Foam Insulation Option with Internal Poly Vapor Barrier?

My existing home has 2×4 exterior walls with a polyethylene sheet installed in front of the studs and behind the drywall. The walls are insulated with faced batt insulation The exterior sheathing is brown fiberboard. House was built in 1977.
I searched this site, but can’t find any acceptable recommendations for insulating with exterior foam panels. I’ve read all the articles about the bad things that can happen when moisture is sealed between an internal and external barrier?
Are there any options to add external insulation? Am I just out if luck?
Thanks,
-Chris
GBA Detail Library
A collection of one thousand construction details organized by climate and house part
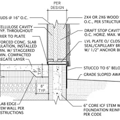
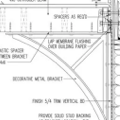
Replies
I should have also added that I live in Maryland.
Chris,
Many energy experts have worried whether it's a good idea to install exterior foam on a house with interior polyethylene. Although it would be better if the poly wasn't there, the fact is that tens of thousands of Canadian homes with interior poly have been retrofitted with exterior rigid foam, and there haven't been any reports of widespread problems. According to building scientist John Straube, all indications show that these retrofits are "not so risky as most people think. These homes will probably be fine."
That said, the installation of exterior foam is not advised on any home that has suffered wet-wall problems like leaking windows, condensation in stud cavities, or mold. If you plan to install exterior foam during a siding replacement job, keep an eye out for any signs of moisture problems when stripping the old siding from the walls. Investigate any water stains on housewrap or sheathing to determine whether the existing flashing was adequate.
If there is any sheathing rot, determine the cause -- the most common cause is a flashing problem, but condensation of interior moisture is not impossible -- and correct the problem if possible. If you are unsure of the source of the moisture, hire a home performance contractor to help you solve the mystery.
If your sheathing is dry and sound, I don't think you need to worry about adding exterior foam. Adding a rainscreen gap will certainly go a long way toward avoiding future moisture problems. Of course, it's important to be meticulous with your details when you are installing your new WRB and window flashing. It's also important to keep your interior relative humidity within reasonable levels during the winter. Never use a humidifier.
To summarize, here are four caveats:
1. Be sure that your foam is thick enough to keep the wall sheathing above the dew point in winter. Read more on this topic here: Calculating the Minimum Thickness of Rigid Foam Sheathing.
2. When the siding is being removed, inspect the existing sheathing carefully for any signs of water intrusion, and correct any flashing or housewrap problems.
3. Install rainscreen strapping so that there is a ventilated gap between the new exterior foam and the siding.
4. Keep your interior humidity under control during the winter; if the interior humidity gets too high, operate your ventilation fan more frequently.
Without removing the interior side air barrier you still have a couple of pretty good options:
Type II (1.5lb nominal density) EPS runs R4.2/inch of thickness, and still provides 1-perm of drying capacity at 3" (R12.6), and about 1.5 perms @ 2" (R8.4). On the outside of 2x4 framing with R11 batts a 2" layer of would roughly double the thermal performance of the wall assembly. With R13 batts 3" would MORE than double the thermal performance.
Rigid rock wool panels are about R4/inch of thickness, and are more expensive per unit R than EPS, but are HIGHLY vapor permeable, completely fireproof, and less susceptible to insect damage. (Some species of ants seem to love nesting in EPS, though that's less of a problem if you can keep the wood dry.)
With a rainscreened siding adding 1-3" of either one of those solutions is just fine in almost any climate, including MD. The most important thing to get right is the window & door flashing and WRB details when retrofitting exterior panels.
With the interior poly it's important not to over- air-condition the place during humid weather. Summertime dew points sometimes hit the mid to high 70s in MD, and under those conditions if you chill out the interior to 72F you'll end up with liquid condensation on the vapor barrier inside the cavity, potentially puddling & saturating the bottom plate of the studs. Air tightness at the sheathing/housewrap layers helps. If it's already air tight 1-1.5 perm EPS would also limit rates of moisture accumulation in the stud bays during the high humidity days. But in general holding the line at 78F rather than some lower temp will be a much safer bet during the sticky-icky dog-days of summer. As long as you can keep the relative humidity in the house under 50% most people find 78F, even 80F pretty tolerable. (This is an issue already, an artifact of the vapor barrier, and not aggravated by adding insulating sheathing.)