Hardwood over a slab: Is 6 mil plastic or roofing felt best?

Hardwood over a slab: Is 6 mil plastic or roofing felt best? Or is there a better idea?
All the info I have found says felt, glued down with mastic is best, or 6 mil plastic. Both go under the subfloor plywood.
I have done 6 mil under plywood, 15 years ago. I just wondered if that approach still is relevant.
GBA Detail Library
A collection of one thousand construction details organized by climate and house part
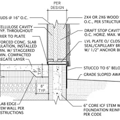
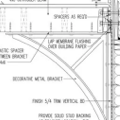
Replies
William,
You may want to read the comments posted on an earlier Q&A thread on the same topic: Wood Floor, Concrete slab, and Moisture.
Fine Homebuilding author (and wood-flooring expert) Charles Peterson recommends 10 mil polyethylene. Here are some more of his tips from his Fine Homebuilding article, "A Wood Floor That Can Survive Anywhere":
There are many ways to build a subfloor. Plywood can be screwed to 2x4 sleepers that have been fastened to the slab on 16-in. centers. Plywood can be scored, glued, and nailed to the concrete, or it can be installed so that it floats over the slab without attachment.
The most cost-effective method, and the one that I and most professional flooring contractors prefer, is the floating-subfloor approach. A floating subfloor is less labor intensive, doesn’t rely on expensive adhesives, and can be integrated with a vapor retarder more seamlessly than other subfloor assemblies.
Always install a class-I vapor retarder
Wood-floor manufacturers recommend that concrete slabs be tested for moisture content before their products are installed. If the moisture content of the slab is too high, the manufacturer specifies the use of a vapor retarder. This suggests that a vapor retarder doesn’t have to be used if the slab has a low moisture content at the time of testing. The problem is that testing represents just a snapshot of the concrete’s moisture level and does not factor in potential moisture levels. A class-I vapor retarder (commonly referred to as a vapor barrier) should always be installed despite a manufacturer’s recommendations about its use.
When you’re installing a wood floor over a concrete slab, the vapor retarder should be placed under the plywood subfloor. This installation contains the moisture in the slab, increases the subfloor’s stability, and helps to keep the finished floor from swelling, buckling, or cracking. Because a floating subfloor isn’t fastened to the slab, no fasteners are poking holes through the vapor retarder. The moisture in the air is another important consideration.
Most wood-flooring manufacturers recommend that their products be installed in an environment that is a constant 60°F to 80°F with a relative-humidity level between 30% and 50%.
Use the highest-quality materials available
When it comes to selecting vapor retarders, plywood, fasteners, and flooring for a basement, don’t skimp on quality. The basement will expose the flaws in inferior products quickly. I’ve used close to every vapor retarder on the market. When it comes to a floating floor, I always recommend at least 10-mil polyethylene sheeting. A 6-mil product is standard, but it isn’t as durable. I use Fortifiber’s Moistop Ultra 10 and Ultra 15 (http://www.fortifiber.com). For the subfloor, I use two layers of 1/2-in. or 5/8-in. exposure-1 plywood when possible. Exposure-1 plywood is exterior grade—perfect for a concrete application. Pressure-treated plywood can be used as well, but it must be kiln-dried. Pressure-treated plywood straight off the yard can have a moisture content as high as 18%, which is high enough to destroy any wood flooring installed over it.
Even though ground moisture is the #1 concern, slab insulation also makes a difference. In areas with deep subsoil temps 55F or lower (basically half of the US lower 48, all of Canada: http://mb-soft.com/solar/soilmap.gif ) the temperature at the bottom of the subfloor can dwell below the summertime indoor air dew point long enough to take on significant moisture and grow mold. Putting rugs or other insulative materials on top of the floor adds to that risk. In those regions putting some amount of rigid insulation between the subfloor so that the subfloor temp tracks the room temp better can mitigate that issue.
William,
Dana is right. In the northern half of the U.S., a slab on grade or a basement slab should have a continuous horizontal layer of rigid foam under the slab. If your builder forgot to include the insulation layer under the slab, then the rigid foam should be installed between the concrete slab and the plywood or OSB subfloor.
Hi, I'm starting to research finishing over my exposed slab on grade floor. I do not want to have to add a sub floor over top of the slab due to having to raise all trim and making all of my rooms shorter.
The original slab has hydronic heat with no insulation, but supposedly has a vapor barrier. I find the vapor barrier questionable as I can get humidity levels above 70% when I measure near some cracks between my slab and foundation wall. I should note that I am in the process (although slow) of adding 4" of vertical insulation 4' below the top of the slab and 4" of exterior foam above the concrete line to keep it away from the bugs.
Also since the slab has cured for over 10 years is it safe to fill these cracks with cement crack repair or would I be better of filling them with foam or sealant?
Mike,
You didn't mention your climate zone. Installing in-floor PEX tubing for a hydronic (radiant) heating system without also installing a continuous horizontal layer of sub-slab rigid foam is a design error.
You didn't mention your climate zone, but trying to use this system to heat your house might be a mistake. You'll end up buying fuel to heat the soil under your slab. In light of the fact that the builder forgot to install any sub-slab insulation, it might be wisest to abandon the heating system.
If you go ahead with your plan, it's fine to seal the cracks in the concrete with caulk or spray foam.
basements my way are never safely dry. I would use the newer snap together flooring that is made more water rresistant floated over the foam underlayment. Safer, way less cost, less to lose if it needs to be ripped out. The new stuff looks good and or I'm finally getting used to looking at it.
Martin,
Thank you for the response. A few notes:
-the insulation was not installed when the floor heat was installed (by previous owner/builder), the house was sold to me as a "fully insulated and heated floor". I used an air hammer to prove there is no vertical or horizontal insulation. Law suits cost more than it would to try to fix it, especially considering once you win, doesn't mean you will collect. I have basically decided to insulate what I can from the exterior to limit the heat loss through the slab and use mini splits to heat/cool the house and the addition I'm putting on in the next few months. I am an all electric home so my option are limited.
-This is in Zone 4 just W-SW of St. Louis, generally pretty humid, milder winters
- Would the spray foam or sealant last long enough to prevent future moisture issues?
-Would concrete cause spalling/ cracking issues due to expansion and contraction this long after the pour has cured?
AJ this is for a slab on grade home so this slab is actually elevated between 2" and 18" above exterior grade. I have lowered the grade at the rear of the home to allow for a deck and better drainage, and will be doing the same where the 2" elevation is to make it closer to 8" as I don't like the idea of framing lumber sitting a few inches off the ground, even with a treated sill plate.
Mike,
I'm glad to hear that you will be heating with ductless minisplits instead of with the hydronic tubing embedded in your slab. I think that's a wise decision.
You still haven't told us what type of flooring you want to install above your slab. Whatever type of flooring you end up installing, it is essential that you follow the flooring manufacturer's installation instructions. These can usually be found online, and usually include advice for installing the flooring above a slab.
In many cases, you should be able to include a layer of polyethylene above the slab while still complying with the flooring manufacturer's instructions.
Martin,
I am looking at Pergo XP right now. It has a cheap underlayment on it but I would probably still use another one over the concrete first.