Leveling a Basement Floor

Looking for advice. Had 3 concrete contractors give me 3 different solutions.
I need to level the (1958, Maryland) 700 sq/ft floor after filling in the chasms left from the plumbing rough-in. The perimeter gap is for a french drain and will have dimple board. Its not feasible to fill gaps with regular concrete and use self-leveler concrete because of the large number of bags I would need $$$. Existing slab is 4”.
The general consensus was to pour 3” of 3-4000 PSI concrete over the entire floor. Some wanted to fill the gaps with gravel first so the entire new pour was a consistent 3”. Others said to pour the entire thing without adding gravel to the gap areas. One said he would drill rebar dowels into the sides of the gaps so that it was tied to the new pour.
I will eventually cover the entire concrete floor with LVP flooring and make this a living area. I have enough room height-wise to pour 3” and still have 7+ feet.
I do not want to use gypcrete or dig up the rest of the floor. I don’t think the lally columns are on footers. Thanks.
Plastic no plastic? – PSI? gravel in gaps first or no gravel? – rebar dowels? mesh wire anywhere? – concrete conditioner first or no – 3” height?
Thanks – Jacob
GBA Detail Library
A collection of one thousand construction details organized by climate and house part
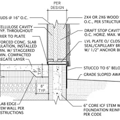
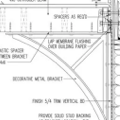
Replies
With how much you already have pulled out, I would really consider busting the rest out and starting fresh. A lot of the hard work is done with so much perimeter available to break what is left. This will allow you to put down well compacted base, sub slab insulation, and a proper vapor barrier. The difference between a ceiling at 7' 2" and 7' 5" is big. You may be able to dig things down even further to gain headroom depending on the footer setup.
I think there is a high likelihood of cracking as the areas over old concrete transition to the new open spaces.
You can check for footers under the columns by drilling a 6" hole right next to the column. New footers can be installed if needed.
I drilled and unfortunately my drill sank into earth once it went past the 4". Very frustrating. The single reason I'm not looking to break everything up is wife is at my throat to finish the house. She's actually upstairs sharpening the knives as I type. Pouring over everything is quicker than supporting the triple 2x8 carrying beams while I pour new footers and wait for them to cure. I certainly agree its best practice though. Thank you for the comment Matt.
I've seen dug down basements where they cut around the columns for something like 2'x2'. They end up as raised section of floor in that situation. Yours could be flush and confine any issues to a small section. I have no experience in dealing with columns that lack footings and the risks they might present.
Just tell your wife that her future 6'6" friend to replace you will appreciate the extra ceiling height. Joking aside, DIY work involves more factors than just good principled construction and you need to carefully weigh all variables.
I'm with Matt on this. Cut around the columns footings and pull everything else out. Fixing this will be more work than the extra bit of demo.
Whichever way you go, one important item is to install a vapor barrier bellow your new slab. This is much easier if you take the rest of the bits out, but possible as is.
In colder climate including even as little as 3/4" of rigid under the slab can make a big comfort difference.
PS. Those columns should have footings (2x2x1 to 3x3x1), the should not just sit on the slab. Since it doesn't sound like they are there, you need to fix it. Much easier now then later with a finished basement.
I don't see any point in adding height. Either fill it flush with the existing floor or take it all out.
I don't understand this comment: "Its not feasible to fill gaps with regular concrete and use self-leveler concrete because of the large number of bags I would need $$$." The least concrete is to fill it flush. Either way the floor is going to need to be leveled.
To put a quarter inch layer of self-leveling concrete over 700 square feet requires 14.5 cubic feet or 29 50-lb bags. They're about $30 at Home Depot near me, so figure about $900. They rent a mixer that can do 300+ lbs per batch so that's only five batches.
The key to this kind of work is having enough labor. It's tough to do by yourself because you're fighting the clock as the concrete hardens. This is especially true with the self-leveling concrete as it sets up very quickly. What you want is 4-5 guys who can load, mix, pour and spread a batch in about five minutes, do the whole job in about half an hour.
Gosh, reading all your suggestions and picturing my wife’s new 6'6” BF are getting me motivated.
What about this plan?
Cut 18-24” perimeter around lally columns and leave this, remove all other concrete, lay 1” of XPS foam and tape, lay vapor barrier (6, 10, 15 mil?), then 6x6” wire mesh mat, then 4-5” of concrete at 3500 PSI.
Thoughts on any of this? Any gravel between soil and foam?
Also, there are differences of over 1.5” which is why I didn’t want to use self-level concrete.
Thanks everyone.
Only note is to try to get EPS foam instead of XPS. XPS has a very high global warming impact.
Also despite all the marketing saying otherwise, EPS performs better in the ground.
With old concrete removed compact the exposed ground. Likely going to have to compact in extra material to help even things out: can't say what material would be best; "gravel" is not a good idea (only compactable material).
If the current slab is off by 1.5" then there's no saving it, rip it out. If you're taking out the whole slab I would dig down as far as the footings allow, the extra headroom in the basement is well worth it. Concrete is expensive compared to crushed stone, if you put down a layer of crushed stone and level it out you'll use less concrete.
You may not need foam insulation under the floor. I'm near you in DC, I just did a Manual J and it came back cooling dominated. So the basement floor contributes more to cooling in the summer than it costs in the winter in heat. If you decide to go with foam the surface below it has to be flat or you'll have air pockets that will weaken the concrete, which is another reason to go with crushed stone.
For a basement slab 3"-4" is fine.
With regard to floor insulation, the primary reason to insulate, in my opinion, is to eliminate the floor as a condensation surface.
I have an uninsulated slab in the basement, shop type space, and just moved a pile of drop cloths and noticed the floor in that area has a distinct musty smell. Air permeable floor coverings allow the surface of the slab to remain cool while moist warmer air can condense on the surface of the slab. Even with vinyl down, there is some risk of this under area rugs.
Thanks all for the answers and feedback. I'm going to HD this weekend to rent the Hilti AVR2000. The rest of the floor is coming up (minus 18" around the lallys unless I can confirm there are footers). If the lallys don't have them, I take some solace knowing the home has withstood 75 years without them already and I'm not adding a lot of weight upstairs.
DCContrarian, thanks for the Manual J. information. I'm along HWY 495, so very close to DC climate. I already messaged the concrete contractor to modify the bid. BTW, the existing floors bottom is already at the top of the footer, so I don't think I can dig out any additional inches of dirt unless the top of the concrete floor can meet the top of the homes footer.
If you have a nice way to hide the top the of footings, you can drop the new slab beside it. This type of micro benching is common when looking at an easy way to add a couple of inches of height without underpinning.
Rigid insulation bellow the slab is more about thermal comfort than energy use. Even in my colder climate (zone 5), unless it is a heated slab, it doesn't effect heat load much.
In most cases you can also skip the mesh. If you have decent soil, unlike driveways, basement slabs don't move enough to cause issues. Whether you install it or not, you slab will eventually crack.
Luckily, the area around the columns will be covered in LVP, so the joint being unsightly isn't an issue. I wasn't able to google a description of micro benching....
My soil is very heavy clay. Interestingly enough, the old concrete floor never cracked and didn't have rebar or mesh installed when it was placed in 58'. Hopefully the new concrete will fare good too.
The gravel comments were a bit confusing. I thought it would be good to have non-compactible gravel to protect against sub-slab capillary action. But another person commented to get gravel that can be compacted, which I took as gravel with fines (not washed). Perhaps the vapor barrier is the heavy lifter here?