Double stud wall

I’m an owner/builder building a 2 story 1300 sq ft SFR. It’s my 2nd build, the first one was in 1999, so a lot has changed since then, and I have a lot of new stuff to learn.
Wanting to do minimal double stud walls with single 2×8 top and bottom plates. Looking at either two 2×3’s or one 2×3 and one 2×4 to fit the 7-1/2″ plates. This leaves an air gap of either 2-1/2″ or 1-1/2″.
Is a 1-1/2″ gap enough to break the thermal bridge of a single stud?
I would rather go with the 2-1/2″ gap but there’s places I may need the strength of the 2×4 2×3 combination due to the high snow load. It’s at 6200′ in the mountains above Reno.
I also want to incorporate advanced framing with the studs and trusses aligned on 24″ centers, so staggering the double studs is probably not an option.
That leads to my 2nd question. I want the advanced framing with the studs and roof trusses aligned on 24″ centers but want to run the floor joists at 16″ O.C. This means the vertical load running through both floors will go from 16″ O.C. to 24″ O.C. Figuring it will get strength through the rim boards, maybe with some Simpson ties and screws in the area of the single top plates, which looks like the weak point of the transition.
I know I should consult an engineer but it’s not in the budget, already had to spend $4k on the septic engineer which took me a half day to calculate and design myself.
GBA Detail Library
A collection of one thousand construction details organized by climate and house part
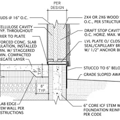
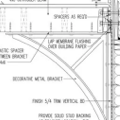
Replies
I'm sure others with more experience can comment with more authority,
but from my novice perspective, I am guessing you will need to check into codes for much of your desired plan. Not sure using only 2x3's, especially on 24" centers will fly.
Structurally speaking, the only way I could see 2x3's working, and perhaps a good idea even for 2x4's if 24"oc (again not something I am sure about in code) would be to tie the two walls together fairly well with plywood gussets, creating a sort of truss effect.
It also sounds like you're planning on both walls being load bearing. It might be worth looking into the concept of an inner load bearing wall, upon which your floor can land, letting the outer wall fly past for better thermal breakage and potentially less issue with the 24"oc vs 16"oc difference at the floor.
Full disclosure: I'm just a homeowner myself, not a professional. So grain of salt.
It sounds like you want to use 2x3s so that they can fit back to back on a 2x8. I also think you’ll need 2x4s in structural walls, but there is an easy solution to making them fit without thermal bridging issues: stagger the studs. There is no need for them to “line up”, so place your exterior stud, then 12” over place an interior stud, then another 12” an exterior stud, etc. This allows the use of 2x4 studs on both the exterior and interior side of the wall, and maximizes the amount of insulation between each stud and the opposite side of the wall in the assembly.
Bill
You have a decent instinct on reducing thermal bridging, but you are incorporating a number of distinct green wall assembly techniques into one wall, and unfortunately the end result doesn't make much sense (and does not meet code). I'll go through your options using some of the techniques you mentioned, and hopefully it will be helpful to you.
First of all, advanced framing: This is a technique to reduce the amount of wood in wall framing, which also reduces thermal bridging. You are correct that this technique involves 24" OC spacing and a single top plate, but this is only possible because advanced framing uses 2x6 framing members. 2x4 framing members in exterior walls must be at 16" OC in most situations*, and 2x3s are not permitted for exterior walls in any code I know of. Advanced framing is not as important for double stud walls, as the thermal bridging can be tackled with other methods, but is still helpful.
As for the floor joist spacing: The easiest way to incorporate 16" OC floor joists into an advanced framing wall is by adding a second top plate, giving you a double top plate like conventional framing. This means that the studs/joists/trusses can be treated like any other conventionally framed building.
Now, for a double stud wall, there is little benefit to using a single plate for both walls, as it is simple and cheap to add a layer of plywood or OSB connecting the plates. This makes it easy to make the wall thicker and add more insulation. One set of studs (one wall) will be treated as your load bearing "exterior wall". It makes most sense for this to be your interior wall, as this will reduce material cost. This wall will have to meet all the standards for stud spacing and bracing as laid out in your local building code (likely 2x6 at 24" OC or 2x4 at 16" OC). Your other wall will not be structural, and only needs to support the exterior cladding, so only needs to meet the requirements for non-bearing walls (likely 2x4 at 24" OC or 2x3 at 16" OC). Joe has a good wall design at over at the Building Science Corporation:
https://buildingscience.com/documents/enclosures-that-work/high-r-value-wall-assemblies/high-r-value-double-stud-wall-construction
If you follow his assembly, you are unlikely to have problems -- it reduces the moisture damage risks found in many double stud designs.
Alternately, you can utilize a single advanced framed wall and eliminate thermal bridging through the installation of rigid exterior foam or mineral wool board. Personally, I think this is the better approach, particularly if you have a good source of reclaimed foam nearby (I do believe there are some in Nevada, as I recall a few being posted in response to someone in California looking for reclaimed foam).
Finally, there is no such thing as "enough" thermal bridging reduction -- the more the merrier, but even a little bit helps.
*If your jurisdiction uses the IRC, you can see stud spacing requirements in Table R602.3(5), available here: https://codes.iccsafe.org/content/IRC2015/chapter-6-wall-construction
Similar situation, but I was planning double stud wall on 2x10 plates.
I concluded the increased cost of framing materials and labor did not justify the R value increase VS. my alternative design that I went with. 2x6 with Zip-R9 sheathing.
The center cavity R value of my double wall was about R31 and the Zip-R9 wall is R28. There's less thermal bridging at the plates, floor and rim boards with continuous exterior insulation as well, I didn't calculate it, but I think this is a net gain in overall R-value of the house.
The thing with double stud walls is they can be any thickness, so if you're going to do it, it aught to be thick. It costs the same in lumber either way.
GSTAN
There is a far more rational way to construct a double
stud wall - We're going to put the air/moisture barrier in
the middle so it can dry to both outside and inside and
insure that the surface of the moisture barrier always
remains above the dew point!
Outer stud wall - ordinary 2x6 with batts (mineral wool or?) -
then fasten 2 or more inches of polyiso to the inner face
of the 2x6 studs - then construct a 2x4 inside wall against
the inner face of the polyiso. The inner 2x4 wall becomes the
service cavity and sheet rock hanger - the polyiso (Foil Faced)
is the air/moisture barrier and is protected from physical
damage by both inner and outer walls and from R value drop
by the insulated outer 2x6 wall - YES! you do need to tape
the seams on the inner side of the polyiso and seal it to the
floor and ceiling with some combo of caulk, tape, or spray-on.
With 3 inches of polyiso the total wall thickness will be 12
inches (stud face to stud face) - the actual R value will be
around 36. Want more R value? Fill the service cavity with
batts or blow in for around R-46, Or increase the thickness
of the polyiso and/or use 2x10 for outer wall. With this wall
design at 12" or more, the foil surfaces (inner & outer) of
the polyiso will remain above the dew point for any temperature
ever recorded (summer or winter) in North America. That means
no condensation in the wall which means no moisture problems!
There are some unstated assumptions here, of course, such
as a working heating/cooling/vent system, good choices for
exterior siding, sheathing, and rain screen, a preference
for living at normal temp/humidity levels, quality construction.
Why fumble around with fragile vapor retarders, exterior foams
vulnerable to insects and/or fire, awkward and labor expensive
siding installation over foam, or insulation prone to settling
over the years?
User...182,
Isn't that assembly really a typical wall with interior foam, and service cavity added?
If you're only using a 2x8 bottom plate (7.25") maybe a cross-hatch or "mooney" wall makes the most since practically and financially. You should be able to advance frame 24" O.C. using 2x6's with the double top plate as mentioned for the floor joists, single top plate if the roof trusses align. For the cross-hatch you can rip 2x4's in half and install horizontally to give you a 7" cavity space which you could then insulate with BIBS.
You'll find that since your already into the cost of additional lumber (in the form of cross-hatch or the 2nd wall of the double assembly), you could allocate that towards furring strips and put the money into foam sheathing over the exterior which has direct bang for buck on whole wall R value. It can be taped for a more robust air barrier and alleviates the typical moisture concerns of the double wall sheathing. You can make up the cost of the rigid foam by installing batts in the wall cavity yourself. (Here, 2x6 BIBS is $.90/sq ft for R-21'ish. I can buy R-21 batts at $.50/sq ft or R19 batts for $.33/sq ft, reclaimed 2" polyiso runs $.50/sq ft)
In my personal shopping experience, Zip R12 ran about $60/panel where as regular zip ran $28 panel and reclaimed foam prices are around $16/sheet for 2" polyiso. If you choose the latter the sheathing is protected by the insulation, the fastener depth and nailing pattern is less, and the furring strips take the fasteners from the siding rather than the zip sheathing.
So in a nutshell, I don't see how you can get a better bang for buck and simple constructed wall than the 2x6 advance frame with foam over the sheathing. Good luck
Thanks for all the replies. What I'm looking for is a simple minimal stud wall because I'm working by myself with maybe part-time help. Yes there is plywood webbing to tie the two studs together so it becomes one stud. So one 2x4 and one 2x3 become a 6 inch stud.
I don't want foam for environmental reasons and it becomes two insulation operations which is more labor. I may just have to go 16 OC on the first floor.
My comparison is to my Seattle home which had r21 walls. If I can eliminate the thermal Wood Bridge and with thicker walls get R-25 or R30 then it should be enough for the colder climate of Reno.
Thinking that an air gap is an air gap so 1.5 should be good enough and 2.5 wouldn't make that much difference with the same total wall thickness
"I don't want foam for environmental reasons ..." This is respectable, I originally had the same thought. My mind was changed by Martin when he said, paraphrased "At least the foam is being put to good use, reducing energy use"
"and it becomes two insulation operations which is more labor." I also said the same thing here. But then I discovered the Zip-R system, which brings it back down to just 1 operation.
>Thanks for all the replies. What I'm looking for is a simple minimal stud wall because I'm working by myself with maybe part-time help. Yes there is plywood webbing to tie the two studs together so it becomes one stud. So one 2x4 and one 2x3 become a 6 inch stud.
While that is true enough structurally, you'll have to talk to your local code official if you want to try that for 24" OC. I think from a labor perspective you are better off treating the 2x4 and 2x3 walls as distinct, as that will keep the wall weight down when assembling.
Edit: As an extra note, no matter what kind of double wall you build, you should put an air barrier on both sides in order to prevent water from condensing in your walls.
>I don't want foam for environmental reasons and it becomes two insulation operations which is more labor. I may just have to go 16 OC on the first floor.
While there are some legitimate environmental reasons for avoiding foam (mitigated by using reclaimed foam), mineral wool board has no such issues. The extra labor from the two insulation operations is probably less than the additional labor from two framing operations (esp. if you are including a rain screen anyway), but if you are doing it yourself what is more important what you find more enjoyable.
If labor is the *biggest* concern, then a single wall using a product like R-Zip is your best bet, as you will almost certainly be using continuous sheathing anyway (no additional insulation or framing operations). You can get up to and extra R-12 on the exterior (making the assembly nominally R30+), and in exchange for some taping you don't need to put up house wrap or deal with a separate air barrier.
>Thinking that an air gap is an air gap so 1.5 should be good enough and 2.5 wouldn't make that much difference with the same total wall thickness
It would only make a difference of ~R2.5, so that seems right.
I'd skip the single plate for double stud idea. With one plate, you'll end up with very heavy walls that'll be hard to stand up, even without sheathing already installed. There's no benefit to a single bottom plate and if you want to tie the two walls together at the top, a single piece of plywood will do. As suggested above, why not put more space for insulation between the two walls. I assume at 6200 feet, you can use the extra insulation.
A minimal stud wall accomplished by framing a double stud wall? If you're aiming for under R30 the cross hatch wall can reach R26-R29 depending on the blown density. If you quantified the actual impact of whole wall R value of your stack up versus that I don't see how it's cost-effective to persist with a double stud wall. It does make sense if you're increasing the wall thickness to allow R40+.
What are you using for sheathing, weather, and air barrier?
You still have to have a rainscreen gap (either mesh or furring will cost extra) especially with the double wall
What windows do you plan on installing?
It would be great if you shared what wall you finally build and the costs/labor associated with it.
A double stud wall 7 1/4" thick with 2x4s and 2x3s 24" o.c. and cellulose insulation is an average R-25.2 center-of-wall. Simply framing with 2x8s 24" o.c. gives an average R-25.0 center-of-wall. Both wall systems have the same thermal bridging at plates etc.. If you're already planning to stand a heavy wall, I don't think the extra effort of using a double stud approach is worth R-0.2.
You might find a Mooney wall, aka cross-strapped wall, easier to build. With 2x6 studs 24" o.c. and 1 1/2" cross-strapping, the wall would be an average of about R-24.5 center-of-wall. But I just built an addition using this method and found it more challenging than I expected. If I try it again, I'll include a final interior layer of vertical 1x3s. But that's even more labor, so I'd lean toward the simple 2x8-framed wall. Or a true double-stud wall, at least 10" thick with separate plates.
Michael:
"I'll include a final interior layer of vertical 1x3s"
For what reason(s) would you include these vertical 1x3's?
Tyler, I found, at least on my little test project, that horizontal strapping on the wall required extra work at electrical penetrations, windows, doors, and at the sloped ceiling. An interior layer of vertical 1x3s would have made all of those items easier. I actually did end up using the vertical 1x3s in a mechanical closet and it made drywall installation easier.
Michael took the words right out of my mouth. Because I just ran the math and a 2x8 conventional wall is about the same R value as a 2x8 double stud wall. And the price of the stud lumber is about the same, not counting the time it would take to build double studs with plywood webs.
The big material savings is going to 24" O.C and the advanced framing. So with a single 2x8 it should be good structurally at the ground floor of a 2 story, and I don't have to worry about trying to get the unconventional double studs past the inspector without engineering.
To answer other questions the wall will have OSB sheathing, probably Hardi plank lap siding, and standing seam (hidden fastener) metal roofing. Maybe plywood sheathing on the knee walls down low, it's on a 17% slope. Also there's high snow load with a total 100 PSF roof load, and 100mph wind load. We've already had two 70mph days this winter.
The first house had T-111 which meant the sheathing siding was all one piece, and all guidelines were followed so after 20 years it was still holding up. But the forest above Reno has a high fire hazard so wanted to move to the cement siding, but the Hardi panels aren't very aesthetic, the grooves aren't deep enough to make it look like real vertical planks like the T-111. Would like to find something that serves as siding/sheathing, looks good, and is economical.
I really wanted metal siding because I re-roofed the Seattle house with metal right before I left and it went really quick. But the HOA won't allow anything that doesn't at least look like wood, and the only simulated wood metal siding I've found is cost prohibitive. And there may be more moisture problems with metal siding?
Also this project is limited in budget and time. Not specifically my labor but the time allowed until completion. The Seattle home was sold in a high market, enough to allow me to pay living expenses for 2 years so I can work the project full time. I built the 1st house working a full time regular job at the same time, that's not happening again.
So is it worth is to compare material costs between this conventional 2x8 wall and these other wall systems mentioned? Because the 2x8 wall is already near the limit.
And are there any opinions on hardi plank lap siding without sheathing, just let in braces for shear? My neighbor did that on his garage but it seems kind of sketchy. It would be nice to somehow have only one sheathing/ siding.
I wouldn’t trust let-in bracing in a 100MPH wind area. I don’t really trust let-in bracing in “normal” wind areas. I don’t trust the diagonal steel strapping either. Both styles of bracing put a lot of shear force on a very small number of nails.
I’d use either regular plywood/OSB sheathing, or at least shear panels at the corners and periodically along any long walls without any corners. I prefer a conservatively framed structure.
You might look at other fiber cement options besides just James hardi offerings. Allura I know makes some thicker (5/16” instead of Hardi’s 1/4”) panels.
Bill
There sometimes seems to be a tension in discussions here between energy efficiency and a robust structure - as th0ugh the former has to come at the expense of the latter. I think that's a mistake.
Yeah, I’ve seen that too. I spend too much time at work doing predictive failure analysis to ever think of taking unecassary risks at home. Plywood shear panels are cheap insurance. All the efficiency in the world means squat if your house is lying flat on the ground after a major storm blows through.
I agree there is no need to sacrifice structural integrity just to be energy efficient. I have real plywood sheathing under my rigid foam on my own house. It helps with sound reduction too. I don’t let anyone use OSB on the roof either since it’s weaker if it gets wet. Sometimes old school has some advantages :-)
Bill
Chris,
I think more people should stand on the roof of a house that was not fully sheathed in plywood VS one that was. It would eliminate the common misconceptions that studs hold up walls.
For budget metal siding (board and batten look), I have used galvanized steel panels sheared to width (not too wide or too tall as it will oil can), with the right primer and paint they last. You can use either wood or cement battens to finish it off. More labour to install but cheap per sqft.
"I think more people should stand on the roof of a house that was not fully sheathed in plywood VS one that was. It would eliminate the common misconceptions that studs hold up walls."
Being rather cat like, I can't help but ask: What is the (mis)conception that studs 'hold up walls'? What would one discover on the roof that would clarify things?
edit: I'm perhaps unclear on if you mean walls that are as of yet unsheathed, but have plans to be; or if you mean walls that have employed some other method of racking resistance.
Tyler,
I was being a bit cheeky. Lot of the stiffness and the strength of a house comes from the plywood on the outside and the drywall on the inside. The studs are there mostly to keep those two sheets a certain distance apart (walls would be just as or even more solid if you used foam instead of studs, thus SIP).
When I was building my home and was finishing up the roof, I remember calling the structural engineer that this doesn't feel stable, maybe some detail was off, it felt like the house was doing the macarena underneath me (the walls/roof were diagonally braced at the corners with temporary 2x4). As soon as the plywood went up, that all changed. Turned into a solid structure.
For the money and for my own place, I would not skip the exterior sheathing.
I gotchya. Thanks for taking the time to explain. Makes sense.
Tyler,
When a wall is sheathed it acts like a box beam. The bottom and top plates function a bit like the chords on a truss, and it becomes appreciably stronger, not just in shear, but in it's ability to resist vertical loads.
The shear resistance of sheathing makes sense, but I honestly have never given much thought to the added resistance to vertical loads. My question was admittedly perhaps a bit sardonic, implying that the studs do hold the wall against gravity; the sheathing just keeps it properly in line with gravity... (I also originally misunderstood what Akos wrote I think). But I'm intrigued and schooled by considering its added vertical strength. My assumption would be that the nailing of the sheathing keeps the studs in a rigid line and prevents them from bending under load.
Not to get completely side tracked here... but does a 1910's bungalow sheathed with horizontal 7/8" thick boards rely primarily on the moment arm created between the nails to resist shear? How much does interior plaster and lathe contribute, if at all? Perhaps there is likely to be diagonal bracing somewhere? (Haven't found it in the particular structure I'm sheltering in... yet)
Tyler,
The sheathing does reduce the studs tendency to bend, but there are other things at play.
- The sheathing helps distribute loads.
- Sheathing makes the whole wall act like a very large box beam. I have worked on multi-unit projects where the exterior walls on one floor were designed as box beams which held up the floor and roof above.
Old board sheathed houses often do rely on the nails to counteract shear forces. Our code no longer allows this, but still does let you sheath with boards as long as they are on the diagonal. Plaster and lathe contribute a lot to shear resistance. Even drywall is acknowledged in our code as being part of the structure. Dana has suggested cavities with spray foam are a lot stiffer too, although I haven't seen any values for that.
Chris, I'm of the opinion that the thinnest double stud wall possible just doesn't make sense. Just look at all the alternatives people have offered you. I say, if double stud is what you want, go with an 11" thick wall (+/-) if you can. That's where double stud walls start to make sense. If you're stuck on the thinner wall, and don't like the options offered above, yet another option for you is a "Bonfiglioli" wall using 2x6s on 24" centers to hold up your snow laden roof and the fir out the studs with 1" of foam plus wood strips. The result is the same thickness wall with less thermal bridging due to the advanced framing and an extra R3 (ish) on the studs, that's only a moderate amount of thermal break, but not nothing. See https://www.finehomebuilding.com/2014/11/26/breaking-the-thermal-bridge for a better description. Fill the cavities with dense pack cellulose and you get R 26 ish. Center of wall.
T1-11 meets the CA Wildland-Interface code as an acceptable exterior material. If you build near Reno you are in a elevated seismic zone so shear panel would be more robust than let in bracing, but you can follow the IBC prescriptive provisions for that guidance.
Ok then, it's going to be 2x8 walls. 1-1/2" EPS in the crawl space, inside the stemwalls and under slab. Glass batts in the walls, floors, ceilings, R25, R40, R50. (maybe blown cellulose on the ceiling) On a percentage basis compared to the Seattle home of R21, R30, R40 it works with the colder temps of 6200' zone 5. Glass batt may not be the best but it's the most affordable and easiest to DIY install.
The advanced framing with all 24" O.C. 2x8's will bring the lumber cost in very close to the 16"O.C. 2x6's conventionally framed of the first house. And avoiding the double stud and multiple insulation operations will keep the labor time more realistic.
The vapor barrier will be Tyvek with tape(or an upgraded similar product), the kraft facing on the batts, and VB paint on the drywall. Also want to focus on sealing using a blower door to test. I think this a facet that could yield good results with more labor than material cost. Really like the idea of the aerosol sealer that fills leaks (think bug bomb) using a blower door type system to pressurize. If it could be made DIY maybe?
I'm considering going to all plywood on the sheathing, at least on all the bottom edges, it goes along with the minimal use of foam, for less VOC's. It's only about 50% more than OSB. The first house was all OSB and it did hold up except where there was a clogged gutter that wicked water into the roof. But there was definite VOC, like when the floor decking got wet during construction and I sanded it with a big belt sander the dust really smelled and felt toxic. But the decking and joists need to be OSB to stay within budget. Maybe the sheathing is the best place to upgrade since the big threat of fire is from the exterior in this area.
And according to NIST fire exit times have gone from 17 minutes in 1970 to 3 minutes in 2015, probably mostly due to OSB and foams.
And this house is affordable at this budget level, will not need any borrowing, and it could even be done check to check for someone younger.
take zip tape and tape all your sheathing seams- cheaper than sealing from the inside. caulk your drywall at the top plate. Instead of 2x8s, use 2x8 top and bottom plates and do a staggered stud wall with 2x4s on 24" centers. I have built a half dozen homes this way- works great and you do mitigate the thermal bridging found with solid 2x4s. Use advanced framing techniques wherever possible...