Frankenstein basement retrofit

Hi All,
I created the attached diagram based on the advice offered here (and elsewhere) to achieve a dry, insulated, and radon-free basement – for a home with a rubble foundation built in the late 1800’s.
I’m far from an engineer, but this is what I plan to give to my contractor regarding what him to do. I would be incredibly appreciative to anyone who could point errors in my outline/thinking or anywhere I should provide more detail for my contractor.
Many many thanks,
Becca
GBA Detail Library
A collection of one thousand construction details organized by climate and house part
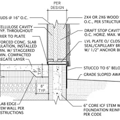
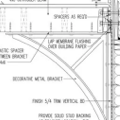
Replies
The 4" of closed cell foam is overkill, and has substantial environmental impact (even if using HFO blown closed cell foam.) There is no reason at all to spec XPS under a 3" slab, and it's even more of an environmental disaster than 2lbs polyurethane. At 2" XPS is only warranteed to R9, and as it's climate damaging HFC blowing agents dissipate out over a handful of decades it will eventually hit R8.4 at full depeletion (Are going to dig it up, test it and file a warranty claim? Didn't think so.) EPS is blown with hydrocarbons, usually variants of pentane, most of which leaves the foam and is recaptured at the factory, not vented to the atmosphere.
The differences aren't even close! There is NO place for XPS as part of a "green building". See:
https://materialspalette.org/wp-content/uploads/2018/08/CSMP-Insulation_090919-01.png
3" Type-II EPS (1.5lbs per cubic foot nominal density) is usually cheaper than 2" XPS, and will still perform at the labeled R12.6 fifty years from now.
Mils aren't the same as millimeters, a 10 mm thick vapor barrier would be a very stiff ~3/8" thick chunk of plastic. A 10 mil vapor barrier would be 0.010" (= 1/100" ) thick.
There appears to be a studwall nudged up against the wall foam(?). In any US climate zone installing the studwall ~2" nominally away from the rubble foundation and installing HFO blown closed cell foam to a thickness that barely touches the stud edges, and insulating the stud bays with R15 batts and no interior side vapor barriers is a moisture safe assembly that beats code minimums, with thermal performance comparable to 4" of HFC blown closed cell foam, at well under half the CO2e foot print.
Dana made good catch on the "10mm" vapor barrier! That would be one CENTIMETER thick, almost half an inch. A "mil" is a THOUSANDTH of an inch, so about 0.0254mm, so a "10 mil" thick material is about 0.25 mm thick. A VERY big difference!
I'd use all one type of spray foam. Since you really need closed cell spray foam against the foundation wall, I'd use closed cell spray foam on the rim joist too. Why? It'll be cheaper for the contractor to do the entire job at once, with one setup and one type of foam. Open cell doesn't really offer any advantages here, at the thickness you show it's not really breathable.
There is no reason to use BOTH EPS and XPS in the floor. Use all one or the other. I'd try to find some reclaimed material here if you can, since it will be both cheaper AND greener, and reclaimed materials are a perfect fit for hidden places like under a slab.
I'd use 5/8" drywall on the ceiling. 5/8" drywall will give a flatter, stronger ceiling, and better sound isolation for very minimal increase in cost. I use 5/8" drywall almost everywhere but that's just me, 1/2" will work in this application too.
Bill
Thanks so much for the quick feedback. I'll update my diagram accordingly. One thing to better understand first:
Dana, when you say "no interior side vapor barriers" are you referring to the dimple mat? And do I read you correctly that the dimple mat is not necessary to route the moisture down the wall because the closed-cell spray foam will do so by itself?
Many thanks!!
Becca
>"... when you say "no interior side vapor barriers" are you referring to the dimple mat? "
No, I'm referring to avoiding vapor barriers between fiber insulation & wallboard, a common (but not always correct) feature of above-grade fiber insulated studwalls. Below grade studwalls need to dry toward the indoors, and a vapor barrier under the wallboard would block that drying path.
>"...do I read you correctly that the dimple mat is not necessary to route the moisture down the wall because the closed-cell spray foam will do so by itself?"
Dimple mats usually aren't essential unless there is a strong history of bulk water coming through the wall. Even 1" of 2lb closed cell polyurethane foam is waterproof from a liquid water point of view, and will seal leaks in the foundtion. The stone/masonry/mortar materials of a rubble foundation tolerates moisture quite well, and doesn't necessarily need to drain. But a dimple mat won't hurt.
Your assembly needs a fire block to separate the void behind the stud wall from the floor framing cavities. To my knowledge no spray foam is a code approved fire block(except the little cans made for small penetrations). See the attached detail.