High-R wall in Zone 7: Roxul OK? Are there potential moisture problems with deep Roxul walls and existing siding?

I have a cabin in the mountains of Colorado (zone 7; 9,200 ft altitude). Yes, it gets cold here, and the heating season is long. Last snow can be as late as the first week of June. First snow often the first week of September. Many wonderful, sunny days in between though, and I tell people the summers are incredibly beautiful up here – the best month and a half you’ll ever see.
I’m doing a gut rehab to turn what is an uninsulated 640 sq ft. 1972 summer cabin kit, into an efficient, warm and hopefully net zero, year round place to be. (installing a 5kw solar PV system, Alpen 925 windows, and probably a mini split ductless HP as part of the remodel. Will be using existing cast iron fireplace insert as supplement heat).
Basic structure is 20’x32′. Post and Beam, with tongue & groove cedar siding that’s integral to the posts – siding fits in slots down center of posts – part of the load bearing strength (aged with lots of character – really want to avoid covering it with exterior rigid foam). Currently it’s completely gutted, with the interior of the siding and post and beam structure fully exposed.
I’m considering a couple of options for building a high R type double wall, using the existing shell as the outer structure.
Inside to outside:
Consideration #1 –
1″ tongue and groove pine (urethane finish)
2×4 24oc new framed inner wall with Roxul fill (R15) – wiring cavity
Intello membrane on exterior side of 2×4 inner wall (protected smart vapor retarder)
7 1/4″ space filled with Roxul (R30) between 2×4’s/Intello and outer wall for thermal break
Air seal inner siding and post joints with Prosoco Joint Sealer and caulking
Post and beam / cedar siding
Total clear wall insulation R value = 45
– – –
Consideration # 2 –
1″ tongue and groove pine (urethane finish)
2×4 24oc new framed inner wall with Roxul fill (R15) – wiring cavity
4″ space between outer wall and inner 2×4’s for thermal break – filled with ccSPF (R26)
Post and beam / cedar siding
Total clear wall insulation R value = 41
– – –
My preference is to go with option 1 – a thick, thermally broken Roxul wall w/ mid placed smart vapor retarder – for fire resistance and to avoid any longterm potential of off-gassing from the closed cell spray foam. (I know there are two sides to the ccSPF discussion – many say it’s safe)
But after reading Building Science Corp. report on “Moisture Management for High R-Value Walls”, I’m concerned that with option 1, the cold interior side of the exterior cedar siding might have significant condensation/moisture problems that wouldn’t have a chance to dry very well in our long cold season – and would be wet much more of the year than dry, esp. on the north side of the cabin. (In the BSC report a comparable high R double wall w/deep fill cellulose and mid-placed poly vapor barrier was rated very poorly for inner sheathing moisture control in a High R wall, and considered high risk in a very cold climate, like mine)
Option 2 – with 4″ of ccSPF – looks like it could eliminate the potential of inner siding condensation because the ccSPF would effectively vapor seal it and move the dew point well within the foam. And the inner surface of the ccSPF would be warm and dry. (But the questions surrounding ccSPF are a concern, both chemically and fire safety)
Additional structure info:
The cedar siding is approx 1 1/2″ thick, solid tongue and groove, and the interior side of it seems to have a light finish of some type – not sure if it would dry well to the outside in option 1 or not. Outer siding finish in semi-transparent stain.
Adding a vented air gap between the siding and outer Roxul insulation layer in option 1 isn’t possible because the siding is in the same vertical plane as the outer edge of the sill plate, CMU crawl space wall, and header beams.
4 ft Crawl space CMU foundation wall will be insulated on exterior with moisture barrier and 4″ XPS foam (R20), then back filled to grade (excavating to install). Crawl space dirt floor will have R10 insulation layer, and sealed 20 mil vapor barrier.
Ceiling has 12 inches of XPS foam (R 60 w/thermal breaks on rafters) that was installed 15 yrs ago and is in great shape – protected with thermal ignition barrier. (may replace it later – but for now it’s ok)
After thinking all of this through, it looks like option 2 is probably the way to go … as much as I’d prefer option 1.
I’m hoping some of you with much more knowledge and experience might look at this and let me know your thoughts … Open to input. Yay, nay or something else.
Thank you in advance.
GBA Detail Library
A collection of one thousand construction details organized by climate and house part
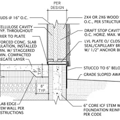
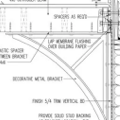
Replies
Robert,
So, you have tongue-and-groove boards installed in slots in your timber frame, right? Do these tongue-and-groove boards have siding on the exterior? Or are these boards considered "siding"?
I'm trying to visualize the exterior: The timber frame is exposed to the weather, right? And so are these tongue-and-groove boards. So what kind of flashing details does the house have at the windows, or an the horizontal ledges of the timber frame?
If there is no siding other than these boards, there is no need to worry about "condensation" on the interior of these boards. Everything will dry out very quickly to the exterior. But you may have to worry about water entry on the exterior.
Both options prevent water vapor from the interior from getting to the exterior siding, if they are implemented well. So I don't think option 2 has any advantages there. And its disadvantages are not only what you mention, but also high cost, and high global warming impact of the "blowing agent" gas used to make the bubbles in the spray foam, 1400X worse than CO2, unless you get the newly available Lapolla spray foam. And you already didn't like it. So I think we can elminate the ccSPF option.
The report you reference notes potential problems in exterior OSB sheathing. You won't have those problems because your cedar boards are much more vapor permeable than OSB, and because they are are more tolerant of high moisture should that occur. Also, the problems noted were associated with air leakage, and you have the opportunity to avoid that if you do this well.
As much as I like smart vapor retarders, I don't think you need one. Their advantage is that they open up with high humidity to allow drying to the inside if the inside is air conditioned, but I don't think you'll have much of that scenario. So I think you could use polyethylene film, or perhaps a peel and stick membrane as a sure way to get good air sealing. Oh, I guess you weren't planning on any sheet goods there? So there wouldn't be anything to stick the peel and stick to. I might put something like 3/8" plywood in there, as I could see the membrane getting torn a bit here and there during the installation of insulation.
On the foundation insulation, I recommend EPS over XPS, because it gives you more R-value per $, especially once it's aged (XPS loses R-value over time), and because it has lower global warming impact (XPS made in North America uses similar blowing agents to those used in ccSPF).
But as Martin notes, the exterior can get wet from rain, and for best drying it should be configured as a rainscreen with air space behind it. It's had that up to now, and it's worked, that shouldn't get any worse. You say that's not an option now, but I think your concern is that there's no way to truly vent that space. A space helps even if it's not truly vented. And there might be creative ways to provide it with a little venting.
Option 1 gives you an air barrier which also creates a utility chase so you can run wires and pipes without penetrating the air barrier. Charlie's idea of using plywood instead of a smart membrane makes sense, but if you build the interior stud wall on the floor and apply the membrane before standing it up, you should be able to avoid damaging it. I'd run it long on top so you can integrate it with the ceiling air barrier. We did that on my house and the membrane didn't get torn.
Martin,
Thank you for your reply. You guys on this site are great for having the patience of Saints in trying to help.
I'll try to describe it as best as possible to help you visualize how it was put together.
The cedar tongue and groove siding is not assembled in a traditional nail on or screwed on fashion It's stacked horizontally betweens the posts with tenons that fit into vertical grooves down the sides of each post (kinda like one long mortise) Posts are 4x4 48" oc . Each piece of siding is 1 1/2" thick x 5 1/2" tall x 44" long (+ the tenons into the posts.) It's stacked with tongue up, groove down, interlocking each other with drainage down and out. … it' the exterior siding, and the interior of the wall structure.
The only flashing is a beveled board on top of the rim joist that hangs 1/2" proud of the plate, and the same at the header beam. Original doors and windows had very simple flush mount wood frames with similar beveled boards for header flashing and sills (they leaked air, but somehow never leaked water into the interior) Never had a wet wall issue in the 28yrs I've owned it. It's actually pretty solid as a result of it's simple interlocking structure.
The new Alpen windows will be placed as "innies" - secured with mounting tabs - in new plywood bucks sealed with prosoco liquid membrane, and expandable foam tape on beveled sills (like the Karuna Passive House on youtube) trimmed with more traditional wood sills, jams, stops, headers, and header angled flashing (thinking copperl) at the top - following the concept of "down and out" for drainage, with a traditional cabin trim look.
Regarding potential condensation on the interior of the siding with the new high R insulation. It's always had plenty of air on the inside and staying dry has never been a problem. Just had lousy brown paneling (like it was taken from the inside of a 1972 chevy van) with a 3/4" layer of celotex in between. Very much a summer cabin. The thin coating of inner finish on the siding - not sure what type - still has me wondering if that might limit outer drying of inner moisture - it's always been able to dry inward.
And being limited in my knowledge and experience with these things, I'm concerned a cold inner siding surface - possibly getting damp through vapor diffusion/convection, might not dry too well to the inside through 10 1/2" of roxul with tongue and groove pine inner facing. (I will have guitars there and need to keep the relative humidity levels in the 35-45% range for them.)
Hope the add'l description helps.
I respect your experience and knowledge, and maybe I'm over thinking the vapor diffusion, cold interior side condensation plane thing too much.
I do like the natural qualities, moisture and fire resistance of Roxul very much. And the idea of thick warm walls in what has been a cold drafty cabin, with wonderful vistas of the Rocky Mountains … well, I think I could live with that, and count myself amount the fortunate to be there.
Curious, Do you have any thoughts on the Intello use or placement?
Robert,
Basically, your house formerly functioned as a log home (or what is known in Vermont as a "plank house" -- a house with stacked horizontal timbers instead of round logs -- which is different from a plank house in the Pacific Northwest).
It worked because it could easily dry in both directions. It probably leaked air like a sieve.
Its performance will change when it becomes airtight and insulated.
I'm still worried about water management on the exterior. Some photos would help.
Martin,
Here's a photo of the exterior. Not much on detail and don't have close ups of the siding, but it might give you a better idea of it.
You're right. You could say it does function as a log home, with milled timbers.
Stephen,
I was planning on doing exactly that with the Intello membrane … installing it on the floor before raising the wall, and going long on top to integrate it with the ceiling for a continuous floor to ceiling/ across ceiling vapor retarder.
I'm curious as to what you might see as a worthwhile benefit of using 3/8's ply instead (as Charlie suggested), since it's not needed structurally … Is it more for durability, less risk of it being compromised or punctured? Or different vapor management /drying characteristics?
I was thinking Intello because it's a stronger, more reinforced material than Membrain.
What type of smart vapor retarder did you use? Would you use it again?
Martin,
Oh yeah … it leaked plenty of air … it's a structural heat exchanger all it's own.
I agree with your comment on it performing differently with the air sealing and insulation mods. My questions revolve completely around that, and how to best approach it for durable results.
When you say you're worried about water management on the exterior … What specifically are you referring to? Do you mean the exterior flashing mods with the new windows? Those will be the only changes to the exterior side.
Thanks again for your time and expertise.
Robert. Using plywood might be cheaper and doesn't require much care to avoid damage, but I'd go with the membrane. Probably it was overkill, but we stapled the membrane and taped over the staples. We used 3M 8067 flashing tape.
We used Siga Majpell, primarily for air sealing purposes. Our double stud wall was designed to dry either to the inside or outside, so we figured Majpell's 0.68 permeance was good enough. We would use it again. It was a bit cheaper than Intello. Intello is a smart vapor retarder, whereas Majpell isn't. You could also use Membrain.
Having the wiring and plumbing inside the membrane greatly simplified air sealing, since we didn't need to worry about sealing around electrical boxes or plumbing lines.
Stephen,
I was also going to staple, then tape over the staples attaching Intello to the exterior side of the 2x4 inner wall studs, floor and ceiling connections as well. It's a simple step for the little bit of extra puncture sealing insurance.
I also like the idea of keeping the wiring, switches and outlets inside it's own chase, for the air sealing benefits too. And later when my girlfriend just has to hang a picture of her cat next to the one of my dog, the Intello won't be punctured.
One of the fortunate things with the cabin being so small (640 sq ft), going with materials that cost a bit more doesn't add much to the overall budget, within reason of course.
The windows are one of those areas where I didn't let budget be the driving factor. Alpen windows are manufactured a couple of hours away, and I was able to tour the facility and see their product firsthand before ordering. The performance numbers for them are really impressive, and high performing windows were central to the plan. Large picture windows to the south and east, and if they don't perform well, nothing I do on the wall insulation will matter much.
Your project sounds great. We used minisplits here in Maine, zone 6. It's been an unusually mild winter, with just two nights below zero F, so the heat hasn't really been challenged. But the minisplits have kept us warm without a problem down to -8 F.
Good windows are definitely worth the investment.
Stephen,
Thanks for sharing your user experience with mini splits.
I'm hoping with the solar PVs being net metered, it won't cost me anything to warm this place over the year average. And with the newer mini splits working to -14 deg F. (reports of working to -20deg) It should be good for the vast, vast majority of the time, if not all of the time. Good passive solar heat gain during the days, and plenty o'sunshine through the winter days to make electricity. I'm pleased.
I'm curious about your wall structure … would you mind sharing the details?
It's nice to read that experienced knowledgable people think the deep filled Roxul wall can work without condensation moisture issues on the outer siding … I'll be very happy if it continues to look like a good way to go with this.
Robert: From outside, our wall consists of
White cedar shingles
Cedar breather as rain screen
Typar, joints taped
Advantech sheathing, joints also taped
2x4 studs 24" o/c-this was structural
5" space
8 1/2" Dense packed cellulose blown through the Majpell
Majpell membrane, joints, holes from cellulose and staples taped
2x4 studs 24" o/ c in line with outer studs
Fiberglass batts
Drywall.
We ended up with a blower door test of .59ach50, so it's pretty tight. This was our contractor's first double stud wall, but he's a smart guy with good workers so there really weren't any problems. House is cozy and warm.
Charlie,
Thanks for your suggestions.
Yeah, air conditioning isn't used in this location …at this altitude, light jackets are good to have even on July evenings after the sun sets.
I was thinking the Intello smart membrane might give me the vapor performance of something like the 3/8's ply, but didn't see a structural need for plywood within the wall cavity … I'm open to doing it though, as long as it would provide an additional benefit, and wouldn't create a vapor sandwich to the outside.
Will also consider the EPS foundation insulation … I was thinking XPS for it's moisture tolerance. And because I've seen EPS (bead board) disintegrate over time in high moisture freeze thaw situations, as I would have below grade … But I'll admit I'm not fully knowledgeable with it, and I have seen plenty of pictures lately of it being used for foundation insulation.
Question for Charlie, (and Martin)
Regarding Charlie's suggestion to put an air space between the 30R Roxul fill and interior side of the siding …I could easily tack 1x2 strips against the interior of the siding spaced 12" or so, and then apply something like tightly stretched Tyvek (vapor open wind barrier) then the R30 Roxul fill against that.
Even accounting for some bulging of the Tyvek it would provide a small 3/4 - 1/4" air space between the Roxul and inner face of the siding. Eliminating the direct contact between Roxul and siding of the current option 1. (though venting that space to the outside is still not possible because of the vertical plane of the structure)
Would that function better for drying (or condensation management?) than if the Roxul were in direct contact with the interior of the siding?
I'm doing the work myself and the small additional time to do it is of no concern.
Stephen,
Thanks for the detail on your wall build. It looks like there are similarities with the final clear wall R values with what you did and what I'm trying to do.
I checked out the Majpall … cool stuff, and looks easy to work with.
Excellent blower door test results … That's not a "pretty good house", it's a "damn good house". Great job.
I will be paying lots of attention to air sealing the exterior wall seams and joints (on the inside) before doing any wall build work. There's your tip to buy Prosoco stock now, before their earnings per share go through the roof (pun intended).
Space between Tyvek and the siding will allow drying better than Tyvek against the siding. And probably a little better than Roxul against the siding with no Tyvek. But I think the Tyvek is important to add to help the Roxul work better by avoiding wind coming through the cracks and blowing warm air out of the Roxul. So I think Tyvek or other house wrap spaced away from the siding is the way to go.
I'm not sure how much success you'll have in doing that just by tensioning the Tyvek. I'd be inclined to use an expanded plastic mesh rainscreen product like Homeslicker or Dri-Wall to provide that spacing.
Martin ... Any thoughts on where this is going?
Based on your experience, is the air space "over thought" for an unnecessary concern? (as we newbs have a tendency to do sometimes.)
Any possible problems introduced by it?
Or would you recommend I stop over thinking it, and follow your original comment ... "If there is no siding other than these boards, there is no need to worry about "condensation" on the interior of these boards. Everything will dry out very quickly to the exterior."
Robert,
It sounds like you are willing to spend the money to have above-average details. That's good.
In many ways, you have a house with leaky siding and no sheathing. So I agree with those who recommend establishing an air space between the interior surface of your existing tongue-and-groove boards and the exterior surface of your wall insulation. The idea of using sticks and housewrap (Comment #16) to create this air space makes sense to me. If you go that route, try to install the housewrap in an airtight manner.
Here is a link to an article that may be relevant: Insulating Walls in an Old House With No Sheathing.
Thank you, Charlie. I'll look into the products you mentioned.
Using Tyvek, or that with something like those other products, to serve as facing for the Roxul, create an air space and eliminate wind washing was exactly the thinking. So we agree on that.
I'm also thinking now I might not air seal the interior horizontal joints of the tongue and groove cedar siding with Prosoco , and leave them a bit "air leaky" as they currently are, to hopefully aid drying in a space that can't be practically vented otherwise. (esp since they've never allowed water intrusion) However minimal that amount of air may be, it maybe could help more than an air tight, dead air space. And I'll have two vapor permeable air barriers within the rest of the wall structure now anyway, (Intello mid placement, and Tyvek inside of siding) So no harm if there's a little bit of allowed air leakage into that interior siding space? maybe a benefit?
The idea of using what was a negative (air leaky siding) as a positive to maybe help manage interior siding moisture concerns … If it really would work that way, I like it.
Very cool … looks like the deep fill Roxul is gonna fly.
Everyones help is much appreciated.
Robert,
You need an air barrier on the exterior side of your assembly, but there are several possible ways to do it.
If you want to spray a vapor-permeable liquid-applied WRB to the interior side of the siding, you could. That would work. Or you could establish an air space behind the siding boards.
I'm still worried about the water-entry details on the exterior, though, and about flashing the windows. Are there any signs that the timber frame is deteriorating because it is exposed to the weather?
One last point: you can't take advantage of winter sunshine when your PV array is covered with snow, so you will need to either (a) clear your panels with a broom every time it snows, or (b) put the PV modules on an adjustable rack so they can be mounted vertically from Oct. 15 to March 15.
Martin, Thank you for your quick reply.
I read that article a few days ago, and it's informed my thoughts on this a quite a bit.
From your response, it sounds like leaving the siding joints unsealed doesn't raise any red flags for you - as long as attention is given to making the house wrap airtight? Do you think it might provide a benefit, as intended?
In my situation I have the advantage of not having to try to place and seal the housewrap in separate stud bays … I can do entire walls with large fields of the wrap, because it's within the thermal break space, and the exterior walls don't have traditional studs as part of their structure
Q: My thinking is, since I won't be making any changes to the exterior siding, I should be able to have a reasonable amount of confidence it will continue to prevent water intrusions. Unless there are physics at play that I don't understand.
A. It depends how often the space was heated in the past. Without insulation, heating it up just a few weekends a year could dry out any moisture in a hurry. So it might have been more tolerant of leaks in the past than it will be in the future.
Martin,
Re: the PVs and snow. Understood. The roof shown in the photo is the north face. The ridge runs almost directly east / west. if I wanted to align the cabin for solar power, I would put it exactly where it is. The southern face will be covered in solar panels … it has a great angle, and clears of snow on it's own not too long after a snow without having to climb up there and sweep it off (daytime solar melt contributes greatly to that)… There would of course be a few days of power generation affected after a heavy snow, and people up here have come to accept that. On southern roof faces here, it's nothing like the way snow lingers around in other locations in the US. Also, the cabin has grid power, and the solar PVs will be grid tied, and are meant to supplement and make it net zero on an annual average basis, but not take it off grid. High winds in winter storms make vertical solar arrays more vulnerable to damage up here when the big ones move through. So compromises are more successful, long term.
All of the timbers are still in great shape … inside and out … never had any water intrusions through the walls and windows or moisture leaks of any kind, and no rot or deterioration. My thinking is, since I won't be making any changes to the exterior siding, I should be able to have a reasonable amount of confidence it will continue to prevent water intrusions. Unless there are physics at play that I don't understand.
I do understand your concerns about the new window flashing … Any suggestions?
Even though I've researched how to install inset windows properly, and discussed it with Alpen Windows (they've been very helpful), I thought about finding an experienced (preferably old school) window installer who could advise me on how to install and flash inset windows the right way. And I want to have the windows inset for better cold weather performance, and extreme weather protection. I think inset windows look better in cabins like this too. More visually dimensional, traditional, and appropriate for the architecture.
Again, your help reviewing this, and your suggestions are greatly appreciated.