Grinder pump energy use
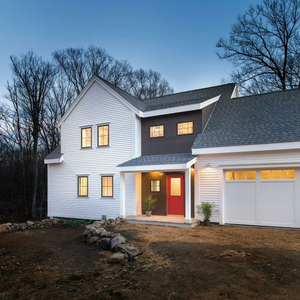
I’m doing an energy model for a new net zero energy Pretty Good House in zone 6A. I’ve done plenty of energy modeling but have a new challenge on this one—there will be a grinder pump for wastewater. I would appreciate some help to make sure I’m accounting for the electrical load properly.
The unit will be a Barnes OGP2022L (https://www.cranepumps.com/downloadables/CATALOGS_OIPMs/BARNES/3B/BE3B-6.PDF)
It is rated for Full Load Amps of 16.5 and Locked Rotor Amps of 53.8. I believe the LRA is only for start-up and can be ignored in my calculations? 240 volts x 16.5A = 3,960 Watts when in use.
It’s a 4-bedroom house with four occupants. I’m assuming 75-100 gallons/day/person, or 300-400 gallons/day total.
There will be a float valve set so the pump moves about 100 gallons at a time., so the pump should only come on a few times per day.
The pressure head is about 5’. On the link above, that indicates the pump will move 30 gallons per minute if pure water. I think I can assume the same for macerated effluent?
At 30 gpm and 300-400 gallons per day, the pump will run 10 to 13 minutes per day. 3,940W x 10/60 x 365 = 240 kWh/yr. 3,940 x 13/60 x 365 = 312 kWh/yr. At our delivered electrical cost of 16.3¢/kWh, that’s about $50/year, which seems reasonable.
Do my assumptions and math make sense?
GBA Detail Library
A collection of one thousand construction details organized by climate and house part
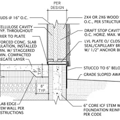
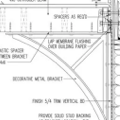
Replies
If that's the approximate total head, then it looks like the pump is way over-sized and will be running at much less than full load.
Meaning it will run at less than 16.5 Amps? Or that we should use a different unit?
Looks like one hell of pump!
Yes Jon is suggesting it might draw less amps. Maybe call the company and ask their opinion on amp draw vs head?
Your math makes sense to me. $50/year is more than reasonable for the problem it is solving.
They way I usually work, I'd mock-up a test with ammeter to know for sure.
Thanks Jamie. I will call the company, good idea. The immediate concern is to make sure we are planning for enough PV to reach net zero annual energy. But double checking the actual draw makes sense too.
Edit to add: I called and they couldn't help me with this question.
Yes to both. And watts will drop much more than amps (because power factor will be low at low loads). I wouldn't want to guess how low. What is the application?
Waste will need to be pumped up 5' to the sewer main.
Into something not pressurized should probably use a small sewage ejector pump.
Jon, my client is the developer of a new subdivision; he sent me the pump he wants to use, along with this note:
"All the houses pump to a low pressure force main sewer that connects to the town system. For a net elevation change our lot is somewhere between flat and about 5' actually uphill of the Manhole where the force main meets the town. The pump will be sitting at about elevation 90' and the discharge into the manhole is about 85'. There are a couple big dips in between. The run is about 1,600' but in this case I don't think it factors in."
I imagine he wants a macerating pump to avoid clogs. This is obviously outside of my expertise, though; if there is a reason to use a sewer ejector pump instead I can recommend it.
Micheal,
I've been down that road. Unless there is something obviously wrong with the pump, use the one the developer specified.
This seems to cover the issues. With your long run creating dynamic head, it might need 25' total head. Compare to the 125' or so that that pump is best for. That being said, I'd probably just guesstimate at $20/year and not spend time with further optimization.
http://www.sspma.org/uploads/8/3/9/2/8392851/sspmasewagepumpsizing.pdf
Deleted
A rough ballpark assuming the effluent is mostly water.
30gpm at 5ft head is 30W hydraulic power.
Say the pump is 50% efficient and the motor is 70%. Works out to around 85W electric.
Would probably take a bit more power to grind things up, my guess is the power consumption would be under 200W.
Akos, thank you for those calculations. I'm a little lost though--it looks like you are ignoring the unit specs and just estimating what this application should require? My goal is to estimate the annual energy consumption of this pump. Do I understand you correctly:
Pushing water up 5' at a rate of 30 gpm will require 30W of power.
Divide 30W by 0.5 for pump efficiency and by 0.7 for motor efficiency, for a total pump power use of 85W.
The grinder might take another 100-115W.
Assuming all of that is correct, it would still run for about 60-80 hours per year. At 200W when running, that's 12 to 16 kWh/yr. That's only $2 to $3 of electricity per year, which seems hard to believe, and an order of magnitude lower than my estimate. But maybe it's accurate, or maybe my math is wrong?
Pretty much.
I took another quick look at the pump and it is capable of almost 150ft of head, at those kinds of lifts and GPM, you do need a big motor, maybe that is why they rate it at 16A. At those lifts and gpm, you are close to 700W hydraulic power (~2000W electric).
I think overall it is hard to say till the pump is in operation or if you can find a place that has that installed and measure. Maybe pumping poop is a lot harder than water.
I've been to places with macerating pumps behind the toilet. It didn't feel or look like a multi kW draw when running.
EDIT: Just saw your longer reply. Pumping along 1500' of pipe will take some extra power. Would be best to do a loss calc on that run and adjust.
Akos, most of the development has been built out and I believe they have similar pumps, but I will check. Thanks for your help!
@JonR #14, that's a great PDF! Thanks for your help.
Regular centrifugal pumps use less power with increased head. Power goes into moving water, gallons per minute. Restricting the flow on the outlet of the pump actually results in reduced energy use. I can’t give you a rule as to how much, but you can get a guess from the pump curves showing horsepower requirements. I would also check that you’ll be operating this pump within the allowable range of its particular pump curve. Running pumps intended for very high heads at very low can sometimes cause problems.
To get closer to the wattage the pump will use, multiply volts * amps * 0.8. The 0.8 is a guess at what your power factor will probably be. It’s very unlikely you’ll be at 1.0 power factor. Jon is correct that the power factor will drop when the pump is operated far from full load. Poor power factor isn’t usually a billable issue for residential customers (commercial customers pay penalties for anything below 0.8 usually), but may result in more light flickering/dimming while the pump is running.
I agree that the pump is probably oversized for the application, but I also agree with Malcolm: using something other than the pump specified by the developer will probably result in finger pointing and project delays.
Bill
It seems to me we would need to add the power required to start the motor to your run numbers.
If we say the pump starts 5 times a day and draws 50 amps for 15 seconds.
240V x 50 A = 12,000 / 480 (1/4 of a minute in an hour) = 25 watt hours per start just to get the machinery up to speed. 25 x 5 times a day x 365 day = 45 kWh a year just to start the equipment before you move the first gallon.
5 times a day is a guess as is 50 amps and 15 seconds feel free to adjust if you have different guesses.
Walt
The motor start current is the locked rotor (LRA) current, but only lasts for a number of cycles with each cycle being 1/60 of a second. Starting current is not going to have any real effect on your energy usage in kWh unless you are starting A LOT (thousands of times a day maybe). An entire year of inrush currents from starting is probably going to cost a few cents or so if that. Not something to worry about.
The LRA number is given primarily for sizing of circuit protection devices (circuit breakers and fuses).
Bill