Calculator for Double-Checking Heating and Cooling Loads

I’m looking for a double check on load calculations for a 1911 home.
Is there a good pay per use calculator available that does not require extensive floor plan inputting?
* Oakland California – Winter lows in the low to mid 40F range.
* 1000 square feet downstairs (9 foot ceilings), 500 upstairs (8 foot ceilings). Crawl space and 1/4 basement below.
* 6-8 inch blown in cellulose in attics
* 50% double pane window inserts, 25% double hung single pane painted shut, 25% double hung operable from 1911.
* No wall insulation
* Lathe and plaster construction.
* Floor insulation in the plan
* Initial CFM50 3083, after some air sealing work CFM50 2370.
* No prior energy usage data is available.
The HVAC contractor so far says:
60k HSPF 9.0 t American Standard TEM6B0C60H51SA Air Handler. Heat Pump Tons 5 SEER 16.25 two stage American Standard 4A6H7060A1000D.
Update: it’s a major local contractor, in business for 100 years, union shop.
GBA Detail Library
A collection of one thousand construction details organized by climate and house part
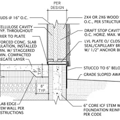
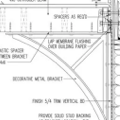
Replies
5 tons for heating in Oakland is absolutely absurd and embarrassing for a contractor to quote a customer.
Pretend it’s a one big 25x 40 x 9 box. If the lid of the box is 1000sqft with an r value of R-18, the heat loss is 1000x (65-40 (design temp)/18). That’s only 1400btus. The sides of the box are (2*9)(25+40) = 1170 sqft. Assuming an R-2 (just plaster, an airspace, some old windows, that’s 1170* (65-40 (design temp))/2. That’s 14,625 btus. The bottom of the box will be determined by your insulation plans. Now the leakage - you can roughly divide CFM50 by 20. Then multiply that by 1.08*the same 25 degree delta and you get 3200btus. So that’s roughly 20000 btus using extremely conservative wall insulation values. Somehow, your contractor thinks there’s 40,000 more unaccounted for. Find a new one!
Heating design temp for Alameda County, per EnergyStar.gov, is 32F.
The temperature swings on the ocean side of Alameda County are smaller than on the other side of the hills. We get a few clear cold nights each winter, but that's about it. A lot more gray foggy days, with little sunshine, and vastly different cooling numbers. No Alameda County average means much.
Rules of thumb are a very bad way to sizes a system but they are useful as a bull stuff detector and if we divide 1500 square feet by 5 tons, I get 300 that number is appallingly high.
Seems to me anything over 700 is way off.
You may find this article interesting.
https://www.energyvanguard.com/blog/air-conditioner-sizing-rules-of-thumb-must-die/
I calculate your ACH50 number at 14.2 before 10.9 after the work it is clear they did some work but consider having them do some more work. I don’t recommend spray foam often but given that it is a half story it is the only thing likely to work. If you could get under 3 that would be great.
I want to challenge you to get the fuel usage history. Most suppliers will share usage history with a new owner and if you get a grumpy clerk try again later.
Consider the possibility of filling your walls with cellulose insulation.
Walta
Cellulose insulation on 1911 stucco is a bad idea, and would lead to wall rot. Nope.
PG&E is the utility, and they won't share without the prior owner authorization.
> PG&E is the utility, and they won't share without the prior owner authorization.
I strongly recommend waiting a full year if possible and collecting your energy usage data before doing anything with upgrading the HVAC system.
Also consider installing a thermostat that logs heating hours used, which you can then use to help make sense of the overall energy numbers.
Also note your comfort levels, and what parts of the house are more and less comfortable.
That data is better than any modeling, and I wouldn't upgrade an HVAC system without having them. I collected 7 years of data, but I'm a bit crazy with these things.
Update from the OP:
Air leakage numbers:
Test in: 3083 CFM50
Test out: 2370 CFM50 after 1st day of air sealing
Test out: 1763 CFM50 after 2nd day, and sealing a pocket door cavity from above
Based on 1500 square feet of floor plan, 4138 square feet for the envelope, and 15624 cubic feet for the volume:
About 7 ACH50
.42 CFM per square foot of envelope,
42 CFM per square of envelope.
Does the house currently have a heating system? Could you wait a month and then use that data?
The house has no heating system. The new owners had the old asbestos covered gravity gas furnace removed as part of this process. Also: there's no indication the new and old owners would have comparable habits.
With your new data I calculate the ACH50 number to be 8.1
(1763x60)/(500x8) + (1000x9) =8.1
How do you calculate ACH or Air Changes per Hour?
To calculate Air Changes Per Hour (ACH), find the CFM of your device and multiply that by 60 then divide that total by the total cubic feet of the room to get your total ACH.
Q= CFM of filtration device
Vol= Room Volume
https://www.vaniman.com/air-changes-per-hour-calculator/#:~:text=To%20calculate%20Air%20Changes%20Per,to%20get%20your%20total%20ACH.
I still think it is worth trying more than once to get the history. It may not be a written policy so much as a grumpy clerk avoiding extra work.
I said consider cellulose it is possible your wall may have a water barrier IE a layer of tar paper in the wall if not I agree.
Walta
100% chance in this area that a 1911 Stucco house has (or "had") a single layer of tar paper as a water barrier. There's a 100% chance it's cracked and old, and likely eaten away by termites on the lower level.
The skin size of the home (all walls, roofs and floors) is 4590 square feet after correcting for an error in calculation.
The old gravity furnace would be very hard to estimate a flue efficiency for.
OP Here:
The heating company revised down to a 3 ton unit
BTUs 36k HSPF 10.2 Fujitsu AMUG36LMAS
Tons 3 SEER 18
variable speed Fujitsu AOUG36LMAS1 Aprilaire MERV 13 whole house filtration system.
Two zone. Heating BTU's 42,000 BTU/h
Better for sure.
But good? Your thoughts?
$ 29,891
I am also in Oakland but totally different house: 1600sqft gut remodel with passive house retrofit level air leakage (1 ACH50), dense pack cellulose everywhere, green everything, etc etc . I have a heat pump with 12kBTU cooling, 16kBTU heating capacity. My spouse has extremely low cold tolerance but comfortable in this set up.
Given that as a baseline, 3 tons for a much leakier house in our environment sounds reasonable but hopefully your contractor has modeled heat loss thoroughly to be more precise in sizing.
Which Heat Pump are you using. Who was the installer, if you don’t mind sharing?
I need to build on my list of reliable Heat Pump installers I can recommend to my audit customers in the East Bay.
Fujitsu Halcyon
Ecoperformance Builders
Ecoperformance love those guys, but they're 6+ months out for bookings.
That unit in your warm climate does almost 4 tons of heat. Still overkill:
https://ashp.neep.org/#!/product/63191/7/25000///0
I would set your place up in an online tool such as (free but they want your email):
https://betterbuiltnw.com/hvac-sizing-tool
Since you have actual air leakage numbers, the result should be pretty close to reality. Sometimes a hyper heat unit is a better fit for a place that needs more heat than cooling but they also tend to be more expensive. You might be able to save a bit and go for a non-hyper heat unit:
https://ashp.neep.org/#!/product/33398/7/25000///0
Depending on what the model says, you might even be able to squeak by with the 2 ton version.
Zoning doesn't work the same way as with a standard furnace. Unless something that specifically comes from Fujitsu, chances are it won't run well. I would stick to a single zone unless there is a very good reason for the extra complexity.
The reason for zoning is there are two floors with different sizes and heat loads.
I will try Better Build NW.
This home is in a 99% heating climate. A/C is mostly not a thing.
Generally the reason for zoning is if an area has very different solar gains from the rest of the house, things like a sunroom or a large living room with big unshaded west facing windows.
Around me in much colder climate it is common to have a single zone for a 3 story house with a finished basement, so 4 stories in effect (mostly works with some seasonal adjustment). No reason why you can't get a two story house comfortable with a single zone.
For the Better Build NW, the ACH you enter is the natural air changes per hour not the blower door ACH@50PA. You need to convert your blower door number:
https://www.greenbuildingadvisor.com/question/what-is-n-factor
> This home is in a 99% heating climate. A/C is mostly not a thing.
I said I'd never need to use the cooling in Oakland, but once I got it with my heat pump, well reality turned out differently.
> The reason for zoning is there are two floors with different sizes and heat loads.
My 2 story place is a single zone and it works fine. There is some temperature stratification (there always is) but not more than 5F.
2 tons with an 3kw electric strip backup seems like a good fit! It’ll probably be >24,000 btu at Oakland’s design temp and you can always lock out the resistance heat should you not need it.
severaltypesofnerd,
I would not go any smaller than this.
Josh
If you decide you must have zoning because you do not want to live with the upstairs being a degree or two different than down stairs consider getting 2 separate minis systems (two outdoor unit). Yes, it will cost slightly more money but you gain better temperature control, redundancy and the ability to turn off half the system when the loads are light.
Do you really need \want the electric back up heat? How often does it get below +10F when you might need it?
Walta
It's Oakland! So never. But it might be the easiest way to get a right sized system and can be never used.
+1 on never used electric resistance backup.
I just did an audit, Blower Door testing, and load calculations on a 1913 home in the Bushrod area of Oakland.
2400 sq ft 2 story over a crawlspace plus garage, all original windows except 3, none of them painted shut or sealed whatsoever.
The Blower Door was 10,250 cfm50, it couldn’t actually even hit 50Pa.
No wall insulation, very patchy and poorly installed R19 batts in the 2 attics.
I found 40 degrees winter and 81 degrees summer design temps.
Load was 54,000 Btu heating and 32,000 Btu’s cooling.
By modeling 5000 cfm50 the loads dropped to ~44,000 Btu’s, and at 2400 cfm50 it showed ~38,000 Btu’s.
It currently has a 100,000 Btu 80% furnace on a leaky duct system and undersized return duct and filter, and the homeowner only uses it for 1-2 hours at night, then 1-2 hours on cold mornings, to quickly warm the house, verifying the oversized furnace.
While I was building my super efficient house, I rented a similarly old and leaky 1700 sqft house in Oakland with a giant gas furnace, and in winter I had energy bills approaching $500/month - and this was before the huge spike in energy prices. I shudder thinking about how much it costs to heat that house now.
In such a house, a heat pump is going to increase the cost of heating.
This is pretty common in old neighborhoods in the Bay Area. In the past, California's climate was mild and energy was cheap, so even with the technology available in those days, there was little incentive to make houses more efficient. Fast forward to today and energy prices have skyrocketed, 2-3x what some other parts of the US pay, and it's a real concern for a lot of people's pocketbooks.
Realistically most of the houses that are in that kind of condition need to be gutted and rebuilt to modern code before considering heat pumps. The issue is that most households can't afford such a project. Cracking the puzzle of how to cost (aka labor) efficiently insulate and seal such houses is an open question.
On the Oakland house I audited and modeled, I recommended Air Sealing to a realistic 5000 cfm50 as well as R19 under the floors and new R38 blown into the 2 attics, after the air sealing. This gets it down to a 3 Ton Heat Pump which will be offset by the solar PV already installed
That sounds good, but at local rates, the insulation/sealing sounds like tens of thousands of work on top of $20k+ for the heat pump installation. So let's say a total of $40k conservatively?
The reality is most people would rather just put in a cheaper gas furnace instead. Which is why I think we need a low cost way of dramatically improving building envelopes. Aerobarrier seems like one approach to this, but it's not a primary air barrier, and doesn't provide insulation.
That is a false choice.
Any house can be heated with a heat pump or gas furnace. There is no need for insulation or air sealing.
The choice between the two comes down to operating cost. I'm in much colder climate and a heat pump is a bit lower than the operating cost using gas. Unlike with gas, you can also install a PV array to offset the usage of a heat pump. Electricity pricing tends to be also much more stable.
In areas with cooling, the cost of a heat pump is about the same as furnace plus basic AC, install is about the same. Getting rid of the gas burner is actually the better option for your wallet never mind the enviroment.
I guess that depends which company you hire, and how far you go. I had a previous customer pay $3 a sq ft to Air Seal and insulate under his floor with R19 batts. Then $2.50 per sq ft to Air Seal the attic and insulate with R38 of blown fiberglass.
At the Oakland audit house, it has about 1500 sq ft of floor and attic space, so $4500 plus $3750. The leaky ductwork and boots will get air sealed with a Heat Pump installation, to pass T24 HERS tests. I usually see quotes of $15,000 to $19,000 for a 3 Ton Mitsubishi inverter Heat Pump, depending on duct upgrades or return and air filter upsizing.
I’ve only had Aeroseal used on 1 gut remodel job, at about $1.50 per sq ft of both floors rather than only counting the floor and attic sq ft of a 2 story. I hate to imagine the cost of Aerobarrier on a house that’s not gutted, and needs substantial masking off of finishes.
The above effort used a local specialist with old school caulk and spray foam, $1250/day with a blower door. You go day by day, until you reach your target or give up :-).
There's a LOT of low hanging fruit, but it takes a blower door to find out.
As far as zoning an HVAC system, it works best when each zone is equal size, or equal load. You want close to the same cfm of airflow going to each zone so that when 1 zone closes, the other zone doesn’t have a massive spike in Total Static Pressure. If you have 400 cfm going to 1 zone and 800 cfm going to a larger zone, then close the larger zone damper, the smaller zone will have to handle 1200 cfm total, and Static Pressure would go through the roof, as it increases fourfold for each doubling of airflow. Of course you really should only zone if you have 2 stage or better equipment, but even dropping to 800 cfm on low stage would overwhelm the smaller zone.
Zoning a 2 story is also more of a necessity when you have larger temp extremes from heating to cooling season. Needing more airflow and heating downstairs in winter, and sometimes needing cooling only upstairs in summer. This really matters in CA where our dry climate requires high airflow per ton for best A/C performance.
For a heating dominated climate you might balance the house with duct design.
severaltypesofnerd,
I've used eQuest in the past. I compared it to Trane Trace and it did not seem to be quite as accurate but it will probably get you in the ballpark and hey, free is free. This may be a little more detailed than what you are looking for though.
Just for a rule of thumb, I generally eyeball hvac systems at 500sf/ton so if your house is 1,500sf then 3 tons is a general rule of thumb for a system for a house that size in a somewhat temperate climate but since your house is older with not much insulation 4 tons may be a closer guestimate.
BTW, ASHRAE has design conditions you can look at for free online: http://ashrae-meteo.info/v2.0/
It looks like the 99% DB Design temperature is 4.2C.
Best of luck.
Josh
I can’t even imagine 3 tons on the house in question. I don’t really like any rules of thumb, but in Oaklands climate it’s definitely based on heating and I would get a load calculation done since insulation values and Blower Door numbers are already available
A reasonable heat loss calculation can be done with a 10 digit handheld calculator. The building elements are defined by U-value and square feet for an annual heat loss using Heating Degree Days. Get a blower door test done, money well spent before making any equipment and building envelope upgrades. Randy Williams has defined very well the calculation for infiltration heat loss.
https://www.greenbuildingadvisor.com/article/measuring-natural-air-leakage
Put this information together and you will have a good baseline for the current home configuration.
“The above effort used a local specialist with old school caulk and spray foam, $1250/day with a blower door. You go day by day, until you reach your target or give up :-).
There's a LOT of low hanging fruit, but it takes a blower door to find out.”
Incense sticks and box fan duct taped into a window is just as affective as a blower door will find the same low hanging fruit and operating a caulking gun is pretty low skill work the only difference is you don’t get the feedback of the ACH 50 numbers.
Walta
Especially on a leaky house, as a DIY starting point to find and fix the easy stuff. That’s what I advised my audit customer with a 10,000 cfm50 Blower Door result to start with.
OP Here. This is what https://hvac.betterbuiltnw.com/ calculator did for this house.
Looks like a 2 Ton would do.
Possibly even a Mitsubishi M Series 1.5 Ton, as it significantly overproduces in heating mode, you’ll see in it’s extended performance charts.
severaltypesofnerd,
It looks like your infiltration load is a little low. Did this software allow you to input the infiltration rate or the results from the blower door test?
It looks like to convert the CFM50 to ACH50 you multiply 2370cfm*60min/hr/13,000 cubic feet = 10.9ACH50. An approximation of the natural ACH according to the www is to divide that number by 20 = 0.55ACH. So, to get the CFM of infiltration = 0.55ACH*13000/60 = 118.5CFM of infiltration. The heat load for that infiltration is btuh=cfm*deltat*4.5 = 118.5*(70-40)*4.5=15,997.5btuh. So, it appears that the actual heat load for your infiltration is probably higher than the estimated 2,697 indicated. If you use the higher value of 15,997.5 then your total heat load is around 36,145.5. This is a good example of why air sealing is so important in a structure.
Best of luck.
Josh
Hi Josh,
Where does the 4.5 come from? I thought it was delta T x CFM x 1.08?
I believe Paul is correct
Oh, yeah, you're right. I guess that lowers it a bit from the 15,997btuh to 3839.4btuh. Thanks for catching the error there. I guess that doesn't really add a whole lot to the load. Looks like the total is closer to 23,987btuh.
I took the AC50 at 8.1 and divided by 40 for ACHnat based on the GBA article.
Then rounded to .2
I also raised the walls from R0 to something that seemed more realistic, assigning some value to plaster and lathe and the external tar paper skip sheating.
The big problem I had with the Better Build NW tool is that it assumes ALL windows are of the same U value, and it forced me to use two 4" ducts for modelling purposes. It had no way of saying which ducts were in conditioned space, but got cranky if I just left those ducts out.
I used these numbers:
* Oakland California - Winter lows in the low to mid 40F range.
* 1911 Construction.
* 1104 square feet downstairs (9 foot ceilings), 551 sf upstairs (8 foot ceilings). Thus about 50% of the downstairs is below conditioned space.
* Crawl space and 1/4 basement below.
* 6-8 inch blown in cellulose in attics.
* 50% double pane window inserts, 25% double hung single pane painted shut, 25% double hung operable.
* No wall insulation. Exterior stucco.
* Lathe and plaster construction
* Heat only climate -- cooling is not really applicable.
Test in: 3083 CFM50
Test out: 2370 CFM50 after 1st day of air sealing
Test out: 1763 CFM50 after 2nd day, and sealing a pocket door cavity from above
ACHnat ratio divisor of 40.
+++++++++++++++++++
The tool did not let me model the glass door, the conditioned space ducts, the mix of window U factors, or the likely actual R value of the empty cavity wall assemblies.
severaltypesofnerd ,
That sounds fairly thorough. Without a lot of extra effort I doubt that you'll get much more accurate.
Josh
What I'd like to do is somehow monitor the system after it's installed, and measure it's right-size-ness. This would be easy with a standard digital data log interface to heat pumps, but I'm not aware of anything. Is there a way?
Its great for homeowners and building designers to do their own calcs so they know what size system *should* be installed and how. But in the end they are often thwarted by the HVAC contractors - especially in rural areas where there is little competition. They refuse to do the job or take any responsibility for it unless it is done their way (over sized.) As long as most of us are at the mercy of local installers and their suppliers it will continue to be an uphill battle to get "right-sized" systems installed, no matter how many calculations we have done. I'm not saying to give up and not bother - but be prepared for exhausting and continuous push-backs that you may ultimately lose unless you are lucky enough to find someone who *gets it*. Good luck!
severaltypesofnerd,
In response to post #47, the easiest method I can think of to determine if the unit is the right size once installed is just to observe how it operates and if the house is kept warm during the winter and cool during the summer. If you look at the run times of the unit that is often an indicator if the unit is sized properly or not. If the unit runs continuously or nearly continuously that is an indicator that the unit is undersized. On the contrary if the unit "short cycles" or turns off and on frequently that is indicator that it is oversized.
You could monitor the energy usage of the circuit for the hvac unit and the meter could provide a log of the energy usage. There are also smart thermostats on the market that can show how often the unit operates but I don't see any that monitor the energy usage and the run times of the hvac system both. I'm sure that some hvac systems can be purchased with a smart thermostat included. I haven't personally used either method so I can't vouch for either one.
I'd be interested to see how others have monitored their energy usage with regards to the hvac system.
Josh
A properly sized unit should run continuously on the design day.
It seems like it almost never happens that installed performance is checked against the design. I think that would be an interesting DOE research project -- install monitoring software on 1,000 houses where a Manual J was run. At the end of a year, compare actual usage to the model. I bet it would be eye-opening.
“severaltypesofnerd | Dec 05, 2022 09:27pm | #47
What I'd like to do is somehow monitor the system after it's installed, and measure it's right-size-ness. This would be easy with a standard digital data log interface to heat pumps, but I'm not aware of anything. Is there a way?”
There are literally dozens of different monitoring systems for electrical use that could monitor the new heat pump.
I bought a Lantern Power monitor and am happy with it. It is more of a build it yourself project.
https://lanternpowermonitor.com/
Walta
A great energy monitor for inverter Heat Pump compressors, as well as any other circuits you’re interested in, is the Emporia Vue at $150-$200 for either an 8 or 16 circuit version