High performance home retrofit (Climate Zone 5)

I am a relatively new member of the GBA community but have been following high performance home techniques on GBA, Fine Homebuilding, etc for some time.
I am a builder in the Boston area and am now renovating my own home. After years of theoretical reading and discussion, I’m going for it and trying to do a whole house retrofit that is as efficient and environmentally friendly as possible. I have sort of glommed on to the idea/path of a Pretty Good Home.
R value targets are BSMT = R20 walls, 1st/2nd floor R32, Attic R60. Slab will be limited to R4-5.
A few questions for the group here are;
1 – Basement is an older junk slab, approx. 2″ thick over rubble and dirt. Walls are larger stone with somewhat smooth concrete skim coat on interior. A few hairline cracks visible. Lot drops of steadily front to back creating a full walk out basement. Front wall approx. 65% below grade, side walls less than 40% on average. Over the last 7 months, basement observed to be dry from both moisture penetration and condensation. With 8′ from slab to joists, I’ve decided to skip the repour and use EPS foam over the slab and walls. The basement will be finished so I plan to tape the EPS with a “european tape” and use a double plywood subfloor over the EPS as seen in several articles here. Questions on the basement assembly are;
* What type of EPS is best for this application? Unfaced, faced, best type of EPS?
* What type of plywood is “most stable” for this type of subfloor?
* Best adhesive for EPS to wall adherence?
* Short sighted not to add drainage to sump for an observed “very dry” basement?
2 – 1st and 2nd floors have been double studded to create an on average 8″ thick wall assembly. Plan is to use Intello inside, blown in cellulose in cavity, mix of old pine sheathing/new 1/2″ OSB on a dormer we added, an outside layer of SonoClimat ECO4 exterior insulation (R4) and finally a self adhered WRB that is TBD. Questions on wall assembly are;
* Can/should the Intello be added once all rough elec and plumbing are complete, then taped to seal? I’m assuming yes and realize this is probably a basic question but want to get it right.
* I plan to use the Intello as the netting for the cellulose. We don’t have room to loose another 3/4″ or 1.5″ for horizontal strapping over the Intello. Is this an acceptable method for install?
* Are specific air-sealing outlet boxes necessary or can you work around standard boxes by taping from the rear of boxes?
* A lot of hype around European WRBs. I have only used Henry Blueskin to date for a self-adhered WRB. At nearly 2.5 times the cost, are the “other” WRBs worth the cost? Brands to consider?
Attic to be blown in cellulose to 18-19″ thick. Slope of roof does cause a section of the roof of no more than 3′ to be limited to 11″ of cellulose. This obviously brings down the R value at this outside edge of the roofline. Not ideal, but we sistered rafters down as low as we could.
Currently the attic has two large gable vents (gable roof with front and rear shed dormers). I have read of some people not venting a blown in cellulose attic. Seems crazy, is that a thing? Only reason I ask is the reduced rafters are right where rafter baffles will have to go, further reducing R value in that section.
I appreciate any advice this knowledgable group is able to share.
GBA Detail Library
A collection of one thousand construction details organized by climate and house part
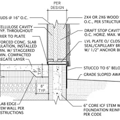
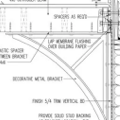
Replies
Hi Joe.
As far as the basement goes, I don't think it is short-sighted not to install a perimeter drain and sump if you have been in the house long enough to know that the basement is dry. I don't have an opinion on what type of EPS is best, though I am hearing from more and more high performance builders that they like the graphite-impregnated EPS (Neopor is one brand name), which has somewhat higher R-value.
Are you going to frame walls inside the foundation? This would allow you to get more R-value in the walls which would be a good idea since much of the basement is above grade.
You can do the two-layer, staggered seam, floating floor with any 1/2 inch plywood subflooring.
As far as the walls go, your plan seems fine. I have never installed Intello but assume it would be much easier to install with the flanged, air-tight electrical boxes than trying to tape it to common boxes.
I don't think anyone can tell you much about the number of fully-adhered WRBs beyond their experience working with them. They just haven't been tested in the real-world for long enough yet. That said, I have heard anecdotally about failures with one common fully-adhered WRB. The thing is, the assembly didn't include a rainscreen detail. I'm not sure any WRBs stand up to water trapped against them in perpetuity.
You are right that most attics with cellulose insulation on the attic floor are vented and most building inspectors require it. There are options beyond soffit and ridge vents though. For example, you may be able to put under-shingle intakes in the roof above the cellulose sheathing. Check out this Fine Homebuilding article: Venting a Tricky Old Roof
I would say that eight months isn't nearly long enough to know that the basement is always dry. That's not even all four season, and presumably not even spring which is the wettest season where you are. What happens in the ten-year maximum event, the 20-year, the 50-year? Water in a finished basement can cause a lot of damage very quickly. What happens if a sewer backs up? Do all of your appliances have pans and drains?
Either build to withstand water or have somewhere for the water to go.
I agree. And if Joe were asking about finishing a basement, I'd have a much stronger opinion (for the most part I think it is a bad idea). But in terms of installing insulation for comfort and efficiency, I'm more forgiving in those opinions.
>"I am a builder in the Boston area and am now renovating my own home.
----------------------
>" * What type of EPS is best for this application? Unfaced, faced, best type of EPS?"
The greenest (and least expensive) solution would be 2-3" of whatever used stuff the Insulation Depot on Waverly Street in Framingham has on hand (usually Type-VIII or Type-II). If you're really struggling to maintain headroom, cut back to 1.5" (R6-ish), or even 1" (only if you're desperate). The upcharge for graphite loaded EPS to go from R4.2 to R5 @ 1" will NEVER be "worth it" for slab insulation from any perspective, performance, carbon footprint, cost, etc.
Leave an inch gap from the EPS to the foundation wall as a drain space for any bulk water incursions.
Put a sheet of 6 mil polyethylene between the foam & subfloor.
>* What type of plywood is “most stable” for this type of subfloor?"
A double layer of CDX, seams staggered, as Brian recommends. If the slab is reasonably flat the double-layering allows the subfloor to be floated, no need to TapCon it to the slab. Leave at least 3/8" around the perimeter to manage seasonal dimensional changes with humidty.
>" * Best adhesive for EPS to wall adherence?"
Any vendor's foam board construction adhesive works. But for the walls use 3.5" (or 4") of reclaimed fiber faced roofing polyiso (which is dirt-cheap and in copious supply in our area,) not EPS which would need to be 5" to hit the R20 target. Polyiso is somewhat hygroscopic, so keep the cut bottom edge off the slab- let it rest on the floor EPS.
>" * I plan to use the Intello as the netting for the cellulose. We don’t have room to loose another 3/4″ or 1.5″ for horizontal strapping over the Intello. Is this an acceptable method for install?"
According the the folks a 475 High Performance Building Supply, NO- not if it's going to be dense packed:
https://foursevenfive.com/blog/how-to-install-dense-pack-cellulose-with-intello-plus-airtight-membrane/
@Brian Pontililo, @DCContrarian and @Dana Dorsett, many thanks for your replies. I was away at the Better Building by Design conference in VT and have been playing catch up.
To answer a question that I left out details on, yes we do plan to finish the basement. More and more, I do not liking finishing basements myself. We have a finished basement as our master now (don't ask) and when a frost free silcaulk let go three springs ago and flooded our basement, I swore I was done with it. That said, we need the space and it's about the best New England basement I've seen in an old house - little below grade foundation, high ceilings, full height walk-out out rear and as mentioned, observed to be very dry.
@DCContrarian, this is a full gut reno so yes appliances will have pans, sensors. I agree about 8 months not been that long. That said, have spoken with several multi-decade owners on my side of the street with similar topography and basement layout and they have attested to very dry basements as did the 42 owner of our house. If you saw the unique topography, you would understand why. That said, noted about additional protections and drainage. Going to think about it.
@Dana Dorsett, thanks for the tip on the Insulation Depot, had not heard of them. Going to call today. As for polyiso, given that we are going to finish the basement and have walls, was planning on using rock wool in the 2x4 stud walls to make up the difference between EPS and achieving an R20 wall. I plan to tape the EPS seams.
I was in touch with 475 earlier in the project and thought they had said I could forgo the channel. Need to check those notes. The article seems to be indicating the biggest risk is the bulging which I've worked around before. Do you think skipping the Intello and simply using the drywall as air barrier is a better way to go? Aerobarrier?
If I skip the tapcon fasteners for the plywood, will I perpetually feel that "bounce" you often feel with a floating floor? Not a big fan of that.
Again, thanks for the input.