Cement board “slab” on grade

Hello GBA folks,
I’m in the process of designing a house in zone 7/8 and would like your feedback on this design idea.
Instead of a concrete slab on grade, glue 2 layers of cement board, such as 1/4″ Hardie board to each other and to 3 or 4 inches of EPS foam. Offset each layer to avoid matching seams. Prepare the bed with crusher fines and perhaps sand to get level and compacted surface for the foam. This might be difficult? Add a vapor barrier below the foam. Finish floor with tile, carpet (glue tack strips to cement board), etc, but I’d like to use cork.
Benefits are cost, doable by homeowner, easier to fix if needed. no wood in floor in case of water spills, and can build in a chase for utilities to make repair easier.
Resell/banker issues is a concern. It would be a cement floor though. Maybe that would help?
Seems like this would be structurally sound for pianos and other stuff, but probably not non-load bearing walls. Is there a better material than cement board or add more layers?
Sorry if this has been discussed before. My googling found nothing. What do you think?
Mike
GBA Detail Library
A collection of one thousand construction details organized by climate and house part
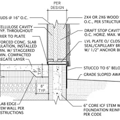
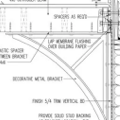
Replies
Sorry, I forgot to mention there was a GBA thread where someone suggested that a concrete slab is not needed structurally and pointed to this website where they use metal studs between the foam. Seems like though gluing to the foam would be sufficient. Sort of like a SIPS.
http://www.polycorecanada.com/products/residential-foundation-floors
Honestly, it's a terrible idea. Yout cost savings would be negligible if any, cement board isn't approved for use as sub flooring, your flooring installer will hate you and will probably refuse to do the job, grading your floor perfectly level will be difficult , there is no provision for column loads or bearing walls, you have no substrate to attach the cement board to, etc. I don't think this is an area where it pays to reinvent the wheel.
Mike - I agree with Rick. I have considered using 2'X 2'X2" concrete "tiles", stained and sealed, for a floor to be laid on 1- 2" of sand over poly over foam, but even this approach is much too labor intensive to be useful. You have to" pay" yourself SOMETHING for your time, or better said, you have to place SOME value on your time. Pouring a concrete floor is a one day event and it's done. Provisions can be made in certain areas to facilitate changes down the road( like lots of conduit for plumbing or electric lines), but it is a material that is fairly unforgiving.It takes planning.
Thanks Rick and Kevin for your thoughts. The material cost is a savings for sure but yes time is money. Getting a compacted sand base level is something I've never done so I don't really know how much time or difficulty is involved. The polycorecanada (web link above) folks use this in their design though. Layering and gluing foam and cement board seems like it would go quick except for edges which would slow you down.
My first floor design has very few non-load bearing walls so I'm not thinking that issue justifies the concrete slab too much.
I suppose one could glue down (and screw) a few layers of OSB instead of cement board to get more rigidity, use an approved subfloor material, and make it easier for flooring installer (likely me).
This idea may not be that great but I agree concrete is unforgiving (has to be done right and when done poorly it is a major pain). I hope someone figures out a good way to reinvent this wheel :-)
Mike,
If you switch from cement board to two layers of 3/4-inch plywood (installed with staggered seams, and screwed together), this idea would probably work.
You still need concrete for your perimeter footings, though. If the Ready-Mix truck is delivering concrete for the perimeter footings anyway, why not just build a thickened-edge slab or a frost-protected shallow foundation?
Disadvantages to your idea: probably no cost savings, and it's a detail that makes the house very difficult to sell.
Here is a link to an article that discusses an idea that is similar to yours: Do I Really Need a Concrete Basement Floor?
Thanks Martin. Are you thinking the 2 sheets of 3/4" OSB are needed in lieu of cement board is due to structural reasons? I don't like the idea of putting wood down where water can't easily escape.
Another thought is to add concrete blocks in areas between footers during the leveling process. They could act as guides for tamping the sand or dirt and would also allow a place to glue down the foam.
The resell/banker issue is huge. I suppose its just wishful thinking that a few layers of cement board could be considered a "slab". On the flip side, concrete is very good at hiding future problems. I've lived the resell problems with cracked and settled concrete as well as the hassles of a poorly done crawl space. Both can be done right but seems like there should be a simpler more efficient way.
Mike,
Often the logic of commonly used construction techniques and materials doesn't seem apparent until you have built up some experience. Just as you might want to do a bit of cooking before deciding you want to substitute the ingredients in common recipes, the time for fundamentally re-thinking how you want to build should probably be reserved for then you really understand what you are rejecting.
Thanks everyone for your thoughts on this. It seems the issue are the time involved and acceptance in a world where there are lots of dollars involved. Best to try it in small applications first.
Martin - yes I'm open to both of those foundation options. I'm probably being driven less by a desire to save $ or concrete and more by trying to design a house that I can modify and work on easily myself.