Crawl Space Water Hazard

I’m conditioning my zone 5 crawl space as part of a gut remodel. I just finished insulating the rim joist and top of the block wall with EPS that extends 2 inches beyond the wall. My plan was to install two inches of laminated EPS to the wall and foam a 1/2 inch gap between wall and wall cap insulation. The floor vapor barrier would be taped to the wall insulation. A perfect air seal is not an issue because there is 2 inches of external EPS covering the block wall. The existing wall shows evidence of rising damp on the lower block but the upper is dry and clear. It came to mind that water must be evaporating before it reaches the upper block. I fear that if I seal the wall water will reach the top and rot the rim joist and floor joist ends. They do not rest on a wall plate and there is no capillary break.
My revised plan is to seal my floor vapor barrier to the lower block with acoustic caulk held on with a 1 x 2 pressure treated batten. The external insulation will prevent condensation, but with 2/3 of the wall exposed the damp can dry to the inside. The floor will have 1 inch of EPS under the vapor barrier. The crawl space will be serviced by the central heating and AC system and have generous passive venting between the living and crawl space. I don’t anticipate a humidity problem unless there is overwhelming evaporation from the block.
Am I right to worry and if so, is my plan sound?
Douglas Higden
GBA Detail Library
A collection of one thousand construction details organized by climate and house part
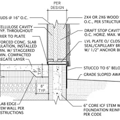
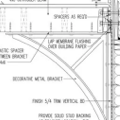
Replies
Douglas,
You should first check for airtightness. Do a blower door test if possible. Your "cut and cobble" EPS insulation in the rim joist area does nothing to seal against air leakage. The rim joist area tends to have very high air leakage and air leakage is your biggest issue when weatherizing after bulk water penetration. Depending on the exterior details, you might want to add a layer of foil-faced polyiso foam to the EPS and seal around the edges with canned foam.
For the floor, your plan will work but you might benefit from a bit more insulation. In zone 5, "pretty good" is about R10-R15 under the slab and about the same or a bit more on the walls. Your plan is about R4 under the vapor barrier and R8 on the walls. Certainly better than nothing. If you can go to 2" under the vapor barrier it will probably pay for itself. Sealing the VB to the wall with acoustic sealant and furring strips will work fine. You could probably afford to apply 2" of the same EPS as you used in the rim joist to the wall as well. This will reduce drying a bit, but probably not too much. 2" low-density EPS is very vapor permeable.
With active conditioning, the crawl should be pretty dry and you should still get drying to the interior in most weather conditions. With 2" of insulation on inside and outside, the wall is in the middle of the thermal envelope and should generally run about halfway between interior and exterior temperatures. That will keep the temperature above the interior dewpoint 99% of the time.
"You could probably afford to apply 2" of the same EPS as you used in the rim joist to the wall as well. This will reduce drying a bit, but probably not too much. 2" low-density EPS is very vapor permeable."
This was my plan until I considered the issue of rising damp. From my research 2 inches of Type I EPS has a perm rating of 2 to 5. I fear that this is too low to insure that the wall will dry.
Otherwise air leakage should not be an issue. I went to great lengths to insure that the house is airtight at the sheathing level and made sure that the sheathing is well sealed to the foundation. With 2" continuous external insulation from below grade to top plate, condensation is not a factor.
In spite of removing about 4 yards of soil from the crawl space floor, head room is still an issue. I'm not willing to lose another inch to insulation. The primary purpose of the floor insulation is to keep the floor above the dew point in summer. With a ΔT of 20 I'm not too worried about winter heat loss.
Are you sure some kind of drain tile and sump pump set up is not in order with that much water going up the wall? Seems like that could be beneficial.
That's a good point. If you haven't already, pay attention to exterior grading and drainage. Get all of your roof water away from the house. If you have a naturally high water table, a French drain might help to drain away bulk water from alongside the footings (no lower). Still, the masonry will wick some moisture up from the ground. As I said above, adding another 2" of EPS to the interior of the walls would probably be safe from a moisture standpoint.
Do remember also that in most jurisdictions, the EPS on the floor and walls must be covered with a fire (ignition or thermal) barrier.
Lstiburek (2015) on the importance of inward drying:
https://www.buildingscience.com/documents/information-sheets/crawlspace-insulation
Tom Wheeler wrote. "Are you sure some kind of drain tile and sump pump set up is not in order with that much water going up the wall? Seems like that could be beneficial."
In the process of my reno I dug a interior perimeter drain and sump system that extends a foot below the floor. When dug last winter, the crawl space was dry to the bottom of the drain trench. Now with spring rains the water table has risen to grade as it often does with our clay soil. In spite of the drain, in some areas the floor is damp as far as ten feet in from the walls. No amount of drainage is going to prevent water from rising up the masonry.
Peter Engle wrote, "Do remember also that in most jurisdictions, the EPS on the floor and walls must be covered with a fire (ignition or thermal) barrier."
Thanks, I had misinterpreted the code. I will cover the existing foam or replace it with Rockwool. This however, throws a monkey wrench into my floor insulation plan. Any ideas for a floor ignition barrier?
Thanks for the link to BSC Jon. Lstiburek says that my EPS has an adequate perm rating but later stresses the need for a capillary break. This is impractical to provide at this point.