Energy efficient, durable & cost effective wall design in Chicago area

My wife and plan to build an energy efficient, passive solar house per NAHB Green Guidelines in Chicago Area. Focus is on insulation, air tightness and windows’ placement.
After going back and forward with the architect and the builder, and spending hours on internet that included a good read – new Building Science Report “High-R walls Case study analysis” – I am currently debating between the following:
Concept 1:
– Airtight Drywall
– 2 x 6″ advance framing (24″ separation)
– Fill in Nu-wool cellulose insulation
– 1.5″ XPS external insulation
– Cultured Stone and Fiber Cement siding
Concept 2:
– 2 x 6″ advance framing (24″ separation)
– Fill in Nu-wool cellulose insulation
– Flash with 1/2″ – 1″ Polyurethane insulation
– 1.5″ XPS external insulation (Foamula)
– Cultured Stone and Fiber Cement siding
Any thoughts? I am also open to different concepts, assuming it’s cost effective.
Thanks!
GBA Detail Library
A collection of one thousand construction details organized by climate and house part
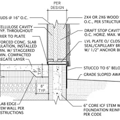
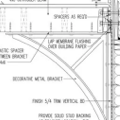
Replies
Cost effectiveness of any wall system is dependent on the rest of the puzzle. Every wall system leads to a certain cost of mechanical equipment, especially in a cold place like Chicago.
In Chicago, I would be trying for at least an R-40 to R-60 wall system with triple glazed windows (there are many ways to get there...), with the goal of heating and cooling your entire house with just an HRV and a mini-split heat pump.
A better performing and more expensive wall system could lead to a radical reduction in expensive equipment (also gets rid of things with lots of moving parts, things that need technicians to maintain them, and things that wear out over time, unlike walls and windows). This wall system will also be substantially more comfortable than a 2x6 wall, with less drafts and cold spots.
We're designing the wall systems of our houses around the equipment, instead designing a house and stuffing a furnace in it, the way we used to. An energy model is the crucial tool to show you what is possible.
Hope this helps!
Jesse Thompson
http://www.kaplanthompson.com/
Thanks Jesse!
I've looked into that .... did the heat loss calculation with thick walls (R>40) and triple glazing lowE windows. The heat loss reduction in comparison with say R25 walls and double glazed windows (low E, high SHGC on south side) was modest - around 15%. In comparison, making the building really air tight (say ACH50pa < 1) would reduce losses for 20% and it's less expensive to do. Due to budget constraints, I've shied away from doing all above and meeting Passive House Criteria ... now I am happy with 50%.
I wasn't suggesting Passivehouse so much as a design optimized for an affordable mechanical system's peak load. If you've already been doing an iterative modeling exercise, you should have the information to do that refinement. We're working hard these days to not see the wall system as an isolated cost issue, it sounds like you're already on that track.
One caveat is that we have seen some energy models (REMrate in particular) discount R-30+ levels of insulation and good windows in ways that don't feel accurate. PHPP seems much more effective at accurately simulating these wall assemblies. Most energy modeling software can't account for different window geometries, for example, it assumes all windows are the NFRC standard shape and size.
With the specific examples mentioned, I would be nervous about the drying capacity of the double foam sandwich of the rigid foam and flash spray foam. In situations like yours we have been recommending:
Exterior rigid foam (thick enough to ensure warm sheathing)
Sheathing as air and water barrier, pressure tested to verify.
Dry blown dense pack Cellulose
Air tight drywall is difficult to verify during construction, in our experience. It's much easier to sheath the building, install doors and windows, tape, seal & caulk all exterior sheathing joints and then blower door test the shell to track all air leaks in the exterior shell before insulation and drywall. There was lots of focus on this approach at the NESEA conference the last few years.
Jesse Thompson
http://www.kaplanthompson.com/
Jesse, thanks again, that is very helpful!
I like the idea to do the blower test before adding insulation, it increases the chances to to meet the goal (ACH50Pa < 1)taking into consideration this will be the first time for the builder to make the house this air tight.
With respect to polyurethane flashing, I see you point. It will be harder for wall to dry. I'll look into its perm rating. On the other hand, I'd like the fact that it also makes house stronger. Although not that frequent, there have been tornadoes in this area.
Lastly, I forgot to mentioned earlier that builder prefers to use OSB on the top of rigid foam insulation.
Respectfully,
Nenad Uzelac
Contact your local Nu-Wool contractor for the correct answers.
I suggest useing what ever framings members your design requires, to determine the amount of wall cavity insulation. The key is just having a NU-Wool contractor installing the Wallseal system. This will go in at a minimum of 3.25#/CF to create a thermal and air barrier at the same point in the wall. Airsealing is also key. Your local Nu-Wool Wallseal contractor can provide you with the load calcs for the HVAC along with energy consumption and a Heating and Cooling guarentee.
Contact Jack Golden 708-426-4356 he can help you find the insulation contracor.
I would suggest looking at geothermal for heating and cooling.
Windows should meet your local zones tax credit requirements at a minimum.