Doubling up on cement fiberboard

I’m planning to use smooth cement fiberboard cut in half lengthwise to create 2 x 8 panels for exterior cladding. Because it will be hard to get the furring strips used to create an air gap perfectly flat and the 5/16″ thick panels in 8′ lengths are not very rigid, I am thinking of doubling up on the cement fiberboard. From outside to in the assembly would be
1. 2 x 8 panel of cement fiberboard
2. 4 x 8 panel of cement fiberboard
3. furring strips
Is this a reasonable solution to getting the dead flat surface I am trying to achieve? Are there drying problems with this assembly?
GBA Detail Library
A collection of one thousand construction details organized by climate and house part
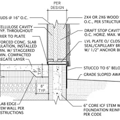
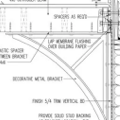
Replies
Cali,
Is this new construction? Are you installing the furring strips on something soft like rock wool? i'm trying to figure out what it is that stops you from having a flat substrate for the siding. Installing cement board panels on furring is something that gets done routinely without problems.
Hi Malcolm
New construction
Furring strips are going over conventional sheathing (plywood vs Zip TBD)
I want to use the Hardie Reveal system with 7/16" cement fiberboard but can't afford it
https://www.jameshardiepros.com/products/hardie-reveal-panel-system
I'm trying to recreate the look with 5/16" cement fiberboard
I have read that the Reveal system uses the thicker material to avoid undulations that can occur with the 5/16" panels
This is the look I am trying to achieve
Cali,
The concern on your installation is the unsupported horizontal edges of the panels. That's probably why they recommend thicker stock. As you can see from the attached photo, 5/16" panels lay flat as long as the edges are supported.
The problem with a second layer of cement board is stopping bulk water from getting between it and the first layer at the horizontal joints. A couple of other problems are you end up with a very labour-intensive installation sanding and coating the exposed edges on each panel, which are vulnerable in a way they aren't on trimmed panel cladding. You also don't end up with reveal deep enough to give the shadow lines you want.
Honestly I think you have two choices. Pay for the lo0k you want and use the appropriate products, or abandon it and use another cladding. Trying to jerry-rig a solution is going to end up causing you grief.
This is our local art services building which uses 5/16" cement board with metal trim on plywood furring at 16" oc.
Malcolm
All edges will be supported- see horizontal trim detail below
Yes, lots of sealing of cut edges but I’m willing to pay that price in order to achieve the look I want
Don’t understand why the reveal is not deep enough- please explain
I’m encouraged to hear that a single layer of 5/16” panels will work!
Cali,
I thought from your post you were trying to substitute a second layer of cement board and eliminate the trim. It was a bit confusing because the reason you gave was cost, and I couldn't understand how installing two layers of panels would be cheaper than one 7/16" one.
If you are still worried about potential waviness, you can always reduce your spacing on the furring to 12" oc.
Sorry for the confusion
The 7/16" system is about 6x the price of a 5/16" system
So 2 layers of 5/16" panels would still be cheaper than 1 layer of 7/16"
Yes- waviness is the concern. I'm going for a dead flat look
Do you think 12" oc furring with standard 16" oc stud framing will work?
Cali,
6x. That's crazy!
There are two things at play governing spacing for attachment to cladding. The building code and manufacturer's installation requirements.
Our code allows the furring to attach to the sheathing, rather than hit studs, as long as the sheathing g is 1/2" or thicker - and practically, it's virtually impossible to pull off 3/4" plywood strips nailed with ring shank nails into plywood sheathing.
Some manufacturers require thicker substrates for attachment of their cladding. Frankly, although I've used Hardi-Panels, I've never looked at what they want.
Aside: Warranty claims are an interesting subject. It might be a good one for a GBA blog - although perhaps because it touches on so many different jurisdictions it would be difficult to give definitive advice. When I brought this up with a lawyer specializing in construction law he suggested it would be unlikely a manufacturer could deny a claim if the failure to follow installation instructions didn't materially affect the defect or failure being claimed against. In your more litigious society it might not be worth taking the chance.
A house I did using Hard-Panels as a base for board & batten:
I like the nice clean lines on that siding Malcolm. Why the inset treated boards for the conduit though, instead of fastening through the siding? Was that a local inspectors requirement?
Bill
Bill,
It's nightmare requirement imposed on us by the power company. You can't bury the conduit in an exterior wall, and the specs call out the length and width of the PT lumber you have to provide as backing. It's bit better once it is painted, but not much.
Given the opportunity to do it again, I'd spring for the extra cost of going underground right from the power pole.
Here is a garage I did with the 5/16" panels. Pretty standard install, strapping over cinder block, no issue with warping. It is still not as smooth as the thicker panels, but not bad for a budget finish. Definitely a lot of cutting an sealing edges.
Did have to put extra strapping at the edges, each edge has its own set back about 1.5", this way you get the nice shadow lines.
Didn't use any flashing at the gaps, couple of years down the road, it is as good as the day installed.
That looks great!
What did you seal the edges with?
When you say that you did not use any flashing at the edges, are you saying you did not use any metal trim and it is an open cladding design?
If so, do you get any animals making a home in the air gap?
The edges were primed and then painted to match the front. The back of the panels were also primed.
Open cladding design, home to the occasional spider but not much else.
The hard part with these is getting the panels the right size. I found it easiest to stack and cut all the ones that sit above another at the same time. This design is not forgiving, there is nowhere you can cheat if things are off slightly.
Any tips on the tool and techniques used to make the cuts?
Also, what fasteners did you use?
The furring runs only vertically, at the vertical gaps it was just painted black. You can see if you look for it, but not noticeable at any distance. Where you see a screw in the pictures, the furring is running from top to bottom.
The screws were shorty GRKs, they are hard to find. If you are going into wood, you can use longer ones which are readily available. I made two drill guides, one for doing the corner holes and one for a hole along the edges. Needed as you need to keep the fasteners even. In retrospect I should have gone with metal roof fasteners, easy to get in any colour plus they have a gasket built in.
A friend of mine recently did some work with these but went with PL + stainless finish nails for holding the panels. Definitely holds, we'll have to see how it lasts.
For cutting I just use an old circular saw I didn't care for with a 7 1/4" diamond blade and a long level as the guide. If you are doing a lot of cuts, might make sense to make something better. It makes a lot of dust, so get good masks, this is stuff you don't want to breath in.
It takes a fair bit of planning to get everything right, lines at windows and doors have to line up, need an even spacing and minimize the waster/number of cuts. Bigger panels always go faster.
Cali,
If I understand correctly, Akos surrounded each panel with furring set back 1 1/2". So it really isn't a vented rain-screen, and only sort of open-cladding. Not that either matter much over concrete block.
Thanks for clarifying Malcolm
Cali,
See Akos reply above. I was incorrect.
Deleted
Akos,
Nice work!