Do I need to put rigid foam on a crawlspace dirt floor?

I live an old 1890s brace/balloon frame in Virginia (Climate Zone 4). Do I need to put rigid foam on the dirt floor? My contractor is adamant that I need to either insulate the dirt floor or the ceiling above to be compliant with IECC. I was under the impression that I could put a vapor barrier on the floor and insulate the walls with rigid foam. Is there a best practice? And if both are acceptable, how much of a difference does the rigid foam make to the comfort/cost savings? Thanks for any input!
Chris
GBA Detail Library
A collection of one thousand construction details organized by climate and house part
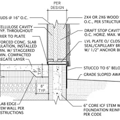
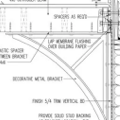
Replies
What type of foundation do you have? How dry is the crawlspace?
It sounds like you are considering creating an unvented crawlspace. Is that your objective?
What type of foundation do you have? Old poured concrete with parging
How dry is the crawlspace? Surprisingly dry given that it is below grade
It sounds like you are considering creating an unvented crawlspace. Is that your objective? Yes
Chris,
If you haven't done so already, you should read this article: https://www.greenbuildingadvisor.com/blogs/dept/musings/building-unvented-crawl-space. Also check out the articles in the sidebar.
I also would start looking for a new contractor.
My understanding is that if the basement walls are insulated (to R10 continuous insulation in zone 4) there is no need to insulate the basement ceiling.
There is never a requirement to insulate a basement slab. Even slab-on-grade foundations only need to be insulated at the edges, not under the slab, and only down to some depth below grade. (For zone 4 that would R10, 2' below grade or down to the footing, whichever is deeper.). See TABLE N1102.1.1
http://codes.iccsafe.org/app/book/content/2015-I-Codes/2015%20IRC%20HTML/Chapter%2011.html
That's not to say that an inch of EPS under a rat-slab on isn't a good idea for zone 4. With R4 and a vapor barrier protected by a non-structural slab the slab temp would pretty much track the room temp, which would average above the summertime outdoor air's dew point temperature, thereby avoiding the "musty basement smell" (assuming you also meet code-min for the walls.) The deep subsoil temp is in the 50s F, and the summertime outdoor dew point averages are in the 60s, which means wood or paper boxes resting on the slab will take on moisture from the room air &/or grow mold unless you mechanically dehumidify the basement air to something well below the slab temperature. That would be quite a bit more mechanical dehumidification for an uninsulated slab than with an insulated slab.
But it's not a code requirement under the IRC (though local codes sometimes vary on all sorts of particulars.)
Steve,
I've read all the articles pertaining to encapsulation. This article is what got my attention though the climate zone is different. https://www.greenbuildingadvisor.com/community/forum/energy-efficiency-and-durability/99602/closed-cell-spray-foam-wall-and-dirt-floor-cr
My contractor wants me to install 2" Dow Blue Board that is taped and sealed to also act as the vapor barrier. He is the GC for the whole job but I said I would handle the insulation since the floors were pulled up. I can overrule him on it, but if he is right I will gladly spend the extra money if it will make that much of a difference.
I will also add that the crawlspace is less that 2' high. I wouldn't be interested in a rat slab since I have duct, plumbing and electrical in the floor still.
Thanks
Chris,
I don't think there is any need to use rigid foam as an air barrier when 20 millimeter poly would be easier to install and seal. In any case, new XPS is not a good choice for environmental reasons.
Two inches of XPS (whether blue, pink, or green, don't really care) is somewhat overkill for an unheated basement slab in a zone 4 climate. Even 1.5" of XPS (or 2" of EPS) would be sufficient to hitting Net Zero Energy with a PV array that fits on the house, provided you bumped up the rest of the house to the whole-assembly performance for zone 4 listed in Table 2, p.10 of this document:
https://buildingscience.com/sites/default/files/migrate/pdf/BA-1005_High%20R-Value_Walls_Case_Study.pdf
(Note hitting those numbers would mean bumping up the basement wall insulation to a continuous R15 from the IRC's R10 code-minimum).
Steve is on the right track here. The vapor retardency of 2" of XPS is about 0.6-0.8 perms, roughly 10x that of even 6 mil polyethylene. Taped XPS is not a true vapor barrier. Using 2" of Type-II EPS (1.5lbs nominal density) with 6 mil polyethylene on top would be more water vapor, air & radon tight than 2" of XPS, and it would be cheaper and greener to boot.
Type-II EPS is a very common roofing foam insulation, and you may be able to find some used roofing EPS (or XPS) which is fine to use under a basement slab (or rat-slab), and a fraction the cost of virgin-stock XPS, and is commonly reclaimed for re-ust. Be aware that polyisocyanurate is also a commonly re-used roofing foam, but unlike polystyrene it should not be used in direct contact with the ground, since it hygroscopic and can wick ground moisture. It's fine for the interior side of foundation walls, as long as the cut edge is kept off the dirt (or slab). One or more of the reclaimers advertising used foam board in your area may have a line on used EPS or XPS, but if you have a poured concrete or block wall that's reasonably flat, you can save a ton of money using reclaimed polyiso for the walls.
https://richmond.craigslist.org/search/sss?query=rigid+insulation
If you're going to insulate the basement floor it's worth pre-installing a perimeter drain and 3-4" of clean pea gravel or crushed stone and compacting it before putting down the foam, poly sheeting, and slab or rat-slab.
If you're in a high radon zone you might consider installing the hooks for a passive radon mitigation system under the slab/poly/foam too.
http://s3.amazonaws.com/finehomebuilding.s3.tauntoncloud.com/app/uploads/2016/04/09112955/021244087-01-passive-system_xlg.jpg
http://www.vdh.virginia.gov/content/uploads/sites/7/2016/01/Virginia-Radon-Map.png
Dana,
Chris' 24 inch high crawlspace has a dirt floor, and he is not inclined to install a rat slab. That is why I thought the 20 mil poly might be the best option. I was also thinking he might (perhaps) want to air seal the rim joist and install some reclaimed foam on the concrete walls. (I wonder what is behind the parging since the house is from 1895, however.) Thought?
Steve,
The foundation walls are sort of an aggregate with some larger and small chunks of fill, but it is mixed concrete and then parged smooth and painted on the exterior. The interior is fairly smooth and shows signs of forms. As for the rim joist, I have a brace-frame walls (balloon frame and western frame combined - the studs penetrate the floor and go to the sill but unlike balloon frame I have a double top plate and studs that only go to the 2nd floor and not the floor length) so this means I have the wall insulation (roxul in my situation since I don't have sheathing) exposed to the crawlspace. I don't know if this changes how I address the air seal on the rim joist.
Thanks
Chris,
When it comes to detailing a crawl space floor in Climate Zone 4, the most important thing is to get a high-quality vapor barrier installed -- usually thick polyethylene with taped seams.
In your climate zone, the investment in a layer of rigid foam on the dirt floor won't yield enough energy savings to justify the investment. That said, if you want to install a rat slab, an inch of foam would be a nice way to lower the moisture content of the slab.
-- Martin Holladay
Martin, Steve & Dana,
Any suggestions on the open stud bays to the crawlspace? Right now I have Roxul and an air barrier. I've attached a simple diagram that show my materials. I don't have sheathing.
Thanks
Chris,
Your illustration doesn't show any stud bays in the crawl space. It does, on the other hand, show stud bays above the foundation -- stud bays that appear to be filled with Roxul mineral wool.
Do you intend to frame up 2x4 or 2x6 walls in your crawl space, on the interior side of the existing R-10 rigid foam insulation?
-- Martin Holladay
Martin,
I'm sorry the illustration doesn't effectively show the stud bays. There will not be a new 2x4 wall in the crawlspace. Here is a drawing I found that shows the balloon frame style that I have. The walls don't have a 2x4 bottom plate. They use the sill and nail into the side of the floor joists. Since it isn't that platform style will the subfloor and bottom plate the stud bay goes through the floor and into the crawlspace. I hope this makes sense.
Thanks
Chris,
I would like to hear what Dana thinks. In the meantime, this discussion from 2013 may help to address some of the details that might be helpful in dealing with an older home and framing strategies.
Sorry. It looks like I left out the link for the 2013 discussion. Here it is: https://www.greenbuildingadvisor.com/community/forum/green-building-techniques/26484/should-balloon-framed-houses-open-crawlspaces-be-sea
If the crawl space doesn't have any mechcanical systems (no ducts, air handlers, water heaters) down there, in a zone 4 location I'd be inclined to skip rigid foam on the floor, just do a good job on insulating and air sealing the foundation walls. As long as no mold-susceptible materials are resting on the uninsulated floor, the mold risk is pretty low. (Somehow I had been picturing a basement or "crouch space" used for storage, ducts, air handlers, etc. ) But even an inch of foam mitigates the risk to near-zero. Any foam on the floor would need some sort of ignition barrier, if not a rat-slab. Rat-slabs DO provide burrowing rodent ingress protection though, which is an additional value. If it's cheaper or easier, cement board laid atop the floor foam & vapor barrier should be sufficient.
The wall foam in a crawl space still needs an ignition barrier of some type though, but using fire-rated Dow Thermax polyiso for the wall foam is often allowed without any additional materials. If the wall is too uneven to use rigid foam and you go with a couple inches of 2lb spray polyurethane sprayed with intumescent paint is often allowed in lieu of thermal/ignition barriers in crawl spaces.
Roxul + air barrier is fine for the bottom of the balloon framing. I can be difficult to make the air barriers truly air tight on old not-so-clean or smooth joists though.
Hi Dana,
The crawlspace does have rigid ducts. It leaks a little bit and a portion of it is resting on the floor. It does have fiberglass insulation but the joints were never painted with mastic, etc. I was hoping that the new encapsulated crawlspace could utilize some of that heat/cooling instead of repairing the whole system.
Unfortunately, the rat-slab wouldn't be available to me. I've got about a week to procure and another week to install before plumbing and electric come into the space behind me. I will definitely tax your recommendation on the thermax for the walls.
Thanks
With ducts in the the crawl space, see if you can't dig up some used roofing EPS for the floor (any thickness) with a vapor barrier on top, with the vapor barrier mastic-sealed to the foundation behind the wall foam. If not used Type-II foam, you can probably find cheap 1" Type-I EPS at a box store (often sold with foil facer on one side), but be aware it's much more fragile/dent-able stuff to handle than the higher density Type-II.
You can deal with covering the floor foam later- or maybe spray it with intumescent paint. Make sure the foam & vapor barrier go under the portion where the duct is currently in contact with the dirt. Don't cut around it, dig down if need be.
What was the contractor recommending you cover the (not really needed to meet code) floor foam with?
How many square feet of floor?
Dana,
What was the contractor recommending you cover the (not really needed to meet code) floor foam with? nothing - we were just planning to tape the seams
How many square feet of floor? 700 sq ft
For clarification, do you mean placing the 1" EPS just under the ducts that are touching the ground (that I will dig under) or do you suggest that I cover the entire floor?
The plan then would be to do the above (whichever method), vapor barrier mastic-sealed to the foundation wall behind the wall foam which will be 2" Thermax that is mechanically fastened to the foundation.
Martin indicated that I wouldn't see a return if I did the floor foam, does this change because I have the ducts?
Thanks
Cover the whole floor with both EPS and the vapor barrier.
When available from reclaimers 2" Type-II roofing EPS is typically half the the cost of box-store or lumber-yard 1" Type-I EPS, and it's much better stuff. In my area 1" box-store EPS runs $16/sheet, and reclaimed 2" EPS runs $5-$10/sheet in truckload quantities. For 700 square feet you're looking at 22 sheets minimum, but buy 25 if it's reclaimed goods since a few sheets might be a bit too beat up . So that's about $350 in foam, maybe $100 in polyethylene, call it $450-500 all-in for material costs if you go with box-store 1" EPS, but it could be down to the $250-350 range if using reclaimed foam. Your 2" Thermax wall is going to be more than that, even if it's fewer sheets.
Between the heat loss & air leakage of the ducts and the potential for moving mold spores around, putting a modest R4 down on the floor is the "right" thing to do. Even if it has a very long "payback" in strictly financial terms, the payback is of course quicker if you get cheap reclaimed goods.
The LAST thing you would want to do is to put insulation between the joists, which would guarantee that all duct losses are truly lost.