HFOs vs. HFCs in spray foam

I am finally ready to insulate my basement with closed cell spray foam. I have the choice between Icynene, Demilec Heatlok HT HFO, or Lapolla Foam Lok 2000-4G.
The latter two brands use HFOs and not HFCs for their blowing agent. I’m not sure which version of Icynene the contractor quoted me for, but he said they weren’t using HFOs yet.
The Demilec HFO product would cost me about $0.50 more per square foot, which translates to roughly $900 more. Of course, if I was completely unselfish, I would pay more and choose the HFO product to reduce my global warming footprint. However, I am still teetering between the two products.
In terms of indoor air quality and long-term health concerns, do HFOs offer less risk than HFCs? Do the products differ in any other way besides the diference in global warming potential?
GBA Detail Library
A collection of one thousand construction details organized by climate and house part
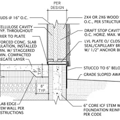
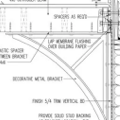
Replies
If you are on GBA, you care about the environment. Go with your conscience and use the HFO products. Future generations will thank you. (I can't speak to the performance difference, if any, for those two blowing agents.)
Jimmy,
I have never heard of any differences between these products when it comes to indoor air quality. It should be said, however, that outdoor air quality -- and the climate -- also matter. We've only got one planet.
The indoor air quality issues sometimes associated with spray polyurethane foams isn't much related to the blowing agent, but rather the temperature and mixture when it's being applied.
If you have a poured concrete or concrete block foundation, you can get there more green-ly and for less money using reclaimed rigid sheet foam for the bulk of the area, and use the spray foam to seal & insulate the band joists and foundation sills to the top of your sheet wall-foam. Unlike site-applied spray foam, the factory-blown foam is created under controlled conditions and monitored for quality before it goes out the door- if the mixture is off by much it doesn't even leave the factory. And after 10-20 years of service any out-gassing issue are very attenuated. To re-use the panel foam in your house uses no new polymer, no new blowing agent, and only piles on to the benefit side of the environmental cost ^ benefit balance.
Closed cell spray foam can be rationalized if the foundation is an uneven and air-leaky surface such as fieldstone or rubble, or rough quarried granite, but poured concrete or CMU walls are easy to insulate using reclaimed rigid foam. You have about 1800' of foundation wall area, which would be about 60 sheets of 2" of roofing polyiso for zone 4A & 4B, 3" polyiso for zones 4C and zones 5 & up. I can usually find 3" reclaimed 4' x 8' polyiso foam for $20/sheet or less, though I've seen it at $25 at times. The 2" stuff is usually $12- $15/sheet. So for 60 sheets you're looking at something like $750-1500 for the wall foam. When comparing it to spray foam the installation labor and fastener hardware have to be factored in too. (As a DIY you can discount your labor, if you like.) You'll still be buying some closed cell foam for the band joists, etc. but overall it should come in quite a bit cheaper (though it will take longer) than an all closed cell foam solution.
Thanks Dana. I should have done that first, but I already have the walls framed out in the basement. For my first house that I built, I was able to get used 1.5" polyiso foam board from Insulation Depot. However, this last time around they didn't have any used foam board in my area. They usually store the foam board they reclaim from a building nearby in rented warehouse space. Other than that, I don't know where else to check.
I usually look for local foam reclaimers searching the local craigslist for the terms rigid+insulation. eg:
https://lexington.craigslist.org/search/sss?query=rigid+insulation
https://nashville.craigslist.org/search/sss?query=rigid+insulation
Hopefully there is sufficient space between the framing and the foundation for slipping in the sheet foam?
If the studs are in contact with the foundation there are potential moisture wicking and condensation issues, and the studs will be thermally bridging that high R/inch foam, undecutting it's effectiveness by a large amount.
The studs are set off the wall by 1". Foam board at this point would be impossible with all the wires, blocking and conduit running between the studs. I will have to do go with the spray foam. The one advantage of the new HFO spray foam is that it can be applied in greater lifts than 2". So they may end up spraying a greater thickness than I paid for because it's hard to get perfect thickness on it and they can't underspray.