Exterior tapered insulation retrofit for low-sloped roof. 1.2/12 to 4/12 pitch

Have a 1950s house in San Diego (3B climate) with an original 1500 SQFT, 1.2/12 pitch tar&gravel roof (BUR). Its over 2x6in tongue & grove boards (no insulation at all). Its reroof time and I’d like to at least have an R40 roof. Was thinking of removing the BUR, installing: air barrier membrane, tapered insulation (24 in high side to 0 in lowside) to make pitch 4/12, OSB, membrane, then shingles. I’d like to replace the BUR w/ shingles because I think its looks nicer and is easier to replace/repair in the future.
Does anyone have any detailed drawings for this? (Most tapered insulation I see is for commercial buildings or for improving drainage. My main intent is to increase slope to make the house suitable for shingles.)
Is it ok to just use foam board to build up the ridge without using framing? (Would like to avoid building a truss system if possible.)
Does this scope seem reasonable? If not would it be better to simply add 12in of flat foam board and use a torch down roof?
Anyone know any good suppliers for affordable EPS, or XPS? Maybe just need to call around? I’m seeing HomeDepot prices for non-tapered at around .90/SQFT for 2in thick EPS.
Thanks for the input GBA community!
GBA Detail Library
A collection of one thousand construction details organized by climate and house part
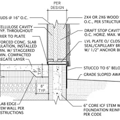
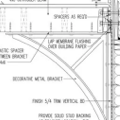
Replies
I don't think you have enough roof area there to taper rigid insulation from 24" to 0". Most tapered roof insulation will be something like tapered from 3" to 2" over the 4 foot width of a sheet. Polyiso would also put you at around R 156 or so with 24" of material, which is a wee bit excessive -- even for green buildings! It doesn't average out, either, so you'd still be loosing (or gaining) a fair amount of heat out at the "R 0" eves.
I think you'd be better off framing out a sloping roof over your existing flat roof here. You could then just vent the open "attic" space, and leave your existing roof insulation below the original roof in place, with that insulation now being on the "attic floor", in effect. If you want to beef up the insulation in that old roof, you could put polyiso over the top of the original roof, inside the "attic" you've constructed with the new sloping roof. You'd need to stick with the recommended interior:exterior R value ratios for your climate zone if going this route though. You could also blow in additional loose fill insulation instead, which will be cheaper, and wouldn't be limited to those interior:exterior R value ratios.
Bill
Greenjames,
It sounds next to impossible. You are going to need a layer of sheathing above the foam, which will have be fastened to something - and I don't know how you would do that with foam that thick.
Add to that is how incredibly hard it will be to consistently slope the roof when you are starting with an existing sloped base.
I would over-frame the roof with wood rafters and (much as I typically try and avoid it) use spray foam before sheathing and roofing. The roof joists could be 2"x4" supported by low knee walls above each existing beam. Taper the rafters to zero at the eaves so the existing fascia remains the same height.
I've over-framed several roof just like that. It was fast and easy.
Ok - So it seems like tapered insulation is out of the question to achieve a large enough pitch/slope for shingles. Given tapered board in the slope required isn't available. Overframe is a solution mentioned by Bill and Malcolm. At $10/SQFT, that would be an additional $15,000 which seems excessive.
It seems like the maximum ridged foam board thickness used is ~6 in. Making the roof R-39 (@ R6.5/in). Perhaps the easiest and most cost effective is to tear off the roof, build w/ a product like NailBase or SIP , then do a torch down roof?
Use a nailbase/SIP product or just build the system using foam board and OSB. Thoughts?
The article below has the best "system" I could find, but its not specific to low-slope roofs. https://www.greenbuildingadvisor.com/article/how-to-install-rigid-foam-on-top-of-roof-sheathing
You can easily stack multiple layers of polyiso to get up to whatever R value you want, so don't feel limited by only those thicknesses that are commonly available.
If you go with torchdown roofing, you'll be building the commercial way. You don't usually use nailbase on commerical flat roofs though, the insulation is often installed right under the roof membrane. It does help a bit for durability -- especially if you're going to be walking on it much -- to put rigid board material on top of the polyiso under the membrane for some additional physical durability. You need to offset the seams of the rigid board from the polyiso seams if you do this.
I would look at EPDM and TPO roof membranes too if you go with a flat roof.
Bill
GreenJames,
15K to over-frame. Yikes! Makes sense to do as you suggest - just add nail-base, and be done.
If you do want to get away form BUR or EPDM, the one option is metal roof. It won't take a lot of tapered polyiso to get you near the 2:12 that some snap lock units are rated for.
Most commercial roofing places will have 1/8" per foot and 1/4" per foot tapered polyiso in stock. You'll have to do a bit of figuring to get the layout right.
You can either strap out the foam with 1x4s or install a layer of CDX/OSB over it before the underlayment and metal roof goes on.
Unfortunately this will all be way more money than a new flat roof.
Considering cost and mild San Diego Climate, do you think it is acceptable to remove old gravel and leave existing tar? Replace all facia and flashing.
Layers would be:
Torch down cap
Underlayment
OSB board (for potentially adding solar in the future)
4-6inch of ridged foam board
Old tar
1.5in T&G
Advantages would be:
No major dust/debri in living space since there is vaulted ceiling with exposed beams
Reduced labor and removal fees
Thoughts?