Hot water, cast iron radiator heat design / remodel

Hi,
I’m looking for some guidance on where to go with our hot water, cast iron radiator heat. We love the radiant heat of the cast iron radiators, so not looking to switch to a different type of heat.
We have two boilers for our 130 year old 6700 sqft house. One newer boiler (7-8 years) and one old boiler that is on it’s last leg.
We’re looking for the best approach to eliminate the risk of the larger boiler deciding to call it quits in the middle of the winter. And, I don’t really want to blindly accept someone trying to sell/install a new boiler that is the same size as the current boiler as I’ve been reading up on the ‘old’ method of calculating heat loss versus the ‘right’ method.
In doing some rough math myself, I believe that our heat loss is somewhere in the 175,000 Btu/hr range. The specs on our smaller (newer) boiler state DOE HTG CAP. 127 159 MBH and IBR Water 110 138 MBH.
We currently have 3 zones (including hot water heater) on smaller boiler and 1 zone on the big old boiler (although it would be nice to break that into 3 zones).
In addition, we have heat exchangers in select rooms. Also a chimney that is not lined, so a high efficiency boiler is out of the question unless we line the chimney.
I have many questions: including whether the smaller boiler could be used to heat the entire house – maybe if it rotated through zones instead of trying to heat all zones at once? Or, if we do need to get another boiler, what is the best configuration / sizing? Are there heating consultants in my area (North Shore Boston) that I could consult with?
Thanks,
Dean
GBA Detail Library
A collection of one thousand construction details organized by climate and house part
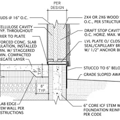
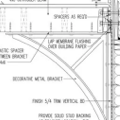
Replies
On the north shore your 99% outside design temp is between +5F & +10F. A heat load of 175,000BTU/hr for 6700' is a ratio of 26 BTU per square foot which is a bit on the high side at that temp unless there is literally no wall insulation and a lot of air leakage, even for an antique. With some tigthtening you should be able to bring that under 140K, maybe even under 120K, but probably not under 100K.
Have you run a fuel-use based heat load sanity check on your rough numbers?
https://www.greenbuildingadvisor.com/blogs/dept/guest-blogs/out-old-new
I've recently been analyzing a house of comparable age and size (a bit under 6000') in SE MA that comes in under 100,000 BTU/hr @ +10F on a fuel-use basis, and that's BEFORE some planned air sealing upgrades. Even though there's more than R40 fluff in the attick in that house a contractor turned in a Manual-J that assumed R8 up there, along with a bunch of other errors to come up with a heat load north of 150K (not including distribution losses) and a recommended 200K boiler. (Clearly that contractor isn't getting the work.)
They're now looking at installing a 110K (in) Lochinvar with a 10:1 turn-down ratio to be able to break it into more zones, and a bit more radiation on one of the zones to deliver more heat and avoid short-cycling. After the planned building upgrades it should have sufficient margin for Polar Vortex coolth.
If a fuel use heat load analysis on your place comes in under 159,000 BTU/hr (and it probably will), the smaller boiler will be able to handle the load.
The high thermal mass of the radiators makes it less prone to short cycling, but some analysis needs to be done if breaking it up into smaller zones. A cast iron boiler that big still needs some load to avoid short cycling. Some of the napkin-math for that can be found here, along with considerations for installing a higher efficiciency boiler:
https://www.greenbuildingadvisor.com/article/sizing-a-modulating-condensing-boiler
A high efficiency boiler can be side-vented with plastic venting. Closing up the chimney (and air-sealing the chimney chase) will lower the actual heat load, since it's drawing air all the time, whether it's firing or not. If it's the same chimney flue serving both boilers it may be oversized and need a liner if only one boiler is in use.
So, run your napkin-math numbers on both the heat load and the radiation (per zone, on any planned zoning) BEFORE talking to any consultants or contractors and keep a spreadsheet going. You'll save yourself time & money by having the basic stuff done up front, and avoid wasting contractors' time by submitting and resubmitting proposals that aren't really optimal.
It's also worth getting a MassSave basic audit on the house looking for low hanging fruit on the weatherization front. A house that old might even qualify for subsidized blower door testing & blower door /IR imaging directed air sealing.
https://www.masssave.com/en/
Thanks for the quick response - and sorry for my delayed response. You provided me with a ton of additional stuff to look up!
To answer some of your questions...
In 2/3 of our house, we are very close to zero insulation 2x4 walls. As we have lathe and plaster on the inside and a 'back plaster' layer within each stud bay I used R6 instead of the R3.4 that I saw for no insulation. R6 might even be a little aggressive?
The fuel use heat load analysis was a good idea. I may need to double check my numbers, but I calculated a 86,128 (base 65 degrees) to 95,098 (base 60 degrees) BTU/hr usage. However, we keep our house cold - we probably average 58-60 degrees in the winter. I certainly want to design a system that meets the 68 degree requirement. I used 1,821 gallons of oil between 11/11/17 and 5/11/18. I used the 140,000 BTU / gallon to convert to total BTU.
I also did a rough calculation on the radiators and baseboard. I calculate a total emission of 334,990 BTU/hr @ 180 degree water temp (217,330 BTU/hr @ 150 degrees). The single zone that I'd like to split has a total of 254,728 BTU/hr (@180 degrees). After split, I'd have 2-3 zones. If 3 zones, they'd be 127,245, 58,378 and 69,105 BTU/hr (@180 degrees). I'd imagine that there is low risk of short cycling?
What are your thought on the longevity of the high efficiency boilers? Many say that a high efficiency only lasts 10-15 years whereas a cast iron lasts 15-30 years.
Condensing gas boilers have improved a lot in the past couple of decades. 10-15 years was never really a typical lifecycle, but 20-25 years would be a reasonable assumption for a new fire-tube condensing boiler with a stainless steel heat exchanger. But do you have gas on your street? Switching to propane is almost always a mistake unless you invest in your own tank and shop around for the best price. The vendor-owned tank micro-monopolies where the propane company owns the tank and the exclusive right to fill it are rife with abuse.
If the average temp in the house was 58-60F use base 55F (not 65F) to come up with the BTU per degree-hour constant, then add 10F to the heating degrees when running the calculation to estimate what the load is at a code-min 68F would be.
Using 140,000BTU/gallon source fuel is slightly to the high side of average. 138,500 BTU/gallon would be more likely. So the 1,821 gallons have 252.2085 MMBTU(million BTU). Burned at 85% combustion efficiency in a reasonably tuned oil boiler 214.377 MMBTU went into the house, the rest went up the flue.
You didn't specify a ZIP code or town. I'll use Beverly Municipal Airport weatherstation KBVY.
Since the beginning and end dates didn't get the full HDD (unless it was filled a minute after midnight on 11/11 and a minute before midnight on 5/11) averaging the HDD55 from 11/11 through 5/10, with the HDD55 from 11/12 through, 5/11 averages out the time of day fill up error. At KBVY that average was 3375 HDD55.
214.377 MMBTU /3375 HDD55 = 63,519 BTU/ degree-day, which is (/24=) 2,647 BTU/degree-hour.
Using +10F as an outside design temp and a base temp of 55F we have (55F-10F=) 45F heating degrees if the indoor temp is 58-60F, with an implied load of 2,647 x 45 = 119,115 BTU/hr.
Adding 10F to the heating degrees to reflect the load at a code-min 65F we get 55F heating degrees and an implied load of 55F x 2,647= 145, 585 BTU/hr
Adding another 10F to reflect what it would take to keep it at 68-70F at 0F outdoors during a Polar Vortex cold snap we have 65F heating degrees, and an implied load of 65F x 2,647= 172,055 BTU/hr.
So the boiler with 159 MBH of output would cover your 99% load at a 60F indoor temp, as well as at 70F, but would it be able to keep the whole house at 70F when it's 0F outdoors.
A load of 172K @ 0F-outside / 70F-inside for a 6700' house is a ratio 26 BTU/hr per square foot, which is consistent with a lot of air leakage and the low wall-R.
If the boilers were de-tuned to 80% to protect the clay lined flues from exhaust condensation the actual load numbers will come in 5% lower. Did the burner tech tag them indicating the tested combustion efficiency on the last tune up?
With 335MBH of heat emitter @ 180F average water temp (AWT) and a 159MBH boiler the AWT with all zones calling for heat would come in at ~140F AWT, with an entering water temp (EWT) at the boiler of 130F. Some oil boilers can tolerate 130F (eg Buderus Logano), but not lower. But the flue condensation is potentially copious at an EWT less than 140F. If it doesn't already have a system by pass branch plumbed into the boiler to keep the EWT above 140F (probably does, but check if you're keeping the oil-burner) a stainless flue liner is in order.
With the smallest zone emitting 58,378 BTU/hr @ 180F AWT and a boiler dumping 159,000 BTU/hr into the system, there is a significant risk of short-cycling if that zone is all fin-tube baseboard. If it's high volume (=high thermal mass) cast iron it probably won't. But in either case a heat purging boiler control strategy should be used, when the boiler output is nearly 3x the amount of heat emitted by the smallest zone.
A 175-200K (input) modulating condensing gas boiler with a 10:1 turn down ratio would be fine with both the zoning and the total design load. With just a 5:1 turn down ratio it would be important to do the math on the available thermal mass in smaller zones.
A couple of possible boilers that would fill the bill would be HTP's UFT-175, Lochinvar's KHB-199, but there are several others to consider if you think you're heading down that road.
Of course, it may be worth spending some money now to lower the heat load. The exterior side stackup of sheathing /siding /weather resistant barriers on the uninsulated walls and the window flashing details would tell whether there are inexpensive safe ways to insulate them.
You've certainly given me more to digest. I think that I understand most of it, but might have more questions as I dig in further.
You guessed right by using the Beverly municipal airport. I do live in Beverly. However, I do get a slightly different HDD when I add up 11/12/17-5/11/18 on the base 55 chart. I get 3424.2. Not sure why...
How do you know/calculate the EWT? You mention that if the AWT is 140F that the EWT would be ~130F.
Lastly, the smallest zone (if I do split the large zone into 3) of 58,378 is a cast iron radiator zone - hence, high volume.
I'll have to check to see if the tech has noted the combustion efficiency.
Without repeating the degreedays.net download I added the 11/11 through 5/10 HDD to the 11/12 through 5/11 data and divided by two to get the average. There was a significant difference between the two, but it wasn't THAT large- I may have missed a day or added a day when using the clumsy spreadsheet tool that was on the machine I was using a the time (an ancient Vista operating system thing.)
At typical pumping rates in a well designed system there's about a 20F delta-T across the radiation at mid-range temperatures (not low temp, not high temp). So to hit an AWT of 140F the boiler output is 150F, the return from radiation is 130F. If it's over-pumped the delta-T might only be 10F. At higher water temps the delta-T increases, at lower temps it decreases. Ideally there would still be at least a 10F delta-T on the radiation at condensing temperatures. But we won't really know the delta-T on your system at any given temp until/unless you've measured it.
At condensing temps the output of radiation is about 1/3 of what it is at a AWT of 180F, so for a condensing boiler you'd like the min-fire output to be no higher than 58,378 / 3= ~19.5K A 200 K condensing boiler with a 10:1 turn down can throttle back to about 19K out. At non-condensing temperatures a 200K boiler would still deliver over 170K of output, and that's the maximum size boiler that makes any sense for the fuel-use calculated heat load. (DO run those numbers multiple times, for multiple periods if you have the data.) While a 200K boiler with only a 5:1 turn down won't short-cycle on a high mass zone it's not guaranteed- you'll have to run the math, and may have to spend more time tweaking the boiler settings to keep it well-behaved.
For the 159 MBH cast-iron boiler feeding high-temp water to just that zone the burner is 3x oversized for the heat emitted, and you're counting on the thermal mass of the zone plumbing and boiler to keep minimum burn times high enough. You're looking at about 100,000 BTU/hr (= 1667 BTU per minute) of excess heat going into the zone. If there's 100 gallons of water + equivalent iron thermal mass in the radiators + zone plumbing + boiler that's 834 lbs of water-equivalent thermal mass, which. takes 834 BTU to raise the temperature by 1F. So when the boiler is firing the temperature is slewing at a rate of about 1667/834= ~2F per minute. With the high/low differential set to 20F the minimum burn time would take about 10 minutes, which is fine. If there's only 50 gallons of thermal-mass the minimum burn time is about 5 minutes, which reduces the net efficiency by about 1-2%. It's worth running the math on the water volume and total iron mass that's in play when just that zone is being served, but I suspect it'll come in at minimum burn time of more than 5 minutes. For rough calculations, every 9 lbs of iron in the radiators plumbing & boiler is worth 1lb of water mass, every gallon of water is good for 8.34lbs. This isn't super-accurate- the density of 180F water is lower than 32F water, and the specific heat of iron varies by alloy, but for estimation purposes it's good enough. Measure the plumbing diameters & lengths and look up the volumes & weights in engineering tables. Find some similar size & shape radiator specs to estimate their water volume- it doesn't have to be super-close.
Heat purging boiler controls typically purge heat from the boiler down to a programmed temperature on a new call for heat, and maximize the high/low differential during a call for heat, then "learn" the system to anticipate the end of a call for heat, cutting the burner and finish the call with the residual heat in the boiler & distribution plumbing, parking the system at a lower temperature between calls from the thermostats. While the peak temperatures are still pretty high, the average temperature is lower, and the lower idling temperature reduces standby losses.
I assume the single boiler is a cast iron boiler, 82-86% efficient correct?
You could tie the two systems together, then install a High efficiency modulating boiler. It runs solo in series/parallel and takes the cool return water and raise it just a little as needed, the other boiler raises it the rest of the way.
This only works if there are secondary loop pump(s) and each boiler would have it's own separate pump each with it's own primary loop. Advantage here is the low efficiency boiler can have constant flow and a 3 way valve to control return water temp to keep it over 130-150F (depending on boiler design). the high efficiency boiler can run constant flow and just run a higher temp rise as demand goes up.
Sizing: You need to size the combined output to the house at design conditions. Ignore what the radiator capacity is. I'll bet your oversized.
Thanks for the quick response!
Yes, both current boilers are cast iron. The smaller one is in that 82-86% efficiency range. The large, old one I'm sure is significantly lower.
Not sure that I follow your thought 100%. I think that you are saying to replace the large old cast iron boiler with a high efficiency boiler, but to make sure that both boilers have pumps to independently heat all 3 zones (4 if hot water heater included)? I'm not fully following your thoughts on the constant flows and water temps of the two boilers - can you explain further.
Sorry for not following...
Consider re-plumbing to allow use of both boilers but turn off the older one. See how well the newer one handles your load. Possibly add an electric boiler if you are just a little short.
Possibly a Chiltrix heat pump would be cost effective in mild weather (when loads and radiators are compatible with < 34K btu/hr at low supply temps).
Good ideas. We've thought about re-plumbing to allow use of both boilers not only to see if the smaller one can handle the load, but to also use the smaller one as a fail safe if/when the larger one decides that it's done.
We do have a few Mitsubishi heat pumps in a few select rooms. They certainly help in mild temps and we don't have to heat the zone, but my understanding is that they won't help us on the coldest of days (I'm using 5-10F as a design temp).
>"We do have a few Mitsubishi heat pumps in a few select rooms. They certainly help in mild temps and we don't have to heat the zone, but my understanding is that they won't help us on the coldest of days (I'm using 5-10F as a design temp)."
Your understanding may be mistaken- what model numbers do you have?
Mitsubishi heat pumps have a specified output at +5F. With the "Hyper Heating" aka "H2i" versions the available capacity at +5F is the full rated heating capacity of the unit, and it's not chump-change. At current oil & electricity pricing in eastern MA it's still going to be cheaper heat than oil.
The expense of re-plumbing to keep the second boiler integrated into the system would be a waste of money, money better applied to lowering the heat load with air sealing & insulation upgrades.
Is the foundation insulated? A high temp boiler & distribution plumbing located in an uninsulated stone foundation is likely to be responsible for 15-25% of the fuel use, that would drop to less than 3% by insulating the foundation walls to the current R15 (continuous insulation) code minimum. So that 145K load would most likely drop to less than 125K. (Unfortunately MassSave won't subsidize foundation insulation, but they 'll subsidized insulating and air sealing the band joists.) In most homes this is pretty easy to rationalize, though still less important than air sealing & insulating above grade walls & attics.