Fan-assisted hydronic radiators vs. staple-up

Hello. Remodel situation…
I am looking for some opinions on the pros/cons of going with fan assisted hydronic radiators in a 1300 sq/ft 1st floor (which has a shed roof with high side ceiling at 16ft).
We have existing top nailed oak that we are trying to preserve.
We were looking at non fan assist in basement, but are having 2nd thoughts with their higher (180F supply side needs).
I’d prefer to keep the supply side water temp <150F. We can get to the 1st floor joist bays easily now, we can also easily route any wall supply to main floor. The overall building envelope is “pretty” tight. Basically we are struggling with the boiler efficiency loss of going staple, the potential shock to the floors (we had prior experience when turning up supply side temp during very cold spells and floors experiencing some cracking), and the added cost to do multi-zone with staple up. Thoughts? Thanks.
GBA Detail Library
A collection of one thousand construction details organized by climate and house part
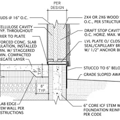
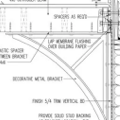
Replies
Any type of emitter will put out some heat at low water temperatures, and more at higher temperatures. That includes all the options: floors, a ceilings, panel radiators, baseboard radiators, or fan convectors. If you want to use a lower water temperature than it is rated for, you will get less heat, but it will still work.
The drop in heat output using, for example, 130 F water vs. 180 F water, will be different for different general categories of emitters. The output from baseboard radiator will drop more than the output from a fan convector, because the baseboard radiator relies on natural convection, and the airflow drops as well as the temperature that the air gets heated to, whereas in a fan convector only one of those factors drops. But that drop in output just means you need more of them--it does not mean you can't supply the heat you need.
If you go with fan convectors, I personally would insist on "ECM" fans for low electric power consumption, and ease of controlling speed without losing efficiency (low speed is nice because it's quiet, as well as saving fan energy). There are three manufacturers of ECM fan convectors I know of. Jaga makes very expensive and very nice ones. Toyotomi units are more reasonably priced. They don't have as many high end design looks avaialble, and they don't have the cooling capability that some Jaga units have. Chiltrix has some very reasonably priced units made for heating and cooling.
The biggest challenge with all of this may be getting the design right--figuring out how much heat output you need is the first step, but then figuring out what heat output you get with the water temperature you want to use, and what flow rate you need for that, etc.
Eric,
Although you frame your question as a "boiler efficiency" issue, I don't think that boiler efficiency has much (or anything) to do with your question.
Step one: You need to perform a heat loss calculation to learn your heating load.
Step two: You need to determine if your boiler rating can handle your heating load. (In almost all cases, it can. Most residential boilers are wildly oversized for the load.)
Step three: You need to design a distribution system based on your preferred water temperature. You've stated that your maximum desired water temperature is 150 degrees; once you know that, you can design a system that delivers enough heat for your design heat load.
If your floor area is too small for a system that uses 150 degree water -- because your heating load exceeds the output of such a distribution system -- you might need to consider installing some fin-tube radiation, panel radiators, or fan-coil units. Any or all of the above can work. If you simply need to decide which of these distribution methods you want, the decision often comes down to budget and personal preferences.
One last point: If you're having trouble delivering the needed heat with a staple-up system, that may be a sign of a bad building envelope. Instead of adding more fan-coil units, it might make more sense to invest in some air sealing work or additional insulation or storm windows. These measures will lower your design heating load.
The key factor for radiant floors is the heat load per square foot of radiant floor, and the water temp required to emit that much heat given the radiant floor method. Even the thinnest sheet metal heat spreaders do a lot for improving the rate of heat exchange out of the PEX and into the floor compared to a simple contact staple up. Extruded heat spreaders are usually even better. By delivering the heat more uniformly to the wood and at a lower temp, the issues with the wood floors warping/cracking from being heated unevenly subside. If it can be heated adequately with suspended tube the heat distribution on the wood is even MORE even, but the water temp requirements are usually much higher.
But without a heat load calc you are shooting in the dark as to whether it'll work at all, let alone with <150f water for the heat load at 99th percentile outdoor temperature bin.
Fan coils or radiators can operate across a wide range of temperatures. Just because the heat rate is specified at 180F doesn't mean you can't design it to deliver enough heat with 120F water. But to do that requires knowing the actual heat load. As a rule of thumb (as opposed to looking it up in the engineering tables for the specific product) a fan coil or radiator will deliver roughly half it's 180F rating when operated at 135F, and a third of it's 180F spec when using 120F water. But fan coils are not exactly linear with temp, and the water flow rate is also a secondary factor. Here's a short-sheet output spec for a popular inexpensive fin-tube baseboard product:
http://www.slantfin.com/images/stories/Technical-Literature/ratings_fineline30_r.pdf
So, whatever you install in the basement can run at almost any water temperature, if you have enough heat emitter so that it can cover the load at that temperature. But if you don't know the heat load, there's no telling how much heat emitter is needed for the water temps you want to run.
For condensing natural gas burners you won't get condensing efficiency unless the water entering the heat exchanger is under 125F. As a rule of thumb, designing the radiation to be able to deliver the 99% heat load at an average water temp of 140F (say, 145F out, 135F back) can deliver very good efficiency, as long as the water temp is controlled with via "outdoor reset", where the water temp delivered varies with outdoor temp, to deliver the lowest water temp that covers the load with the existing radiation.
Low temp convecting panel radiators are much more comfortable than fin-tube convectors, since a larger fraction of the heat is delivered via direct radiation. It's more expensive than fin tube convectors, but it's cheaper than radiant floors, and easier to design with.
If you are cutting up the house into multiple zones there are plenty of design issues to resolve to make sure you don't short-cycle the boiler into low efficiency and high maintenance. In my neighborhood a tight code-min 1300' addition/remodel would have a design heat load under 15,000 BTU/hr which is the minimum of output of many small modulating condensing boilers, and to not short-cycle the boiler all season often requires more radiation than it takes to heat the place. This is also an issue with basement zones, which typically have very low loads. Assuming it's already installed, what model/size your boiler?
These are really only the introductory paragraphs for hydronic heating 101. Unless you're going to take the course you may be better off hiring an energy nerd to run the heat load numbers, and paying a hydronic heating designer (= not just a plumber with some heating experience) specify the heat emitters & pumps, etc. But it's good to have a handle on the napkin-math version of the system design already sketched out in order to have meaningful conversations about the compromises that will need to be made.
You probably do not require Fan assisted stuff as others have already stated . You do however Need to perform a room by room heat loss and a survey of the installed radiation , whatever that radiation may be . Dana pointed out something very important also , Even if your plumber is a licensed professional does not necessarily mean he is capable .
Take a look at these products that operate with low water temps and wont break the bank .
http://smithsenvironmental.com/wp-content/uploads/Heating-Edge-2-Literature.pdf
http://smithsenvironmental.com/wp-content/uploads/Silent-Fin-Heating-Edge-Literature.pdf
http://www.emersonswan.com/ckfinder/userfiles/files/Decoro%20Design%20Radiators%20Literature.pdf
I offer the following as a warning . Do not attempt to use the 4 GPM output numbers . It is almost impossible to guarantee that flow rate at an average water temp based on the fact that damn near any boiler will reach high limit and degrade temp below AWT before firing is enabled again . Also , using 300xs more water and the power associated with it for a 5.7% gain in output is crazy .
Thanks to everyone who replied. This is excellent information.
I should have posted my heat loss calcs at the top of the post. After digesting everything I have decided to go a completely different direction. The plan is to go with mini-splits throughout as a means to fine tune the zoning. The house has 5 physical zones. When looking at the cost of the staple up OR warmboard plus the cost to build out a multi zone panel, plus the challenges of dialing in the water temp to maintain efficiency... the math on cost and added complexity just didn't make sense to me.
I decided to shift the extra expense to tightening the building envelope and adding exterior insulation. Another factor is that for 2 of the 5 zones we needed AC, so we were already invested in getting a heat pump build out.
Again, thanks for the thoughtful and detailed replies. I find this community extremely valuable.