Damp Cellulose in Wall Cavities

We are in the middle of a deep energy retrofit, and Wednesday before last we had a massive storm roll through. I had a section of west-facing wall that was stripped to the board sheathing that was pummeled by horizontal rain. The wall cavity is filled existing cellulose insulation, probably from the 70’s. When poking a finger into one of the installation holes or gaps between boards, it still feels damp to the touch.
We are wrapping the walls in a self-adhered vapor-permeable air barrier (Grace Vycor En-VS), followed by foil-faced polyiso foam. The interior walls are 100-year-old lath-and-plaster, with an unknown number of coats of paint. My question is:
1) Should we remove the old cellulose and blow in new before wrapping the sheathing, or
2) Go ahead and install the vapor-permeable peel-and-stick housewrap to prevent further water intrusion, but wait for a period to allow for drying, or
3) Is it safe to move forward with the housewrap and foam installation?
We are in Climate Zone 4, and having an unseasonably warm winter (temperature is 60F today). I appreciate any advice seasoned hands can offer.
-Nathan
GBA Detail Library
A collection of one thousand construction details organized by climate and house part
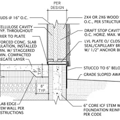
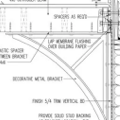
Replies
If believe the moisture that got in was from the rain, and not from vapor drive, the first thing I would do is find out how it got in. I'd start by checking all flashing details, and roof/soffit areas, looking for leaks. You don't want anything to get in after you complete your deep energy retrofit. The big downside of sealing things up for energy efficiency is that you greatly reduce the ability for moisture to get OUT of anything, which is why you want to make sure moisture can't get IN in the first place. This is very important before you move forward with your project.
Note that foil faced polyiso will negate the vapor permeance of the air barrier you're using. The foil facer is a vapor BARRIER, and if you layer a vapor barrier over anything (vapor retarder or even something completely vapor open), you end up getting the properties of the vapor barrier dominating the assembly. All this means is that your air barrier is now just an air seal that acts as a vapor barrier, no different from a sheet of polyethylene. The foil faced polyiso will block any mositure trying to escape through that permeable air barrier layer.
What you do after you seal up any leaks depends on how wet that cellulose is. If it's just a tiny bit of moisture, I'd give it a chance to dry and see if things improve. If it dries out in a reasonable amount of time (which will be at least a few days), then you're probably OK to leave it in as long as it hasn't done any unusual settling. If it doesn't want to dry out (high humidity levels, rainy weather, etc.), or you just can't wait, then it's better to pull out the old stuff and put in new.
I'll stress one more time that you absolutely want to find out how it got wet in the first place and fix that before moving forward with your project though. As soon as you close things up with the new materials, any future moisture problems are going to be much more serious.
Bill
Bill, thanks for your reply. I know how it got wet - we had the siding off, so only the board sheathing was exposed, and had a record storm (85 mph winds driving rain horizontally) that pushed water into the gaps between the board sheathing. The insulation was dry before the storm, and we are adding flashing details as part of the build-out of the wall.
The cellulose is damp but not so much you can squeeze moisture out of it. I think I will go ahead and wrap the walls with the peel-and-stick to avoid further intrusion, but leave that exposed (i.e. no foam) for a week or two for further drying.
I had a very similar occurrence. Rain pouring through old gapped board sheathing before the WRB was fully installed. But we were still down to studs w/o any insulation or interior walls.
The spec for the Vycor En-VS looks to be 15 perm and 90 day exposure allowed.
I share Zephyr's concerns re: the polyiso acting as a vapor barrier. For my reno, I assumed water will someday find its way into the exterior walls. We allowed for a drying path to the exterior.