Closed-cell spray foam between studs with various exterior continuous insulations

I want to make a few questions very explicit to get some good solid answers.
Concerning the use of continuous insulation on the exterior of a wall assembly – we know that the use of any rigid foam (perhaps with the exception of mineral wool boards) will severely limit or eliminate the potential for outward drying. With this in mind it becomes necessary that any rigid exterior foam we do use is thick enough to keep the interior moisture accumulation surface above the dew point during the heating season. – and further that any materials inside of this moisture accumulation surface be vapor open enough to allow inward drying – since little to no outward drying will occur.
Although closed cell foam used between the studs will eliminate the possibility of inward drying from the inside surface of the exterior insulation – it does not of course limit drying from its own inward surface – and since the close cell foam’s inward surface is the new moisture accumulation layer we should be able to conclude that an assembly with thin exterior insulation and enough additional closed cell foam between the stud bays will not allow moisture accumulation VIA moisture condensing out of the warm interior air at the inner face of the closed cell foam.
Why then is installing closed cell foam between the stud bays with exterior insulation a potentially bad idea? The only reason I see is this: (In most situations), we will have sandwiched a layer of moisture sensitive/rot prone sheathing between two impermeable layers – such that if water should soak into this layer – say at a poorly detailed window flashing – it will be very difficult for that layer to dry out, thus rot will occur.
But, and this is my question – if our exterior insulation is such that the foam insulation is directly against the framing – such as with ZIP R sheathing – then spaying closed cell foam does not leave a moisture sensitive layer sandwiched between two impermeable layers – and is therefore a good solution for solving the issue of ZIP R being too thin for colder climate zones.
Can you confirm that this line of thinking is all correct?
GBA Detail Library
A collection of one thousand construction details organized by climate and house part
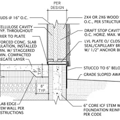
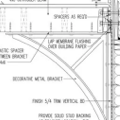
Replies
It's fine to put closed cell foam on the interior surface of ZIP-R to limit condensation inside the stud bay in colder climates.
But in colder climates the performance of the ZIP-R will be well below it's ASTM C518 tested & labeled R value.
At 1" most 2lb closed cell foam isn't even a class-II vapor retarder, but at 2" it is. But if you don't need more than a flash-inch for dew point control (which you don't in a 2x6 assembly with 1.5" ZIP-R, except in the colder half of zone 7 and in zone 8)) there's no point to doing any more than that inch, since the R-performance is so severely undercut by the framing.
At 2" unfaced 1.5lb density (Type-II) EPS is not even a class-II vapor retarder, and doesn't dramatically impede drying toward the exterior, since it has a higher vapor permeance than the OSB sheathing most of the time. That's sufficient exterior-R for dew point control with 2x6 / R23 studwalls in US climate zone 5 (which is better than code), and 2x6 / R15 studwalls in climate zone 6 (which is just shy of IRC 2012 and higher code-minimums). And since the OSB is inside the insulation layer it's better protected from exterior moisture drives than ZIP-R.
Why wouldn't you use 5.5 inches open cell foam, regular Zip with the taped seams and an inch of unfazed EPS? Dana, am I wrong about this being a good stack up for a lower environmental and dollar cost to the builder?
Patrick,
Q. "If our exterior insulation is such that the foam insulation is directly against the framing - such as with ZIP R sheathing - then spaying closed cell foam does not leave a moisture sensitive layer sandwiched between two impermeable layers. Therefore, is this a good solution for solving the issue of ZIP R being too thin for colder climate zones?"
A. It's one possible solution; I'm not sure whether I would go so far as to call it a good solution.
One thing that I've learned over the years is that builders have strong opinions about wall assemblies, and it's hard to change people's opinions. If you like the approach, go ahead -- the approach you describe won't have issues with moisture accumulation.
My only comment: many green builders try to avoid the use of closed-cell spray foam, because it requires the use of blowing agents with a high global warming potential.
Joe: Open cell foam is too vapor-open to be used that way unless there is sufficient exterior-R for dew point control at the OSB. An inch of EPS (R4-ish) is not for dew point control on 2x6 / R23construction in zones 5 & up, but would be fine in climate zone 4.
But in zone 4 ZIP-R would give you higher performance than an inch of EPS in US climate zone 4, and would be a thinner wall. The value of ZIP-R relative to it's cost isn't always rational in colder climates where it's performance is lower lacks sufficient R for dew point control even at the labeled-R. But for zones 4 & lower it can be worth it, especially when dealing with crews unaccustomed to exterior foam installation.
Thank you for your response Martin,
Indeed, I should not have written "good approach" - rather safe from a moisture management stand point - which is really all my question was concerning (which is not to say I am not interested in what's cost effective, practical, or environmentally friendly)
One issue that I didn't get into but that I run into where we build is the fact that although we are only located in climate zone 5 - it isn't uncommon for architects to spec wall assemblies with total values up to R38 - so even though the IRC might say R7.5 continuous insulation on the outside is safe, with another R30 on the inside we might be getting into trouble depending on how that remaining R30 is achieved.
Thanks again.
It's the ratio of the exterior R to the total that matters if the interior side is going to have a vapor permeance greater than 1 perm, since it's the ratio that determines the average wintertime temp of the sheathing or first condensing surface, depending on context.
It's a good idea for the vapor permeance to be greater than 1 perm either in one direction or the other of a moisture-susceptible material such as wood sheathing. Better still is to have it above 1-perm in both directions, and protected from wintertime moisture loading by the R-ratio. In climate zone 5 wall assemblies that's about 25% of the total center-cavity R being on the exterior, 40% for unvented roof assemblies.
Exactly - the point being that just saying R7.5 on the outside is safe in climate zone 5 isn't necessarily the case.
As follow up question - we have clients that will be having a whole house humidification system included in their HVAC. From what I can tell if we assume that they will keep the house at 70 degrees and 45% relative humidity this will drastically change safe ratio of exterior to interior insulation. We are located in Boulder CO - zone 5 - and from what I can tell with this situation we need a min. of 65% or more of the insulation outside the moisture accumulation surface - which in the suggested assembly would be the inside of the closed cell foam. Can anyone offer more on determining the ratio when the homeowner will be humidifying the home?
Patrick,
Q. "Can anyone offer more on determining the ratio when the homeowner will be humidifying the home?"
A. Here is a link to an article that will explain everything you need to know about this sort of calculation: Are Dew-Point Calculations Really Necessary?
I there is 1-perm or lower materials between the susceptible sheathing and the interior 45% RH is just fine. The dew point of 70F/45% RH air is about 48F, as long as the winter AVERAGE temp at the first condensing surface is 48F there will be no moisture accumulation. The presumptive dew point built into IRC code for zone 5 is something like 38-40F so elevating the dew point by 8-10F does require the first condensing surface to be closer to the interior than code, but not a huge amount closer.
For zone 5 the prescriptive exterior R to the first condensing surface is ~25% of the total center cavity R. The binned hourly mean temp over the coldest 10 weeks of winter is about +35F. If you presume a mean interior temp of 70F, (35F above the average winter temp) the location within the insulation layers that averages 48F is (48F-35F)/35F= 37% of the way in from the exterior. With a ratio of 37% of exterior/total you wouldn't even need latex paint as a vapor retarder- bare air-tight wallboard would be sufficient.
If you bumped it to 35% it would be more than sufficient, but it's not even necessary: If you're concerned about the stack-up, a layer of Certainteed MemBrain is a heluva lot cheaper & greener than another inch of closed cell foam, and would operate under 1 perm (a class-II vapor retarder), slowing the average migration of water vapor into the cavity, without signficantly slowing it's escape.