Going in Circles with PSF

We are in Marine Zone 4
We are getting conflicting information on how to insulate a 2×10 -16″OC Cathedral Ceiling.
This what we’ve been told so far.
R12 of either ccPSF or ocPSF is all that is need. It is a waste of money to do anything more than what he code (R28) requires.
The underlay on our roof is GAF Deck Armor. Peel and stick Winter Guard should have been used instead of Deck Armor.
Don’t use ocPSF because:
– it is a sponge and does not dry
– if the leak is small or intermittent it will take years for the water to pass through it and possibly never if it is sprayed with vapor retarder.
Don’t use ccPSF because:
– water will not drain through it.
– it will not allow the trusses to expand/contract which may cause issue with the connections.
Use ccPSF because:
– it holds the water closer to the surface so it will dry.
Use ocPSF because:
– it costs 30% less and does a better job than ccPSF.
Use mineral wool instead of ocPSF.
GBA Detail Library
A collection of one thousand construction details organized by climate and house part
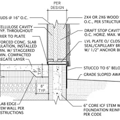
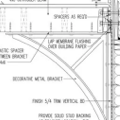
Replies
I'm guessing this is an UNvented cathedral ceiling. That rules out mineral wool.
I've never liked the argument against spray foam because "you won't see leaks". You don't always see leaks anyway, and I've never like the idea of building something a certain way because we expect it to fail and want to see the failure. Do a good job of roofing so that you shouldn't have leaks to begin with in my opinion.
You need code minimum R value, and that's not R12 in a roof. if your code is R28, that's the minimum you put, no exceptions.
You can do a mix of closed cell and open cell, or put enough closed cell for vapor control and then fluffy stuff under that to fill the rest of the rafter bays. It's best not to have any air space where air can circulate within the assembly.
I would not use only open cell spray foam here. You want at least enough closed cell spray foam against the sheathing to prevent moisture issues.
I can't comment on the deck armor vs winter guard.
Bill
Hi Bill
Thank You for the reply.
Ridge and soffit venting can be added but we are being pointed toward PSF due to the ease of application.
We already had a leak on the new roof within a month due to workmanship. The best roofing companies will always give jobs to people that are learning. Wasn't much only 2 cups of water over 24hrs during a storm and it was easy to hear the water dripping with no finishing on the inside. I also have friends with 4 year old PSF sprayed on sheathing with a suspected leak due to the Gyproc screws showing rust. They've been told to leave it alone until summer.
The discussion about not spending more to exceed the R28 code came about when we were going to fill the space between the 2x10s with foam (R54).
John
John,
I would opt for the open cell foam in your case. Open cell is much more forgiving as it can be removed more easily if you do run into problems later. It tends to be more benign from an environmental perspective too although that is changing. I'll echo what Bill said about the mineral wool. No fluffy stuff in an unvented roof! (People get away with this... but your ceiling air barrier must be 100% bomber and no showers/boiling of water is allowed.) :-)
The real risks with open cell foam in a ceiling is that it may not prevent warm moist air from reaching the underside of your sheathing. This shouldn't be a big concern however in your mild climate. Also, at 9.5" depth, the oc foam will keep out most of the warm, wet interior air. Consider conditioning the attic for added safety. If your climate is so mild that no AC is needed then I would consider monitoring the attic for moisture and have a plan to act if RH get high.
Hi Rick
Thanks you for the reply.
The discussions yesterday is to provide venting and not use PSF.
The detail I've shown would be for the roof between the pony walls that are 15' part.
Outside of the pony walls the ceiling would be insulated with cellulose.
The XPS or EPS(foil faced) will allow water to drain down and land on the cellulose if there was a water leak.
John
I would use 1" foil-faced polyiso for your upper layer of rigid insulation, and EPS for the lower layer. The reason for the foil faced polyiso is that the foil adds a radiant barrier facing the vent space, and it's a more durable material than EPS or XPS.
I'd use EPS for the lower layer and I'd make sure it's unfaced so that it will have some vapor permeance. You don't want a double vapor barrier. I would NOT use XPS here, either, not just because it's the least green of the three rigid foams, but also because it's not as vapor open as EPS is.
Bill
Hi Bill
Polyiso was not the first choice for the top layer due to loss in temperatures below 50F which we are (for how long?) below 6 months of the year.
We would prefer to use EPS over XPS
Cork is a fire barrier and does not compress as easily so we'd prefer to use it on the bottom layer but finding it might be difficult.
John
The polyiso R value loss in cold temperatures is overrated. I used to think similar thoughts to you, and was convinced by another GBA member (Dana Dorsett) that it's not as much of an issue as some think. He seems to be on a bit of a leave as of late, or else he'd probably be on here telling you the same thing :-) For the shoulder months, polyiso is BETTER than the others, so you come out ahead overall. Even with R value de-rating, polyiso isn't any worse than XPS, and a little better than EPS, since you typically derate polyiso from around R6 per inch to R5 per inch, and that is the same as the labeled R value rating of XPS (which will degrade over time to about the same as EPS), and better than the typical R4.2 per inch for EPS.
I've never heard of cork being used as a fire barrier. Isn't it flammable itself? It doesn't matter in your assembly though, because 5/8" drywall is actually RATED as a fire barrier. There is no need for an additional fire barrier behind the drywall. If you want a more fire-proof assembly, just use a second layer of 5/8" drywall with the seems taped and mudded. Two layers of 5/8" type X drywall gives you a 1 hour fire rating.
Type-II, or one of the higher numbered versions, of EPS will be more physically durable than the Type-I "crumbly" version you often see. This might take care of the compressibility issue you're worried about.
Bill
>"Polyiso was not the first choice for the top layer due to loss in temperatures below 50F which we are (for how long?) below 6 months of the year"
The performance of polyiso PEAKS when the average temp through the polyiso is about 50F, not an outdoor temp of 50F. If it's 70F indoors a 50F average temp through the foam would correspond to 30F outdoors, and it's definitely NOT colder than 50F.
Take a look at Figure 1 in this document:
http://www.owenscorning.com/NetworkShare/EIS/10019949-FOAMULAR-XPS-vs-Polyiso-Tech-Bulletin.pdf
The crazy non-linear line is 2lbs density roofing polyiso. Note that this is thermal conductivity, the opposite of thermal resistance, and it's plotted against the mean temp through the foam, not the cold-side temperature. The lowest conductivity (= highest R) for the polyiso occurs at a mean temp of about +15C (59F), but it's still performing pretty close to it's labeled performance at +10C (50F), but below that it falls off dramatically. The mean temperature at which the foam is required to be tested for labeling purposes is 75F, indicated by the red dashed vertical line.
In R-value (rather than thermal conductivity) it' looks like this:
https://i.imgur.com/a3SvC7H.png
Again, mean temp through the foam, not the cold side temp. The curve for Type II EPS would be comparable to the mineral wool batt (in grey). At a mean temp through the foam of ~+35F the polyiso & EPS would be about the same. (Say 30F on the exterior of the polyiso layer, 40F on the interior side.) And with a long term rated R of only R5.2 (the circles in the middle on each of those curves) it would have to be some of the crummiest roofing foam available on the market. (most are in the R5.6-R5.7 range). Any 1lb density foil faced polyiso would outperform that.
There is no location in zone 4C where it's cold enough to require derating the polyiso. Even at the 99% outside design temps of +20F-30F it's still doing at least as well as EPS, and it's only colder than that 1% of the hours in a year.
A potential revision of your stackup would be an unfaced EPS on the upper foam layer with foil faced polyiso on the underside the assembly can dry just fine through an inch of any density unfaced EPS, and the foil facer on the polyiso is a very effective true vapor barrier keeping interior side moisture drives at bay, and you can just skip the separate vapor retarder layer. The average temp through the polyiso would stay pretty close to it's labeling tested temperature.
In zone 4C if you're going to put LOW-permeance foam on the exterior side of your assembly it needs to be at least 20% of the total R, at which point the interior side vapor permeance doesn't need to be any tighter than standard latex paint on sheet rock or 1" of Type II EPS, no separate vapor retarder required.
Is this an attic or a cathedral ceiling?
Hi
It's a finished attic that is 9' to the bottom of the collar ties.
John
"The polyiso R value loss in cold temperatures is overrated."
Hi Bill
Thank you again.
I wasn't looking at Polyiso from the perspective that it starts with higher R / in.
Choosing a thickness will be interesting as the cold will penetrate through 1/2" Polyiso while only penetrating a proportion of the into 1 1/2" or 2" Polyiso.
John
I wouldn't get too hung up on the "cold penetrating the polyiso". In your entire assembly, you're talking about R value changes of probably less than one unit (R1). It's not enough to make much difference.
I would probably use 3/4" or 1" polyiso just because it's more physically durable, and probably a bit easier to secure in the rafter bays without doing anything special. You certainly won't hurt anything using thicker material though.
Note also Dana's proposal with the polyiso and EPS layers reversed from what I mentioned. This would be easier to air seal. EPS is less durable, so you'd need to be a bit more careful stuffing in your batts. There are always tradeoffs :-)
Bill