Does a heated slab need insulation under the slab?

I live in Alaska and I am building a heated slab foundation, The lot I am building on is a good gravel base after removing the top 1 to 2 feet of top soil. I am being told two different stories by two different contractors. One says I need 1″ to 2 ” of insulation under the slab and the second says the good gravel base is better and will keep things warmer once it reaches temperature. I visited a shop today with a heated slab and no insulation except on the perimeter and it was warm and was heated with a hot water heater. I want to do it right but don’t want to waste money.
Confused.
GBA Detail Library
A collection of one thousand construction details organized by climate and house part
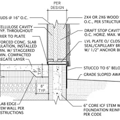
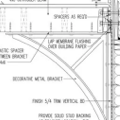
Replies
William,
They're both wrong, because in Alaska you need a lot more than 1" or 2" of insulation. The heated slab at the shop you visited was warm because of the heating, not because it wasn't losing heat into the earth. Did you ask what it cost to keep that slab warm?
There's been some debate lately about how much is enough. Basically if you can afford it, don't skimp. The best way to analyze the heat loss into the ground is with Passive House Planning Package software (PHPP). You'd need to hire a PH consultant for this. There are also sources for salvage foam board removed from commercial buildings, which would mitigate both the high cost of foam and the environmental impacts of this material.
William,
1. I agree with Thomas: the fact that the slab was warm tells you nothing about the energy required to heat the building. (In fact, the more hours a day that the slab feels warm to the touch, the worse the insulation level, and the higher the heating bills.)
2. In Alaska, the gravel under your building will always be colder than your indoor temperature, so your slab will be losing heat to the ground and therefore needs to be insulated.
3. Heated slabs need more, not less, insulation than unheated slabs.
4. In Alaska, I wouldn't install less than 6 inches of rigid foam under a heated slab. And you need vertical insulation at the slab perimeter as well.
I agree that insulation is imperative to a properly installed snowmelt system. Also, a slab sensor such as a Tekmar 090/091 is necessary for efficient operation.
The ground under the slab will freeze, the objective is to heat the slab above freezing temperatures and minimize downward and edge heat loss. Most Engineers will design a system at 150 btu's per square foot, with proper insulation, this number can realistically be reduced to around 100 btu's per foot. A typical water heater is 35,000 btu's input, hardly enough to heat a slab of any size, add the efficiency factor of a typical water heater at 70%, this makes the design highly inefficient. A condensing boiler with proper snow melting controls is the preferred method.
David,
Who said anything about a snow-melt system? I assumed this was a residential slab foundation.
And an ordinary residential water heater is perfectly adequate for heating a well insulated home. Not particularly efficient, mind you -- but it should have plenty of capacity for the job if you make an airtight building with good windows and thick insulation.
Martin,
Sorry, I guess i interpreted the question wrong.
I do agree that the passive haus approach is the optimal path to reduce the amount of energy required to heat the home.
I stand by my opinion that a water heater is not a realistic solution to provide that energy. Water heaters and boilers are constructed under entirely different regulations. I have seen many water heaters installed for space heating with poor results, mostly because the delivery water temperature falls within the condensing temperatures and water heaters and flue pipe are not equipped to handle the acidic fluid.
Thanks for correcting me, I enjoy reading your posts
please feel free to contact me [email protected]
I would keep this guy as far away from your project as possible. He either has no clue, or he's a low-price git-er-done type, I don't see a third option. The other guy doesn't sound fully informed either.
I think he's talking about the thermal mass of the gravel/soil under the slab, but I wouldn't want that for a heating system. You could get some r-value from the soil, but it would take such a large mass that it would take hours to change the temperature significantly. The heating system will be easier to control if it's a small thermal mass on top of foam.
David
I am lost by your comment "the delivery water temperature falls within the condensing temperatures and water heaters and flue pipe are not equipped to handle the acidic fluid. "
The flue temp is going to be the same whether it is domestic HW or used to heat a slab. I agree the efficiency of a boiler and WH are different.
To the OP
You have to remember hot goes to cold. I know everyone talks of heat rising. Heat will go in any direction. Hot air is buoyant so hot air rises but that is different than saying heat rises. So any heat poured into the slab is going to a colder area. It will heat the area above which is what you want and it will heat the area below, that is what you don't want. We put insulation in the sides and top of our building and now we are learning the value of putting it under.
Since you are making the floor the heat transfer mechanism it will be hotter than any other surface and it will be a larger surface. If you want to keep it in the building then you need to restrict the movement of heat to the ground below. The more insulation. the better.
GBA is a good place to learn about energy efficiency. Builders compete on price and it look nice when his bid is cheaper. It is up to you to give the builder the specs you want and are will to pay for. You pick the counters, cabinets, flooring etc. Pick the insulation. If the builder has never done it that way you may get some resistence. I think it is at that point that you better learn how it should be done and look over his shoulder. Figure out the specs and come back and ask.
One last thing. Be sure the builder pours the concrete on top of sheets of poly.
Robert, I would differ with your very last comment. I would place the VB on the gravel, put the foam on top of that, and then pour. I think this will keep the insulation slightly drier. Whether it matters.... any other opinions?
with a closed cell foam you are not worried about that. If you put the poly on the gravel you will get lots of little punctures which will let air and water through. Place the poly on the smooth surface of foam it will have few if any punctures. plus the concrete will be adhered to making a few punctures a non issue.
Robert, I have been using a product called Stego Wrap, which is IIRC a 15-mil material. It can take a lot of traffic when placed over gravel and get no punctures at all. It costs a lot more than typical poly sheeting and there is tape and mastic available with it.
David,
is a layer of sand over the gravel an option you'd consider -- to "protect" the poly?
No, I think sand starts to defeat the purpose of the gravel, part of which is to provide a capillary break. The Stego Wrap goes down on the gravel, then we walk around taping it together and dealing with pipe penetrations and other stuff that needs sealing. It handles this traffic with no problem whatsoever. Then we lay the XPS on it and start tying rebar. Then tubing, then concrete.
I think the key is not to use poly.
(duplicate)
Will Carver: WHERE in Alaska? Juneau, or Barrow? That will make a difference in your foam thickness. In Fairbanks, I have determined that 8" is a minimum, and will have 10-12". Yes, it is spendy, but build a spread sheet and look at the cost vs payback time. If you give me some data, I can run it through my SS in minutes; free! Just be warned: I don't have PHPP software, but will show you the assumptions I used to build my SS, and think they are reasonable. You be the judge of the worth of the output. Email me at jolinak at gci dot net. I am not a pro, so do your own homework and we'll compare notes. john
I live in Sterling Alaska on the Kenai Penninsula.
David
What I have seen is to place poly over the foam. Some foams are vapor permeable. If there are any tears it would allow water to move between the foam and the poly. The moisture could then make its way through. It would be a small amount and may not matter. The bigger problem would be water going through a seam and then through a crack or maybe between the rigid and the slab.
When a slab is poured on the poly, punctures and failed seams do not matter. If the poly is 2% damage you still have 98% protection.