Closed-cell vs. open-cell foam for insulating mudsill/rim joist

Hi there,
I’ve been working with a spray foam contractor to insulate the mudsill / rim joist area on the top of our 1890’s home in Boston (climate zone 5a). The house has a fieldstone foundation, with large beams (directly contacting the foundation) that serve as both mudsill and rim joist. We have the typical high humidity in the basement as one would expect. At this point the basement is unfinished, although we have a vision to finish it at some point in the future.
The contractor recommends open cell foam (8 inches depth for R-30), and while he understands the value of closed cell in preventing winter condensation, he says that the depth of the open cell would suffice as a vapor retarder. Is that a reasonable proposition, or should I be pushing for the use of closed cell?
GBA Detail Library
A collection of one thousand construction details organized by climate and house part
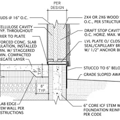
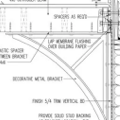
Replies
Closed cell in this location would be best, if done coorectly.
Foam guys have to switch and clean out hoses when going from open to closed cell or vise versa. They don't like doing anymore than they have to.
I really dont care if they want to, they must do it for a rim joist area as far as im concerned!
8 inches of open cell spray foam would still be pretty permeable (~8 perms), and so is vulnerable to some winter condensation. By code, you would need to use a class I or II vapor retarder on the interior of the assembly to reduce condensation risks.
Open cell foam is way too vapor permeable to use on cold above grade field stone foundations. Over the winter it will accumulate moisture in the foam on the cold side, and it doesn't take very much moisture or very many freeze/thaw cycles for it to separate from the stone. (It'll usually stick to the wood just fine though with most of the moisture going into the wood.)
This definitely calls for a closed cell solution for at least the first 30% of the total R. Code minimum is R15, which would be almost there with 2" of HFO blown closed cell foam (R13.8-R14). That's more expensive than 8" of open cell, but you don't really need R30 anyway, especially if you're not actively heating & cooling the basement.
When it comes time to finish out the basement installing a studwall as close as possible to the foam and use blown fiber insulation to raise the performance. It would be fine up to an additional ~R30 of fiber insulation before wintertime moisture accumulation at the foam/fiber boundary at the above grade section becomes an issue.
High humidity in a Beantown basement is usually a summertime air leakage problem. While it will still likely need some mechanical dehumidification after sealing & insulating with 2" of closed cell, it won't be nearly what it was before.
Deleted
Off topic comment....We were in driving about in Medford and Somerville last weekend as my grandaughter was playing in the NCAA D3 Womens' Lacrosse Playoffs for Tufts.. It was fascinating to see how the area, once heavily working class and a little down-at-the-heels seemed to be full of block after block of old homes (probably turn of century) that appeared re-sided, or were undergoing re-siding and new window installations....lots of Tyvak where there wasn't new siding. Looked like a lot of general upgrading and energy efficient improvements. BTW, her team is headed to Virginia for NCAA semi-finals and finals starting Saturday.
Probably some renewal going on. It’s good to see these historic areas getting restored, there are a lot of neat old buildings out there. The federal hill area of Baltimore is like this, and pretty much that entire area has been reworked and is really nice now — and pretty much fully occupied. Good to see.
Good luck to your granddaughter and her team! If you like seafood, there are lots of great places in Maryland and probably the eastern side of Virginia too.
Bill
Having lived in a few of those old triple deckers & duplexes in Somerville (as rentals) I can vouch for just how much low-hanging fruit there is on the efficiency tree there is for most of them. As condos or single-family homes the budgets for fixing the comfort and efficiency problems of that housing goes way up. I can't quite believe what some of those places are selling for now compared to their assessed values ~30 years ago when I helped a family with a full-gut rehab on a house in North Cambridge. The concept of "affordable housing" starts to feel pretty academic in those former working class 'burbs. (Affordable for whom?) Could former Somerville mayor, former congressman Mike Capuano afford to buy his own house now? Maybe...
Fixing that housing stock up is sure a lot greener than the full knock-down, replace-with-McMansion action going on in some of the less-dense suburbs of Boston.
Yeah, us poors have to live further down the (non-functional) tracks now
Would it change the recommendation from closed to open cell if the exterior was wrapped in say 2” of faced polyiso? It would then need to dry to the interior?
I'm not sure how the above grade foundation could be wrapped with 2" foil faced polyiso.
If it's just the band joist that has the 2" polyiso you could get away with ~6" of open cell (the most that can be safely applied in a single pass) on the wood only, but that won't seal the mudsill to the foundation reliably for the duration. The foam in contact with the foundation would still have potential moisture accumulation and frost damage separation over time if open cell foam were used.
Not to hijack his thread but since the op is on the path to energy upgrades. I was referring to the exterior wall/ band joist if it were wrapped with impermeable insulation (faced polyiso) on the exterior. As the band joist can wick moisture from the rocks/ blocks since they did not use capillary breaks back then. I was under the impression that a vapor open interior insulation should be used. I imagine you would want to control basement humidity levels?
Most fieldstone doesn't have anywhere near the wicking capacity of poured concrete or CMU, making capillary break is less critical. Quarried limestone might have that issue, but not granite or basalt, etc. Most field stone in Boston is low/no wicking igneous type rock.
With foil faced foam on the exterior of the band-joist only (and not the foundation) it's fine to use 2" of closed cell on the interior. Most closed cell foam is still more than 0.5 perms @ 2"- it's not the same moisture trap that a true vapor barrier would be.
Basement humidity in the "-A" climate zones is almost always about summertime air leakage from the outdoors into a basement at or below the dew point of the outdoor air, and literally never about vapor permeance of the wall insulation. It can sometimes be related bulk water seepage through the walls, or from the soil to a slab that has no vapor barrier, but even that is rarely "the" reason for high indoor RH.
In Boston the subsoil temp (and often the slab temp, even in summer) is less than 55F, and the mean outdoor dew point over the summer is north of 60F. Stopping the outdoor air infiltration fixes the first 75% of the basement humidity problem, but it will still need some amount of mechanical dehumidification (or air conditioning) to manage it.
Any insulation to the interior will make the perimeter woof framing colder and therefore less drying potential. I don't see structures like this getting wet from wicking up through the rubble foundation; what I do see is poor surface water management such as splashback getting the wood assembly close to grade wet. Make sure you are managing moisture loads both inside and out as you take on this energy detail.
Peter