Double Stud Wall sheathing and vapor barrier

Hello,
I am building a 10″ thick double stud wall that will be dense packed with blown in cellulose. I live in Virginia in climate zone 4 in a mixed-humid climate. I am worried about warm air getting into my wall cavities and possibly condensing on the cold sheathing during the winter months. I have been thinking about my different options and was hoping to get some advice on each option.
Option 1. I am going to install a smart vapor barrier (Intello Plus) on the inside of my wall between the drywall and studs. The smart vapor barrier has a perm of 0.17 in winter and a perm of 13.20 during the summer. This would prevent exfiltration of warm air into my walls during the winter, but allow any moisture that enters my walls from the exterior during the summer to dry out towards the interior. For the sheathing I am planning to use 5/8″ densglass sheathing which has a perm of >17. This will allow any moisture that does enter my walls during the winter to dry to the exterior during the summer. As the water resistive barrier, I intend to use felt paper with a Cor-A-Vent or 1×4 rain screen over top. For the siding I am using cedar and cement fiberboard.
Option 2. Install Intello Plus on the inside. Use 2″ thick Agepan THD high perminsulation sheathing with a 18 perm rating. The Agepan also acts as the water resistive barrier since it is wax impregnated and I would tape the seams with Siga tape. I would still have to do the 3/4″ rain screen over top. The Agepan adds an extra R-5.7.
I suppose both might be good options but the Agepan costs twice as much as the Denglass, which is $21/sheet (4’x8′). I am also wondering if I need the Intello Plus smart vapor barrier since I have high perm sheathing for both options.
Thanks for any advice.
GBA Detail Library
A collection of one thousand construction details organized by climate and house part
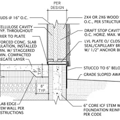
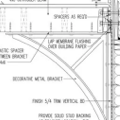
Replies
In zone 4 you don't need or want a vapor barrier in your stackup. The cold sheathing problem is more of a cold climate issue, that only gets serious in zone 6 or higher.
What you need is an air-barrier, not a vapor barrier, and while Intello could provide that function, so could many things, but caulking the bottom plate to the subfloor and using air-tight wallboard technique work just fine. And with dense pack that's more than enough from both an energy use and moisture transfer perspective. Cellulose dense-packed to 3lbs or more, it's fairly air retardent.
With rainscreened siding you can use OSB on the exterior even in zone 5 without an interior vapor retarder, as long as the interior is reasonably air tight. In zone 4 there's nothing gained by adding the smart vapor retarder. In zone 4 the cellulose itself can safely buffer the wintertime moisture load, even with 1-perm OSB on the exterior. And with a higher-perm sheathing it won't need to- it'll be drying constantly to the exterior, since moisture can leave more easily through the high-perm sheathing than it can get in via latex-painted wallboard, even with minor air leaks (though you'd still want to make it pretty air tight.)
From a bang/buck point of view it's probably just as well to use 3/4" asphalted fiberboard, which at least 5 perms even when bone-dry, 15+ perms at high humidity, and runs about R2 @ 3/4". It's not as structural as OSB or plywood, but it's more structural than DensGlass, and if you follow the fastener spacing recommendations would meet structural code without bracing in most locations. But with double studwall construction you wouldn't have to even cut-in bracing if you want to make the thing more hurricane resistant than you'd get with fiberboard sheathing alone, since the bracing can be applied to the interior side of the exterior studs. With fiberboard sheathing under rainscreened siding it's really a "who cares" sort of thing, since it's highly tolerant of moisture itself, and is more vapor open than the interior side latex paint. Cost-wise it's comparable to 1/2" OSB. (Both GP Stedi-R or Celotex fiberboard come in 3/4" structural grade, and run about R2, 1/2" structural grade runs about R1.5.)
Question for Dana: with a vapor-open wall, does the vapor coming through add measurable to the latent heat load the A/C has to deal with? If so, OSB on the outside might reduce A/C costs, but I suspect that would be a negligible effect.
Thank you Dana. This is great information. For future use, how do I determine the structural rating of sheathing? Is it normally listed in the spec sheets as the racking strength?
I am worried about DensGlass and Stedi-R because in the case of Stedi-R, the spec sheet says, "Stedi-Structural Sheathing can provide adequate racking strength when applied over studs 16" o.c." My studs will be 2x6's at 24 o.c.
Of course Let-In Bracing is an option as you have mentioned, but it'll add another step in the framing. After all is said and done, I might just have to use OSB.
Just to be sure Dana's point on the bracing was clear--it's like let-in bracing, but it doesn't need to be let in. It's thus quite quick and easy to do.
Apparently Georgia Pacific doesn't make Stedi-R anymore or rather it's only supplied in limited quantities from their Texas facility.
Anyways, these materials are specified in the International Residential Code (IRC) with Stedi-R and Celotex being considered Structural Fiberboard Sheathing (SFB) and Densglass being Gypsum Board (GB). SFB can only be used for maximum 16" stud spacing. GB would require more braced wall lengths than sheathing with OSB or plywood, which is considered wood structural panel (WSP). Of course, you can mix and match per the IRC, but I think I'm just going to stick with OSB material. I'll probably end up using ZIP system because apparently it's as vapor permeable as OSB, but a better air barrier for sure.
Additionally, I have too many windows on the South facing side of my house to be able to use LIB, SFB or GB as my bracing methods.
In conclusion, as Dana mentioned, Zone 4 does not have a high risk of condensation potential within the walls so I'll use the airtight drywall method and sheath with ZIP and call it a day. That is unless, there's something that I'm missing.
Charlie has it right- with a double studwall the bracing doesn't have to be let-in.
To have sufficient structural strength at 24" o.c. spacing the structural studs have to be 2x6, not 2x4.
Pre-ordering finger-jointed 2x3s for the non structural studwall reduces thermal bridging, and is as flat or flatter than milled 2x4s. (Milled 2x3s are prone to bowing & twisting, and make for a not-so-flat finish wall.)
Depending on the load requirements you can usually get there with using OSB or plywood as shear panels only at the corners to stabilize the wall, and filling the wall between with any sheathing you like.
In your climate (and even in zone 5) you can get away using only latex paint on air tight gypsum as the interior vapor retarder, with OSB under rainscreened siding.
Asphalted fiberboard with sealed seams is a WRB too, but it's harder to make it fully air tight from the exterior. Caulking it to the framing inside every stud bay with acoustic sealant would be a good start, and doubling up on it by taping over the seams on the exterior sealed over the tape with fiber reinforced roofing patch, which adheres well to asphalted fiber.
On the sunny south side it's really hard to end up with wintertime moisture drive problems, since solar heating of the sheathing drives off most of the accumlated moisture even in winter. It's the north side and shaded corners that never get direct sun that are at highest risk, but in your climate & stackup that risk is still miniscule.
In a zone 4 climate with a simple shape to the footprint of the house and careful construction it's possible to get to Net Zero Energy with a whole-wall R of about R25, which doesn't need a double studwall approach. (Download BA-1005, and read the first chapter, taking note of Table 2, p.10: http://buildingscience.com/documents/bareports/ba-1005-building-america-high-r-value-high-performance-residential-buildings-all-climate-zones/view ). A 24" o.c. 2x6 wall with R20 cellulose and 3" of exterior rigid rock wool sheathing (or 2.5" of EPS) would get you there, possibly more simply & cheaply than a double studwall approach. Dense packing fat walls such as double studwalls is complicated, and the number of contractors who know how to do it right are limited.
Another R25-ish wall that works moisture wise even in very cold climates is 2x6/cellulose 24" o.c. with higher perm sheathing (DensGlass or Celotex) on the exterior with a layer OSB detailed as the primary air barrier on the interior, with a 2x4 wall set tight to the OSB for the electrical & plumbing runs, insulating the 2x4 wall with R15 batts or cellulose. That puts a ~1 perm smart vapor retarder (the cellulose) inside the inner half of the total R.
The design problem to solve with that last stackup or a standard double studwall approach is the thermal bridging at the subfloor and floor joists, which is not trivial in a would-be high-R assembly. The exterior insulating sheathing approach doesn't have that difficulty, since the insulating sheathing is on the exterior of all structural wood as a thermal break. If you haven't already, download and study this document for comparison. The simplest double studwall analyzed is Case 4, discussed in some detail starting on p37 (p41 in pdf pagination):
http://apps1.eere.energy.gov/buildings/publications/pdfs/building_america/high-r_value_walls_case_study_2011.pdf
Thanks Dana. I'll take a look at the reports and thanks for the tip about finger-jointed 2x3's.
My double stud wall is modeled after some of Robert Riversong's designs: https://riversonghousewright.wordpress.com/about/11-pictures/
To insulate the plates and rim joists, the 2x3's will sit on a separate plate going all the way down to the sill plate of the basement wall. However, in my design, the 2x3s will not support the weight of the roof like in Riversong's drawing. Obviously, 2x3's couldn't be used for that load anyways. The interior 2x6's @ 24 o.c. will be supporting all of the loads.
I was planning on tipping up these 2x3 walls in 10-12 ft. wall sections or simply lining up each 2x3 individually and tying them into their adjacent 2x6 with 1x4 gussets spaced 24" o.c. Then I would nail in the top plates separately. I am largely building this house with my wife and dad so I'm thinking the double stud wall will be the simplest strategy.
My previous, smaller house we built on our farm was made using 2x6s @ 16 o.c. with 1.5" of polyiso foamboard on the exterior. We didn't have the money, knowledge, or time to airseal everything perfectly or dense pack with cellulose so the energy efficiency might not have been as good as it should have been. I didn't really like cutting, screwing, and taping in all of those foam panels after already doing the same thing with the OSB panels. The gable ends are a pain in the rear with the gables being so high up.
I am hoping to sheath and tape once and be done with it hence the appeal of Zip. For the dense-packed cellulose, I'll do it myself to make sure it's right. I will use Insulweb to contain the cellulose in each stud bay so there is no drifting from bay to bay. And since we are doing this pretty slow, the drywall won't go up as fast and I'll be able to see if there is any settling of the cellulose. I know the chart by BSC says that R-25 is good enough, but I figure R-33 is better and wouldn't take that much more work.
Attached is a picture of the front side of our house.
Here is the attachement.
Jimmy,
Adapting Riversong's design in the way you intend brings up a couple of points.
Riversong tied his walls together with frequent gussets to in effect make site-built trusses. You don't need anything like 24"oc to stiffen the 2"x3s". I'd bet every 6 to 8 feet would do.
Riversong was always a bit sketchy or dismissive about the necessity of bracing. If you have decided to sheath the exterior wall, you still have a bit of a problem in that the load-bearing elements of the structure (the inner wall) still has no shear resistance.
Hi Malcolm,
You bring up a great point. I didn't realize that simply sheathing the non-load bearing exterior studs wasn't going to help my interior load bearing walls with its shear strength. I thought that the gussets at 24" o.c. would tie everything together, but now that I picture it - I see that it won't. Major oversight on my part. I see that Riversong does metal T-bracing on some of his designs - https://www.greenbuildingadvisor.com/content/riversong-wall-trusses
I might have to remove or shorten the width of some windows to be able to use metal T-bracing for my braced wall panels in order to avoid having to sheath the inner and outer walls. I suppose I could go with no sheathing like Riversong, but really my mind can't comprehend that.
One challenge is that a part of my house will have 12' walls to accommodate a shed roof and Let-In Bracing is not allowed for walls over 10ft.
I now understand why Larsen trusses went on after the house was sheathed. Maybe 3" of foamboard over 24" stud bays dense packed with cellulose is the simpler option. Moreover, I can get very cheap, used foam board from Insulation Depot, which has a facility one hour from my house.
I just dread the thought of having to frame out 30+ rough openings and finding all of my studs during siding installation over all that foamboard.
Too many things to think about. I'm going to sleep on it.
Jimmy,
You have bumped up against the dilemma all double-wall builders face. I'd put the main options something like this:
- Make the outside wall load-bearing. You forgo continuous insulation at the floors and take your chances on damp sheathing.
- Make your interior walls load-bearing. Sheath both walls, or forgo sheathing on the exterior making the sequence of insulating, siding and trim more complex.
I don't think there is any clear-cut answer. Both are routinely done. I guess another question would be whether they are more difficult than exterior insulation with all its attendant flashing problems?
looking at all the present options for increasing wall performance, you begin to see why most North American builders continue to use 2"x6"s.
Thanks Malcolm. I just came upon an amazing realization. I was calculating the amount of braced wall panels I needed incorrectly and overestimating how much I needed. The braced wall panel section of the IRC is one of the most confusing things I have ever had to interpret in my life. Luckily, this little guide helped: http://www.palatine.il.us/assets/1/building_permits/IRC_Wall-Bracing_A_Guide.pdf
Anyways, my mistake was in thinking "braced wall line spacing" meant the actual length of each wall line. The difference was 25ft. vs. 42 ft., which lowered the amount of braced wall lines needed by 10 ft. This is huge. I believe I can now use Simpson Metal T-bracing for my braced wall panels without having to drastically reduce my openings. Although, the IRC says that Let-In Bracing can be used only on a maximum 16" o.c. stud wall, the Simpson WB series bracing says I can use it on 24" o.c. spacing when installed in "X" pairs or in opposing "V" fashion.
The double stud wall may be a possibility after all. This after almost being resigned to using foamboard and spending an hour studying Dudley boxes. I was worried about having to install 100+ pound triple-pane Intus windows over 3" of foamboard and a 1/2" plywood dudley box!
Jimmy, That's great. I share your trepidation about complex window details.
I just encountered another issue on the double stud wall that I am planning to build. If I have a front porch with roof, where do I attach the ledgers? My rim joists are actually hidden behind the non-load bearing 2x3's. Will I have to do a free standing deck?
It's possible I could attach the ledger to the 2x3 studs provided I screw at least 2 timberloks at each stud. For added strength, I could also put blocking between each stud where the ledgers will be. In this case, I would have to definitely do the 1x4 cleats 24" o.c. up the wall to tie the 2x3s into the load-bearing 2x6s.
What do you all think?
See attachment for more details of the design. Thanks for any insight.
Here's the attachment.
Jimmy,
I'd be inclined to keep the bearing on the inner-wall and treat the ledgers in a similar the way to what they do when there is foam on the exterior. Here is one variation:
http://cchrc.org/docs/best_practices/REMOTE_Manual.pdf
Jimmy,
There are lots of reasons why porches and decks should have independent foundations rather than depending on a ledger to support floor joists. Don't be afraid of the "independent foundation" route.
Thanks Malcolm and Martin. I am leaning towards the free standing deck approach. I think my building inspector would be very curious about those blocks connecting the ledger to the rim joist. They might require an engineer's stamp, which would cost me a couple hundred to even a thousand dollars to get.
On another note, my building permit reviewer said that I didn't need to brace the interior load-bearing wall if the outside walls were already sheathed/braced properly. I am still going to use Simpson metal bracing on the interior walls as I want to be under roof before putting up my non-load bearing 2x3s. This is all in an effort to avoid more rain and snow getting on my framing than needed. The metal cross bracing will keep the walls steady for the trusses and roof deck.
If anyone is coming in for the Green Building Conference in D.C. from November 18-20 and wants to make a side trip out to see my construction let me know. Our farm is about 1 hour and 30 minutes from D.C.
Jimmy,
I don't see how making the deck freestanding helps solve the problem of how to support the shed roof over it.
I'm also not clear how sheathing the outer wall, which doesn't support the floors or roof helps provide shear support to the load bearing structure. I'd be interested in your BI's rationale.
Hi Malcolm,
The shed roof would have to be supported by posts in the front and the back. All of the posts would be tied into the wood deck with post anchors lag screwed into the deck and blocking underneath and it would bear directly over the concrete piers. The posts in the back would obviously be higher to get the appropriate pitch. Doubled 2x8s with a ledger strip or rafter hangers would support the higher side of the rafters. The lower end of the rafters would sit directly on the doubled 2x8 header with bird's mouth notched in and hurricane ties.
I actually did this with the previous house we built because a cantilevered second floor prevented us from tying the ledger to the rim joist. The only drawback is that we may have to dig the piers that are closer to the house a little deeper because the backfill in that area may not be compacted enough. Also, we will have posts sitting close to our wall, but we can always use those posts to hang stuff on like garlic or shovels.
I would then have to extend metal flashing to bridge the slight gap between the shed roof and wall and tape it and have the WRB lap over it. More work than tying directly into the rim joist that's for sure. I guess I can talk to the building permit office about the other method you shared and see what they say.
In regards to shear:
On my framing plans, I showed 1x4 gussets @ 24 o.c. connecting the two studs. I will also tie the 2x3s into the trusses at the top. I'm guessing he thinks that the sheathing on the outside will prevent wind from racking the interior walls. Really, it was just a 2 minute conversation over the phone and I wasn't going to push the issue because I didn't want to have to amend my plans again. I always have to keep in mind that we have more relaxed zoning and building officials compared to our more Northern neighbor counties like Fairfax, Arlington, and Alexandria, VA. For comparison, it takes 2-3 weeks to get a plan reviewed and approved here, whereas it would take 4-6 months in those other counties.
So I will still brace the inner walls for added strength and sheath the outer walls for extra strength, air barrier, and ease of applying siding.
Still hoping that this takes less time than going the 2 layers of foamboard route. At the very least, it will be cheaper.
On another note - I'm having a hard time finding dove-tailed 2x3s let alone 2x3s. I might have to just use 2x4s for my non-load bearing studs, which will raise the cost.
Jimmy,
You wrote: "I guess I can talk to the building permit office about the other method you shared and see what they say."
I wouldn't. you sound like you have developed a pretty good plan of action. I'm sorry - I don't think I've been much help to you in this thread, but despite that you seem to have got to where you need to anyway! Good luck with your build.
Edit: In a lot of markets 2"x3"s are more expensive than 2"x4"s. I hate working with them. Being forced to use 2"x4"s may be a blessing in disguise.
Malcolm,
Don't worry, you da man and have helped me think this through a lot better. Everyone on here has helped a lot and the discussion made me go out and study Let-In Bracing and metal bracing. I've been reading all of the GBA articles and comments for a few years now and didn't have a need to post a question because almost all the questions I had were already answered on the forums here.
But I had to finally post a question because this double stud wall method is like one big jigsaw puzzle and I'm glad I did post because I have learned a lot. It's nice to have a community like GBA. After building this house, I am going to get my builder's license and try to start building energy efficient, healthy, and long-lasting homes for others. I credit GBA community for giving me an equivalent of a Bacherlor's in Green Building and for free!
I know this was posted a couple of months ago, but wanted to send an update about the wall bracing for my house construction. I used the Simpson WB bracing and most likely overbraced my walls just to be safe. In some instances, I extended the bracing up to attach to my rim joists like some builders do with sheathing to tie their walls to the floor joist system. I looked at some pictures of Riversong's double stud houses and it seems he didn't brace as much as I did so I have confidence that my house has enough shear strength. Moreover, I will be sheathing the outer studs and since they are tied into my load bearing walls, it will provide additional strength.
Here are some pictures. I was able to get my house under roof before the 20" of snow fell. 6"-8" still got into the house, but I'm grateful.
You can see the beginnings of the double stud wall. I have only completed the first floor section. On top of the single plate of the exterior studs I will be putting a piece of 3/4" plywood that extends back to the house as a fireblock. Also, I might have to do some headers and jack studs on these outer walls as they will be bearing heavy Intus triple pane windows. The 9' window will weigh 274.5 lbs. I see that Riversong only relies on a single plate along with some cripple studs to support the weight and I'm guessing that is enough, but I think I'll overbuild in this instance and maybe do a double 2x4 or 2x6 header. At the very least, a 4x4 should do.
Jimmy,
Pictures like that should make me stop complaining about framing in the rain.
Framing in the Rain - sounds like a good title to a song.