.
I'm also concerned about moisture in the sill, since the exterior brick I would expect reduces exterior drying and prevents me from jacking the sill up to install a waterproof membrane. Any thoughts?
>"What happens when the fieldstone and mortar gets cool enough for the water to freeze during the winter? I mean, I guess it was already moist previously, so this was already happening on some scale."
I think you already answered your own question. Fieldstones aren't much affected by freeze thaw when laying around on or near the surface in the field, and are if anything DRIER when used in a foundation. The structural contact is stone-on-stone- the mortar is just there as a sealant and to help keep the stones from sliding, and not much affected by freeze/thaw too.
>"I'm also concerned about moisture in the sill, since the exterior brick I would expect reduces exterior drying and prevents me from jacking the sill up to install a waterproof membrane. "
Neither fieldstone nor (most types of) brick have anywhere near the wicking potential of concrete, limestone, or cinder block/CMU. It doesn't take very much above grade exposure on the exterior to provide an adequate drying potential for this already much lower ground moisture wicking issue. But before insulating the foundation, testing the sill in multiple locations over multiple seasons with an inexpensive 2-prong wood moisture meter to verify moisture content doesn't hurt. It won't likely change much after insulating, unless the basement was fully heated keeping the brick 10s of degrees warmer in winter. Most early 19th century homes were barely heated at all (even in the living spaces) in their early years, and the construction methods & materials were adapted to that lack of heat.
The frost heave issue is also affected by a lack of heating. Unheated air leaky structures are at much higher risk of frost heaving, since the entire basements could drop below freezing (indoors). The direction of the heave follows the direction of heat flow, so when a basement is 25F and the soil n the other side of the foundation wall is 35F the flow is from the soil toward the basement. As ice crystals form on the colder stones it pushes the stones in toward the basement. In warm insulated (even if not fully heated) basement the heat flow is in the other direction, and even if ice crystals form it only has the insulation and indoor air to push against- it goes nowhere.
It's fairly common for slabs in unheated breezy New England barns & garages to buckle from frost heave, less common but still possible for the foundation walls in those buildings to frost heave. Frost heaving foundation walls or slabs in conditioned heated houses is all but unheard of, independent of foundation material.
How about the heating system? From what I've found, gas is not available. I think the oil boiler is from 1997, so it's probably time to consider its replacement. Should I consider solar + air to water heat pump keeping the hydronic system? Or should I abandon the hydronic system and go with a ducted system or mini/muliti-splits. (The layout is probably not conducive to mini-splits.)
2000 gallons of heating oil/year makes switching fuels easier to justify on a economic basis (plus heating oil is awful environmentally). Air to water systems are less common compared to ducted systems and you'd have to have enough radiation to use water lower temperatures, or have backup (existing boiler or electric) for the coldest days. Maybe ask if you can get the actual oil receipts? Also, figuring out how much of the house was heated during the winter and to what temperature would help.
A quickie heat load estimate:
2000 gallons over 5500 annual heating degree days (the recent -decade average at Logan Airport) is 0.36 gallons/HDD. At 138,000 BTU/gallon and 85% efficiency that's 0.36 x 0.85 x 138,000= 42,228 BTU/HDD, or (/24hours=) 1760 BTU per degree-hour.
At a base temp of 65F and a 99% design temp of 12F (the 99th percentile temperature bin at Logan, that's 65F-12F= 53F heating degrees. 53F x 1760 BTU/F-hr = 93,280 BTU/hr
To deliver that much heat at +12F would take 6-8 tons of cold climate heat pump, which would be pretty expensive up front. Spending as much as half the heat pump price on lowering the load with air sealing & insulation could conceivably bring the block load down to the 4-5 ton range, and if window upgrades are included it could conceivably even hit 3.5-4 tons.
To address whether/when to retire the boiler...
What is the DOE &/or IBR output BTU spec on the boiler?
What is the high limit set to on the boiler?
Is it operated as a single zone, or is it broken up into multiple zones?
What type of radiation? (Bulky cast iron, tall convectors, fin-tube baseboard or ...???)
Don't assume that because it's old enough to vote (is it registered? :-) ) that it's on it's last legs.
Most oil boilers can go 40+ years with some maintenance, and even if it's 3x oversized for the design load it can be made to operate at reasonable efficiency using retrofit heat purging economizer controls, and possibly down-firing it to a smaller gph nozzle (after analyzing the system in greater detail.) Unless it's showing signs of excess wear tear (can it still be tuned to better than 80% combustion efficiency?) or it's leaking it's better to plan on fixing up the thermal deficiencies of the house first, and continue to monitor wintertime fuel use against heating degree day data to better track the real heat load. For detail on how to run the load numbers by fuel use see:
https://www.greenbuildingadvisor.com/article/out-with-the-old-in-with-the-new
So, a year later, I have a little better data. I'm estimating around 1600BTU per degree hour at 60F or 1400BTU per degree hour at 65F, based on 80% efficiency. But... we've been having flame issues and it appears we've had a bad pump for a while. So our furnace might not have been consistently maximally efficient. Based on a 2F 99% design temperature, our 99% heat load is around 90000BTU. There's probably a lot of room to improve that with some air sealing and insulation.
Today though, we found the boiler is on its last legs. We have discovered an intermittent water leak.
So, given that the boiler has to be replaced, what options should I be considering?
Additionally, should I consider a condensing sealed-combustion direct vent oil boiler? How about condensing? I admit some concerns about the corrosiveness of oil boiler condensate?
Bottom line, no. The quality of the available #2 oil in this area doesn't really cut it for condensing oil boilers or super small nozzle sizes, and it becomes a maintenance PITA for very marginal gains in efficiency. (Condensing oil boilers work in parts of Europe, but not New England.)
Don't replace the boiler until you've fixed up the house. On a house in this condition there is more oil to be saved by making the HOUSE more efficient than making the BOILER more efficient via condensing. A tuned-up 1997 vintage boiler (got a model number?) can usually still hit the mid-80s for raw combustion efficiency, and with a heat purging economizer control the as-used AFUE can come pretty close to the raw combustion efficiency.
The engineer just went through today, and confirmed something that I wondered about. The entire support of the first floor of the house has been redone, and doesn't actually rely on the original foundation. It's unclear whether the second floor framing is supported by the brick or through the first floor.
What this means, though, is that there are a bunch of wood girders all around the outside of the basement on lally columns that are inside the foundation. This might be pretty easy to insulate without worrying about trapping moisture in wood.
Oh wow. Interesting. I can sort of relate to this also. Would love to see photos of this and hear what you’re thinking (and GBA folks) for control layers with this new info.