Foil or felt faced polyiso

Is there any major difference between foil faced and felt faced polyiso in normal applications (wall sheathing for above-grade walls)? Is the foil facing more stable with respect to R value over time?
I ask because the reclaimed insulation guys have felt faced priced lower than foil faced. In my application, the foil facing won’t be facing an air space so it won’t help with IR radiation.
Bill
GBA Detail Library
A collection of one thousand construction details organized by climate and house part
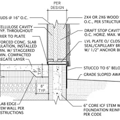
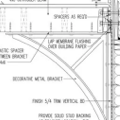
Replies
Also consider the permeability to moisture. In most cases, I'd prefer some permeability to the nearly none of foil.
Foil faced goods are usually 1-1.5 lbs per cubic foot density and deliver about R6/inch performance or slightly higher. Fiber faced polyiso is usually 2lb density and about R5.6-R5.8/inch.
With current products being primarily blown with pentane the performance should pretty stable over time, since pentane is a small enough molecule to escape quickly enough to not really be a factor in an LTTR test. Some of the CFHC blown stuff from the early 1980s is pretty stable too (at a somewhat higher R/inch), but some of the '70-'80s goods loses quite a bit of performance over time. Which magic-mix of vintage blowing agents really stood the test of time and which didn't aren't really very consequential at this point, since they are all contraband under the Montreal protocol, and have a high global warming potential problem too (unlike pentane.)
Fully depleted at an absolute worst-case you can assume at least R4.5/inch, but in reality it'll usually be R5.5/inch or better even after 40-50 years. From a dew point control at the sheathing design perspective it's generally safe to assume R5/inch, but if you're super-conservative and designing to the minimum assume R4.5/inch. That would be true for 1lb density foil faced goods too.
That sounds like there’s not a lot of practical difference between foil and felt facings for wall sheathing applications.
I’m thinking about using 2” of polyiso with an exterior layer of 1” of XPS for better cold weather performance here in zone 5.
Bill
Why the exterior 2" layer of XPS? Foil faced 1" polyiso will be easier to air seal, and outperform it more than 90% of the time.
At 1" Type-II EPS would have the same performance as 1" XPS at full depletion of the HFC blowing agents used to make the XPS, and would have the same monotonically rising performance with falling temperature characteristics.
An exterior layer of 2” polyiso over the exterior wall, with 1” XPS over that with seams staggered — 3” total. The idea would be for the XPS to keep the polyiso warm enough to avoid any serious cold weather derating of the polyiso. I had not thought to look into EPS, do you know approximately how many years XPS must age before EPS approaches its cold weather performance?
Btw, I’ve seen you post very detailed performance metrics for various forms of rigid insulation before. Do you have, or can you link to, a chart or table showing the performance of especially polyiso over temperature? I have actually seriously considered setting up an environmental chamber to measure this (in which case I would share the results), but it’s a lot of time to construct the measuring setup and a lot of time to run the tests.
Bill
At 40 years most XPS blown with CFHCs hit R4.5/inch (per testing by EPS vendors). It's not clear if HFC134A blown foam will last that long.
The easiest quick reference for polyiso derating can be found in Figure 2 of this document:
http://msdssearch.dow.com/PublishedLiteratureDOWCOM/dh_09b4/0901b803809b49c0.pdf?filepath=styrofoam/pdfs/noreg/179-00263.pdf&fromPage=GetDoc
Note that the polyiso curve in the sample has to be some of the crummiest 2lb roofing polyiso out there- it only tests at R5.2/inch @ 75F mean temperature through the foam, but even when the mean temp through the foam is 0F it's still delivering R4.3/inch. It's probably legit to add R0.3 or even R0.5 to the that curve for a more representatitive sample, or you can just take it as your worst-case.
At depletion XPS would hew pretty closely to the gray "Mineral Wool Batt" curve in that graphic.
With ~3" of roofing iso on the exterior of a 2x4/R15 rock-wool wall, when it's 0F outside 68F indoors the mean temp through the foam layer is going to be about 17F, and the mean temp through that outer inch is going to be about 3-4F. Replacing that outer inch with fully-depleted XPS it only adds about R1 at that temperature, R2 for fresh XPS.
But the average mid-winter outdoor temperature in most zone 5 locations is north of 20F. At 20F outdoors, 68F indoors the mean temp through 3" of foam would be about 32F, a temperature at which the difference in performance of fully depleted XPS and worlds-crummiest polyiso would be would be less than R0.5, and replacing the outer inch with depleted XPS would be only adding ~R0.2, and even fresh XPS would be adding less than R1. That's during mid-winter. During most of the shoulder seasons even the crummy polyiso tested would outperform depleted XPS.
If it's going on the exterior of 2x6/R23 the numbers move a bit, but from a total energy use point of view it's hardly worth thinking about or spending extra money on. Lower density foil faced polyiso will do better than the goods in that chart, if not quite as good as Dow Thermax, seen in Figure 1 on this bit o' marketing fluff:
http://msdssearch.dow.com/PublishedLiteratureDOWCOM/dh_098a/0901b8038098a7e2.pdf?filepath=styrofoam/pdfs/noreg/179-00379.pdf&fromPage=GetDoc
What tapes are you using to seal the felt faced? My local recyclers only have felt as well.
Im leaning towards two 1” layers staggered.
I’ve been using foil faced wherever I need to tape it. I’m only using felt faced in a few cut and cobble spots where the air seal is at the edges and done with spray foam so taping isn’t necessary. There are a lot of reports of tapes peeling off and failing to stay stuck on the felt faced polyiso. If you go with felt faced insulation, it’s probably worth testing your tapes to make sure they stick before you buy a bunch for the project.
Bill