Concrete-Free Slab in Wood Shop
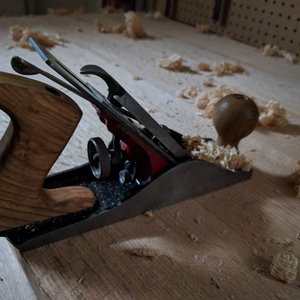
Hi All,
I just bought the acreage I’ve been dreaming about for years and I’m now in the planning phase for a roughly 24×40 detached woodworking shop. In an effort to limit the environmental impact of what is (mostly) a hobby, I’m trying to build the shop with limited energy use and embodied carbon in mind. A Pretty Good Woodshop, perhaps. I’m in Zone 6 in Minnesota and the plan is for a wood frame building on concrete stem walls. I feel like I have a pretty decent handle on the wall and roof details that would get me the performance I’m aiming for and avoid high GWP products like spray foam.
My question is about the floor. I’d really like to avoid pouring a concrete slab for several reasons. A wood floor would have less embodied carbon, be easier to stand on for long periods and would be something I could do myself rather than subbing out.
I could do a traditional platform frame, but that would require a ramp or step up into the building and all the more complicated details that come with insulating a crawl space (again, trying to avoid spray foam).
Recently, I’ve seen several articles from Michael Maines, Ben Bogie, Jake Bruton and others on slabless slabs with a double-layer plywood or OSB over EPS foam. This seems like an ideal solution, but I’m concerned about the heavier loads from my reasonably large cast-iron tools. Additionally, I’m considering a couple of interior walls for an office with lumber storage above, which would put some point loads in a few places.
I understand the theoretical compression math—25 psi EPS should hold 1500 psf at 1% compression. None of my tools are over 1000 lbs, and all bear on at least 2 sq. ft. I would assume that double 3/4 t&g plywood would further distribute that load. Still I’m concerned that over the long term, there might be significant creep/compression that would lead to an uneven floor.
Does anyone have experience with these slab-less slabs in a situation where they will have higher dead loads than are typical in a residence? Am I stuck with concrete? Should I just pour a floor and upsize a future PV installation and call it even? Are there other low-carbon solutions that I’m not thinking of? Thanks in advance for the advice!
-Ben
GBA Detail Library
A collection of one thousand construction details organized by climate and house part
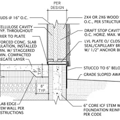
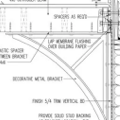
Replies
Ben,
Also another Ben here and I commend you on your consideration of a low carbon woodshop with a concrete free slab. I'm glad to hear you bought the acreage of your dreams as your dreams sound exactly like mine with a low-carbon woodshop and avoiding concrete where possible. So I've been thinking about this situation myself for both a woodshop and even the radical idea of a concrete free slab in a garage for cars.
From my understanding, the most important thing to ensure a solid slab-less slab is to have a solid and well compacted sub base that is nice and level. You want to make sure you have a nice base of well compacted gravel of about 6" that you compact in 3" lifts to make sure that it is all well consolidated. Then you can place your vapor barrier and then 2 layers of EPS foam above this, alternating the directions of the sheets (same as the plywood).
Another option to look into would be using Glavel as your sub base instead of gravel ( https://www.glavel.com/ ). This is a foam glass product that replaces gravel and provides insulation values. You could probably reduce your foam thickness and use a higher PSI EPS foam instead (if you can source it). However I suspect the 25 psi EPS foam is easier to source and paired with standard gravel will be cheaper overall.
If you are concerned about the loads from current or even future equipment and uneven settling, I suggest stepping up to thicker sheets of plywood like 7/8" or 1-1/8" as the thicker plywood will result in a stiffer floor that will be able to spread out the loads better. Or you could do 3 layers of subfloor, depending on if you prefer hauling fewer heavier sheets or more lighter weight sheets. In either case, be sure to screw and glue the layers together so that they work as one large plywood panel. Using an easy to apply subfloor adhesive like the foaming product from Advantech, will probably make the process easier instead of trying to use a traditional viscous subfloor adhesive.
On that topic, I would look at using Advantech instead of plywood as it is very stiff and has great water resistance with the waxes and resins built into it. This will help with long term durability as you work in the woodshop.
If you haven't seen it yet, Josh Salinger from Birdsmouth Construction gave a great presentation on Passive House Accelerator about their concrete-free slab construction process: https://www.youtube.com/watch?v=QO_kAsQsA2A
Hope that helps!
Great to meet another Ben with similar outside-the-norm building interests! I have read about Glavel, but haven’t considered it for this project specifically. You’re right, it could essentially eliminate the foam, other than perhaps a very thin layer to take up any slight inconsistencies in the Glavel and protect the vapor barrier. I’ll have to price it out. I’m worried that it might be expensive to get all the way to the midwest where I am, but it’s worth a look.
Also a great tip on the subfloor adhesive-I will look into that as well.
Yea, the Glavel could be pricey, especially if you are able to source reclaimed EPS in your area of the desired PSI rating or higher. Glavel is pretty lightweight so it's not like you are trucking actual gravel from NY to MN, but it would add embodied carbon to your project and costs.
Engineers use a 3X factor for long-term creep under sustained loads on foam, so 25 psi foam can really handle more like 8 psi, or 1200 psf. The PSI rating is based on 10% deformation, so in theory, 4" of foam could compress 0.4". Loads don't transfer directly down but spread out an an angle, so in reality it would likely be less than that, but to be conservative, I pretend the load will go straight down to soil.
I imagine that 0.4" deformation is too much for you; I'd want more like 0.04". (Every material deflects or deforms; engineering is largely a matter of limiting deflection so it's not a problem.) Deformation in foam is fairly linear so if you want 1/10 the rated deformation, you are limited to 1/10 the load rating, or in this case, 120 psf. That's four times more than allowed for residential living spaces and even more than for assembly spaces. But if the load isn't spread evenly, you could have excessive deformation.
Regarding two layers of Adventech vs. a single layer over sleepers, I prefer sleepers for reduced carbon emissions and because the math says that under normal loading it will perform fine. (And no problems after six years on the one project I've used it on says it works.) But many people seem to feel that two layers of Adventech is stronger. The math is beyond me to decide which is actually stronger but I think they are roughly equal.
Old mills often had thick, solid wood floors. If I were you, I'd consider a surface layer that can spread the load farther than either of the systems described above. Something like a first layer of 2x4s at 12" o.c. and a top layer of T+G 2x6s in the opposite direction would spread the load nicely.
The information on long-term creep is really useful—it’s understanding the engineering of how the load is spread that is a bit out of my wheelhouse. Without knowing how much the plywood or sleepers are spreading out the load, it seems like a direct-load scenario would necessitate at least 60PSI foam under a heavy tool with a relatively narrow base.
Your idea of the 2x4 frame got me thinking. My day job is currently in theatre design, where it’s common to use shop-made stressed-skin platforms (we call them triscuits, after the square wheat crackers) for scenic floors. Cost may become a factor here, but I wonder if I could build sections of 2x4 frames skinned with a thinner (1/2”?) plywood on both sides acting in tension/compression. That would spread the load out significantly. Then I could run a layer of t&g solid wood as the finished floor. I will have to contemplate that further—thanks for the reply!
I like the "Triscuits" nickname. In construction they are called torsion boxes. With the right materials, adhesive and fasteners they can work well, but many glues such as regular PVA wood glue have long-term creep that could be an issue. Epoxy or other higher-end ($$$) adhesives would probably work well.
Again, I had a similar idea I posted below. Great minds and all that! I concur with MM about using other adhesives that don't creep. Check with Advantech to see if their subfloor adhesive creeps over time and if you could use that for the torsion box triscuits or if you have to go with epoxy like MM suggested.
Micheal's points and assembly suggestions kind of gave me an idea. What are your heaviest tools and can you increase their footprint by placing them on a wider base without causing issues with accessibility or creating a tripping hazard? If you only have a few very heavy tools, you could build a platform for them to address the concern about loading without having to increase the capacity in the rest of your shop for just a couple of tools.
Do the math on your heaviest tools to see what size base you would have to build to get their loading down to the 120 psf that Michael suggests.
Carbon aside, a wood floor for a work shop would have several advantages over a slab. Much easier on edged tools when dropped, easier on the body when standing for long periods, and being able to fasten to the floor would all be great.
Unless you are buying industrial tools, the weight per square foot is not very high. Unisaw maybe 600 pounds. That weight on 4 points is hard on the finish floor
Standing in an antique boat work shop with wood plank floors last night, thinking that would be a cool if expensive floor.
There is EPS out there with much higher load ratings as well, 40PSI I've seen for sale locally from used suppliers. But I think some of the GEOFoam used for road base and so on gets up to 60psi.
At one point I worked on a project to replace a section of a factory floor for an automotive stamping plant. Loads were basically double stacked dies that weigh 100,000lbs sitting on wood blocks. The final flooring was end grain wood blocks. Over layers of crisscrossed Ibeams, etc.
An update, for anyone following along or finding themselves in a similar situation. I've done some further reading that has proven fruitful. It turns out that EPS Foam behaves like a linear elastic material up to 1% deformation. Shortly after 1% is the yield point in the stress/strain curve and the response is less elastic. In in other words, EPS deformed less that 1% will spring back. More than 1% can lead to long term compression. So at less than 1% deformation, creep is minimal.
For whatever reason, sheet foam is advertised at 10% deformation. So Type IX EPS (which is the most dense that is easily available for me) has a 10% deformation of 25 PSI and a 1% Deformation of about 9 PSI. That works out to about 1300 pounds per square foot. That's also not accounting at all for the way that plywood or sleepers would distribute any load to a wider surface area.
Since my heaviest tools are in the range of 800 lbs, and all bear on at least 2 sq. ft., I'm still below 1% deformation (roughly 1/32" in 3" foam) by a factor of three. The plywood or sleeper floor should make that an even more comfortable safety factor.
Here's a link to a bit more detail - https://www.geofoam.org/technical/
I'll try to remember to circle back next year once the shop is built and the tools have been moved in to let you all know if my coffee slides off the table in the direction of my cast-iron band saw...
bgoldendesign,
I was in a nearby cabinet shop and saw one of these in action. If you use a lot of sheet goods, you might want to consider making one:
https://www.youtube.com/watch?v=Pzg7ZZ57ydc
That thing is pretty clever! I’m not sure how you could lean four sheets of plywood on either side of it the way he describes, but the rest of it looks pretty useful.
Bill
I’ve had a few wood shops, all with concrete floors. I spent extra time installing below slab dust collection and electrical boxes, and it worked fabulously. If I were you (and saving concrete was the goal) I would pour a frost protected shallow slab (grade beam). The total concrete used is almost exactly the same as a 4’ stem wall and footing.
If you decided you didn’t like the concrete floor, you could always add flat 2x4 sleepers and sheet the floor with plywood.
Advantages of concrete:
Smooth and flat
Easier to sweep
Flame/spark proof
Easy to scrape dripped paint, glue, etc
More light reflective
Much easier to roll tools and machines
Can be repurposed much easier into normal garage
Resistant to bugs/rodents
Cons:
Reflects noise
Hard on feet (I use 2’x2’ interlocking foam tiles at work stations)