Exterior Rigid Foam and Mineral Wool in Stud Cavities

Thank you for this wonderful website. I have learned much here but have a remaining question.
I live in NY close to NYC in zone 4 and have 4” of rigid foam on the exterior with 2×4 framing and nothing between studs. I was thinking of adding mineral wool between studs.
My dad thinks that 4” of foam on the exterior is good enough and mineral wool between studs moves the dew point further inside which could get the mineral wool wet and tender it useless. Furthermore, there could be a danger of mold behind drywall because dew point is further inside.
Does that make sense?
GBA Detail Library
A collection of one thousand construction details organized by climate and house part
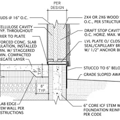
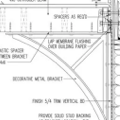
Replies
With low interior humidity and reasonable interior side air sealing, the dew point being in the mineral wool will be rare (or never) and when it does, moisture accumulation will be limited to the point where it won't be a problem.
Hi Chris,
I think you will find the conversation and links shared in this Q&A thread helfpul.
Hi Kiley, yes that question is just like mine. Does that mean I would have to make the interior drywall airtightike Jon mentioned?
Four inch foam outside might be enough and allows me to spend the money for something else.
4 inches of polyiso would get you about R26, and that would be all continous insulation -- no thermal bridges -- so a pretty good performing wall. Mineral wool in the 2x4 framed wall would give you another R15, but with the thermal bridging of the studs, your overall performance comes down to around R13.7 or so. That would bring your total assembly up from R26 (with exterior rigid foam only) to about R39.7 -- a pretty serious wall!
With your ratio of R26 on the exterior, and the R15 batts on the interior, you have over 63% of your total R value on the exterior of the wall. You shouldn't have any condensation issues with a wall like this, and mineral wool is not prone to saturating with moisture.
I would install the drywall airtight anyway as belt and suspenders air sealing, but it would be easy to get a good air seal with exterior rigid foam too. Either way, your overall wall should perform pretty well.
Bill
Thank you for your explanation! I covered the exterior sheathing with Prosoco product and tape the two layers of foam as well.
At 72F and 40% RH the interior dew point is going to be 46F. If you choose to incorporate cavity insulation, based on the math Bill did above, the equilibrium temperature on the inside of the sheathing is expected to reach 46F and starts water condensation when the outdoor temperature drops to 72 - ( (39.7/13.7)*(72-46) ) = -3F. You will get slow ice accumulation on the inside of the sheathing given these interior conditions if the outdoor temperature ever drops to 72 - ( (39.7/13.7)*(72-32) ) = -44F.
The ratio here seems perfectly fine, with far thicker foam than the typical rule of thumb about exterior insulation. You have a significant hygric buffering capacity in the wall before things can get too bad, even if we dip into dry ice temperatures for a few days. I might slightly prefer dense-packed borated cellulose from this perspective, which comes with a lot of capability to absorb water as well as a built-in antifungal treatment, but it's harder for most people to install than unfaced rockwool batts.
Proviso 1: Bathrooms & especially showers with exterior walls. 80F interior air at >90% RH in winter is going to make this math look very different, albeit only briefly. What is the specific evidence-based guidance on that matter these days?
Proviso 2: Polyiso in particular is unique in that unlike other rigid foams, it gets rapidly worse as things get colder. You'll need to do some math with the de-rating curves to determine the precise impact this has on the above equation at whatever your design temperature is.
Thank you for the illustration.
If I were to install nothing in the stud bays then I would be perfectly fine with condensation on the interior of the sheathing? Because your second term ( (39.7/13.7)*(72-46) ) goes to infinity if there is less and less insulation between the studs.
I guess that is what my dad was saying all along.
With no cavity insulation and lots of exterior foam, the inside of the sheathing will be almost the same temperature as the inside air of the home; Without a temperature difference, nothing can condense.
As you add cavity insulation and make it thicker and thicker, while keeping the exterior foam the same, you couple the surface of that sheathing closer and closer to the outdoor air temperature than to the indoor air temperature, by distancing it thermally from the inside.
The good news is that by commonly accepted standards ( https://www.efficiencyvermont.com/Media/Default/bbd/2019/docs/presentations/efficiency-vermont-bbd-rethinking-the-rules-on-minimum-foam-thickness.pdf https://www.constructioncanada.net/specifying-polyiso-for-continuous-insulation-in-walls/ ), your design already has so much exterior foam insulation that condensation is unlikely to be much of an issue in your climate... so you're free to fill the 2x4 wall with as much rockwool as you like without incurring much risk. If you built this house in Antarctica that might change.
This condensation hazard is much more relevant for people who are going to put half an inch of foil-faced foam on the outside of the 3.5" or 5.5" thick cavity insulation in their stud bays. If you think about it, a foil-faced or poly-faced foam that's 0 inch thick is indistinguishable from something marketed as a vapor barrier.
>"Proviso 2: Polyiso in particular is unique in that unlike other rigid foams, it gets rapidly worse as things get colder. You'll need to do some math with the de-rating curves to determine the precise impact this has on the above equation at whatever your design temperature is."
"Rapidly worse" may be a bit of an overstatement. Typical derating for polyiso takes it down from a bit over R6/inch in thicker sizes to R5/inch -- the same as XPS, and a bit better than EPS which is around R4.2 or so per inch. If you look at overall performance over a year, you come out ahead with polyiso. The only time polyiso might be outperformed by other types of rigid foam is during extreme cold periods. Dana Dorsett, who pointed this out to me some years back, liked to refer to the "rapidly derated" polyiso in those tests as being "worlds crummiest polyiso". He was probably right, and the manufacturers have been working to improve things.
I'm going to have to get around to putting my test rig together to get some real data here. I have the parts, but not the time to do the machining of the plates and software work. Hopefully later this year, we'll see.
Bill
It's in Owens Corning literature, but BSC apparently conducted the testing. See the graph on the upper right of page 2:
http://www.owenscorning.com/NetworkShare/EIS/10019949-FOAMULAR-XPS-vs-Polyiso-Tech-Bulletin.pdf
They're claiming:
R-2 at 15F
R-6 at 60F
and a fairly steady trendline from the one to the other. Outside this range, R-value is somewhat steadier.
Owens Corning sells XPS, so they aren't exactly unbiased. The BSC study is the one usually referred to, and the big issue people have is that BSC found different manufacturer's products performed differently, and they won't release which were best/worst. Not all polyiso suffers as much, which is why Dana commented that the really bad one is "world's crummiest polyiso" -- quite possibly selected to look bad. Dow Thermax doesn't show the same drop (and they advertise this), and old polyiso didn't either -- the issue is with some of the newer blowing agents.
All that fun stuff said, note that it is talking about a "mean" temperature. That means you need an outdoor temperature of -40F to have a mean temp of -15F across the polyiso, which is what would give that R2 value in that Owens Corning publication. A -15F OUTDOOR temperature isn't going to make the polyiso perform at R2.
Always be careful with the numbers, their meaning, and who is putting those numbers out there.
Bill
Use something like R5.6/in and sometimes R5.0 for typical polyiso. About R4 for EPS.
https://www.buildingscience.com/documents/information-sheets/info-502-temperature-dependent-r-value