Do screws through exterior insulation reduce the wall R-value?

I was in a Net Zero Building class this weekend and there was mention that screws that are used to attached exterior insulation reduce the whole wall R-value by 39%.
The screws are attached from the outside thru the rainscreen, insulation, WRB, sheathing and into the framing.
This individual referred to an article from Energy Design Update (no issue was noted). I’d check but $600.00 for a subscription is too rich for my pockets…..
Any help here on the article or data at least, with other references?
GBA Detail Library
A collection of one thousand construction details organized by climate and house part
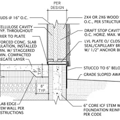
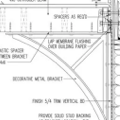
Replies
The thermal conductivity of steel is a about 200x higher than insulation, 100x that of wood, but it still takes a lot of screws to reduce the performance by fully 39%. Each square inch of screw cross section is "worth" about 200 square inches of insulation in terms of heat transfer. (rough order of magnitude.)
If you have 1/4" diameter timber screws 24" o.c. that's only (Pi x 0.125"^2 =) about 0.05 square inches of screw for every (24" x 24" =) 576 square inches of wood & insulation. The (200 x .05=) 10 square inches of "wood & insulation equivalent) that represents means the whole-wall heat transfer is increased by ( (576+10) / 576= )1.02x. That's a 2% hit in "clear wall" performance. Real walls will have more fasteners than that due to edges, windows & doors, etc, so it might be a 5% hit in whole-wall performance. With 16" o.c. screw spacing that roughly doubles, and might be as much as 10%, but it would take a heluva lot of screws to be a 39% hit in thermal performance.
Anybody making that 39% assertion needs to show their math, and the underlying assumptions about fastener spacing.
For a relative thermal conductivity reference:
http://www.engineeringtoolbox.com/thermal-conductivity-d_429.html
Dana,
As always - Thanks. I assumed there was some conductivity, but not that much. Looking for someone who can refer the actual article, that hopefully cites references too.
Dana – my math doesn’t match yours! I once looked into the thermomass foundation walls and was very surprised to calculate that the conductivity of the steel form ties was painfully high. Additionally, some people complained on-line that they got cold spots at these points – validating my concern. If I ever did that wall, I’d go for fiberglass ties (I assume they exist, but don’t really know).
This always made me worry about the fasteners in walls with external foam.
From the engineering toolbox reference cited in comment #1, I see the conductivity of 1% carbon steel at 43 W/mK. It’s less for stainless steel at 16 W/mK. The same chart lists XPS at 0.03 W/mK (R5 per inch is 0.029, but let’s stick with the 0.03 number). Conductivity ratios are therefore 1400 to 1 for the carbon steel and 530 to one for the stainless fasteners. At 1400 to 1, your calculated values must increase seven fold.
Did I miss something in engineering toolbox the table? The 200 to one “order of magnitude estimate” of relative conductivities is indeed within an order of magnitude, but we need better precision than plus or minus a factor ten! Otherwise the 2% - 5% number you calculate becomes as large as 20% - 50%, something we cannot ignore.
Assuming the above values are correct, using 1/4” diameter carbon-steel fasteners at 24” o.c., I calculate 12.3% more heat flowing through Brad’s exterior insulation (using the all-foam no-fastener wall as the basis). At 16” o.c., this rises to 27.5%. What about 12” o.c.? Then you lose half the insulation value of the foam! In addition, the extra length of steel through the furring strips and into the load bearing wall, and the fact that the screws have a much wider head, all make the situation slightly worse.
However a 1/4” diameter fastener seems beefy. The Headlok fasteners (carbon steel) have a 3/16” shank diameter so we can divide all of the above percentages by 1.8: 24” o.c. now has only a 7% hit and the 16” o.c. has a 15.5% hit. Using stainless steel fasteners? Then heat flow through the fasteners is an additional three times less.
My conclusion? Pay attention to the fasteners. Thoughts?
Bill,
Yes, ThermoMass recommends a fiberglass tie to reduce thermal bridging. Here is the ORNL study..
https://www.google.com/url?q=http://www.thermomass.com/files/thermomass_ornl_doe_thermal_performance_kosny.pdf&sa=U&ei=Nr7zVMfXJsuwggSNtYSgAQ&ved=0CAcQFjAB&client=internal-uds-cse&usg=AFQjCNGLkJqyo5f6xM5tpwUmKNVJp1cU8Q
Thanks Brad.
The data point to pull from that ORNL study is that, relative to fiber composite connector (16" o.c.), 6 ga. mild steel connectors (12 " o.c., 0.194" thick, don't know how wide) reduced the R value of the 2" XPS insulation by 28%. This can be (sorta) applied to a wall built with exterior foam board insulation with steel screws. One must scale for the cross section of the steel penetrations (unknown) and their spacing.
Equivalent metal penetrations at 24" o.c. would yield a R-value reduction of 7%; 16" o.c.? then R value decreases 12% relative to a no fastener foam layer. Of course Headlok fasteners probably have a smaller cross section than the form ties by at least a factor of two. (just guessing - I'm no building professional). So perhaps I'm being slightly alarmist?
I still say - pay attention to the fasteners.
I've been looking at the Thermomass wall and I believe that they make reference to the weakness of rebar connectors between the wythes and play up their proprietary carbon fiber fastening system, so there's no reason to shy away from Thermomass due to rebar connectors. The drawback, to my limited understanding, is that they don't sell their fasteners as stand-alone devices, meaning that you have to buy the XPS predrilled with fasteners attached and then have they whole enchilada shipped to your building site.
If you have helper monkeys who can drill locally purchased XPS and then attach the fasteners, that's likely a big cost savings. Luckily other companies sell only the fasteners.
As to the thermal bridging of the fasteners mentioned in the OP, I believe Dana omitted the contribution that between studs insulation contributes to whole wall metrics. To get to the whole wall metric, you need to take sections of the wall and the fastener performance is restricted to the wall only in the 1/4" section where they are fastened into the studs. Depending on the method of framing used, used, then 24" OC or 16" OC studs means that the entire wall between the studs in not compromised, in an ideal state, from drywall to exterior sheathing.
It's been a long time since I studied thermodynamics, so it's beyond my ability to respond intelligently on this point - how is heat transfer through the wall at the midpoint of the16"/ 24" OC framing affected by the greater thermal conductivity of the fasteners 8"/12" away? For the heat at the center to migrate to the area of the fastener it still has to traverse through insulation and that insulation is uniformly applied, so I'm uncertain if the heat will funnel towards the fastener instead of just progressing from hot to cold and moving outwards. If there is no funneling effect towards the fastener, then the only heat loss which should occur is in that small, compromised, part of the wall and the rest of the wall performance should be unimpeded.
I can't see the 39% figure as accurately representing the real world physics of the situation.
Brad,
This question has been discussed on GBA several times. When building scientist John Straube was asked to respond to a report that fasteners through rigid foam could reduce the thermal performance of the rigid foam by 45%, here's how he responded: "The effect [that fasteners have on the thermal performance of rigid foam sheathing] is on the order of 1 to 2 percent. Variations of this have been modeled repeatedly. 45 per cent [reduction in thermal effectiveness is] technically preposterous."
If you like to read long Q&A threads, here is a link to one of the discussions about this issue: AECB website and point thermal bridges.
Martin,
Thank you again!
Martin,
That was a looong Q&A thread, and It seems that some in the conversation were determined to believe that screws/nails do pose a R-value reduction. I believe you and Straube. Any chance you can get your hands on the article that the Energy Design Update reported on the R-value reduction?
I'm inclined in my PERSIST house construction to capture data at the stud and screw interface and at the face of the stud adjacent to the screw tip......just to provide hard data. Unless someone can cite an actual real world study that was done.....
I may be moving myself into crank territory, but here goes anyway...
In this article from the 9th Annual North American Passive House Conference, September 12-13, 2014):
http://rdh.com/wp-content/uploads/2014/10/NAPHC-2014-Thermal-Bridging-Through-Exterior-Insulation-Higgins-Shane-Finch.pdf
The authors perform three dimensional thermal modelling (rats not real data) on walls with external mineral wool insulation. The levels of external insulation were Passive House level with 4”, 8” and 12” of exterior insulation. Among the various systems for attaching this to a stud wall, they modeled stainless steel and galvanized screws through wood or metal strapping. These were 16” o.c. horizontally and either 16” or 12” o.c. vertically. The results quoted below have the screws going into 2 x 6 Wood Framing. I couldn’t find a diameter for the screws in the paper – perhaps I missed it.
The result is in the attached figure: the results are all in % degradation of the exterior insulation.
Summarizing:
Galvanized screws 16” o.c. horiz. & 16” o.c. vert.: 9 to 13% degradation
Galvanized screws 16” o.c. horiz. & 12” o.c. vert.: 12 to17% degradation
S.S screws 16” o.c. horiz. & 16” o.c. vert.: 3 to 4% degradation
S.S. screws 16” o.c. horiz. & 12” o.c. vert.: 4 to 6% degradation
Martin, any web reference to the modelling referenced by John Straube? I’d love to read that.
Brad,
I've used several methods to search back issues of Energy Design Update, and I can't find any articles on this topic. To the best of my recollection, no such article was published in EDU during the 7 years when I was editor.
Bill,
Thanks for sharing the data from the modeling study.
Here's my "pretty good house" summary: John Straube refers to a 1% to 2% degradation in thermal performance. Higgins, Shane, and Finch refer to a 3% to 17% degradation in thermal performance. The difference may have to do with whether we are talking about the degradation in thermal performance of the exterior insulation layer or the degradation in thermal performance of the entire wall assembly -- or it may have to do with other factors.
The bottom line is, we need to have these screws for structural reasons. Let's make a ballpark guess and conclude that the screws result in a degradation in thermal performance of about 10%. (This is "pretty good house" math.) If this really bothers you, make your rigid foam 10% thicker.
(And yes, I know that you can't buy rigid foam that is 2.2 inches thick. Here's my point: How much does it matter if your wall assembly is an R-40 wall an R-36 wall? If this really matters to you, then design an R-44 wall.)
This may be the report referenced by John Straube:
http://apps1.eere.energy.gov/buildings/publications/pdfs/building_america/fasteners_wood_walls.pdf
That answer (thinner insulation, but higher R-value, more fasteners, each with smaller diameter) is about 4.5% whole-wall degradation of R-value. This paper models ALL the fasteners in the wall - drywall side as well.
Another good read!
Another conclusion from this discussion; Fasteners used without foam to attach siding and strapping and sheathing and drywall, All are changing the insulation values of the framing of a building. More fasteners is good for high wind areas and tornadoes, less fasteners and SS fasteners are good for R values, especially the unknown ones that none of us calculate when bragging about our super insulated domiciles...
great topic
aj
Bill- thanks for digging up more accurate & nuanced models (and mea-culpa for the order of magnitude error!).
Even if fat fasteners at some tight spacing degraded the exterior insulation by as much as 39%, that does not degrade the whole-wall R by anywhere near that amount. The fasteners do not penetrate the entire assembly- they are anchored in wood at one end, and covered by siding at the other. Furthermore, the fasteners are not uniform in diameter- they have heads of far larger diameter than shafts, and they also have tapered points. The modeling does not work in 2-D, due to this non-uniformity, which is why the NREL modeling is far better than any armchair-engineer's napkin math model. Check out the isotherms and color-rendered heat flux density in figure 4 p. 9 in that document:
http://apps1.eere.energy.gov/buildings/publications/pdfs/building_america/fasteners_wood_walls.pdf
Hello,
I am new here, but am a MASc Student in Building Science. I have completed some initial models in HEAT3 to simulate the effects of metal fasteners penetrating exterior insulation (no insulation placed in the stud space). The nominal R-value of the wall is R-36 with all insulation placed on the outside. Using a 5mmØ stainless screw at 16" c/c horizontally and 12" c/c vertically reduces this R-36 wall to an effective value of roughly R32.(no air films ) Density of screw placement, material properties of construction material, as well as arrangement of materials , all effect the overall R-value. I think its important to look at the details of the wall assembly your considering and not take values from other setups. How much energy is lost through these screws over one year though? Tough to say if it is going to push your house over the passive house limits or not.
Zombie thread..........
I blame this tempest in a teapot on computers, for two reasons. First, people enter numbers into computers and get an answer, and assume it is correct. Obviously they never had an early windows computer, where the calculator would occasionally give wrong answers. Second they never did hand calculations and had the stuff burned into their brains,
Like when calculating an assembly R value, one includes the air film
adding in the value of the air film changes the btus lost by the roughly .02 sq ft of screws per 100 square feet of assembly from an apparent .6 per degree, or an apparent 24 percent of an R40 assembly, to .019 or around .8 percent[ nominal R40 assembly is 2.5 btu per 100 square feet per degree].
That does not factor in that screws are not little perforations into the interior as a computer might consider them, but are actually screwed into an insulator, further reducing their impact.
Remember always that the first 'R' is the most important
R values lower than one give irrational answers in home insulating equations, and so whether the air film is a real function or a fudge, it works. It means little in a well insulated assembly it means a lot on poor insulators.
I would hate to see some of the posters calculate the heat loss on an uninsulated steel building. I don't think they make furnaces that large...................
edit
used a value of 30 btu/square ft for thermal conductance of steel, 56 .187 fasteners per 100 square feet