How to Find Studs Through Exterior Insulation

Hi everyone,
I have 2 questions about installing vertical furring strips for siding over 3″ of exterior Roxul Comfortboad insulation (over a peel and stick WRB/exterior air barrier). I plan to connect the furring to the studs (nominally at 16″) with long structural screws through the insulation.
1) How do you efficiently locate the studs once WRB and exterior insulation are installed, to reliably hit the studs with the screws? I assume the studs will not all be at exactly 16″ c/c, due to framing having to line up for openings, beams, etc.
2) If I do miss the stud when installing the screws, my instinct is to leave the screw, or else there will be a hole in my exterior air barrier (I also plan to have an interior air barrier). However, any ideas of how I would seal that 1/4″Ø hole through 3″ of Roxul insulation if I did remove the screw?
Thanks!
GBA Detail Library
A collection of one thousand construction details organized by climate and house part
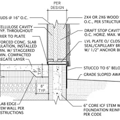
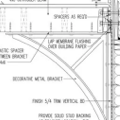
Replies
The real answer here is that it’s hard to do, and it’s a shame the difficulty isn’t discussed more often. Having said that there’s a few things that helped me achieve a first hit rate of about 93%. Even that isn’t great if you think about it, that’s 7 screw misses. Worse are the near misses, where you bust out the side of the stud, or if the grain cups to one side and bends the screw out, etc.
Here’s a list of practical and somewhat impractical steps I took to help.
0. Do a good job get the studs plumb. It is more important here than absolute spacing.
1. Use a speed square to draw a line down the middle of each furring strip. It’s pretty quick when you have them in a pile and get after it.
2. Pre drill the hole for each screw in the furring strip. You can do this at the same time. It will make your battery last longer during the install, and you won’t have to think. It helps. If you can stand it, have a helper pre start the first and middle screws in the hole so that the install can be quick.
3. Mark the location of the center of the stud on the foundation with something as light as a pencil mark. That’ll help line up the bottom line.
3.1 Align the rafters with the studs if possible. I used my rafter tail as a visual guide for the top of the furring strip. Line that up first, and plumb the furring strip with a 6’ level. That will get you close to being in the right spot.
4. Use the smallest diameter fastener that will satisfy your load requirements. It’s cheaper, and there’s less chance of splitting the stud. I tried spax powerlag, fastenmaster headlock, and the Simpson screw. My preference was for the spax. Buy them in bulk, they ain’t cheap. The fastenmaster was cheaper, but more flimsy imo, and had more trouble driving in.
5. Use a drill and not an impact driver. It has sufficient deriving capability, is faster, and so much quieter. You can also feel a miss better.
6. Don’t overtighten the fasteners, just snug up where the MW minimally compresses is enough. You can adjust them later.
7. Butt the insulation between furring strips. The edges are more compressible than the field, and if you try to hide an insulation seam with a furring strip it’ll be harder to make the wall flat while not having one or two that are sunk in too far.
8. Pull a missed screw, and put on a dab of caulking from the inside of the sheathing. It’ll air seal the hole, and there’s no water getting through that much space to the web anyways.
9. The corners are harder to get right, I’d consider two 1.5” layers of polyiso just in those areas, maybe a foot on either side, just to help make them square.
10. Pull a string line between corners at every line of screws, and micro adjust the plane of the furring strips to just barely touch.
Hope it helps!
Wow Kyle, what a great response! Thank you! I feel like your response could be a whole article on GBA or FHB.
I was planning to use HeadLOK screws because I am familiar with other FastenMaster products, but will look into the spax also.
Also, point 8, great idea and I am glad I asked now before all the stud cavity insulation is installed.
I will try to remember to report back with any lessons learned once I am done (not likely until later this summer).
Thanks James, though I’ll admit to only repeating most of what I’ve read elsewhere, and tried myself :). Except for the drill, my own hatred of noise spawned that one.
James,
I used the reply above in another comment, and I was wondering how yours turned out - any updates?
Ha! Good timing, I just referred back to this post a couple days ago as I am purchasing materials right now. I am about to start in hopefully 2 weeks (much later in the season than planned… sigh) but I will post some pictures and any lessons learned after that.
Awesome! Good luck and thanks for the update.
Hi Kyle,
Sorry for the much delayed response. Here are photos of the exterior insulation and strapping. Our process (after some trial and error) was to predill the holes with a Kreg cabinet jig (didn't have a drill press) and pre-start the screws (GRK R4 5-5/8") before aligning the strapping on the wall.
Some lessons that may be useful to others in the future:
1) Pre-drilling with the jig, rather than free hand, was the biggest improvement to our success rate for hitting studs. Any small angle is really exaggerated by the long length of the screws. Afterwards I discovered an inexpensive tool called DrillBlock from Home Depot that would also work, but the Kreg jig also ensured the holes were all the same distance from the edge of the strapping, so as long as the first screw hit, and the strapping was vertical, then the rest of the screws usually hit.
2) The screws are surprisingly expensive... $1 CAD per screw and probably used 1 screw per 2 sf. If you are budgeting for this wall assembly, don't forget to account for this.
3) We used ripped strips of 3/4" plywood on the corners. We took a lot of time to get them plum in 2 directions but once screwed together, they feel very strong.
4) "Strapping" I could buy at box stores in Ontario is only 5/8" thick, so I bought cheap 1x10 boards (3/4" x 9.25") and ripped them into 3" strips. I wanted 3/4" for better nail hold from the siding. There was a fair amount of wastage throwing out parts with large knots from the cheap wood, but I needed many small pieces too, so I was able to cut around them, and it was still the cheapest option. We used leftover plywood for some 3" strips too... it is definitely stronger.
5) Because it was so late in the season, I only took the time to carefully line up the strapping on the high gable wall (in/out from the wall) so far. Others have expressed concerns about this but I found this relatively easy as long as all of the screws start with the insulation maybe 3/16" compressed so you have room to drive the screws in/out to get everything lined up.
6) I zip tied a piece of plywood with a scrap of insulation to the top of my ladder so I could lean the ladder against the exterior insulation without damaging it.
Great writeup Kyle! I'd like to add a couple of points as well from my personal experience:
1. Make a template from 5~6" long piece of 4x4 hardwood block by predrilling it with the same drill bit you would use for predrilling furring strips. Drill this hole at a 5° angle. This template will make predrilling your furring strips much easier and more consistent.
2. I highly recommend Strong-Drive® SDWS TIMBER Screw (Exterior Grade) https://www.strongtie.com/strongdrive_exteriorwoodscrews/sdws-db_screw/p/strong-drive-sdws-timber-screw-exterior-grade. Despite their larger diameter (compared to HeadLOC equivalent), they go in very easy and cause no splitting even when they are not driven in the center of the stud. I've done a few tests driving these screws off center of the stud and even as close as 3/8" to the stud edge they caused no splitting.
The Simpson sds screw is nice! I just thought they were overkill when I tried a box of them. I’m nearly certain I could winch the earth closer to the moon with one, if I had a long enough cable.
The problem I had with them was probably the lumber I was using. All SYP with wide growth rings. A lot of the time it would follow the channel between two summer rings, and part the stud, without splitting it. I’ll see if I can find a picture.
James,
I've used one of these to keep the holes aligned with good success.
Lining a stack up on a drill press wouldn’t be a bad idea, but they’re one of those tools that are super handy to have, once or twice a year it seems. Nobody has the tall ones. I wish they were cheaper.
Well done James! That looks very neat. Good tip on the cabinet jig too!
You can use a plunge router to predrill the holes too, which works well if you have an edge guide for the router (to set the edge offset). Spiral upcut bits work great for that.
Good use of a tool that you probably already have, assuming the furring strips are 1x or similar thickness.