Cost of efficiency- case study

I have been watching several local builders evolve their systems over the last several years to increase air tightness and insulation. I just was in a new build and was told that the house was tested to .5ACH and the extra costs to achieve this was approximately $10k (CAN$). The majority of this cost is in labour.
The house is a single story, 4 bed spec home in CZ 7A.
The air barrier is the WRB, which is caulked to the foundation and bottom plates and then carried through the top plates to join the ceiling poly layer. Plumbing and mechanical penetrations are detailed with EPDM gaskets, ceiling lights are placed in air tight boxes made from construction scraps. Interior wall poly and interior rim joist areas are constructed as vapour barriers but not air barriers.
Wall construction is 2×4 stagger stud on 2×8 plate. Ventilated attic and conditioned crawl space.
Whereas $10k is not insignificant, the builder was able to downsize the furnace and the operating costs of the home will be relatively low.
FYI
GBA Detail Library
A collection of one thousand construction details organized by climate and house part
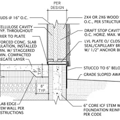
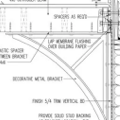
Replies
If .5ACH is the end point, what’s the starting point? Does that $10k include any above code insulation or not? Seems like $10k could have prevented a lot more emissions spent elsewhere and won’t pay back. But will provide somewhat higher comfort levels, but that’s pretty subjective.
Paul,
Many jurisdictions across British Columbia, where plumb_bob and I live, are now mandating blower door tests. Until now code compliant houses seemed pretty tight, based on visual inspection of the interior poly, but no one really knew what that meant. It will be interesting to see what these "regular" houses test out at now they will be tested.
Let me offer another data point:
I did the AeroBarrier process on my house. It got the ACH50 from over 4 to 1.4. It cost $3500. I consider it money well spent.
You really need to know what the starting point was to be able to do anykind of meaningful analysis or comparison here. If it cost $10k to go from 1234ACH50 (maybe they neglected to to put in drywall or sheathing, so air could go right throuh the wall) down to 0.5, maybe that was a good investment. If you only went from 0.6ACH50 down to 0.5ACH50 for that $10k, then you didn't get nearly as much for your money. Without knowing the starting point, you really can't draw any conclusions here as to the economics of the problem.
There certainly is something to gain by increasing air tightness of a home, but you get into diminishing returns as you strive for smaller and smaller numbers in front of the "ACH50" part. It would be interesting to see a graph of cost vs xACH50, to be able to figure out where the "sweet spot" is, but I've never seen any data to show anything like that. Usually people are either aiming for some specified target to meet a particular standard (building code minimum, Passivhaus, etc.), or they are just trying for as good as they can get without going too crazy.
Bill
Not only is there diminishing returns financially, there are also diminishing returns in performance. Going from 10 ACH to 5 is huge. Going from 5 to 2.5 is significant. Going from 2.5 to 1.25 might not matter and going from 1.25 to 0.625 probably won't be noticed.
It depends on how performance is quantified. It'd be interesting to see how indoor air quality differs in a 2 month period of constant wildfire smoke for 2.5 to 1.25 ACH50
I think the (unstated) starting point is probably what you'd expect the average new home to be, as built by production builders, on their 25th build of the same floor plan, in typical working/weather conditions. Probably something like 6 +/- 2 ACH50?
I believe our code "assumes" a standard house build will have an air tightness of 3.5ACH50. However, this would largely be based on houses in the major population centers (South coast) where weather is much warmer that up North where I am. Local climate (periods of -40c in the winter) dictates that drafts are unacceptable, so the baseline for air tightness would be higher in the North.
Also, because we have a small market, builders or trades with a poor reputation do not last and the general quality of construction is quite good.
Having watched this evolution over the last several years I can confidently say that buildings are getting tighter, but have no opinion as to if the money spent is "worth" it.
Where you all are at, what would be the premium on a build with better than average energy efficiency?
One note: because the majority of the $10k is in labour costs, it is quite achievable for DIY builders. I am in the process of adding an addition to my house and have done a fastidious job of air sealing and agree that material costs are minimal.
"Where you all are at, what would be the premium on a build with better than average energy efficiency?"
The cost divided by the discounted kwh saved should be equal to the electricity rate (or fossil rate) regardless of location. So for me, to justify $10k I'd need to save 10,000 kwh/year for ten years at a 5% rate to equal my $.13/kwh, or 5,000 kwh/year for 30. I only use about 10,000 kwh/year so it's not happening.
I'd assume zero resale value for efficiency increases, but maybe that'll change. If so, the math gets a little better.
You also get an increase in comfort, which is harder to assign a dollar figure too. Admittedly, as you start getting into smaller and smaller ACH50 numbers, the difference in comfort probably won't be noticed.
Bill
Remember that once you get past the level of heat that keeps your pipes from freezing the only purpose of HVAC is comfort.
Im more asking: if you approached a production builder with a plan, and then approached a "progressive" builder using advanced techniques and systems with the same plan, what would the price difference be?
That's going to vary so wildly, and I'd be afraid to even put a range on it. Maybe at most $30k (USD)? I'm not sure who would even be more expensive.
Learning how to get from 7+ ACH50 to 3 ACH50 is a big learning curve; many "standard procedures" need to be changed, and it can be expensive. Once you know how to get to 3 ACH50, getting to 1 ACH50 is mostly about paying closer attention to the fine details. Once you can reliably reach 1 ACH50, it can be fun to see just how low you can go; 0.6 (Passive House) is the next milestone but builders on my projects have made it down to 0.1 ACH50. The energy savings at 0.1 ACH50 compared to 1.0 ACH50 are a few dollars a year; there will rarely be a reasonable payback or ROI to go that low, but going from 7 to 3 to 1 ACH50 shouldn't cost $10K extra, at least not after the first one.
Perhaps data for this discussion - I spent $350 on Fentrim and about $1k on 3M 8067 to tape the seams on my sheathing and the sheathing to the foundation for a 3400 sq ft two story.
Won't know for a while where we landed yet though to know the benefit of that work. Not sure where I'd spend another $8500...
Jason_K,
But what alternatives are you measuring that expense against? All the building codes I'm familiar with require the installation of a continuous air-barrier, so the additional cost of a particular approach has to be deducted from some cheaper baseline.
Malcolm, codes may require it, but that doesn't mean it's actually enforced.
Where I'm at, they're still on 2009 IECC (R13 wall, R38 ceiling for my CZ). So that expense is additional cost that wouldn't have been spent - I had to push our builder (and their framer), and do a lot of the taping myself. It would have just been a leaky shell otherwise.
There would have been a WRB with taped seams, but that needs to be there regardless IMO.
Jason_K,
That leaves me shaking my head. For the last three decades the air-barrier up here has been interior poly, taped and sealed. So the incremental expense of doing a good job is pretty small - and the baseline installation to get your insulation and air-barrier inspection still yields a pretty tight house.
I see your point. The alternative for you was basically no distinct air-barrier at all.
Where did you end up? I’m in the same situation as you where most builders don’t even know what a blower door test is and everyone laughs at me when I’m slinging tape and sealant.
My target with tape, sealant and common sense is ACH below 2.5
Malcolm, with all the forensic testing of buildings happening now, are you supposed to use poly or would one of those special Membrane barriers be allowed?
rockies63,
Our code calls for a vapour-barrier (which up here is defined a bit differently, as any material under 1 perm), and that's still usually poly, but nothing precludes using a variable-perm membrane, or foam either. Up to now poly hasn't caused much of a problem in our varied climates, but I guess that's a different question that whether it's the best choice.
We know the disadvantages (precludes drying to the inside, can trap moisture in cooling conditions), but there are advantages too. It's a distinct, visible air-barrier that is easy to inspect and test. It's also something insulators have done for decades here, so all the details are understood by them and the rest of the trades.
I expect there is probably an "80/20 rule" situation here, where some smaller percentage of the effort and expense is responsible for a larger part of the savings. Systematic, scientific research on this would be very valuable. Maybe that work's been done. I wouldn't know where to find it though. That's the sort of thing that industry organizations often sponsor. If only I was the president of the NAHB!
Very interesting comment, by the way. Thanks for sharing the information.
Efficient buildings aren't built, they're designed.
What I mean is that efficiency is something that has to be designed in. And I would argue that an efficient design isn't at all inherently more expensive than an inefficient one.
https://www.jlconline.com/how-to/insulation/practical-air-sealing_o seems to have information regarding expense and resultant improvement in air sealing. I haven't been able to finish reading this yet with the paywall that doesn't want to let me register and pay to read.