Protecting Foundation EPS Foam: Acrylic or Cementitious Finish

I know this question has been beat pretty good over the years, but I’m having a hard time pulling the trigger on the best product for protecting foundation EPS.
None of the articles on here or elsewhere provide what I would consider ‘advice’ on the matter so much as a list of options (a form of advise perhaps). I know, I know… no perfect solution.
I’ve narrowed it to an acrylic product—namely Styro industries Tuff II,
and a polymer modified, fiberglass reinforced, cementitious coating—namely Silpro FSB.
I can’t decipher what the practical differences would be between these finishes.
Reading the literature of the FSB makes it sound like a few more steps (actually involving a few of their other products as scratch coats). The Tuff II seems pretty straightforward and the use of the stick on mesh seems both simple and robust.
If Tuff II is as robust, that’s my lean. But what I don’t want is a coating that someone’s gonna stub their toe on and cause a hole.
Anyone have experience with these products, or generally with acrylic vs cementitious surface finishes?
GBA Detail Library
A collection of one thousand construction details organized by climate and house part
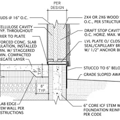
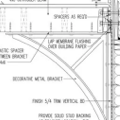
Replies
Tyler,
The exterior of my first house was synthetic stucco over EPS. The synthetic stucco was pretty durable. The only real damage we had was when the electric company's trencher bumped into a corner while trying to lay cable. On the plus side, the repair was pretty straightforward.
I have 4” of EPS on the outside of my stem wall/slab edge with a custom bent sheet metal cap. I struggled with the same problem as you and being very cheap (thrifty?) and seeing the high price of specialized composites I finally settled on a very inexpensive approach. Over the foam I troweled a cementatious coating that is the first coat product for the “Dri-Vit” system designed to go over EPS. It is very adhesive and pretty durable depending on how thick it is applied. The only problem that arose is at the seams of the EPS that were spray foamed then taped I got enough expansion and contraction from temperature cycling to develop cracks at every joint. The fix was to make plunge cuts with an oscillating cutter (IE- Fien) and then fill the kerf with flexible urethane sealer. I don’t think many people realize the large amount of expansion and contraction that occurs with EPS foam.
Tyler,
FWIW, I have 6" of EPS foam cladding my house and due to the dreaded local flickers and woodpeckers, I needed a tougher base coat than Dri-Vit's standard issue. I went with Parex 121 Dri Hi which has about double the impact resistance. The same weight of mesh was used although one alternative for slowing down the birds would be using a heavier mesh. While the flickers and woodpeckers have been held at bay, a "folding" side mirror proved a match. I have dropped shovel handles against the house before with no ill effect, so judge accordingly.
Mind you the foam directly under the coating is the 1lb foam used by the stucco crew over my much denser EPS main layer. Knock on wood, I have only suffered one field area crack in the whole house. First season cracks where the stucco meets the windows were expected due to thermal cycling and quite easily taken care of with caulk. It has taken five years for those to start showing again, which probably reflects poorly on my caulk selection. We have regular temp sweeps of 30-40 degrees even in winter. The sun load of course adds to that. So far the expansion of the underlying foam has not proven to be an issue.
Freeze thaw cycling and moisture load is something to consider when making your choice. Even though I live in a very dry area, the ground can keep a pretty big wet load on your finish, especially the fall and spring. I chose to encapsulate the entire foundation foam with Grace shield and then protect that with 1/2" steam shower rated Hardi panels I hung from a convenient flashing detail that occurred at the belt line. Fussy to detail, but the end result looks like a standard foundation and so far so good. I did detail the bottom edges that go a few inches below grade with a washed stone pocket that drains to the bigger stone filled drain system I have for my gutterless house. The thinking was to prevent standing water being absorbed by the Hardi board and causing freeze thaw break down. Seems to be working.
If you are not backfilled yet, do consider how far down below grade you will be going and what form of critters or insects will be rooting around below that.
Roger, your installation seems to maybe meet a lot of the challenges I'm facing, at grade. Do you have any photos you could share? Can you tell me more about the steam shower rated Hardie? We also are planning on extending our stone along the foundation up to grade and using underground gutters/French drain (no gutters on the eaves). Thanks
I have had good luck using fiberglass infused parge products over ICF blocks, such as Parge ALL. The key is buying rolls of fiberglass mesh and embedding this into the parge as you apply it. The fiberglass can be acquired through your lumber yard if they sell ICF's. It makes for a very strong top coat. I have had zero issues on houses in which we have done this. My test is the weed wacker test. If it can survive a weed wacker that is pretty good.
I used Tuff II on my house and after ten years it looks great. It's over XPS with which I was able to sculpt bullnose corners. In areas that seemed vulnerable I added another layer of mesh and mud.
Do you have any idea how thick a layer you ended up with on average?
In the places you didn't do an entire new mesh layer, did you do two coatings of the tuff II?
I used the double layer around windows and especially window sills. I'd guess it's 1/8" thick. The rest is single mesh single coat. Mine suffered no damage, but it's still plastic on foam. but i'ts easily repaired. Use spray foam to build up missing foam, shape and reapply the Tuff II mesh and goop.
Interesting thoughts about rapid drying and workability. I did mine during a mild zone 6 November. I had plenty of open time.
Thanks all for the experience.
I had pulled the trigger on ordering Tuff II before reading, so we'll see how it goes. Sounds like it should be on par with most sorts of coatings.
The foam expansion issue is an interesting one I hadn't given much thought to. I'll scratch my head as to mitigation, but I may just have to come back if cracks develop. I suppose one could butt the foam together with a poly expansion joint from the getgo. Seems like a bit of work though.
Tyler,
I just finished coating my foundation foam retrofit with Tuff II. ~200 LF of coating over faced EPS. Right before coating, I scored and peeled the poly facing off 12" wide, then lightly scratched the foam with a wire brush, shop vacuumed off the loose pieces, sticky mesh and coated. Only working what I could do in the next few hours. The foam and sticky mesh attract dust quickly. I also used 4" galvanized outside corner flashing to make "corner beads" for protection and a crisp finish. As an aside, it also worked great to parge on termite mesh. A detail that took me a while to figure out since all the details I found were for new builds with a termite barrier integrated under the sill plate.
It doesn't have any seasons in service yet, so I can't comment on durability. The material has some elasticity and coupled with a high-quality mesh to add tensile strength, I am expecting good quality service from it. I used Styro's sticky mesh, their specifications are not detailed enough to compare it to other similar mesh products on the market. I suspect its the same or similar to the medium to higher strength stick on meshes out there.
I trowled my finish on with a 12" taping knife, end goal being a smooth trowel finish. A pool trowel with rounded ends instead of sharp ends may have reduced the lines I fought, but I didn't pick one up to try. Spraying on with a texture gun and smoothing with a trowel might ultimately have been easier but wasn't too bad trowel only. I could do about 65 ft, prep to finish one coat in 3 hrs or so. Finish coat in half that time.
Tuff II skins over fast, even faster in direct sun, warm temps and wind, or even light breezes. Its acrylic water base. I finished the south side of the foundation at dusk with a headlamp to combat this. The first coat in full sun ended up pushing ridges out at the foam joints which were hard to scrape and blend out on the finish pass. I didn't have this on any other side of the house.
Work small areas quickly, condition the mix with a little water for easier finishing. A spray bottle with clean water helps blend drier areas with wetter when you get out of sync or the mix is drying out on you. As long as the stuff is wet it finishes beautifully and works easily. Two coats were enough and mandatory for a nice finish/coating thickness. Three probably would have really dialed it in. The coverage was pretty close to 80 SF listed on the container.
Good luck with your project!
Michael