High humidity in spray foam attic

Hello all,
Last fall I had my attic spray foamed. Warm temperatures have arrived and I am experiencing higher than anticipated temperatures and humidity in my attic.
I have 3 main questions (pertinent details follow):
1. Is a semi-conditioned attic RH in the 60 – 70% range cause for concern?
2. Should my attic be 10+ degrees warmer than the interior? It will get much warmer here in the coming months and I am worried that the attic temperature difference will grow.
3. Is the fact that the ridge vent is still in place (but foamed closed) a possible source of high humidity in the attic?
—
Here is what I recorded yesterday in late afternoon:
Attic: 86F / 71% RH
Outside: 88F / 44% RH
Inside: 76F / 50% RH
And this morning at 9AM:
Attic: 74F / 53 % RH
Outside: 74F / 75 % RH
Inside: 76F / 53 % RH
—
Here are my home’s details:
– 1960s ranch approx 1400 sq ft
– Climate zone 2
– Dark roof shingles with a sealed roof deck
– 5.5 inches of open-cell Icynene which covers the rafters
– Roof was previously vented with a gable vent and ridge vent; gable vent hole was sealed and foamed and ridge vent was foamed
– Crawl space has been encapsulated / sealed to exterior and has a SaniDry CX dehumidifier set to 50% RH
– New 2-stage heat pump (American Standard / Trane) sized correctly with dehumidification function set at 50%
– Blower closet (central return) was sealed off from attic with spray foam
– Ductwork is in attic; no supplies or returns have been added to attic
– Original rigid ductwork has not been mastic sealed and has original paper-backed fiberglass insulation covering, some in poor condition
– No plants, aquariums, or other additional humidifying sources in home
– New range hood vented to exterior through roof
– New bathroom fan with humidity sensor vented correctly through gable end
Thanks for your consideration!
GBA Detail Library
A collection of one thousand construction details organized by climate and house part
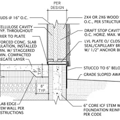
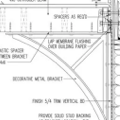
Replies
From what I've read you want to have a supply and return in an enclosed attic.
https://www.greenbuildingadvisor.com/blogs/dept/musings/creating-conditioned-attic
Question 5: Is there any need to condition the attic with a forced-air register?
Okay, you’re coming down the home stretch now. You’ve insulated your sloped roof and your gable walls. You’ve protected any exposed foam with a thermal barrier like drywall. You’ve done your best to limit air leaks in the tricky area at the attic’s perimeter, where the rafters meet the top plates of your exterior walls.
You’ve just created a conditioned attic. Now your HVAC contractor asks you whether or not you want a supply register and a return grille in your attic.
The answer to this question depends on several factors. If you have insulated the roof assembly with closed-cell spray foam, you probably don't need a supply register or return grille in your attic. If you’ve done a good job insulating and air sealing, the temperature of the air in your attic will approximate indoor conditions, even without a supply register or a return-air grille.
If you have insulated the roof assembly with open-cell foam and you live in a humid climate, however, there is increasing evidence that you probably need to install a supply register and a return grille in your attic in order to keep humidity levels low enough to avoid damp roof sheathing. For more information on this issue, see Open-Cell Spray Foam and Damp Roof Sheathing.
Conditioned attics have a few drawbacks
Creating a conditioned attic is a solution to a fundamental design flaw (locating ductwork or HVAC equipment outside of a home’s thermal envelope). But conditioned attics are not unalloyed blessings; they come with their own set of drawbacks.
These drawbacks include:
Installing insulation along a sloped roof is always more expensive than installing insulation on an attic floor.
It’s usually easier to perform air sealing work on the attic floor than to ensure that a conditioned attic is well sealed.
In a home with a conditioned attic, it’s much harder to locate roof leaks or repair rotten roof sheathing than in a home with an unconditioned attic.
Damp roof sheathing will always dry faster in a home with an unconditioned attic than in a home with a conditioned attic.
The bottom line: unless you have ductwork in your attic or you plan to convert your attic to living space, an unconditioned attic is usually preferable to a conditioned attic.
Read more: https://www.greenbuildingadvisor.com/blogs/dept/musings/creating-conditioned-attic#ixzz47PVeWAdj
Follow us: @gbadvisor on Twitter | GreenBuildingAdvisor on Facebook
Nic,
A lot of issues here. One issue is that your roof has much less than the minimum code level of insulation. In fact, you have only 52% of the code minimum.
In Climate Zone 2, the 2012 IRC requires a minimum of R-38 insulation. Since you have 5.5 inches of open-cell spray foam, you have only R-20.
I haven't read a lot on this topic, but it sounds like moisture is stored within the building materials in the attic, and released daily as the sun heats the roof. Have you checked whether the ducts are sweating, which seems likely at 86F and 71%? How much air leakage is there between the attic and the living space?
The choice of open cell foam here is puzzling, both from an R-value perspective as Martin points out, and from a vapor permeability perspective too. In any case, the options seem limited. Sounds like one solution is to dehumidify the attic by adding supply and return ducts or by placing a stand-alone unit in the attic.Another might be to replace the open cell foam with closed cell, or simply revert to a vented attic.
Nic,
If your attic is humid during warm weather, it's always a good idea to verify that there are no air leaks that allow hot, humid exterior air to enter your attic. A blower door test would be a good idea.
If your attic is hot in warm weather, step #2 would be to add more R-value -- with the aim of at least meeting code-minimum levels for R-value. Now that you've started with open-cell spray foam, your options for correcting the problem are limited; it probably makes sense to fur down your ceiling with some type of strapping or additional framing, then add more open-cell spray foam, fiberglass, mineral wool, or cellulose to reach R-38 or more.
On the interior side of your roof insulation, you should install a "smart" vapor barrier, and/or drywall (for fire protection) and a layer of vapor-retarder paint.
The next step would be to install a supply air register connected to your forced-air HVAC system, as well as a return-air grille.
Open cell foam at the roof deck is fine in a US zone 2 climate, but it indeed takes about 10-11" to hit the code min R38, as Martin correctly points out. By "...which covers the rafters..." do you mean to asy the rafters 2x4s, and now covered with 2" of foam, or 2x6 with the foam trimmed flush, or are the rafters deeper, with more cavity left that could be filled?
With no air exchange with the rest of the conditioned space it will take a long time to remove the moisture that is cycling into & out of your roof deck. The fact that the attic temp and outdoor temp are identical in the AM but the outdoor RH is much higher than indoors is an indication that there is at least SOME drying going on- you'd have to track that over a few weeks to be sure that it wasn't just a weather anomaly that produces a higher outdoor high-RH for that one data point, but I suspect it's real enough.
Verifying air tightness would be important, but if it were super-leaky I'd expect the attic air's dew point in the AM go hew more closely to the outdoor dew point, which it doesn't. Adding registers would likely fix the humidity cycling problem (more quickly if a smart vapor retarder is added) but not the low-R problem. The order in which to do it would be air-seal, insulate, THEN add a modest amount of air exchange if it's still a problem. The means by which you insulate depends a bit on your existing rafter depth & configuration. If it's encapsulated 2x4s you may want to do something different than just furring out or "Mooney wall" framing for the extra depth.
Thanks for all the replies. Much appreciated!
After monitoring temperatures and humidity for a few more days, I can confirm that so far it appears that the high temps and RH are short-lived from early afternoon until early evening - maybe about 6 hours or so. Before and after that time both the temp and RH is the same or slightly above the interior. I'll continue to monitor.
@Chris M: I have read that adding supply & return to the attic is one method of dealing with this type of problem, but I am hoping to figure out the source of the humidity first.
@Martin: I am aware of the R-20 rating of the current insulation. I asked the insulation company about this and they assured me that the performance of the home would exceed my previous R-38 blown fiberglass and that this was not an issue. I have now read your previous article on this issue and see that I should indeed have R-38 regardless of the air sealing qualities of Icynene. This is a frustrating issue for me. I am not a builder - just a homeowner. I spoke with insulation companies for advice as well as did some reading online and thought that this job would give me good performance. In fact, the winter utility bill was about 50% of the previous year, and the home seems to be performing better so far during the cooling season, even after replacing the old 3 ton AC with a 2 ton. I still want to achieve the best possible performance though, and clearly the attic is not doing that right now.
Also @Martin: A blower door test sounds like a good idea. Adding additional R-value also sounds like a good idea. I have read your article about installing rigid foam on top of roof sheathing. It sounds like this is another (maybe very good) option for me - is that correct?
@D Dorsett: the rafters are 2x4s and now covered with approx 2" of foam, so that the rafters are totally covered. Indeed there does seem to be quite a bit of drying of the attic occuring - see the info I posted at the beginning of this post.
---
One of my initial questions was whether the existing ridge vent across the entire length of the roof is a possible source of the high humidity? It was foamed in, but of course the open-cell foam is not a vapor barrier. What do you all think? Should I also be removing the ridge vent and sealing the apex of the roof closed?
Also, how concerned should I be about damage to the attic right now? Do I need to urgently worry about mold or rot?